The Wall Of A Drying Oven Is Constructed By Sandwiching
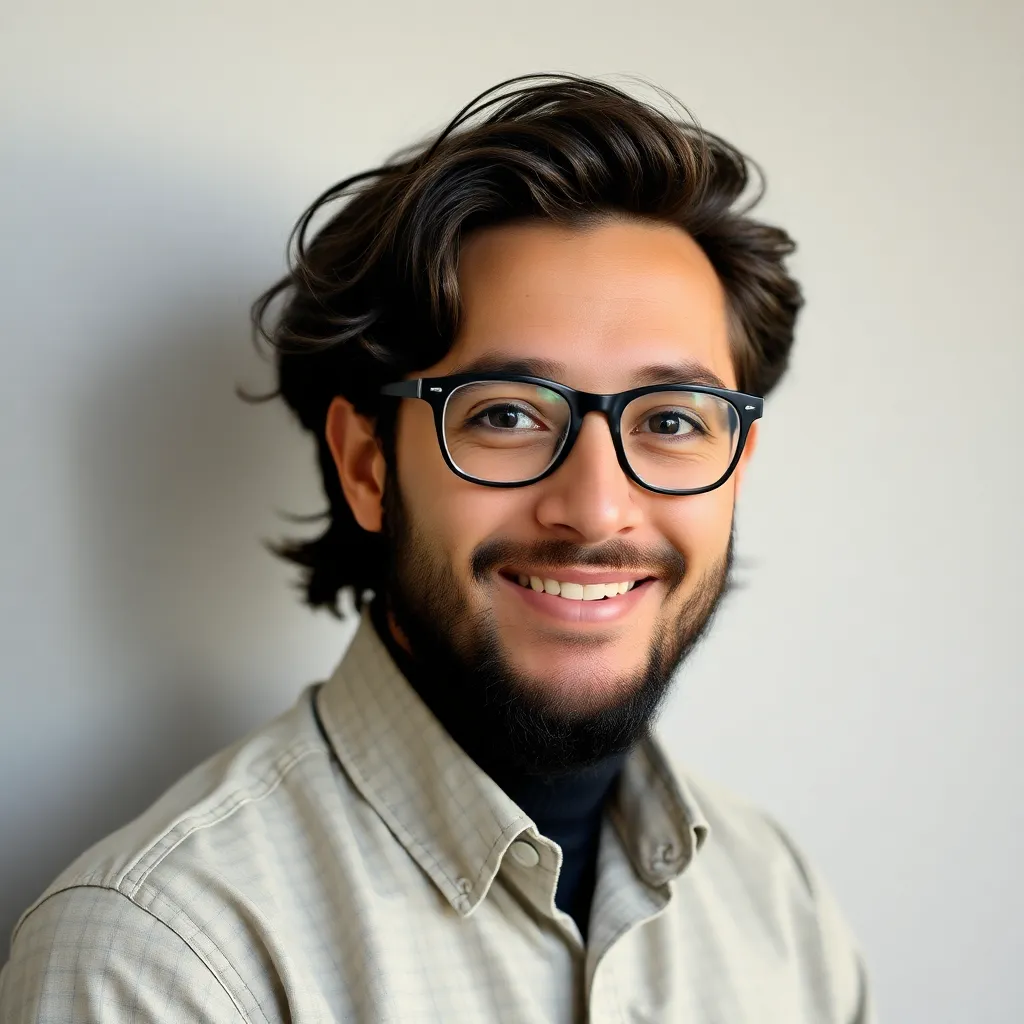
Holbox
Apr 03, 2025 · 6 min read

Table of Contents
- The Wall Of A Drying Oven Is Constructed By Sandwiching
- Table of Contents
- The Wall of a Drying Oven: A Deep Dive into Sandwich Construction
- Understanding Sandwich Panel Construction
- Material Selection for Drying Oven Walls: A Critical Analysis
- Core Materials:
- Facing Materials:
- Design Considerations for Optimal Performance
- Thermal Analysis and Optimization
- Joint Design and Sealing: Preventing Heat Loss and Moisture Ingress
- Advanced Considerations: Integration with Other Oven Components
- Conclusion: The Significance of Optimized Wall Construction
- Latest Posts
- Latest Posts
- Related Post
The Wall of a Drying Oven: A Deep Dive into Sandwich Construction
The design and construction of industrial drying ovens are critical for efficient and safe operation. A key component influencing performance, energy efficiency, and longevity is the oven's wall construction. Sandwich panel construction has emerged as a dominant method due to its numerous advantages. This article delves into the intricacies of sandwich panel construction for drying oven walls, exploring materials, design considerations, thermal performance, and the overall impact on oven functionality.
Understanding Sandwich Panel Construction
Sandwich panels, at their core, consist of three layers:
-
Core Material: This is the central layer, providing insulation and structural support. Common core materials include polyurethane (PUR), polyisocyanurate (PIR), mineral wool, and phenolic foam. Each offers unique properties in terms of thermal conductivity, compressive strength, and fire resistance.
-
Facing Materials: These are the outer layers, providing structural strength, surface protection, and aesthetic appeal. Common facing materials include galvanized steel, stainless steel, aluminum, and composite materials. The choice of facing depends on the oven's operating temperature, chemical exposure, and desired durability.
Material Selection for Drying Oven Walls: A Critical Analysis
The selection of materials for each layer of the sandwich panel significantly impacts the oven's performance and lifespan. Let's examine the pros and cons of common materials:
Core Materials:
-
Polyurethane (PUR): PUR foam is a popular choice due to its excellent thermal insulation properties, relatively low cost, and ease of processing. However, its susceptibility to moisture absorption can affect long-term performance.
