The Understatement Of The Beginning Inventory Balance Causes
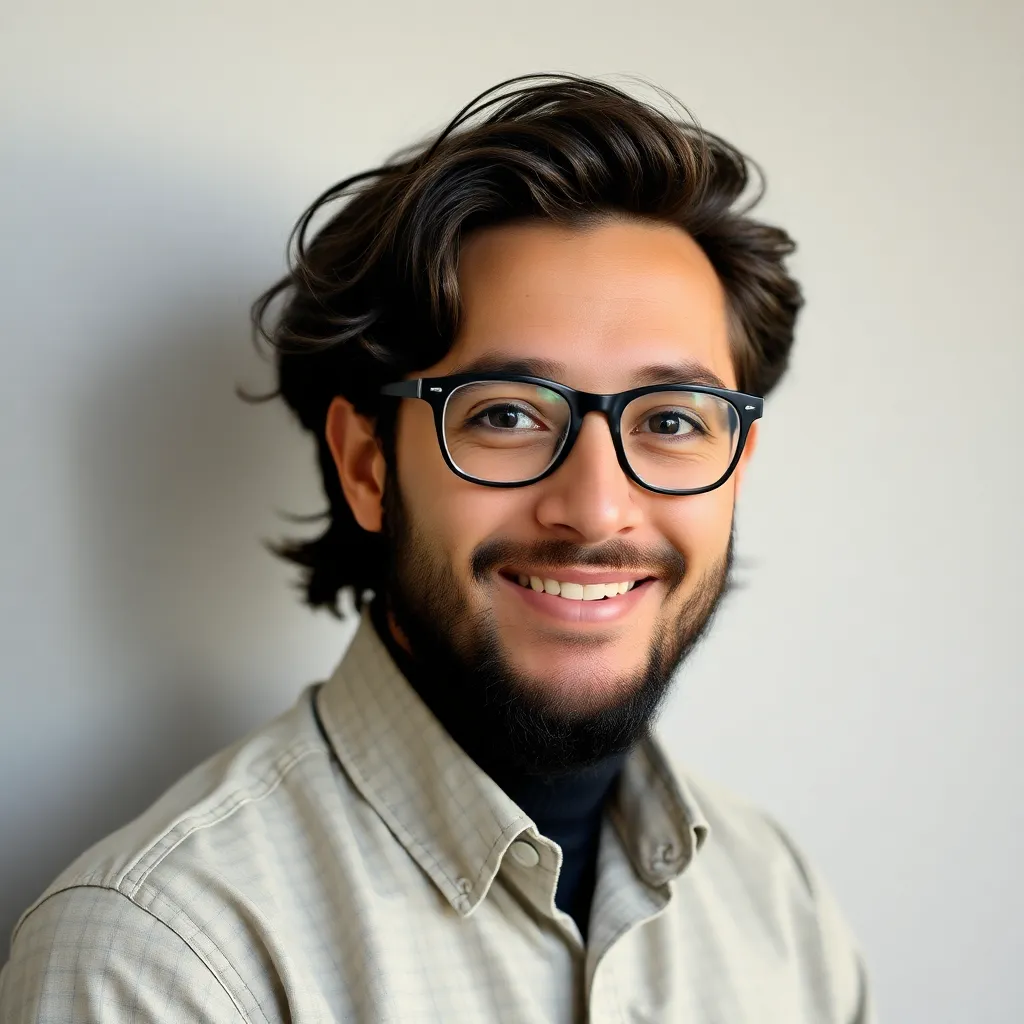
Holbox
Apr 02, 2025 · 7 min read

Table of Contents
- The Understatement Of The Beginning Inventory Balance Causes
- Table of Contents
- The Understatement of Beginning Inventory Balance: Causes, Consequences, and Corrections
- Common Causes of Beginning Inventory Understatement
- 1. Errors in Physical Inventory Counts:
- 2. Errors in Inventory Valuation Methods:
- 3. System Errors and Data Management Issues:
- 4. Intentional Misstatement:
- Consequences of Understated Beginning Inventory
- 1. Distorted Financial Statements:
- 2. Operational and Strategic Implications:
- 3. Legal and Regulatory Consequences:
- Correcting and Preventing Understatement of Beginning Inventory
- 1. Correcting the Understatement:
- 2. Preventing Future Understatements:
- Conclusion
- Latest Posts
- Latest Posts
- Related Post
The Understatement of Beginning Inventory Balance: Causes, Consequences, and Corrections
The beginning inventory balance, the value of inventory at the start of an accounting period, serves as a crucial foundation for accurate financial reporting. An understatement of this balance can trigger a domino effect, distorting financial statements and potentially leading to significant legal and operational repercussions. This comprehensive article delves into the various causes of beginning inventory understatement, its cascading consequences, and effective methods for correction and prevention.
