The Traditional Method Of Maintaining Product Quality Has Been The
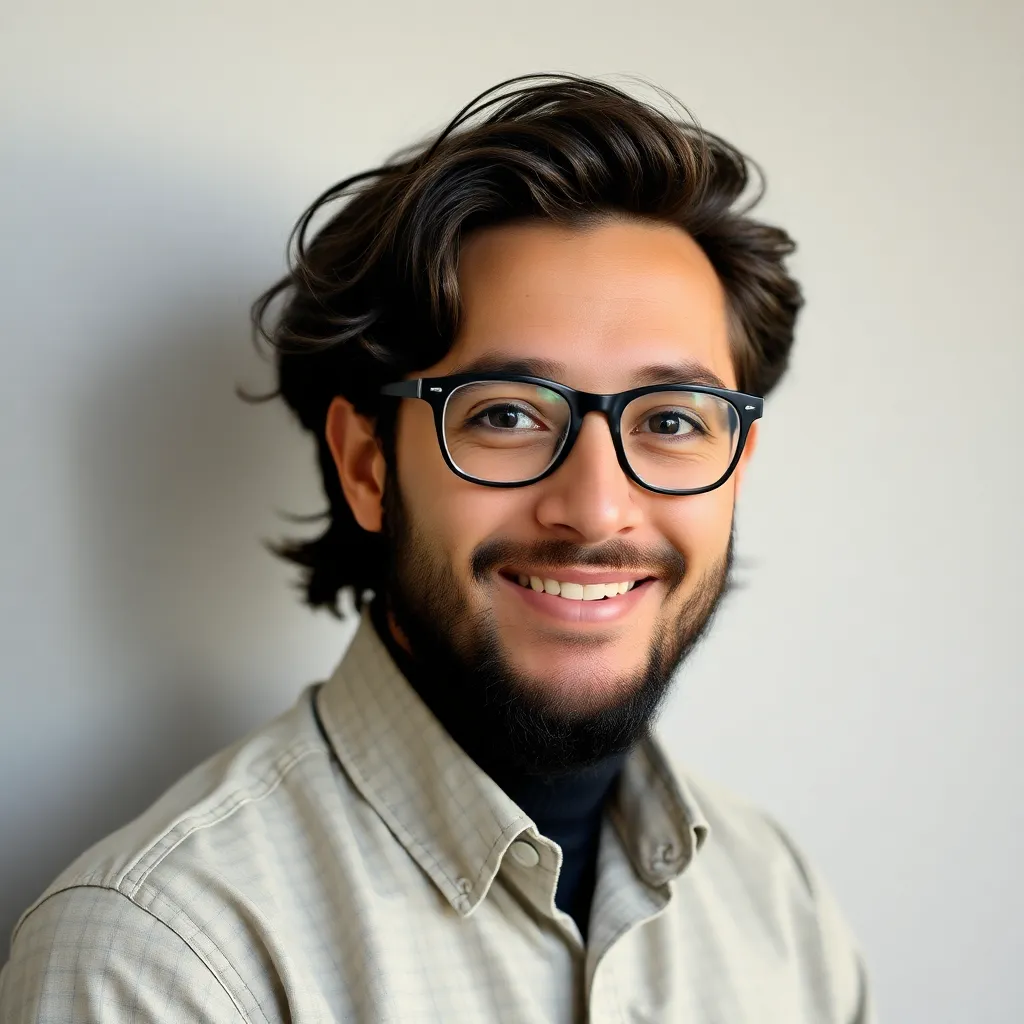
Holbox
Mar 31, 2025 · 6 min read
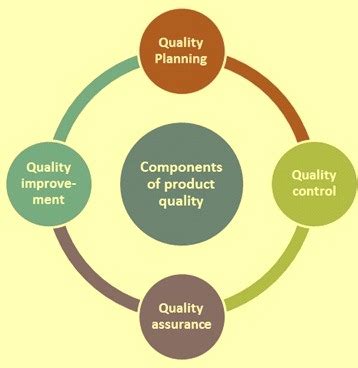
Table of Contents
- The Traditional Method Of Maintaining Product Quality Has Been The
- Table of Contents
- The Traditional Method of Maintaining Product Quality Has Been the... Foundation for Modern Quality Control
- The Pillars of Traditional Quality Control
- 1. Inspection and Testing: The Eyes and Ears of Quality
- 2. Standardization and Specification: Defining the Blueprint for Quality
- 3. Statistical Process Control (SPC): Unveiling Patterns in Production
- 4. Continuous Improvement (Kaizen): The Pursuit of Perfection
- The Evolution of Traditional Quality Control
- The Enduring Relevance of Traditional Methods
- Integrating Traditional and Modern Methods: A Synergistic Approach
- Conclusion: A Legacy of Quality
- Latest Posts
- Latest Posts
- Related Post
The Traditional Method of Maintaining Product Quality Has Been the... Foundation for Modern Quality Control
The traditional method of maintaining product quality has been the bedrock upon which modern quality control systems are built. While technology has revolutionized the process, introducing sophisticated tools and automated systems, the fundamental principles remain remarkably consistent. This article delves deep into the traditional approaches to quality control, examining their core tenets, exploring their evolution, and showcasing their enduring relevance in today's dynamic manufacturing landscape.
