The Thickness Of A Flange On An Aircraft Component
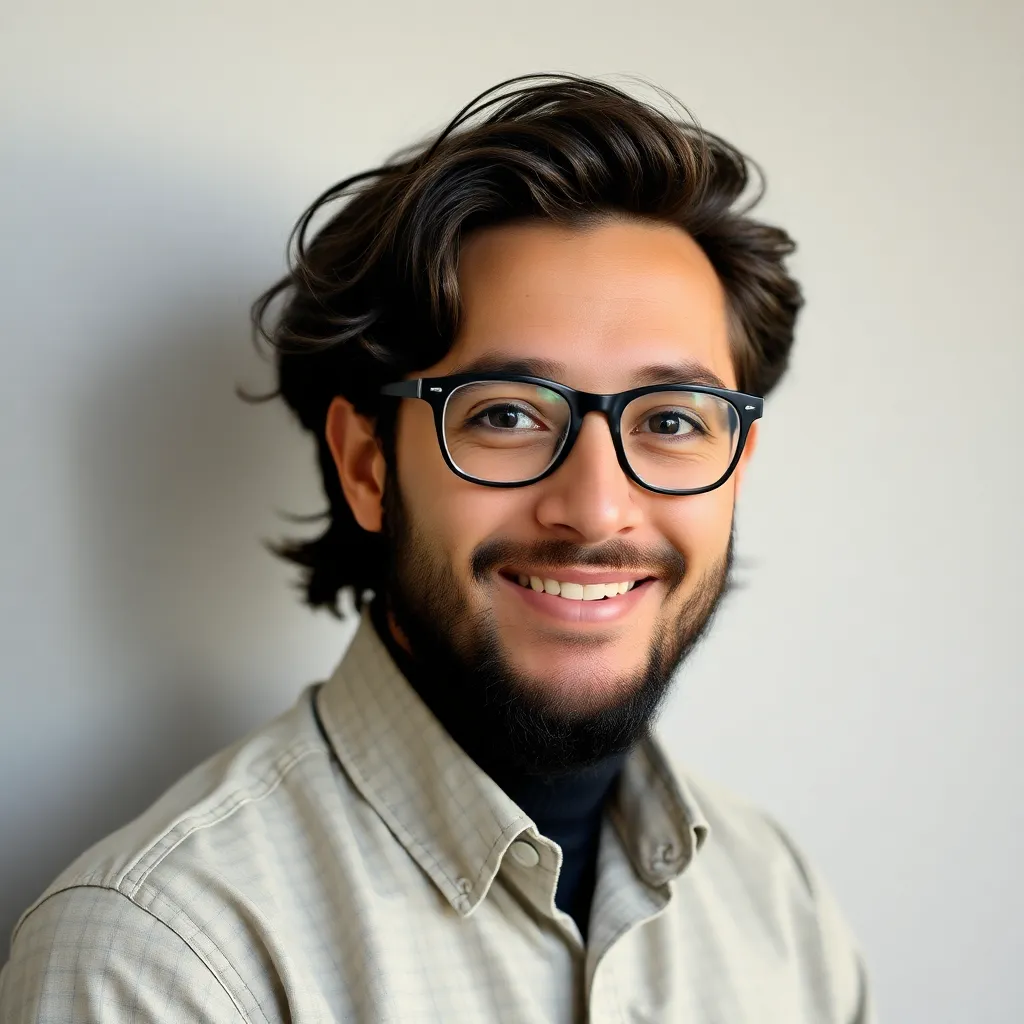
Holbox
Apr 03, 2025 · 5 min read

Table of Contents
- The Thickness Of A Flange On An Aircraft Component
- Table of Contents
- The Thickness of a Flange on an Aircraft Component: A Deep Dive into Design Considerations
- Factors Influencing Flange Thickness
- 1. Applied Loads and Stress Analysis:
- 2. Material Properties:
- 3. Manufacturing Process:
- 4. Environmental Factors:
- 5. Fatigue Considerations:
- 6. Joining Methods:
- Design Codes and Standards
- Advanced Design Techniques
- 1. Optimization Algorithms:
- 2. Topology Optimization:
- 3. Additive Manufacturing:
- Conclusion
- Latest Posts
- Latest Posts
- Related Post
The Thickness of a Flange on an Aircraft Component: A Deep Dive into Design Considerations
The seemingly simple flange—a projecting rim, collar, or rib—on an aircraft component plays a crucial role in its structural integrity and overall performance. Its thickness isn't a matter of arbitrary choice but a meticulously calculated value influenced by numerous factors. This article delves deep into the intricacies of flange thickness determination, exploring the underlying engineering principles and design considerations that dictate its dimensions. Understanding these factors is paramount for ensuring aircraft safety and reliability.
Factors Influencing Flange Thickness
The thickness of an aircraft component's flange is a critical design parameter determined by a complex interplay of factors. These include:
1. Applied Loads and Stress Analysis:
The primary driver behind flange thickness calculation is the magnitude and type of loads the component will endure during flight. These loads can be categorized as:
- Tensile Loads: Pulling forces that tend to stretch or elongate the flange.
- Compressive Loads: Pushing forces that tend to compress or shorten the flange.
- Shear Loads: Forces that tend to cause one part of the flange to slide past another.
- Bending Moments: Forces that cause the flange to bend or flex.
Sophisticated finite element analysis (FEA) techniques are employed to simulate these loads and accurately predict stress distributions within the flange. This analysis identifies areas of high stress concentration, guiding the design towards appropriate thickness to prevent failure. Safety factors, often exceeding 1.5, are incorporated to account for uncertainties and unexpected loading conditions.
