What Does It Mean For A Process To Be Capable
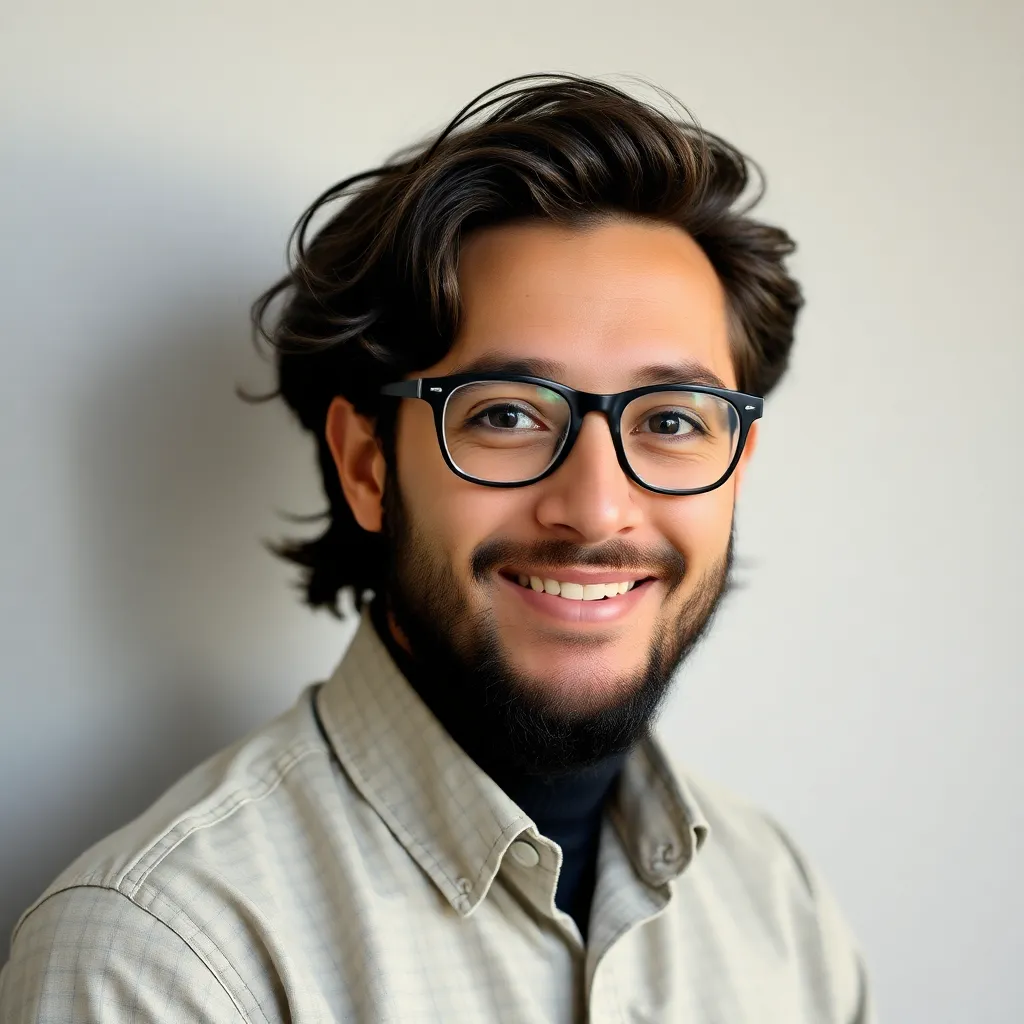
Holbox
Mar 31, 2025 · 6 min read
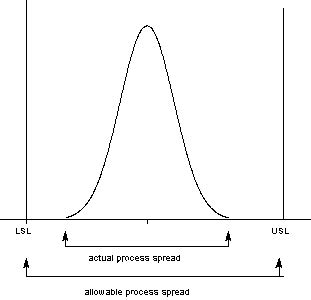
Table of Contents
- What Does It Mean For A Process To Be Capable
- Table of Contents
- What Does It Mean for a Process to Be Capable?