The Pillars of Traditional Quality Control
Traditional methods of quality control centered around several key pillars, all interconnected and mutually reinforcing:
1. Inspection and Testing: The Eyes and Ears of Quality
This was, and remains, the cornerstone of quality control. Traditional inspection involved meticulously examining finished products for defects, often manually. This hands-on approach allowed for detailed observation, catching subtle flaws that automated systems might miss. Testing, often destructive, involved subjecting samples to rigorous procedures to evaluate their performance and durability under specific conditions. This ensured that the product met pre-defined specifications and standards.
Key Aspects of Traditional Inspection and Testing:
- Visual Inspection: Careful examination of the product for surface flaws, imperfections, inconsistencies in color or texture.
- Dimensional Measurement: Using tools like calipers, micrometers, and rulers to ensure the product conforms to the specified dimensions.
- Functional Testing: Assessing the product’s performance against its intended purpose. This could involve rigorous simulations or real-world testing.
- Destructive Testing: Sacrificing a small sample to determine its ultimate strength, resilience, and durability under extreme conditions. This often involved methods like tensile testing or impact testing.
Limitations of Traditional Inspection and Testing:
While crucial, relying solely on inspection and testing was limited. It was reactive rather than proactive, identifying defects after they were produced, leading to wasted materials, time, and resources. Furthermore, the accuracy and consistency of manual inspection depended heavily on the skill and diligence of the inspector.
2. Standardization and Specification: Defining the Blueprint for Quality
Traditional quality control emphasized establishing clear and precise standards and specifications for each product. These documents meticulously outlined the required materials, dimensions, tolerances, and performance characteristics. This standardization ensured consistency across production runs, reducing variability and improving the predictability of the product's quality.
Importance of Standardization:
- Consistent Quality: Standardization eliminated ambiguity, guaranteeing that each product met the same stringent quality requirements.
- Improved Communication: Clearly defined specifications facilitated effective communication between designers, manufacturers, and quality control personnel.
- Simplified Inspection: Standardized parameters simplified the inspection process, making it easier to identify deviations from the norm.
- Reduced Defects: By proactively establishing standards, manufacturers could minimize defects during the production process.
3. Statistical Process Control (SPC): Unveiling Patterns in Production
While statistically-based quality control is more often associated with modern methods, the seeds were sown in traditional approaches. Early forms of SPC involved tracking key production variables and using simple statistical tools like control charts to monitor process stability. This allowed manufacturers to identify potential problems before they led to a significant number of defects. Early adopters used these techniques to detect patterns and trends, enabling timely adjustments to maintain quality.
Benefits of Early SPC Implementation:
- Early Problem Detection: Monitoring key variables enabled the prompt identification of deviations from the desired parameters.
- Predictive Quality: By understanding process variability, manufacturers could better predict the likelihood of defects.
- Process Optimization: SPC data provided insights into optimizing production processes for improved efficiency and reduced waste.
