What Are Two Goals Of Operations Management
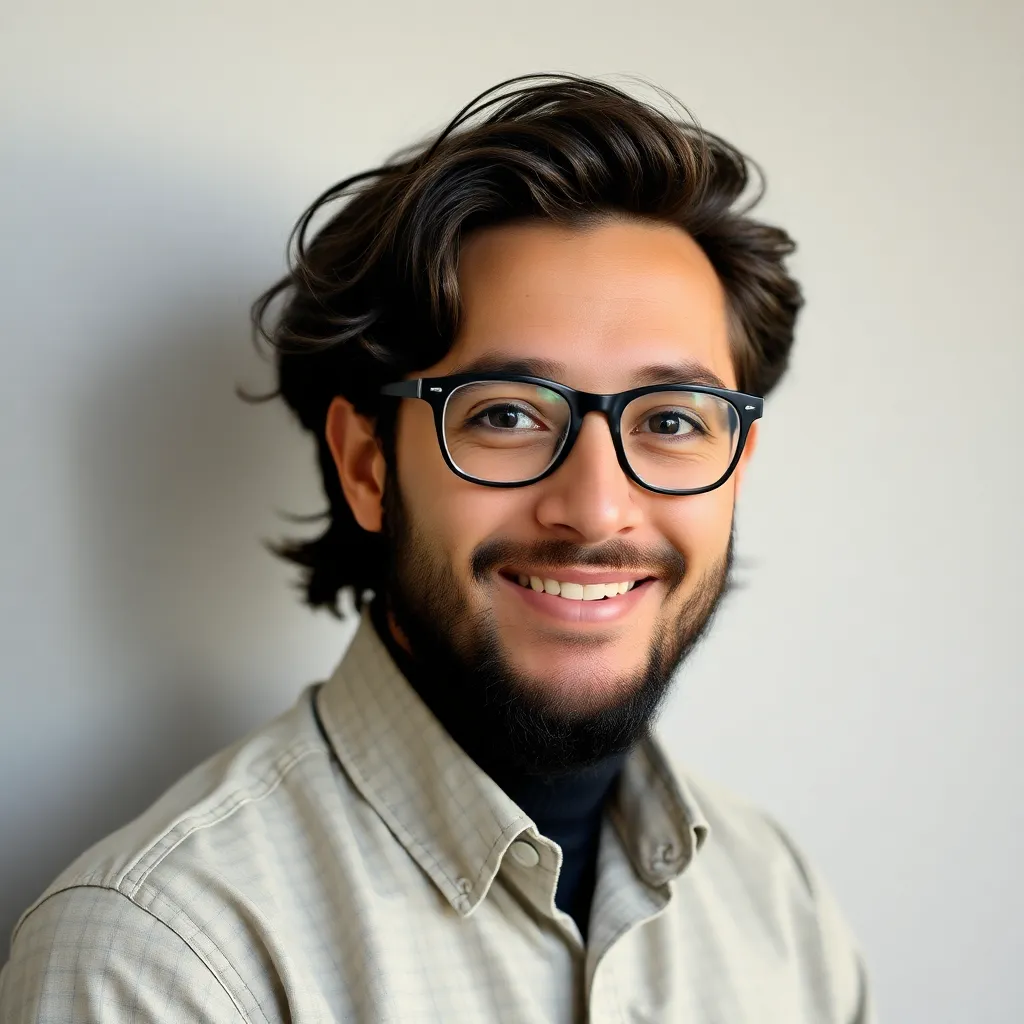
Holbox
Apr 25, 2025 · 5 min read
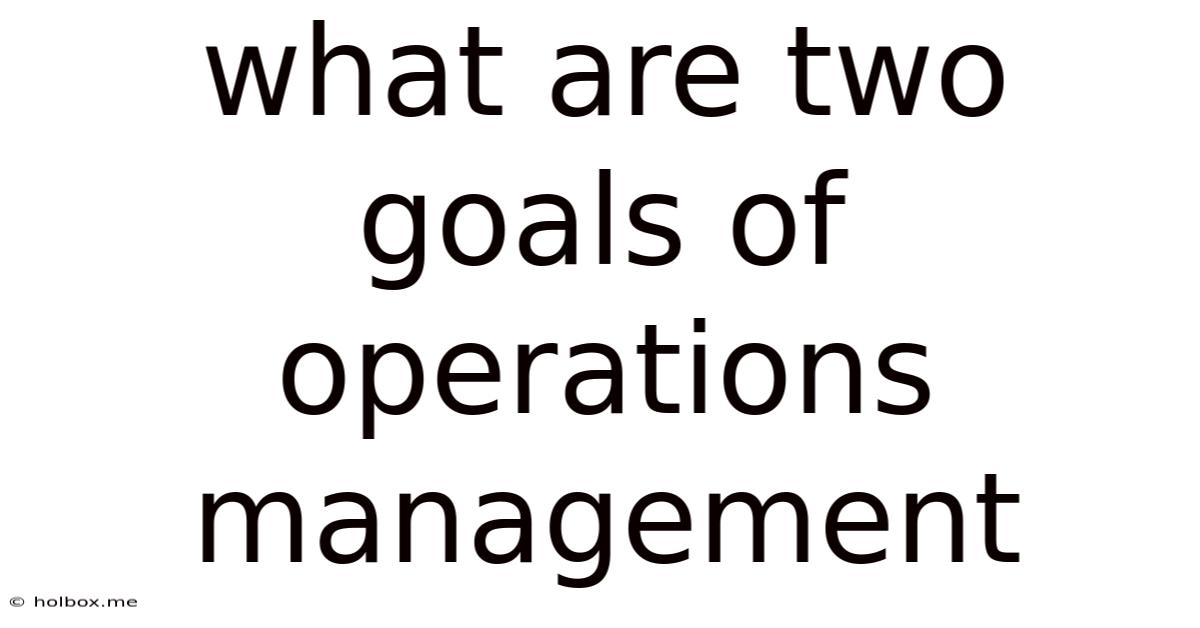
Table of Contents
- What Are Two Goals Of Operations Management
- Table of Contents
- What Are Two Goals of Operations Management? Efficiency and Effectiveness: A Deep Dive
- Efficiency: Maximizing Output with Minimal Input
- Key Metrics of Efficiency:
- Strategies for Improving Efficiency:
- Effectiveness: Meeting Customer Needs and Achieving Strategic Objectives
- Key Metrics of Effectiveness:
- Strategies for Improving Effectiveness:
- The Interplay Between Efficiency and Effectiveness
- Achieving the Optimal Balance:
- Conclusion: A Holistic Approach to Operations Management
- Latest Posts
- Latest Posts
- Related Post
What Are Two Goals of Operations Management? Efficiency and Effectiveness: A Deep Dive
Operations management (OM) is the backbone of any successful organization. It's the engine that transforms inputs (resources like materials, labor, and technology) into outputs (products or services) that meet customer needs. While OM encompasses a vast array of activities, two overarching goals consistently guide its strategies and practices: efficiency and effectiveness. These goals, though intertwined, represent distinct yet equally crucial aspects of successful operations. This article will delve into each goal, exploring their nuances, practical applications, and the delicate balance required to achieve both simultaneously.
Efficiency: Maximizing Output with Minimal Input
Efficiency in operations management is all about doing things right. It focuses on minimizing waste and maximizing productivity by optimizing the use of resources. The ultimate aim is to achieve the highest possible output with the lowest possible input cost. This translates to:
Key Metrics of Efficiency:
