Theory And Design For Mechanical Measurements
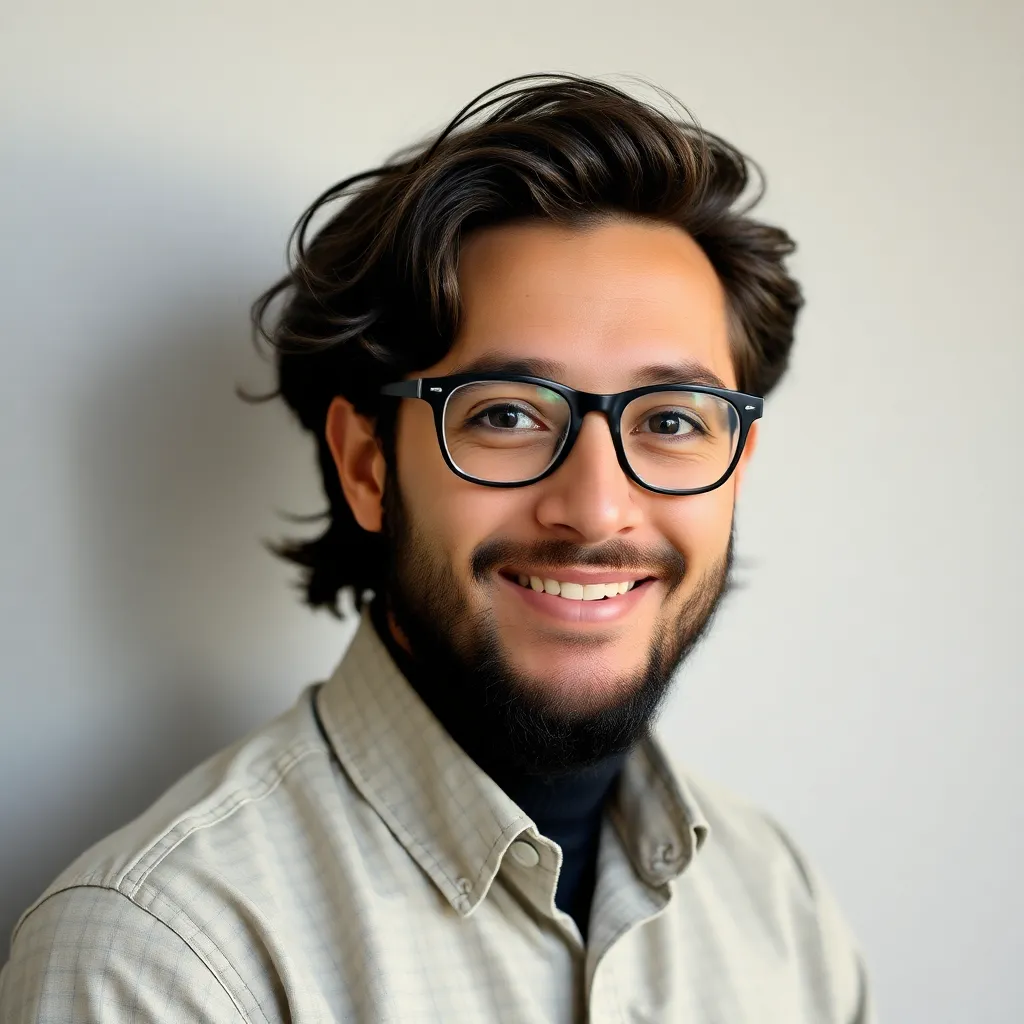
Holbox
May 09, 2025 · 8 min read
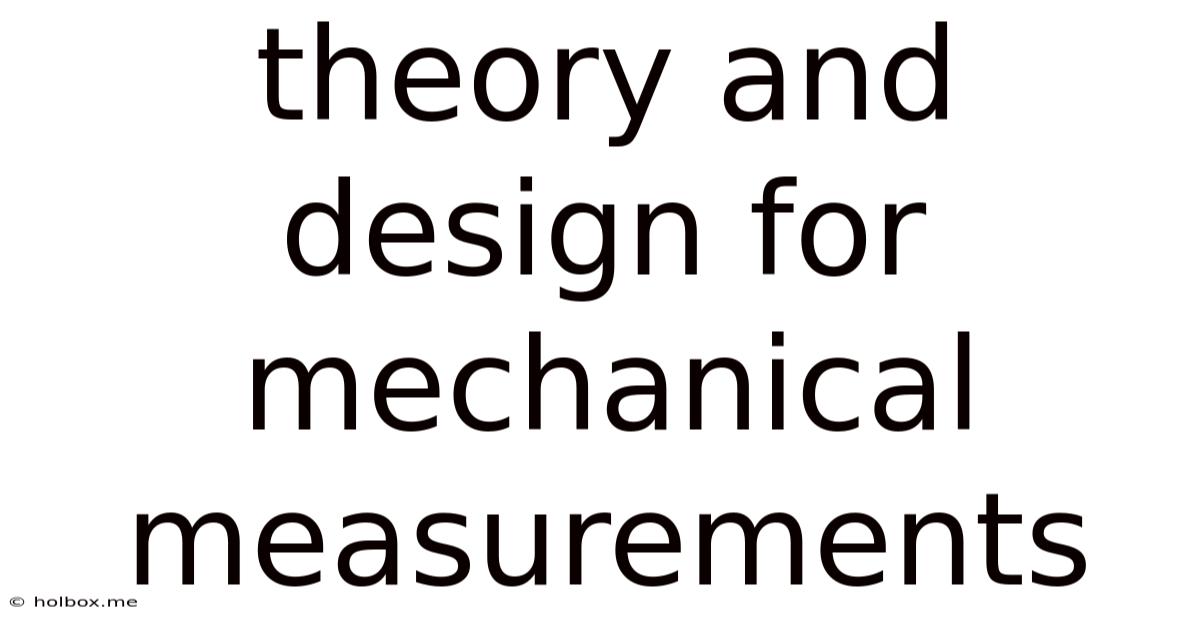
Table of Contents
- Theory And Design For Mechanical Measurements
- Table of Contents
- Theory and Design for Mechanical Measurements
- Fundamental Principles of Mechanical Measurement
- Accuracy and Precision
- Calibration and Error Analysis
- Static and Dynamic Characteristics
- Types of Mechanical Measurement Systems
- Strain Gauges
- Load Cells
- Pressure Sensors
- Accelerometers
- Displacement Sensors
- Design Considerations for Mechanical Measurement Systems
- Selection of Sensors and Transducers
- Signal Conditioning and Amplification
- Data Acquisition and Processing
- System Integration and Calibration
- Environmental Considerations
- Cost and Maintainability
- Advanced Topics in Mechanical Measurement
- Digital Signal Processing (DSP)
- Uncertainty Analysis
- Non-Destructive Testing (NDT)
- Conclusion
- Latest Posts
- Latest Posts
- Related Post
Theory and Design for Mechanical Measurements
Mechanical measurements form the bedrock of numerous engineering disciplines, providing crucial data for design, analysis, and control. Understanding the underlying theory and principles of design is paramount for obtaining accurate, reliable, and meaningful results. This comprehensive guide delves into the theoretical foundations and practical considerations involved in designing effective mechanical measurement systems.
Fundamental Principles of Mechanical Measurement
Before diving into specific designs, it's vital to grasp the fundamental principles governing mechanical measurements. These principles ensure the accuracy, precision, and reliability of the obtained data.
Accuracy and Precision
Accuracy refers to how close a measured value is to the true value. A highly accurate measurement minimizes systematic errors, which are consistent and repeatable deviations from the true value. Sources of systematic errors include instrument calibration errors, environmental factors (temperature, pressure), and inherent biases in the measurement process.
Precision, on the other hand, reflects the reproducibility of measurements. High precision indicates minimal random errors, which are unpredictable variations in measurements. Random errors arise from factors like noise, vibrations, and limitations in the resolution of the measuring instrument. While precision is essential, it doesn't guarantee accuracy. A measurement system can be highly precise but inaccurate if a significant systematic error is present.