Common Causes of Beginning Inventory Understatement
Several factors can contribute to an inaccurate, and specifically understated, beginning inventory balance. Understanding these causes is the first step towards implementing robust inventory management systems.
1. Errors in Physical Inventory Counts:
- Inaccurate Counting: Human error during the physical inventory count is a primary culprit. This can involve miscounting items, overlooking items altogether, or double-counting. The larger and more complex the inventory, the higher the risk of such errors.
- Damaged or Obsolete Goods: Failing to properly identify and account for damaged, obsolete, or near-obsolete goods leads to an understatement. These items may still be physically present but have diminished or zero value.
- Inadequate Training: Insufficient training for personnel conducting the physical count can result in inconsistent methodology and ultimately inaccurate counts. Clear procedures, regular training, and standardized forms are essential.
- Lack of Technology: Relying solely on manual counting methods in large warehouses or businesses with expansive inventory increases the likelihood of errors. Implementing barcode scanning, RFID technology, or inventory management software significantly improves accuracy.
2. Errors in Inventory Valuation Methods:
- Incorrect Costing Methods: Using an inappropriate cost flow assumption (FIFO, LIFO, weighted-average) can lead to inaccuracies. Applying the wrong method will impact the value assigned to the inventory, potentially causing an understatement.
- Miscalculation of Costs: Errors in calculating the cost of goods sold (COGS) can indirectly affect the beginning inventory. If COGS is overstated, the beginning inventory will be understated, and vice versa. This often involves incorrect allocation of overhead or direct costs.
- Ignoring Obsolescence or Damage: As mentioned earlier, failing to account for obsolescence or damage leads to an overvaluation of the existing inventory. When this happens, the stated inventory is artificially higher than its true value.
- Incorrectly Applying Lower of Cost or Market (LCM): The LCM rule mandates that inventory be valued at the lower of its historical cost or its market value. Failure to accurately apply this principle can lead to an understatement if the market value falls below the historical cost.
3. System Errors and Data Management Issues:
- Software Glitches: Bugs or errors within inventory management software can lead to incorrect data recording and reporting, potentially resulting in an understated beginning inventory. Regular software updates and testing are crucial.
- Data Entry Errors: Manual data entry carries a high risk of errors, particularly in large datasets. Simple typos or incorrect data input can significantly impact the overall inventory value.
- Lack of Data Integrity: Poor data management practices, including insufficient data validation and reconciliation processes, can allow errors to persist and accumulate, leading to a cumulative understatement of the inventory.
- Ineffective Inventory Tracking: Inadequate tracking of inventory movements (receipts, sales, returns) can cause discrepancies between the physical count and the recorded inventory levels, resulting in inaccuracies.
4. Intentional Misstatement:
- Fraudulent Activities: In some cases, the understatement of beginning inventory might be intentional. This could be motivated by a desire to inflate profits, meet financial targets, or hide losses. This is a serious ethical breach and a potential criminal offense.
- Management Pressure: Pressure from management to achieve specific financial targets can incentivize employees to manipulate inventory records, leading to intentional understatements.
Consequences of Understated Beginning Inventory
The repercussions of an understated beginning inventory balance can be far-reaching and severely impact the financial health and reputation of a business.
1. Distorted Financial Statements:
- Overstated Gross Profit: An understated beginning inventory directly leads to an overstated cost of goods sold (COGS). This, in turn, artificially inflates the gross profit margin, painting a misleading picture of profitability.
- Misleading Net Income: The overstated gross profit flows into the net income calculation, resulting in an inflated net income figure. This distorted picture of profitability affects various crucial business decisions.
- Inaccurate Inventory Turnover Ratio: The inventory turnover ratio, a key performance indicator, is distorted, leading to flawed analyses of inventory management efficiency.
- Distorted Balance Sheet: The understatement affects the balance sheet by underreporting the value of assets (inventory). This misrepresentation can mislead investors and creditors.
2. Operational and Strategic Implications:
- Poor Inventory Control: An understated inventory count hinders effective inventory management. The business might underestimate demand, leading to stockouts or overstocking, both of which are costly.