- Productivity: This measures the ratio of output to input. Higher productivity indicates greater efficiency. For example, producing more units per labor hour shows improved productivity and therefore efficiency.
- Cycle Time: This refers to the time it takes to complete a process. Reducing cycle time means faster production and improved efficiency.
- Inventory Turnover: This metric indicates how efficiently inventory is managed. A high turnover rate suggests effective inventory management, minimizing storage costs and the risk of obsolescence.
- Defect Rate: A lower defect rate signifies fewer wasted resources and improved efficiency. Quality control measures are crucial for maintaining a low defect rate.
- Resource Utilization: This assesses how effectively resources (machinery, labor, space) are being used. High resource utilization implies minimal idle time and optimized resource allocation.
Strategies for Improving Efficiency:
- Lean Manufacturing: This philosophy focuses on eliminating waste in all forms (overproduction, waiting, transportation, unnecessary processing, excess inventory, unnecessary motion, defects). Techniques like Kaizen (continuous improvement), Just-in-Time (JIT) inventory management, and value stream mapping are integral to lean manufacturing.
- Six Sigma: This data-driven methodology aims to reduce defects and variability in processes. It employs statistical tools and techniques to identify and eliminate the root causes of defects, improving efficiency and quality.
- Automation and Technology: Automating repetitive tasks using robots, software, and advanced machinery can significantly improve efficiency by increasing speed, accuracy, and consistency. This also frees human resources to focus on more complex and value-added activities.
- Process Optimization: Analyzing and streamlining processes to identify bottlenecks and eliminate unnecessary steps can significantly improve efficiency. This often involves using tools like process mapping and flowcharts to visualize and optimize workflows.
