Turbine Blades Mounted To A Rotating Disc
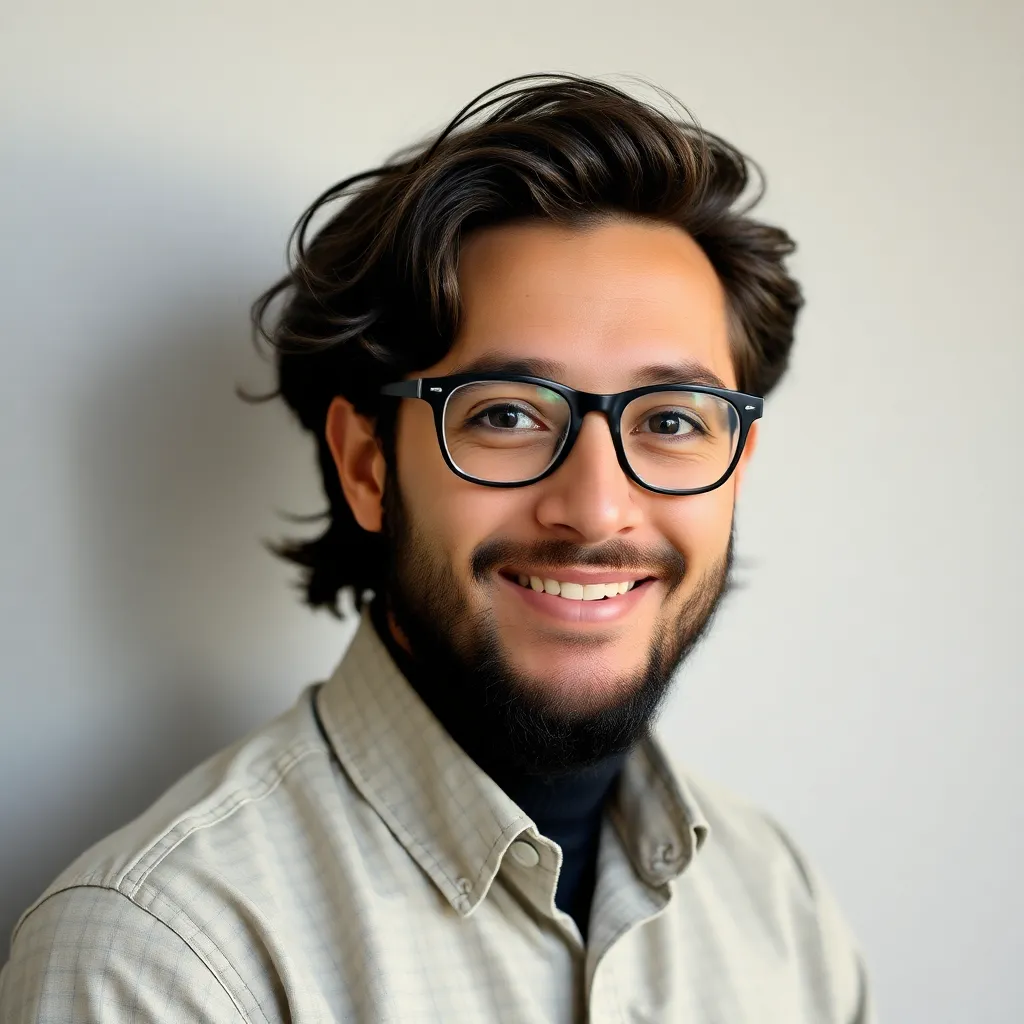
Holbox
Apr 04, 2025 · 7 min read

Table of Contents
- Turbine Blades Mounted To A Rotating Disc
- Table of Contents
- Turbine Blades Mounted to a Rotating Disc: A Deep Dive into Design, Manufacturing, and Operation
- The Rotating Disc: The Foundation of Power
- Material Selection: A Balancing Act
- Disc Design: Optimizing for Strength and Weight
- Turbine Blades: The Heart of Energy Conversion
- Aerodynamic Design: Efficiency and Performance
- Material Considerations: Withstanding Extreme Conditions
- Blade Cooling Techniques: Managing High Temperatures
- Mounting the Blades: A Precise and Critical Process
- Ensuring Secure Attachment: Avoiding Catastrophic Failure
- Advanced Manufacturing Techniques: Precision and Efficiency
- Ongoing Research and Development: Pushing the Boundaries
- Conclusion: A Complex Interplay of Engineering Disciplines
- Latest Posts
- Latest Posts
- Related Post
Turbine Blades Mounted to a Rotating Disc: A Deep Dive into Design, Manufacturing, and Operation
Turbine blades, mounted to a rotating disc, form the heart of countless power generation and propulsion systems. From the massive turbines driving power plants to the smaller, high-speed engines powering aircraft, the design, manufacture, and operation of these components are critical for efficiency, reliability, and longevity. This article will delve into the intricacies of this crucial assembly, exploring the challenges and advancements in this sophisticated field.