- Suboptimal Purchasing Decisions: The inaccurate inventory data leads to poor purchasing decisions, either resulting in stock shortages or excessive inventory holding costs.
- Inefficient Production Planning: In manufacturing businesses, inaccurate inventory data negatively impacts production planning, potentially leading to production delays or excess production.
- Impact on Customer Relationships: Stockouts can severely damage customer relationships, leading to lost sales and customer dissatisfaction.
3. Legal and Regulatory Consequences:
- Auditing Issues: An understated beginning inventory will likely trigger findings from external auditors, potentially leading to qualified audit opinions or even litigation.
- Securities Law Violations: If the understatement is intentional and material, it could lead to violations of securities laws, resulting in significant fines and legal action.
- Tax Implications: The understatement of inventory can have implications for tax liabilities, potentially leading to underpayment of taxes and subsequent penalties.
- Loss of Investor Confidence: If discovered, the understatement of beginning inventory significantly impacts investor and creditor confidence, potentially making it harder to secure funding in the future.
Correcting and Preventing Understatement of Beginning Inventory
Addressing an understated beginning inventory requires a multi-faceted approach focusing on correction and prevention.
1. Correcting the Understatement:
- Conduct a Thorough Physical Inventory Count: The first step involves conducting a meticulous physical inventory count, preferably using advanced technologies to minimize errors.
- Reconcile with Existing Records: Compare the results of the physical count with existing inventory records, carefully investigating and documenting any discrepancies.
- Adjust Financial Statements: After determining the extent of the understatement, adjust the affected financial statements to reflect the correct beginning inventory balance. This requires adjusting COGS, gross profit, and net income for the previous period(s).
- Implement Accounting Adjustments: Make necessary accounting entries to correct the inventory account and related accounts (COGS, etc.). Proper documentation is essential.
- Inform Stakeholders: Inform relevant stakeholders, including investors, creditors, and auditors, about the correction and its impact.
2. Preventing Future Understatements:
- Implement Robust Inventory Management Systems: Invest in reliable inventory management software that integrates with other business systems. This provides real-time visibility into inventory levels and movements.
- Regular Physical Inventory Counts: Conduct regular cyclical inventory counts, rather than relying on infrequent annual counts. This helps identify and correct errors promptly.
- Train Personnel: Provide comprehensive training to personnel involved in inventory management, emphasizing proper counting procedures, data entry techniques, and the application of inventory costing methods.
- Implement Internal Controls: Establish strong internal controls to prevent errors and fraud. This includes segregation of duties, regular audits of inventory records, and authorization controls for inventory transactions.
- Utilize Technology: Embrace barcode scanning, RFID tags, or other technologies to automate the inventory counting and tracking processes, minimizing human error.
- Continuous Monitoring and Reconciliation: Regularly monitor inventory levels and reconcile them with recorded data. This helps identify discrepancies early on, before they escalate into significant problems.
- Improved Data Management: Invest in data management practices that prioritize data integrity and validation. This includes data cleaning, data backups, and regular data reconciliation.
- Establish Clear Procedures: Create and enforce clear, documented procedures for all aspects of inventory management, from receiving goods to conducting physical counts.
Conclusion
The understatement of beginning inventory is a serious issue with potentially devastating consequences for businesses. Understanding the various causes, recognizing the potential ramifications, and proactively implementing corrective and preventative measures are crucial for ensuring the accuracy of financial reporting, maintaining operational efficiency, and safeguarding the company’s reputation and financial stability. A rigorous, technology-driven, and well-documented approach to inventory management is essential to prevent future occurrences and protect the long-term success of the enterprise. By focusing on accurate data collection, robust systems, and strong internal controls, businesses can significantly reduce the risk of beginning inventory understatement and its associated detrimental effects.
Latest Posts
Latest Posts
-
A Mathematical Sentence With An Equal Symbol Used
Apr 05, 2025
-
Which Of The Following Is Correct About Environmental Policy
Apr 05, 2025
-
The Entry For Manufacturing Overhead Cost Applied To Jobs
Apr 05, 2025
-
Suppose Banks Increase Excess Reserves By
Apr 05, 2025
-
You Want To Move The Image Around In A Slide
Apr 05, 2025
Related Post
Thank you for visiting our website which covers about The Understatement Of The Beginning Inventory Balance Causes . We hope the information provided has been useful to you. Feel free to contact us if you have any questions or need further assistance. See you next time and don't miss to bookmark.