Three Broad Categories Of Definitions Of Quality Are
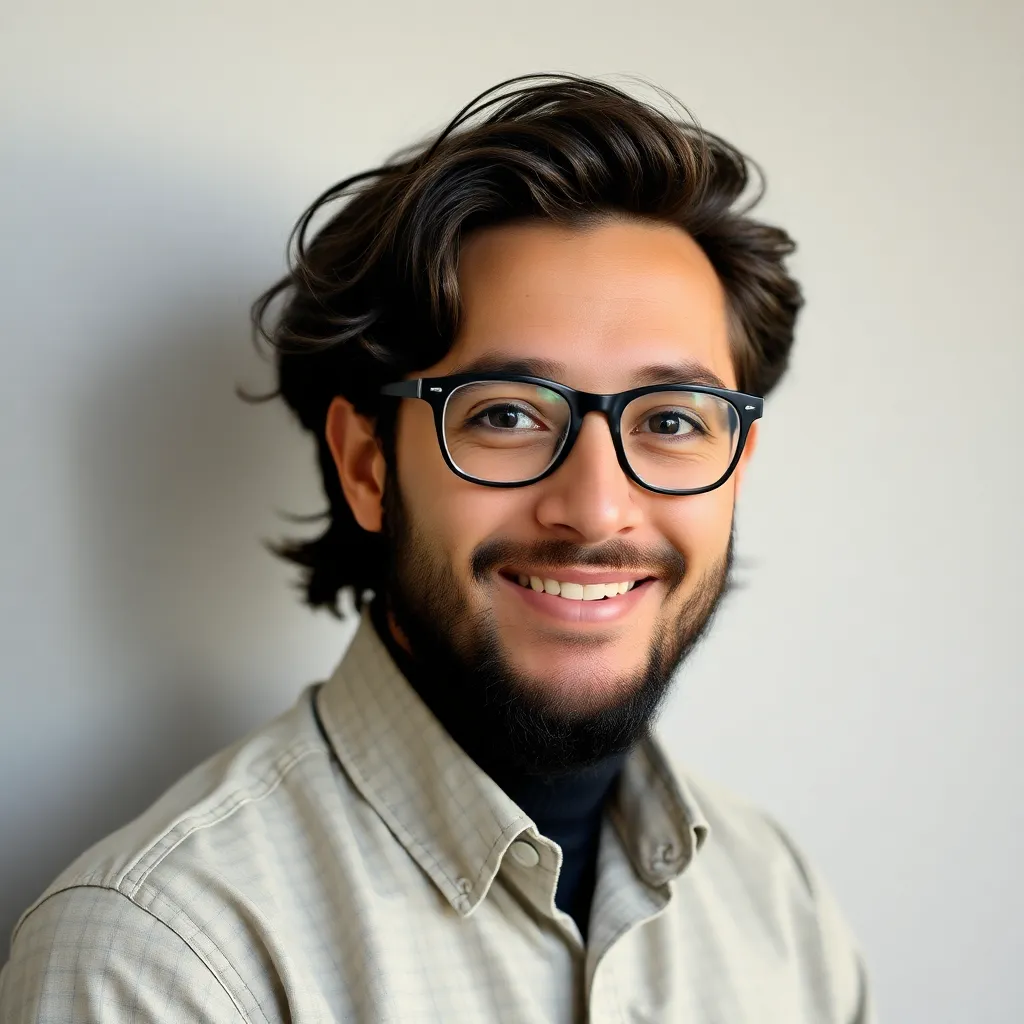
Holbox
Apr 04, 2025 · 7 min read

Table of Contents
- Three Broad Categories Of Definitions Of Quality Are
- Table of Contents
- Three Broad Categories of Definitions of Quality
- 1. User-Based Definitions of Quality: Meeting Customer Needs and Expectations
- Understanding Customer Needs and Expectations
- Key Aspects of User-Based Quality
- The Importance of User Feedback
- 2. Manufacturing-Based Definitions of Quality: Focusing on Process and Production
- Key Aspects of Manufacturing-Based Quality
- Tools and Techniques for Manufacturing-Based Quality
- The Role of Technology
- 3. Product-Based Definitions of Quality: Focusing on Inherent Attributes
- Key Aspects of Product-Based Quality
- Measuring Product-Based Quality
- Limitations of Product-Based Definitions
- Integrating the Three Approaches
- Latest Posts
- Latest Posts
- Related Post
Three Broad Categories of Definitions of Quality
Defining "quality" is surprisingly complex. While we intuitively understand high-quality products or services, pinning down a precise, universally accepted definition proves elusive. The concept of quality shifts depending on the context, perspective, and even the historical period. However, we can categorize the numerous definitions of quality into three broad categories: user-based, manufacturing-based, and product-based. Understanding these distinctions is crucial for businesses striving to deliver exceptional products and services and for consumers seeking informed purchasing decisions.
