The Steel Shaft Is Made From Two Segments
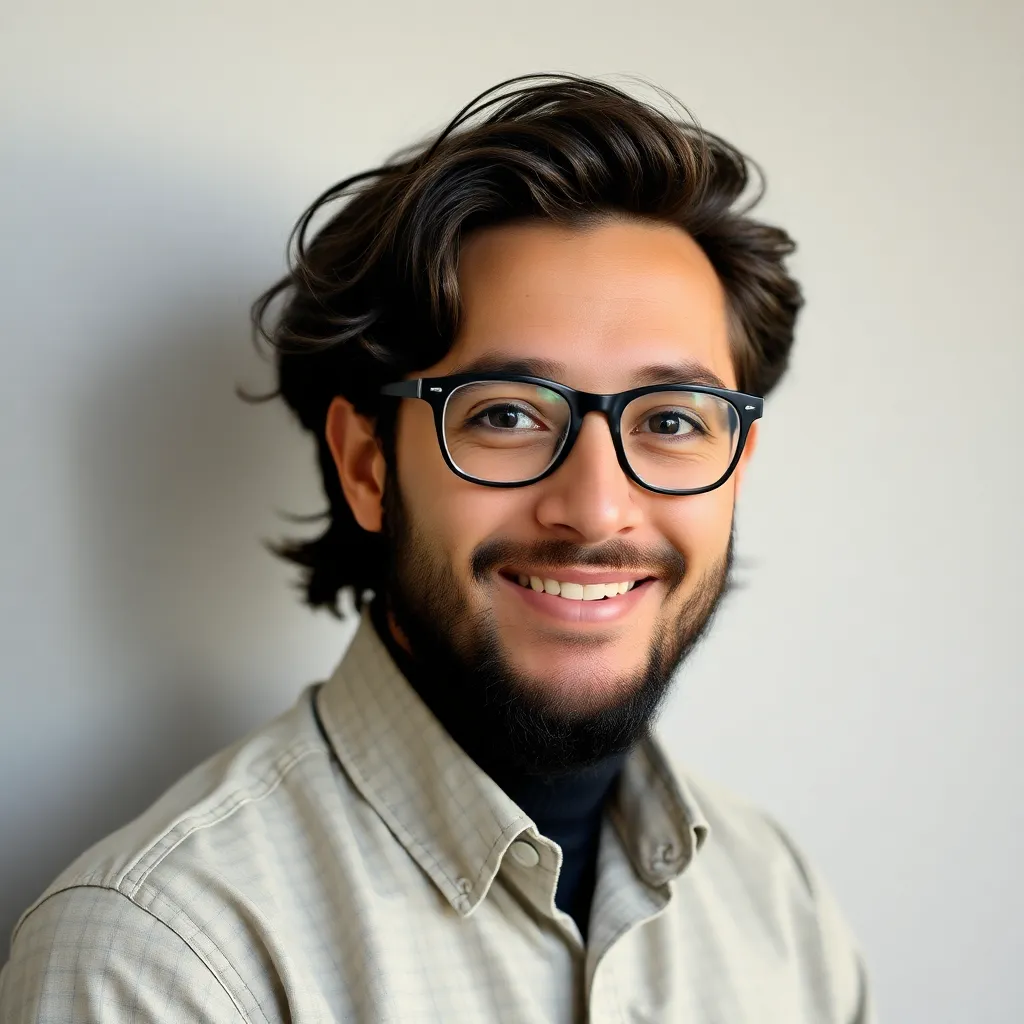
Holbox
Apr 03, 2025 · 7 min read

Table of Contents
- The Steel Shaft Is Made From Two Segments
- Table of Contents
- The Steel Shaft Made From Two Segments: Design, Manufacturing, and Applications
- Design Considerations for Two-Segment Steel Shafts
- 1. Material Selection: The Synergy of Different Steels
- 2. Geometry and Joining Techniques: Ensuring Seamless Integration
- 3. Surface Treatments: Enhancing Durability and Performance
- Manufacturing Processes for Two-Segment Steel Shafts
- 1. Individual Segment Manufacturing: Precision Machining
- 2. Joining Process: Ensuring Structural Integrity
- 3. Final Machining and Finishing: Achieving Dimensional Accuracy
- 4. Quality Control and Inspection: Guaranteeing Product Reliability
- Applications of Two-Segment Steel Shafts
- 1. Automotive Industry: Enhanced Durability and Performance
- 2. Aerospace Industry: Meeting Demanding Requirements
- 3. Industrial Machinery: Optimizing Cost and Performance
- 4. Energy Sector: Enhanced Reliability and Efficiency
- Conclusion: A Versatile Solution for Diverse Applications
- Latest Posts
- Latest Posts
- Related Post
The Steel Shaft Made From Two Segments: Design, Manufacturing, and Applications
Steel shafts, fundamental components in countless machines and systems, often require specific properties tailored to their application. One intriguing design approach involves creating a shaft from two distinct segments, each possessing unique material characteristics or geometries. This technique offers significant advantages in terms of cost-effectiveness, performance optimization, and enhanced functionality. This article delves into the intricacies of two-segment steel shafts, exploring their design considerations, manufacturing processes, and diverse applications.