Calibration and Error Analysis
Calibration is a crucial step in ensuring the accuracy of mechanical measurement systems. It involves comparing the instrument's readings against known standards, allowing for the identification and correction of systematic errors. Regular calibration is essential to maintain accuracy over time, particularly with instruments that are subject to wear and tear or environmental influences.
Error analysis is a systematic process for identifying, quantifying, and minimizing errors in measurements. This involves understanding the different sources of error (systematic and random) and their potential impact on the overall accuracy of the results. Statistical methods, such as calculating standard deviations and confidence intervals, are often used to quantify uncertainty in the measurements.
Static and Dynamic Characteristics
Mechanical measurement systems can be characterized by their static and dynamic characteristics.
Static characteristics describe the system's behavior under constant or slowly changing conditions. Key parameters include:
- Sensitivity: The change in output for a unit change in the input. A high sensitivity indicates a greater response to variations in the measured quantity.
- Linearity: How well the output of the system is a linear function of the input. Deviations from linearity represent non-linearity errors.
- Range: The span of input values over which the system can operate accurately.
- Threshold: The minimum input required to produce a detectable output.
- Hysteresis: The difference in output for the same input when approached from different directions.
Dynamic characteristics describe the system's response to time-varying inputs. Important parameters include:
- Frequency Response: The range of frequencies over which the system accurately measures the input. A system with a limited frequency response may not accurately capture rapid changes in the measured quantity.
- Time Constant: A measure of how quickly the system responds to changes in the input. A shorter time constant implies a faster response.
- Damping: The dissipation of energy within the system, which affects its response to oscillations.
Types of Mechanical Measurement Systems
Mechanical measurement systems are diverse, each tailored to specific applications and measurement requirements. Here are some examples:
Strain Gauges
Strain gauges are widely used for measuring strain, which is a measure of deformation under stress. They operate based on the principle that the electrical resistance of a conductor changes when it is subjected to strain. Strain gauges are typically bonded to the surface of the object being measured and connected to a Wheatstone bridge circuit to convert the resistance change into a measurable voltage. They are incredibly versatile and find applications in stress analysis, load cells, and pressure sensors.
Load Cells
Load cells are transducers used for measuring force. They typically employ strain gauges bonded to a load-bearing element, such as a beam or column. When a force is applied, the element deforms, causing a change in resistance in the strain gauges. This change is then converted into a force measurement. Load cells are essential components in weighing scales, testing machines, and robotic systems.
Pressure Sensors
Pressure sensors measure pressure by utilizing various transduction mechanisms. Common types include:
- Bourdon tube pressure gauges: These devices use a curved tube that straightens when pressure is applied. The movement of the tube is mechanically linked to a pointer that indicates the pressure.
- Diaphragm pressure sensors: These sensors use a flexible diaphragm that deflects under pressure. The deflection is measured using various methods, such as capacitive sensing, resistive sensing, or optical sensing.
- Piezoresistive pressure sensors: These sensors use a piezoresistive material whose resistance changes with applied pressure.
Pressure sensors find widespread use in industrial control systems, automotive applications, and medical devices.
Accelerometers
Accelerometers measure acceleration, either linear or angular. Microelectromechanical systems (MEMS) accelerometers are increasingly common, utilizing capacitive or piezoresistive sensing to detect changes in acceleration. They are crucial components in inertial measurement units (IMUs), which are used in navigation systems, motion tracking, and vibration monitoring.
Displacement Sensors
Displacement sensors measure the distance or position of an object. Various technologies are used, including:
- Linear Variable Differential Transformer (LVDT): An electromagnetic device that provides a high-accuracy, non-contact measurement of linear displacement.
- Potentiometers: These devices use a variable resistor whose resistance changes with the position of a sliding contact.
- Capacitive sensors: These sensors measure the change in capacitance between two electrodes as the distance between them changes.