The Rotating Disc: The Foundation of Power
The rotating disc, often referred to as the rotor, serves as the structural backbone for the turbine blades. It's a high-precision component subjected to extreme centrifugal forces, high temperatures, and potentially corrosive environments. The materials chosen for the disc are critical, balancing strength, weight, and resistance to fatigue and creep. Common materials include nickel-based superalloys, titanium alloys, and even advanced ceramics for specialized applications.
Material Selection: A Balancing Act
The selection of the disc material is a complex process involving trade-offs between various properties:
- High Strength: The disc must withstand the immense centrifugal forces generated during operation, preventing catastrophic failure.
- High Temperature Resistance: Turbine discs operate at elevated temperatures, often exceeding 1000°C (1832°F). The material must retain its strength and resist creep (slow deformation under stress) at these temperatures.
- Creep Resistance: Long-term operation at high temperatures causes creep, leading to gradual deformation and potential failure. Materials with exceptional creep resistance are crucial.
- Fatigue Resistance: Repeated cycles of stress and strain can lead to fatigue cracks and eventual failure. High fatigue resistance is vital for long operational life.
- Corrosion Resistance: Depending on the application, the disc may be exposed to corrosive environments, requiring materials with suitable corrosion resistance.
- Forgeability & Machinability: The material needs to be readily forgeable into the complex shape of the disc and machinable for precision finishing.
Disc Design: Optimizing for Strength and Weight
The design of the rotating disc is critical for minimizing weight while maximizing strength. Sophisticated computational fluid dynamics (CFD) and finite element analysis (FEA) are used to optimize the disc's geometry, minimizing stress concentrations and maximizing its ability to withstand centrifugal forces. Common design features include:
- Variable Thickness: The disc's thickness is often varied across its radius, with a thicker section near the hub to withstand higher stresses.
- Internal Cooling Channels: For high-temperature applications, internal cooling channels are incorporated into the disc to manage temperature gradients and prevent excessive thermal stresses.
- Airfoils & Features: Certain designs incorporate carefully sculpted airfoils or other aerodynamic features to improve air flow and cooling efficiency.
Turbine Blades: The Heart of Energy Conversion
Turbine blades are the actual energy conversion elements. They are aerodynamically shaped to extract energy from a flowing gas or fluid (steam, air, etc.), converting its kinetic energy into rotational energy. Their design is extremely complex, involving careful consideration of aerodynamics, thermodynamics, and materials science.
Aerodynamic Design: Efficiency and Performance
The aerodynamic design of turbine blades is crucial for optimizing efficiency. This involves:
- Airfoil Shape: The shape of the airfoil is optimized to efficiently extract energy from the flowing fluid, maximizing lift and minimizing drag.
- Blade Angle: The angle of the blade relative to the flow direction is critical for effective energy extraction. This angle often varies along the blade's span (from root to tip) to account for changes in flow velocity and pressure.
- Blade Profile: The precise curvature of the blade's surface is carefully designed to optimize the flow of the fluid over the blade, reducing losses and maximizing efficiency.
- Cascading Effect: The arrangement of multiple blades in a cascade configuration is studied meticulously, as the wake of one blade will influence the performance of the next.
Material Considerations: Withstanding Extreme Conditions
Turbine blades, like the disc, face extreme conditions:
- High Temperature Strength: They must withstand the high temperatures of the flowing gas, maintaining their strength and dimensional stability.
- Oxidation Resistance: At high temperatures, blades are susceptible to oxidation, which weakens the material. Protective coatings are often applied.
- Corrosion Resistance: Depending on the application, blades might be exposed to corrosive gases or particles. Corrosion-resistant materials and coatings are used.
- Thermal Fatigue Resistance: Repeated heating and cooling cycles lead to thermal fatigue, potentially causing cracks. Materials and designs that minimize thermal stresses are crucial.