Design Considerations for Two-Segment Steel Shafts
The decision to construct a steel shaft from two segments isn't arbitrary. It stems from a careful analysis of the required mechanical properties and operational conditions. Several key factors influence the design process:
1. Material Selection: The Synergy of Different Steels
The primary design consideration revolves around choosing the appropriate materials for each segment. This often involves combining steels with contrasting properties. For instance:
-
High-strength steel for the core: This segment usually bears the brunt of torsional and bending loads, requiring a high yield strength and fatigue resistance. Common choices include high-carbon steels, alloy steels (such as chromium-molybdenum steels), and even advanced materials like maraging steels for extremely demanding applications.
-
Tougher, more resilient steel for the outer segment: The outer segment might prioritize impact resistance, wear resistance, or corrosion resistance, depending on the application. This could involve using stainless steels, low-alloy steels with enhanced toughness, or surface treatments like carburizing or nitriding to enhance surface hardness.
The selection process carefully balances the desired properties of the combined shaft. A high-strength core ensures sufficient load-bearing capacity, while a protective outer layer enhances durability and longevity.
2. Geometry and Joining Techniques: Ensuring Seamless Integration
The geometry of each segment is crucial for both functionality and manufacturability. Careful consideration must be given to:
-
Shaft diameter: The diameter of each segment needs precise calculation to ensure optimal stress distribution and avoid stress concentrations at the joining interface. This often involves Finite Element Analysis (FEA) simulations to predict stress and strain under various loading conditions.
-
Joining Methods: Seamless integration of the two segments is paramount. Various joining methods exist, each with its strengths and limitations:
-
Welding: Welding offers a strong and potentially cost-effective solution, but requires careful control to avoid heat-affected zones that might compromise the shaft's integrity. Advanced techniques like laser welding offer improved precision and reduced heat input.
-
Shrink fitting: This method involves heating the outer segment to expand it and then sliding it onto the core segment. Upon cooling, the interference fit creates a strong mechanical bond. This method is suitable when precise dimensional control is critical and welding is undesirable.
-
Mechanical fastening: Bolts, screws, or keys can join the segments. This approach is simpler but might compromise the shaft's strength and torsional stiffness compared to welding or shrink fitting.
-
The choice of joining method directly impacts the shaft's overall performance and must be carefully evaluated based on the specific application and required load capacity.
3. Surface Treatments: Enhancing Durability and Performance
Surface treatments play a significant role in enhancing the lifespan and performance of a two-segment steel shaft. Common treatments include:
-
Hard chrome plating: This increases surface hardness and wear resistance, particularly beneficial for applications involving significant friction.
-
Nitriding: This diffusion process introduces nitrogen into the surface, enhancing hardness, fatigue strength, and corrosion resistance.
-
Shot peening: This process introduces compressive residual stresses into the surface, increasing fatigue life and resistance to crack propagation.
The selection of surface treatments is dictated by the specific operational environment and the expected wear mechanisms.
Manufacturing Processes for Two-Segment Steel Shafts
The manufacturing process for two-segment steel shafts requires precision and control to guarantee the integrity of the final product. The specific steps vary depending on the chosen materials, geometry, and joining method. Generally, the process involves the following stages:
1. Individual Segment Manufacturing: Precision Machining
Each segment is initially manufactured separately using conventional machining techniques like turning, milling, and grinding. The accuracy of these processes is critical to ensuring a proper fit and preventing stress concentrations at the joining interface. Computer Numerical Control (CNC) machining is often employed for precise control and repeatability.