1. User-Based Definitions of Quality: Meeting Customer Needs and Expectations
User-based definitions of quality center on the customer's perception and satisfaction. It's not about inherent attributes of a product or service but rather how well it fulfills the user's needs and expectations. This approach emphasizes the subjective nature of quality, recognizing that different customers may have vastly different requirements.
Understanding Customer Needs and Expectations
The cornerstone of user-based quality is a deep understanding of customer needs. This involves:
- Market research: Conducting thorough market research to identify target audiences, their preferences, pain points, and desired features. Surveys, focus groups, and interviews are valuable tools here.
- Competitive analysis: Analyzing competitors' offerings to understand what aspects customers value and where improvements can be made.
- Customer feedback mechanisms: Establishing robust systems for gathering customer feedback, such as online reviews, surveys, and direct communication channels.
Key Aspects of User-Based Quality
Several key aspects contribute to a positive user experience and, therefore, a high-quality perception:
- Performance: Does the product or service perform as expected? Does it meet its intended purpose effectively and efficiently? For a car, this might include fuel efficiency, speed, and handling. For software, it might involve ease of use and functionality.
- Features: Does the product or service offer the features and functionalities that customers desire? This often involves balancing essential features with desirable extras.
- Reliability: Is the product or service dependable and consistent in its performance over time? Reliability is crucial for building trust and customer loyalty.
- Conformance: Does the product or service meet the specified requirements and standards? This aspect bridges the gap between user-based and product-based definitions.
- Durability: How long-lasting is the product or service? This is particularly important for tangible goods but also applies to the longevity and support of software or services.
- Serviceability: How easy is it to maintain, repair, or receive support for the product or service? Excellent customer service is a significant factor influencing user perception.
- Aesthetics: Does the product or service appeal to the customer's sense of style and aesthetics? This can be particularly relevant for consumer goods and design-focused products.
The Importance of User Feedback
Continuous monitoring of customer feedback is vital for maintaining and improving user-based quality. Analyzing this feedback helps identify areas for improvement, address customer complaints, and proactively develop new features or functionalities that meet evolving needs.
Example: A smartphone manufacturer might prioritize battery life, camera quality, and user-friendly interface based on user feedback and market trends. Ignoring these aspects, even if the phone boasts cutting-edge technology internally, will likely lead to negative customer reviews and lower sales.
2. Manufacturing-Based Definitions of Quality: Focusing on Process and Production
Manufacturing-based definitions emphasize the processes and methods used in creating a product or delivering a service. This approach focuses on minimizing defects, improving efficiency, and adhering to strict standards throughout the production chain. Quality is seen as a result of a well-managed and controlled process.
Key Aspects of Manufacturing-Based Quality
Several key elements characterize this approach:
- Process control: Implementing rigorous quality control measures at each stage of production to detect and correct defects early. This often involves statistical process control (SPC) techniques.
- Defect prevention: Focusing on preventing defects rather than simply detecting and correcting them. This proactive approach leads to greater efficiency and higher quality.
- Standardization: Implementing standardized procedures and processes to ensure consistency and predictability in the manufacturing process.
- Automation: Utilizing automation to reduce human error and improve the speed and consistency of production.
- Continuous improvement: Embracing a culture of continuous improvement (Kaizen) to constantly refine processes and improve efficiency and quality. Lean manufacturing principles often play a significant role here.
- Supplier management: Carefully selecting and managing suppliers to ensure the quality of raw materials and components used in production.
Tools and Techniques for Manufacturing-Based Quality
Various tools and techniques are employed to achieve high manufacturing-based quality:
- Six Sigma: A data-driven methodology aimed at reducing variation and defects in processes.