Blade Cooling Techniques: Managing High Temperatures
Cooling techniques are paramount for high-temperature applications. Several strategies are employed:
- Internal Cooling Channels: Complex networks of internal cooling channels are designed to circulate cool air or gas through the blade, removing heat and maintaining a lower operating temperature.
- Film Cooling: Small holes on the blade's surface inject cool air to create a protective film of cool air, reducing heat transfer to the blade material.
- Impingement Cooling: Jets of cool air are directed at the blade's surface, rapidly removing heat.
Mounting the Blades: A Precise and Critical Process
Mounting the turbine blades to the rotating disc is a crucial step, demanding high precision and robust attachment mechanisms. Several methods are employed:
- Fir-Tree Root: This is a common method, where the blade's root features a complex "fir-tree" shape that interlocks with corresponding slots in the disc. This provides a strong, secure connection that can withstand high centrifugal forces.
- Integral Blading: This advanced technique involves casting or forging the blades directly into the disc, eliminating the need for separate attachment mechanisms. This offers superior strength and fatigue resistance.
- Dovetail Joint: A simpler and often more readily manufactured solution, this uses a dovetail shape for secure attachment. However, it is generally less robust than other methods.
- Blisk (Blade-Integrated Disk): This is an advanced manufacturing technique that integrates the blades and the disk into a single piece, improving strength and efficiency, reducing assembly and reducing the number of parts.
Ensuring Secure Attachment: Avoiding Catastrophic Failure
The connection between the blade and the disc must be exceptionally strong and reliable. Any loosening or failure of this connection can result in catastrophic damage to the turbine. Advanced techniques such as:
- Precise tolerances and manufacturing processes: To ensure perfect fitting and secure attachment.
- High-strength materials: Used in the blade root and the disc to maximize strength and fatigue resistance.
- Protective Coatings: To prevent corrosion and oxidation at the interface.
- Non-destructive testing (NDT): Such as ultrasonic testing, is routinely employed to detect any defects or flaws in the connection.
Advanced Manufacturing Techniques: Precision and Efficiency
The manufacture of turbine blades and discs demands high precision and advanced manufacturing techniques. Several methods are used:
- Investment Casting: A precise method used to create complex blade shapes with intricate internal cooling channels.
- Forging: Used to create strong and durable discs with tailored microstructure.
- Additive Manufacturing (3D Printing): Emerging as a powerful technique for creating complex geometries and intricate internal cooling channels. This is increasingly used to improve performance and reduce material waste.
- Machining: Used to finish and precisely shape blades and discs.
Ongoing Research and Development: Pushing the Boundaries
Research and development in turbine blade and disc technology is ongoing. Focus areas include:
- Advanced Materials: Exploring new materials with higher temperature capabilities, improved creep and fatigue resistance. This includes advanced ceramics and composites.
- Improved Cooling Techniques: Developing more efficient cooling strategies to further increase operating temperatures and efficiency.
- Advanced Manufacturing Processes: Implementing additive manufacturing and other techniques to create more complex and efficient designs.
- Computational Modeling: Refining CFD and FEA techniques for more accurate predictions of performance and lifespan.
Conclusion: A Complex Interplay of Engineering Disciplines
The design, manufacturing, and operation of turbine blades mounted to a rotating disc represent a complex interplay of several engineering disciplines. From materials science and aerodynamics to manufacturing processes and computational modeling, continuous innovation is crucial for pushing the boundaries of efficiency, reliability, and longevity in power generation and propulsion systems. The quest for lighter, stronger, and more efficient turbines continues to drive advancements in this vital field. The focus remains on enhancing performance, lifespan, and reducing environmental impact across diverse applications. The future promises even more sophisticated designs and materials, enabling more powerful and efficient turbines for generations to come.
Latest Posts
Latest Posts
-
Which Of The Following Is A Web App
Apr 07, 2025
-
2 Methyl 4 1 Methylethyl Octane
Apr 07, 2025
-
The Demand Curve Focuses Entirely On The
Apr 07, 2025
-
A Nation Based On Individualism Would Agree That
Apr 07, 2025
-
The Deflection Plates In An Oscilloscope
Apr 07, 2025
Related Post
Thank you for visiting our website which covers about Turbine Blades Mounted To A Rotating Disc . We hope the information provided has been useful to you. Feel free to contact us if you have any questions or need further assistance. See you next time and don't miss to bookmark.