2. Joining Process: Ensuring Structural Integrity
The joining process is a critical stage and is executed carefully to ensure a strong and reliable bond. As previously mentioned, welding, shrink fitting, or mechanical fastening are the common methods. Quality control measures, including non-destructive testing (NDT) techniques like ultrasonic inspection, are implemented to detect any defects or flaws in the joint.
3. Final Machining and Finishing: Achieving Dimensional Accuracy
Following the joining process, the entire shaft undergoes final machining and finishing operations to achieve the desired dimensions and surface finish. This might involve additional grinding, polishing, or surface treatments to ensure optimal performance and longevity.
4. Quality Control and Inspection: Guaranteeing Product Reliability
Rigorous quality control measures are employed throughout the entire manufacturing process to ensure the final product meets the required specifications and quality standards. This includes dimensional inspection, material testing, and NDT techniques to detect any flaws or defects.
Applications of Two-Segment Steel Shafts
The versatility of two-segment steel shafts makes them suitable for a wide range of applications across various industries:
1. Automotive Industry: Enhanced Durability and Performance
In the automotive sector, two-segment shafts find use in various components such as:
-
Driveshafts: Combining a high-strength steel core with a corrosion-resistant outer layer protects against harsh environmental conditions and extends the lifespan of the driveshaft.
-
Crankshafts: Utilizing different steel grades in the crankshaft can optimize both strength and fatigue resistance, enhancing engine performance and reliability.
-
Steering columns: A two-segment design can incorporate a high-strength core for structural integrity and a wear-resistant outer layer to minimize wear and tear.
2. Aerospace Industry: Meeting Demanding Requirements
The aerospace industry demands materials with exceptional strength-to-weight ratios and high fatigue resistance. Two-segment shafts find applications in:
-
Turboshaft engines: High-strength cores withstand the demanding loads, while outer segments provide corrosion protection and improved surface finish.
-
Helicopter rotor shafts: These shafts require exceptional strength, fatigue resistance, and durability to withstand cyclic loading during operation.
-
Aircraft control systems: Precise control and reliability are crucial in aircraft control systems, and a two-segment design can optimize these characteristics.
3. Industrial Machinery: Optimizing Cost and Performance
Numerous industrial machinery applications benefit from the cost-effectiveness and performance advantages of two-segment shafts:
-
Gearboxes: Combining different steel grades allows for optimizing gear meshing and load-bearing capacity, enhancing gearbox performance and efficiency.
-
Rolling mills: These high-stress applications benefit from shafts with superior strength and fatigue resistance.
-
Mining equipment: The durability and corrosion resistance of a two-segment design are advantageous in harsh mining environments.
4. Energy Sector: Enhanced Reliability and Efficiency
The energy sector uses two-segment shafts in applications such as:
-
Turbogenerators: These shafts must withstand significant torsional loads and operate reliably for extended periods.
-
Wind turbines: The shafts in wind turbines experience cyclic loading and exposure to harsh environmental conditions. A two-segment design optimizes both strength and corrosion resistance.
-
Pumping systems: In high-pressure pumping systems, durability and resistance to wear are critical, making two-segment shafts an attractive option.
Conclusion: A Versatile Solution for Diverse Applications
Two-segment steel shafts offer a compelling combination of cost-effectiveness, performance optimization, and enhanced functionality. By carefully selecting the materials, geometry, and joining methods, engineers can create shafts tailored to the specific requirements of each application. The versatility of this design approach, coupled with advancements in manufacturing technologies, ensures its continued relevance in a wide array of industries. As material science and manufacturing techniques continue to evolve, we can expect even more innovative applications of two-segment steel shafts in the future. The careful design and manufacturing process are crucial for success, demanding a deep understanding of materials science, engineering mechanics, and manufacturing processes. This approach continues to be a vital part of engineering design, pushing the boundaries of performance and durability across various sectors.
Latest Posts
Latest Posts
-
Which Of The Following Is A Web App
Apr 07, 2025
-
2 Methyl 4 1 Methylethyl Octane
Apr 07, 2025
-
The Demand Curve Focuses Entirely On The
Apr 07, 2025
-
A Nation Based On Individualism Would Agree That
Apr 07, 2025
-
The Deflection Plates In An Oscilloscope
Apr 07, 2025
Related Post
Thank you for visiting our website which covers about The Steel Shaft Is Made From Two Segments . We hope the information provided has been useful to you. Feel free to contact us if you have any questions or need further assistance. See you next time and don't miss to bookmark.