- Employee Training and Empowerment: A well-trained and empowered workforce is a more efficient workforce. Investing in training programs and providing employees with the autonomy to make improvements can boost productivity and efficiency.
Effectiveness: Meeting Customer Needs and Achieving Strategic Objectives
Effectiveness in operations management is about doing the right things. It focuses on achieving organizational goals and satisfying customer needs. Effectiveness ensures that the outputs produced are relevant, valuable, and meet the required specifications. This involves:
Key Metrics of Effectiveness:
- Customer Satisfaction: This measures how well the organization meets customer expectations regarding quality, delivery, and service. High customer satisfaction indicates effective operations.
- Market Share: A larger market share suggests that the organization's products or services are effectively meeting customer demands and competing successfully.
- On-Time Delivery: Meeting delivery deadlines is crucial for customer satisfaction and effective operations.
- Quality: Meeting or exceeding quality standards ensures customer satisfaction and minimizes returns or rework, improving overall effectiveness.
- Innovation: Developing new products or services and improving existing ones demonstrates effectiveness in adapting to market changes and exceeding customer expectations.
Strategies for Improving Effectiveness:
- Market Research and Customer Feedback: Understanding customer needs and preferences is crucial for developing effective products and services. Regular market research and collecting customer feedback are essential.
- Product and Service Design: Designing products and services that meet customer needs and are competitive in the market is fundamental to effectiveness. This involves considering factors like functionality, aesthetics, usability, and price.
- Supply Chain Management: Effective supply chain management ensures that the necessary resources are available when and where they are needed. This minimizes disruptions and ensures timely delivery.
- Strategic Planning and Alignment: Operations management strategies should be aligned with the organization's overall strategic goals. This ensures that operations contribute to the achievement of the organization's objectives.
- Adaptability and Flexibility: The ability to adapt to changing market conditions and customer needs is crucial for maintaining effectiveness. This involves developing flexible processes and systems that can be easily modified to respond to new challenges.
The Interplay Between Efficiency and Effectiveness
While efficiency and effectiveness are distinct concepts, they are inextricably linked. An organization can be highly efficient in producing a product that nobody wants, rendering its efforts ineffective. Conversely, an organization may be effective in meeting customer needs but do so inefficiently, leading to high costs and reduced profitability. The ultimate goal is to achieve a balance between both: to be both efficient and effective.
Achieving the Optimal Balance:
- Value-Added Activities: Focus on activities that directly add value to the product or service from the customer's perspective. Eliminate or streamline non-value-added activities.
- Continuous Improvement: Embrace a culture of continuous improvement, constantly striving to improve both efficiency and effectiveness. Employ methodologies like Kaizen and Six Sigma to drive continuous improvement.
- Data-Driven Decision Making: Utilize data analytics to monitor key performance indicators (KPIs) related to both efficiency and effectiveness. This allows for informed decision-making and adjustments to optimize operations.
- Cross-Functional Collaboration: Break down silos and foster collaboration between different departments (e.g., marketing, sales, operations) to ensure alignment between operational goals and overall organizational objectives.
- Employee Engagement: Engaged employees are more likely to contribute to both efficiency and effectiveness. Create a workplace culture that values employee contributions and empowers them to improve processes.
Conclusion: A Holistic Approach to Operations Management
The two primary goals of operations management—efficiency and effectiveness—are not mutually exclusive but rather complementary. Achieving a balance between these two goals requires a holistic approach that encompasses strategic planning, process optimization, technology adoption, employee empowerment, and a commitment to continuous improvement. By focusing on both doing things right (efficiency) and doing the right things (effectiveness), organizations can create efficient, effective, and sustainable operations that drive profitability and deliver exceptional customer value. The journey towards optimizing both efficiency and effectiveness is ongoing, requiring consistent monitoring, adaptation, and a commitment to continuous improvement in all aspects of the operations. Ultimately, the success of any organization hinges on its ability to master this delicate balance.
Latest Posts
Latest Posts
-
Under What Conditions Are Gases Most Likely To Behave Ideally
May 08, 2025
-
Vinny And Sandra Have Just Had Their First Baby
May 08, 2025
-
Mr And Mrs Garcia Took Their Three
May 08, 2025
-
This Guidance Identifies Federal Information Security Controls
May 08, 2025
-
Particle P Moves Along The X Axis Such That
May 08, 2025
Related Post
Thank you for visiting our website which covers about What Are Two Goals Of Operations Management . We hope the information provided has been useful to you. Feel free to contact us if you have any questions or need further assistance. See you next time and don't miss to bookmark.