- Understanding Process Capability: Beyond Simple Accuracy
- Key Elements of Process Capability
- Measuring Process Capability: The Role of Capability Indices
- Cp: Process Capability Index
- Cpk: Process Capability Index (Considering Centrality)
- Pp and Ppk: Performance Indices
- Interpreting Capability Indices: What the Numbers Mean
- Improving Process Capability: A Multifaceted Approach
- The Importance of Process Capability in Different Industries
- Beyond the Numbers: The Holistic View of Process Capability
- Conclusion: Continuous Improvement is Key
- Latest Posts
- Latest Posts
- Related Post
What Does It Mean for a Process to Be Capable?
Process capability is a critical concept in quality management, representing the ability of a process to consistently produce outputs that meet pre-defined specifications. Understanding and improving process capability is crucial for any organization aiming for high-quality products or services and efficient operations. This article delves deep into the meaning of process capability, exploring its key elements, measurement methods, and practical implications.
Understanding Process Capability: Beyond Simple Accuracy
Process capability isn't just about whether a process produces the right results on average. It's about the process's consistency and its ability to consistently produce results within acceptable limits. A process can be accurate on average but still highly incapable if its output fluctuates wildly. Imagine a machine designed to produce bolts of a specific length: even if the average length is correct, significant variations above and below the target render many bolts unusable. This highlights the importance of both centrality (average) and dispersion (variability) in assessing process capability.
Key Elements of Process Capability
Several key elements contribute to a comprehensive understanding of process capability:
- Specifications: These are the pre-defined acceptable limits for the output of a process. They are often expressed as upper and lower control limits (UCL and LCL). These limits define the acceptable range of variation.
- Process Mean: This represents the average value of the process output. A process mean close to the target value indicates better centering of the process.
- Process Standard Deviation: This indicates the amount of variability or dispersion in the process output. A smaller standard deviation suggests better consistency and predictability.
- Process Variation: This encompasses all sources of variation influencing the process output. These sources can range from inherent variability in materials, machine wear and tear, operator skill differences, and environmental fluctuations.
- Capability Indices: These are statistical measures that quantify the process capability based on the relationship between the process variation and the specifications. Common indices include Cp, Cpk, Pp, and Ppk.
Measuring Process Capability: The Role of Capability Indices
Process capability is most effectively measured using capability indices. These indices provide a quantitative assessment of how well the process performs relative to its specifications. Let's explore some of the most common indices:
Cp: Process Capability Index
The Cp index measures the potential capability of a process, assuming the process is centered on the target value. It's calculated as:
Cp = (USL - LSL) / 6σ
where:
- USL = Upper Specification Limit
- LSL = Lower Specification Limit
- σ = Process Standard Deviation
A Cp value of 1 indicates that the process spread is equal to the tolerance range. Values greater than 1 suggest the process is capable, while values less than 1 indicate that the process is not capable. Higher Cp values signify greater capability.
Cpk: Process Capability Index (Considering Centrality)
Unlike Cp, Cpk considers both the process spread and its centering. It's the minimum of two values:
Cpk = min[(USL - μ) / 3σ, (μ - LSL) / 3σ]
where:
- μ = Process Mean
Cpk provides a more realistic assessment of process capability than Cp, as it accounts for potential off-center processes. A Cpk value of 1 indicates that the process is capable, and higher values represent better capability.
Pp and Ppk: Performance Indices
Pp and Ppk are similar to Cp and Cpk, respectively, but they use the overall variation observed in the process data, rather than the within-subgroup variation. This makes them useful for assessing the overall capability of a process, regardless of whether it is in statistical control.
Pp measures the potential performance of a process, while Ppk considers both the performance spread and its centering.
