The Two Basic Types Of Cost Accounting Systems Are
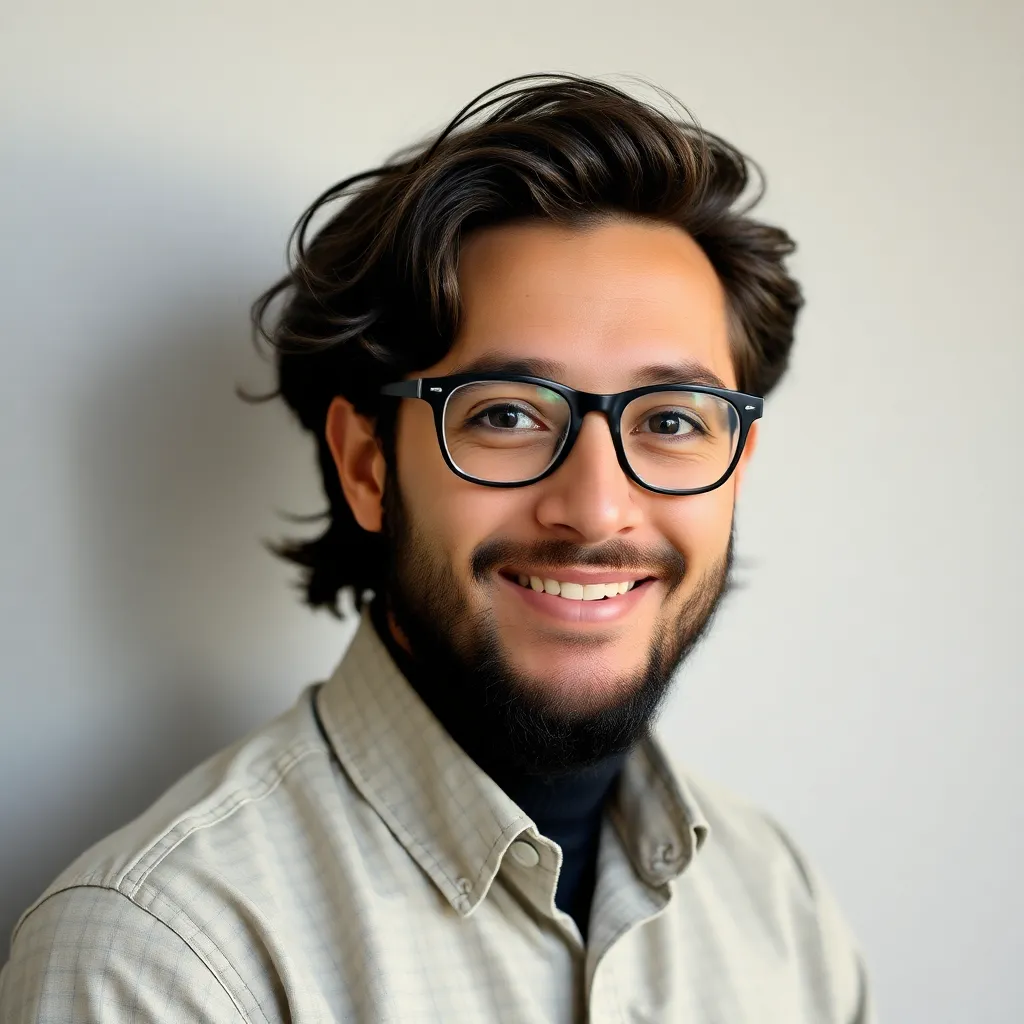
Holbox
Apr 04, 2025 · 6 min read

Table of Contents
- The Two Basic Types Of Cost Accounting Systems Are
- Table of Contents
- The Two Basic Types of Cost Accounting Systems Are: A Deep Dive into Job Order and Process Costing
- Job Order Costing: Tracking Costs for Unique Projects
- Key Characteristics of Job Order Costing:
- Advantages of Job Order Costing:
- Disadvantages of Job Order Costing:
- Process Costing: Averaging Costs for Mass Production
- Key Characteristics of Process Costing:
- Advantages of Process Costing:
- Disadvantages of Process Costing:
- Choosing the Right System: Job Order vs. Process Costing
- Hybrid Systems and Other Considerations
- Latest Posts
- Latest Posts
- Related Post
The Two Basic Types of Cost Accounting Systems Are: A Deep Dive into Job Order and Process Costing
Cost accounting, a crucial aspect of managerial accounting, plays a vital role in helping businesses understand their expenses. This understanding is fundamental for pricing products, improving efficiency, and ultimately, boosting profitability. While various cost accounting methods exist, two basic systems form the foundation: job order costing and process costing. This article will delve into the intricacies of each, exploring their applications, advantages, and limitations. We'll also highlight key distinctions to help you choose the most appropriate system for your business.
Job Order Costing: Tracking Costs for Unique Projects
Job order costing is a method used to assign costs to individual projects, jobs, or batches of products that are unique and distinct from one another. Imagine a custom furniture maker: each piece of furniture represents a unique job, with its own materials, labor, and overhead costs. This system meticulously tracks the costs associated with each job from inception to completion.
Key Characteristics of Job Order Costing:
- Individual Job Tracking: The core principle is tracking costs for each distinct job. This requires meticulous record-keeping for every element involved in the production process.
- Direct Cost Allocation: Direct materials and direct labor are easily traceable and directly assigned to specific jobs. For example, the cost of the wood used in a specific table and the labor hours spent crafting it are directly attributed to that table's cost.