- Total Quality Management (TQM): A comprehensive approach to quality management that involves all aspects of the organization.
- ISO 9000: A series of international standards that provide a framework for quality management systems. Certification demonstrates commitment to quality.
The Role of Technology
Technology plays a crucial role in modern manufacturing-based quality control. This includes:
- Automated inspection systems: Using automated systems to inspect products for defects with greater speed and accuracy than manual inspection.
- Data analytics: Analyzing production data to identify trends, predict potential problems, and optimize processes.
- Robotics: Employing robots to perform repetitive tasks with high precision and consistency.
Example: A car manufacturer might use robotic welding to ensure consistent weld quality, employ statistical process control to monitor engine assembly, and implement rigorous testing procedures to ensure the safety and reliability of its vehicles. These processes contribute to a high level of manufacturing-based quality.
3. Product-Based Definitions of Quality: Focusing on Inherent Attributes
Product-based definitions emphasize the inherent characteristics and attributes of a product or service. This approach focuses on objective, measurable qualities of the product itself, regardless of customer perceptions or manufacturing processes.
Key Aspects of Product-Based Quality
Key characteristics defining product-based quality include:
- Performance: The product's ability to meet its intended purpose effectively. This often involves objective measurements, such as speed, efficiency, or accuracy.
- Reliability: The product's consistency and dependability over time. This can be measured through mean time between failures (MTBF) or other statistical measures.
- Durability: The product's ability to withstand wear and tear and remain functional over an extended period.
- Features: The product's attributes and functionalities. These can be objectively described and quantified.
- Conformance: The degree to which the product meets pre-defined specifications and standards. This often involves precise measurements and tolerances.
- Aesthetics: The product's visual appeal and design. While subjective, certain aspects, such as symmetry or color consistency, can be objectively measured.
Measuring Product-Based Quality
Measuring product-based quality involves using objective metrics and standards:
- Dimensional measurements: Measuring physical dimensions, such as length, width, and height, to ensure conformance to specifications.
- Performance testing: Conducting tests to assess the product's performance under various conditions.
- Durability testing: Subjecting the product to simulated wear and tear to assess its longevity.
- Material analysis: Analyzing the composition and properties of materials used in the product.
Limitations of Product-Based Definitions
While product-based definitions offer objectivity, they have limitations:
- Ignoring customer needs: Focus solely on product attributes may neglect crucial aspects of customer satisfaction. A perfectly manufactured product might still fail to meet customer needs or expectations.
- Difficulty in capturing all aspects: Some aspects of quality, such as aesthetics or user-friendliness, are difficult to quantify objectively.
- Limited applicability to services: Product-based definitions are less applicable to services, which are intangible and less easily measured.
Example: A manufacturer of precision instruments might define quality based on factors such as accuracy, repeatability, and sensitivity, measured through rigorous testing and calibration procedures. The focus is on meeting strict technical specifications, irrespective of customer perception.
Integrating the Three Approaches
Ideally, a comprehensive approach to quality management integrates all three definitions: user-based, manufacturing-based, and product-based. Understanding customer needs (user-based) guides product design and development. Efficient manufacturing processes (manufacturing-based) ensure consistent product quality, and objective measures (product-based) provide a benchmark for performance. This holistic view leads to superior products and services that satisfy customers and deliver long-term business success. The constant feedback loop between these three approaches ensures continuous improvement and a robust quality management system. A company that masters this integration will be well-positioned to thrive in today's competitive market.
Latest Posts
Latest Posts
-
The Main Focus Of Nihs Conflict Of Interest Policy Is
Apr 14, 2025
-
Data Concerning Follick Corporations Single Product Appear Below
Apr 14, 2025
-
Gig Harbor Boating Is The Wholesale Distributor
Apr 14, 2025
-
Which Of The Following Characters Precedes Excel Functions
Apr 14, 2025
-
Diseases In Focus Chapter 25 Male Age 49
Apr 14, 2025
Related Post
Thank you for visiting our website which covers about Three Broad Categories Of Definitions Of Quality Are . We hope the information provided has been useful to you. Feel free to contact us if you have any questions or need further assistance. See you next time and don't miss to bookmark.