- Optical sensors: These sensors use light to measure displacement, often employing techniques like triangulation or interferometry.
Design Considerations for Mechanical Measurement Systems
Designing an effective mechanical measurement system involves careful consideration of several factors:
Selection of Sensors and Transducers
The choice of sensors and transducers depends on the specific measurement requirements, such as the type of quantity being measured (force, pressure, displacement, etc.), the required accuracy, the range of measurement, and the environmental conditions. Careful consideration must be given to the sensor's sensitivity, linearity, and frequency response to ensure it meets the application needs.
Signal Conditioning and Amplification
The signals from sensors often require conditioning and amplification before they can be processed and displayed. Signal conditioning may involve filtering noise, linearizing non-linear responses, and converting the signal to a suitable format for data acquisition. Amplification increases the signal strength to improve the signal-to-noise ratio and enhance the accuracy of the measurement.
Data Acquisition and Processing
Data acquisition involves collecting the processed signals from the sensors. This may involve the use of analog-to-digital converters (ADCs) to convert analog signals into digital data that can be processed by a computer or microcontroller. Data processing involves analyzing the acquired data to extract meaningful information, often involving filtering, smoothing, and statistical analysis.
System Integration and Calibration
Integrating the various components of the measurement system requires careful consideration of compatibility, interfacing, and communication protocols. Proper calibration of the entire system is crucial to ensure the accuracy and reliability of the measurements. This includes calibrating individual sensors and verifying the overall system response.
Environmental Considerations
Environmental factors such as temperature, humidity, vibration, and electromagnetic interference (EMI) can significantly impact the accuracy and reliability of mechanical measurement systems. Proper design should consider these factors and implement strategies to minimize their effects, such as using temperature-compensated sensors, shielding against EMI, and vibration isolation.
Cost and Maintainability
Cost is an important consideration in the design of mechanical measurement systems. The selection of components, the complexity of the system, and the required level of accuracy all contribute to the overall cost. Maintainability is also essential, ensuring that the system can be easily serviced and repaired, minimizing downtime.
Advanced Topics in Mechanical Measurement
This section briefly touches upon more advanced topics within mechanical measurements:
Digital Signal Processing (DSP)
DSP techniques play a crucial role in enhancing the accuracy and reliability of measurements by filtering noise, compensating for non-linearity, and improving the resolution of the measurements. Techniques like Fast Fourier Transforms (FFTs) are commonly employed for analyzing frequency content in signals.
Uncertainty Analysis
A comprehensive uncertainty analysis is crucial for determining the overall uncertainty associated with a measurement. This involves identifying and quantifying all sources of uncertainty, including sensor uncertainties, environmental effects, and data processing errors. This assessment provides a realistic estimate of the reliability of the obtained measurements.
Non-Destructive Testing (NDT)
Mechanical measurement techniques are widely used in NDT, which involves evaluating the integrity of materials and structures without causing damage. Techniques like ultrasonic testing, eddy current testing, and acoustic emission testing rely on mechanical measurements to assess the internal properties and detect flaws in materials.
Conclusion
The theory and design of mechanical measurement systems are multifaceted and require a solid understanding of fundamental principles, sensor technologies, and signal processing techniques. By carefully considering factors such as accuracy, precision, calibration, and environmental influences, engineers can design reliable and effective measurement systems that are crucial for various engineering applications. Continuous advancements in sensor technology and data processing techniques continue to push the boundaries of mechanical measurement, enabling more precise, efficient, and insightful measurements.
Latest Posts
Latest Posts
-
How Many Days Is 100 Years
May 20, 2025
-
102 Kg In Stones And Pounds
May 20, 2025
-
111 Kg To Stones And Pounds
May 20, 2025
-
How Many Seconds In 5 Mins
May 20, 2025
-
What Is 35 Inches In Cm
May 20, 2025
Related Post
Thank you for visiting our website which covers about Theory And Design For Mechanical Measurements . We hope the information provided has been useful to you. Feel free to contact us if you have any questions or need further assistance. See you next time and don't miss to bookmark.