Interpreting Capability Indices: What the Numbers Mean
The interpretation of capability indices is crucial for effective process improvement. Generally, values above 1.33 are considered excellent, values between 1.0 and 1.33 are considered adequate, while values below 1.0 suggest the process is not capable and requires immediate attention.
However, the interpretation shouldn't be strictly based on numerical thresholds alone. The context of the process, the cost of defects, and the industry standards should also be considered. A process with a Cpk of 1.1 might be considered acceptable in some low-stakes applications, while it may be deemed insufficient in other contexts with higher quality demands.
Improving Process Capability: A Multifaceted Approach
Improving process capability often involves a multifaceted approach focusing on identifying and reducing the sources of variation in the process. This can include:
- Statistical Process Control (SPC): SPC techniques, such as control charts, are used to monitor process performance, identify potential problems, and prevent them from escalating.
- Root Cause Analysis: Tools like fishbone diagrams and 5 Whys are used to investigate the root causes of variations and defects.
- Process Optimization: Techniques like Design of Experiments (DOE) can be used to systematically optimize process parameters to minimize variation and maximize output quality.
- Operator Training: Proper training and skill development can significantly improve operator performance and reduce variability associated with human error.
- Equipment Maintenance: Regular maintenance and calibration of equipment can help prevent machine-related variations.
- Material Selection: Choosing high-quality materials with consistent characteristics can help reduce input-related variations.
The Importance of Process Capability in Different Industries
The importance of process capability varies depending on the industry and the nature of the products or services produced. In industries with strict quality requirements, such as pharmaceuticals, aerospace, and medical devices, maintaining high process capability is critical to ensuring product safety and reliability. A failure to meet capability standards in these sectors could lead to serious consequences.
In other industries, the impact of low process capability might be less severe but can still lead to increased costs due to scrap, rework, and customer dissatisfaction. Regardless of the industry, continuous improvement in process capability is essential for achieving operational efficiency and sustainable competitiveness.
Beyond the Numbers: The Holistic View of Process Capability
While numerical indices are essential for quantifying process capability, a holistic view encompassing the entire process is equally vital. Consider these additional aspects:
- Customer Requirements: Process capability must align with customer requirements and expectations. Meeting specifications doesn't guarantee customer satisfaction if the product or service doesn't fulfill their needs.
- Sustainability: Sustainable practices should be integrated into process improvement efforts. Minimizing waste and resource consumption is crucial for long-term process capability.
- Employee Engagement: Engaging employees in process improvement efforts fosters a culture of continuous improvement and enhances the chances of achieving sustainable capability improvements.
- Technological Advancements: Utilizing modern technologies and data analytics can offer significant opportunities for improving process understanding and implementing targeted improvements.
Conclusion: Continuous Improvement is Key
Process capability is not a one-time achievement but a continuous journey of improvement. Regular monitoring, analysis, and adjustment are vital to maintain and enhance process capability over time. By effectively measuring, understanding, and addressing the sources of variation, organizations can enhance their process capability, leading to improved product quality, increased efficiency, enhanced customer satisfaction, and a stronger competitive edge. A robust process capability assessment and improvement strategy are crucial for long-term organizational success in today's demanding business environment. Remember, continuous improvement is the key to maintaining a highly capable process and achieving sustainable competitive advantage.
Latest Posts
Latest Posts
-
Nutrition Through The Life Cycle 7th Edition
Apr 03, 2025
-
Add Substituents To Draw The Conformer Below
Apr 03, 2025
-
A Firm Pursuing A Best Cost Provider Strategy
Apr 03, 2025
-
Below Are Incomplete Financial Statements For Bulldog Incorporated
Apr 03, 2025
-
Pn Pediatric Nursing Online Practice 2023 A
Apr 03, 2025
Related Post
Thank you for visiting our website which covers about What Does It Mean For A Process To Be Capable . We hope the information provided has been useful to you. Feel free to contact us if you have any questions or need further assistance. See you next time and don't miss to bookmark.