-
Polyisocyanurate (PIR): PIR foam offers superior thermal performance compared to PUR, with a higher R-value for the same thickness. It also exhibits better dimensional stability and moisture resistance. However, PIR is generally more expensive than PUR.
-
Mineral Wool: Mineral wool provides excellent fire resistance and sound insulation. Its thermal performance is good, but generally not as efficient as PUR or PIR. It's a heavier material, potentially increasing structural load requirements.
-
Phenolic Foam: Phenolic foam boasts outstanding thermal insulation properties and high compressive strength. It offers excellent fire resistance and low smoke emission, making it a suitable option for high-temperature applications. However, it's typically more expensive than other core materials.
Facing Materials:
-
Galvanized Steel: Cost-effective and readily available, galvanized steel offers good corrosion resistance. However, its thermal conductivity is relatively high compared to other options. Suitable for applications with lower temperature requirements.
-
Stainless Steel: Offers superior corrosion resistance and higher temperature tolerance than galvanized steel. Its higher cost is justified in environments with aggressive chemicals or high operating temperatures.
-
Aluminum: Lightweight, corrosion-resistant, and with high thermal reflectivity, aluminum is an excellent choice for applications requiring low thermal mass. However, it can be more susceptible to damage than steel.
-
Composite Materials: Composite facings offer a blend of properties, often combining the strength of steel with the corrosion resistance of other materials. These materials can be tailored to specific application needs.
Design Considerations for Optimal Performance
Designing the walls of a drying oven using sandwich panels requires careful consideration of several factors:
-
Thermal Performance: The primary function of the oven wall is to minimize heat loss. The choice of core and facing materials, as well as panel thickness, directly influences the overall thermal efficiency. Calculations using thermal conductivity values are essential for accurate design.
-
Structural Integrity: The wall must withstand the stresses imposed by its own weight, the oven's internal pressure, and external forces. The structural design must account for the panel's compressive and shear strength, ensuring stability and preventing deformation.
-
Moisture Resistance: Moisture ingress can damage the core material and compromise the oven's performance. The design must incorporate measures to prevent moisture penetration, such as sealing joints and using moisture-resistant materials.
-
Fire Safety: The oven wall's fire resistance is crucial for safety. The choice of core and facing materials, as well as any additional fire-retardant treatments, must meet relevant safety standards.
-
Cleanability: Maintaining hygiene is critical in many drying oven applications. The choice of facing materials and the design of the wall's surface should facilitate easy cleaning and prevent the accumulation of dirt or debris.
Thermal Analysis and Optimization
A detailed thermal analysis is crucial to determine the optimal thickness and material selection for the sandwich panels. This analysis involves calculating the heat transfer through the wall, considering factors like:
- Conduction: Heat transfer through the solid materials of the panel.
- Convection: Heat transfer through air movement within the panel's structure (though minimized by the core material).
- Radiation: Heat transfer via electromagnetic waves.
Software simulations can aid in this process, allowing for the optimization of the panel design for maximum thermal efficiency and minimizing energy consumption. The analysis should also consider the operating temperature range of the oven to select appropriate materials with sufficient temperature resistance.
Joint Design and Sealing: Preventing Heat Loss and Moisture Ingress
The joints between the sandwich panels are critical points for heat loss and moisture ingress. Proper joint design and sealing are essential for maintaining the oven's thermal efficiency and longevity.
Common joint design techniques include:
- Tongue and groove joints: These offer mechanical interlock, improving structural integrity and reducing the gap for sealant.
- Overlapping joints: Simple to construct, but require careful sealing to prevent heat loss and moisture penetration.
- Recessed joints: These allow for a smooth, flush surface, making cleaning easier and reducing the accumulation of debris.
Effective sealing is achieved through the use of appropriate sealants that are compatible with the materials used in the panel construction. These sealants should be durable, resistant to high temperatures and chemicals, and capable of maintaining their sealing properties over time.
Advanced Considerations: Integration with Other Oven Components
The oven wall's design must be integrated seamlessly with other oven components such as:
- Doors: The door design must ensure a tight seal to prevent heat loss and maintain the oven's internal temperature.
- Heating elements: The positioning of heating elements must be carefully planned to ensure even heat distribution and avoid potential damage to the oven wall.
- Ventilation system: The wall construction must accommodate the ventilation system, allowing for efficient air circulation and heat removal.
- Instrumentation and control systems: The wall design should provide appropriate access points for sensors, controllers, and other instrumentation.
Conclusion: The Significance of Optimized Wall Construction
The wall of a drying oven, constructed using sandwich panels, is a critical component influencing its overall performance, efficiency, and longevity. Careful consideration of material selection, design considerations, thermal analysis, and joint design is essential for creating a robust, energy-efficient, and safe drying oven. By optimizing the sandwich panel construction, manufacturers can ensure the oven meets the specific requirements of the application while minimizing operational costs and maximizing its service life. The choice of materials and design should always be driven by a comprehensive understanding of the intended use, ensuring optimal performance and adherence to safety standards.
Latest Posts
Latest Posts
-
The Phrase Behavioral Expressions Of Distress Refers To
Apr 09, 2025
-
The Ph Scale Is A Mathematical Indicator Of
Apr 09, 2025
-
The Norton Introduction To Literature 14th Edition Pdf
Apr 09, 2025
-
A Special Order Should Be Accepted
Apr 09, 2025
-
You Have Set Up An Appointment For An In Home
Apr 09, 2025
Related Post
Thank you for visiting our website which covers about The Wall Of A Drying Oven Is Constructed By Sandwiching . We hope the information provided has been useful to you. Feel free to contact us if you have any questions or need further assistance. See you next time and don't miss to bookmark.