- Overhead Allocation: Indirect costs, or overhead (factory rent, utilities, depreciation), are allocated to jobs based on a predetermined overhead rate. This is usually calculated by dividing total overhead costs by a chosen allocation base, such as direct labor hours or machine hours. The chosen allocation base must be carefully selected to ensure an accurate representation of overhead consumption.
- Job Cost Sheet: A critical document used in job order costing is the job cost sheet. This sheet meticulously records all costs associated with a specific job, providing a comprehensive overview of its profitability.
Advantages of Job Order Costing:
- Accurate Job Profitability: The meticulous tracking allows for precise determination of the profitability of each job, enabling businesses to identify profitable and unprofitable projects.
- Improved Pricing Decisions: Understanding the cost structure of individual jobs allows for more informed pricing decisions, ensuring both competitiveness and profitability.
- Better Inventory Management: By knowing the exact cost of each completed job, inventory valuation is simplified and accurate.
- Effective Cost Control: Detailed tracking encourages cost control and highlights areas of inefficiency within individual projects.
Disadvantages of Job Order Costing:
- Complex and Time-Consuming: The detailed record-keeping can be cumbersome and time-consuming, especially for businesses with a high volume of jobs.
- High Administrative Costs: The system requires significant administrative overhead to maintain accurate records and track costs effectively.
- Difficulty with Mass Production: It is less suitable for businesses that produce large quantities of identical products. The system becomes impractical when dealing with thousands of identical units.
- Potential for Inaccuracies: Despite the meticulous nature, errors in recording costs can significantly impact the accuracy of the final job cost.
Process Costing: Averaging Costs for Mass Production
Process costing, in stark contrast to job order costing, is best suited for businesses that produce large volumes of identical or similar products. Think of a food processing plant producing canned goods or a textile mill manufacturing fabric. In these scenarios, individual products are virtually indistinguishable, making tracking costs for each unit impractical. Instead, the average cost of producing a unit is calculated.
Key Characteristics of Process Costing:
- Averaging Costs: Costs are averaged across all units produced during a specific period, typically a month or quarter.
- Cost Accumulation by Department: Costs are accumulated by production department or process rather than by individual units.
- Equivalent Units: A key concept in process costing is equivalent units. This represents the number of completed units that could have been produced if all efforts were applied to completed units. This accounts for work-in-progress (WIP) inventory.
- Cost per Equivalent Unit: The total cost of production is divided by the total equivalent units to arrive at the cost per equivalent unit. This provides the average cost of producing a single unit.
Advantages of Process Costing:
- Simplicity and Efficiency: It's relatively simple and efficient, particularly for businesses producing high volumes of identical products.
- Cost-Effectiveness: Lower administrative overhead compared to job order costing.
- Suitable for Mass Production: Ideal for businesses with continuous production processes.
- Easy Inventory Valuation: Provides a straightforward method for valuing inventory.
Disadvantages of Process Costing:
- Less Accurate Unit Cost: Averaging costs obscures the actual cost of individual units, potentially masking inefficiencies within the production process.
- Limited Job Profitability Analysis: It does not provide a detailed breakdown of profitability for individual units or jobs.
- Inappropriate for Customized Products: Not suitable for businesses producing unique or customized products.
- Potential for Inaccuracies in Cost Allocation: Allocating costs across departments might lead to some inaccuracies if departments have significantly different cost structures.
Choosing the Right System: Job Order vs. Process Costing
The choice between job order costing and process costing hinges on the nature of your business and its production processes. Consider these factors:
- Type of Products: If you produce unique, customized products, job order costing is the appropriate choice. If you manufacture large volumes of identical or similar products, process costing is more suitable.
- Production Process: Continuous production processes with uniform outputs favor process costing, while discrete production processes with distinct jobs benefit from job order costing.
- Level of Detail Required: If detailed cost information for each job is necessary for pricing and profitability analysis, job order costing is preferable. If a general cost per unit is sufficient, process costing is adequate.
- Administrative Resources: Job order costing requires more administrative resources, while process costing is more streamlined.
Hybrid Systems and Other Considerations
While job order and process costing represent the two basic systems, businesses often employ hybrid approaches to address the specific complexities of their production environment. For example, a company might use job order costing for custom orders and process costing for standard products.
Furthermore, other cost accounting methods exist, including activity-based costing (ABC), which focuses on allocating overhead based on activities that drive costs. The selection of a specific cost accounting method is a critical decision that should align with the unique characteristics of the business and its objectives. Thorough understanding of both job order and process costing forms a strong foundation for implementing and optimizing any cost accounting system. Remember, the goal is to gain valuable insights into your cost structure to enhance profitability and make informed business decisions. Continuous evaluation and adaptation of your chosen system is vital for maintaining accuracy and relevance in a dynamic business environment. Consulting with a financial professional experienced in cost accounting can be beneficial in selecting and implementing the best system for your particular needs.
Latest Posts
Latest Posts
-
Old Economy Traders Opened An Account
Apr 08, 2025
-
Classify The Given Items With The Appropriate Group Multipolar Neuron
Apr 08, 2025
-
In General Enzymes Are What Kinds Of Molecules
Apr 08, 2025
-
Tom Is Working On A Report That Contains Employees
Apr 08, 2025
-
What Were The First Eukaryotic Organisms To Colonize On Land
Apr 08, 2025
Related Post
Thank you for visiting our website which covers about The Two Basic Types Of Cost Accounting Systems Are . We hope the information provided has been useful to you. Feel free to contact us if you have any questions or need further assistance. See you next time and don't miss to bookmark.