4. Continuous Improvement (Kaizen): The Pursuit of Perfection
The philosophy of continuous improvement, although more widely recognized in the context of lean manufacturing, was implicitly embedded in traditional quality control practices. Master craftsmen and skilled artisans consistently strived to refine their techniques, seeking ever-better ways to produce high-quality goods. This inherent drive for excellence drove improvements in materials, processes, and techniques.
Principles of Continuous Improvement:
- Regular Review: Continuous evaluation of the manufacturing processes to identify areas for improvement.
- Feedback Loops: Gathering feedback from various stakeholders (workers, customers) to identify shortcomings and areas needing attention.
- Iterative Enhancement: Implementing incremental improvements over time, leading to gradual but significant quality enhancements.
The Evolution of Traditional Quality Control
The traditional methods were largely reactive, focused on detecting and correcting defects after they occurred. This approach, while effective to a certain extent, often resulted in significant waste and inefficiency. The evolution of quality control involved a shift towards proactive methodologies, emphasizing the prevention of defects rather than just their detection.
This shift was influenced by several key factors:
- Growing Consumer Demand: As consumers became more discerning, the demand for higher-quality products increased.
- Technological Advancements: The development of sophisticated measurement instruments and statistical tools enabled more effective quality control.
- Emergence of New Methodologies: The introduction of techniques like Total Quality Management (TQM) and Six Sigma further refined the approach towards quality control.
This evolution led to the integration of several new approaches:
- Preventive Maintenance: Regularly maintaining equipment to prevent breakdowns that could lead to defects.
- Process Capability Analysis: Evaluating the ability of a process to consistently meet predetermined specifications.
- Design of Experiments (DOE): Using statistical techniques to optimize product and process designs.
The Enduring Relevance of Traditional Methods
Despite the advancements in technology and the emergence of more sophisticated quality control methodologies, the fundamental principles of traditional quality control remain highly relevant:
- Human Expertise: The skills and experience of skilled workers remain crucial in identifying subtle defects and ensuring quality. Automated systems are tools, but human judgment is often indispensable.
- Focus on Details: The traditional emphasis on thorough inspection and attention to detail is still crucial in preventing defects.
- Emphasis on Standards: Clearly defined specifications and standards remain fundamental to ensuring consistent product quality.
- Continuous Improvement: The pursuit of continuous improvement remains a cornerstone of achieving and maintaining high quality.
Integrating Traditional and Modern Methods: A Synergistic Approach
Today, the most effective quality control systems integrate both traditional and modern techniques. Automation streamlines processes, increases efficiency, and improves consistency. However, human expertise is crucial for interpreting data, solving complex problems, and ensuring that the automation itself operates flawlessly. The key lies in leveraging the strengths of both approaches to create a robust and efficient quality control system.
For example, automated vision systems can quickly detect surface defects, but human inspectors are still necessary to assess the severity of those defects and decide whether to reject the product. Statistical process control software helps analyze data, but the insights derived from that data need to be interpreted by skilled personnel to understand the root causes of problems and implement appropriate corrective actions.
Conclusion: A Legacy of Quality
The traditional method of maintaining product quality, based on inspection, standardization, statistical process control, and continuous improvement, laid the foundation for modern quality control systems. While technology has revolutionized the process, the fundamental principles remain highly relevant. By integrating traditional methods with modern technology, companies can build robust quality control systems that ensure consistent product quality, reduce waste, and enhance customer satisfaction. The legacy of these traditional methods continues to shape the pursuit of excellence in manufacturing and beyond. Understanding their core principles offers valuable insight into building a successful and effective quality control strategy in any industry.
Latest Posts
Latest Posts
-
What Defines A Long Term Investment Check All That Apply
Apr 04, 2025
-
A Market Product Grid Is A Framework To Relate
Apr 04, 2025
-
The X Coordinate Of An Ordered Pair Specifies The
Apr 04, 2025
-
Organisms That Extract Energy From Nonliving Environmental Resources Are Called
Apr 04, 2025
-
The Body Of A Direct Request Letter Should
Apr 04, 2025
Related Post
Thank you for visiting our website which covers about The Traditional Method Of Maintaining Product Quality Has Been The . We hope the information provided has been useful to you. Feel free to contact us if you have any questions or need further assistance. See you next time and don't miss to bookmark.