2. Material Properties:
The material's yield strength, ultimate tensile strength, and fatigue strength are crucial in determining flange thickness. High-strength alloys like aluminum, titanium, and steel are commonly used in aircraft construction. Each material possesses unique mechanical properties that dictate its ability to withstand different stress levels. The selection of material significantly impacts the required flange thickness—stronger materials allow for thinner flanges, reducing weight.
3. Manufacturing Process:
The manufacturing method used to create the flange influences its final thickness. Processes like forging, casting, machining, and forming introduce variations in material properties and dimensional tolerances. For example, a forged flange may possess superior strength compared to a cast one, potentially allowing for a thinner design. The manufacturing process also dictates the achievable tolerances and surface finish, which can indirectly affect the flange's load-bearing capacity.
4. Environmental Factors:
Aircraft components are exposed to harsh environmental conditions, including extreme temperatures, vibration, and corrosion. These factors can degrade material properties over time, reducing the flange's strength and potentially leading to failure. The design must account for these effects by either selecting materials with superior resistance to environmental degradation or by increasing the flange thickness to compensate for potential strength reduction. Corrosion allowances are often included in the thickness calculations.
5. Fatigue Considerations:
Aircraft components experience cyclical loading during flights, leading to fatigue failure over time. Fatigue cracks initiate at stress concentrations, and their propagation can lead to catastrophic failure. Therefore, the flange design must incorporate fatigue analysis to ensure that the component can withstand the expected number of flight cycles without experiencing fatigue failure. This often necessitates a higher flange thickness than that predicted by static stress analysis alone. Stress concentration factors are incorporated to account for the geometry's influence on fatigue life.
6. Joining Methods:
The method used to join the flange to other components influences its design. Bolted joints, welded joints, and riveted joints each introduce different stress distributions within the flange. The design must consider the stresses generated by these joining methods and ensure that the flange thickness is sufficient to prevent failure at the joint. Stress risers at the bolt holes or weld seams need careful consideration. Proper design practices, such as using appropriate hole sizes and radii, help minimize these stress risers.
Design Codes and Standards
Aircraft component design adheres to stringent industry standards and regulations to ensure safety and reliability. These standards dictate specific design requirements and acceptance criteria, including those related to flange thickness. Examples include:
- ASME (American Society of Mechanical Engineers): Provides codes and standards for pressure vessels and other mechanical components. While not directly focused on aircraft, aspects of ASME standards are relevant to certain aircraft components.
- MIL-SPEC (Military Specification): Defines detailed requirements for military aircraft components, including material specifications and design guidelines.
- FAA (Federal Aviation Administration): Sets regulations and certification standards for aircraft and their components, impacting flange design through its certification requirements.
- EASA (European Union Aviation Safety Agency): Similar to the FAA, EASA establishes airworthiness requirements for aircraft operating in Europe.
These standards often provide guidance on allowable stress levels, safety factors, and fatigue life requirements, directly influencing the flange thickness calculations. Adherence to these codes is crucial for obtaining certification and ensuring the airworthiness of the aircraft.
Advanced Design Techniques
Modern aircraft design leverages advanced techniques to optimize flange thickness while maintaining structural integrity:
1. Optimization Algorithms:
Computer-aided design (CAD) software incorporates optimization algorithms that automatically adjust flange thickness based on predefined constraints and objectives. These algorithms explore various design options to find the optimal thickness that minimizes weight while satisfying all stress and fatigue requirements.
2. Topology Optimization:
This technique allows designers to explore unconventional shapes and material distributions within the flange to minimize weight without sacrificing strength. It can lead to flanges with optimized thicknesses that are not uniformly distributed, resulting in significant weight savings.
3. Additive Manufacturing:
Advanced manufacturing processes like 3D printing allow for the creation of complex flange geometries that are not feasible with traditional methods. This enables the design of optimized flanges with intricate internal structures that maximize strength and minimize weight, potentially leading to thinner designs.
Conclusion
Determining the appropriate flange thickness on an aircraft component is a complex engineering endeavor requiring a deep understanding of various factors, including applied loads, material properties, manufacturing processes, environmental conditions, and design standards. Meticulous calculations, often involving sophisticated FEA and fatigue analysis, are essential to ensure structural integrity and safety. Advanced design techniques, coupled with adherence to stringent industry standards, contribute to optimizing flange thickness, leading to lighter and more efficient aircraft designs. The seemingly simple flange, therefore, represents a critical element in aircraft design, highlighting the importance of precision engineering and adherence to rigorous safety protocols. The pursuit of optimal flange thickness is a continuous evolution, driven by advancements in materials science, computational methods, and manufacturing technologies, all working in concert to ensure the safety and reliability of the skies above.
Latest Posts
Latest Posts
-
Techniques For Building Employee Empowerment Include
Apr 08, 2025
-
A Perfectly Elastic Supply Curve Is
Apr 08, 2025
-
Old Economy Traders Opened An Account
Apr 08, 2025
-
Classify The Given Items With The Appropriate Group Multipolar Neuron
Apr 08, 2025
-
In General Enzymes Are What Kinds Of Molecules
Apr 08, 2025
Related Post
Thank you for visiting our website which covers about The Thickness Of A Flange On An Aircraft Component . We hope the information provided has been useful to you. Feel free to contact us if you have any questions or need further assistance. See you next time and don't miss to bookmark.