The Six Sigma Process Improvement Method Should Be Chosen When
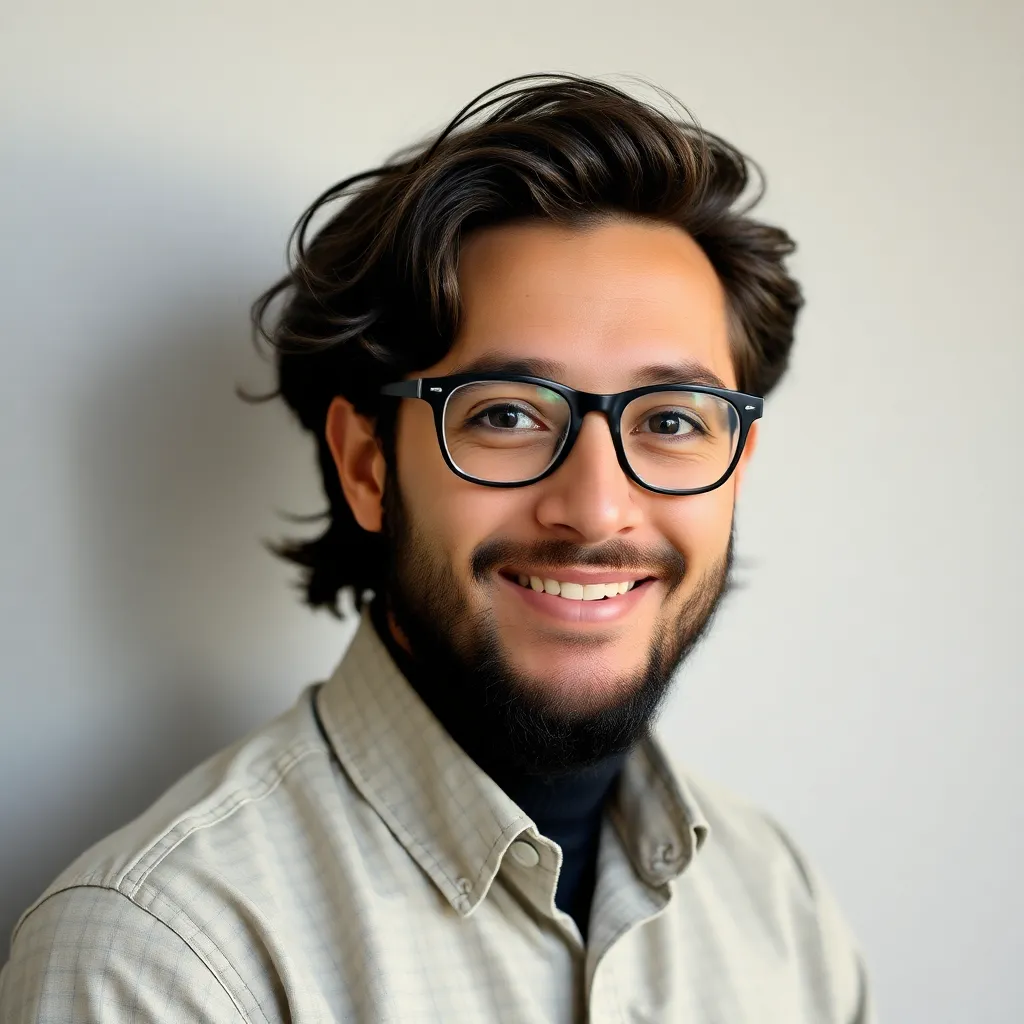
Holbox
Mar 13, 2025 · 6 min read
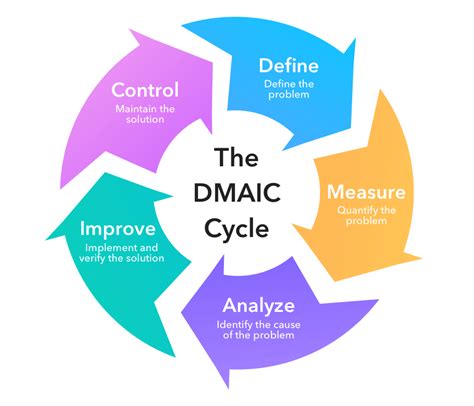
Table of Contents
When to Choose the Six Sigma Process Improvement Method: A Comprehensive Guide
Six Sigma, a data-driven methodology aimed at minimizing defects and maximizing efficiency, isn't a one-size-fits-all solution. Choosing to implement Six Sigma requires careful consideration of your organization's specific needs and circumstances. This comprehensive guide explores the situations where adopting the Six Sigma process improvement method is particularly advantageous, helping you determine if it's the right fit for your project or organization.
Understanding the Core Principles of Six Sigma
Before delving into when to choose Six Sigma, let's briefly review its core tenets. Six Sigma focuses on:
- Data-driven decision making: Reliance on hard data and statistical analysis to identify problems and measure improvements. This eliminates guesswork and ensures objective evaluation.
- Process improvement: Systematic identification and elimination of process variations that lead to defects or inefficiencies.
- DMAIC methodology: The widely used DMAIC (Define, Measure, Analyze, Improve, Control) cycle provides a structured approach to process improvement projects.
- Reduction of variation: Minimizing variability in processes is crucial for consistent quality and predictable outcomes. Six Sigma aims to achieve a level of quality where only 3.4 defects per million opportunities occur.
- Continuous improvement: Six Sigma isn't a one-time fix; it fosters a culture of continuous improvement and ongoing monitoring of processes.
Situations Where Six Sigma Excels
Six Sigma shines in situations characterized by specific challenges and opportunities. Let's examine these in detail:
1. High Volume, Repetitive Processes
Six Sigma is ideally suited for processes involving high volumes of repetitive tasks. Manufacturing processes, call center operations, order fulfillment, and data entry are prime examples. In these scenarios, even small improvements in efficiency can translate into significant cost savings and increased output over time. The ability to pinpoint and eliminate recurring errors within these high-volume processes is a core strength of Six Sigma.
Example: A manufacturing plant producing thousands of units daily could leverage Six Sigma to identify and eliminate defects in the assembly line, leading to fewer product recalls, reduced waste, and increased customer satisfaction.
2. Significant Process Variation
When a process suffers from excessive variability, leading to unpredictable outcomes and inconsistent quality, Six Sigma provides a structured approach to identify and reduce the root causes of this variation. The DMAIC methodology allows for a systematic investigation, pinpointing factors contributing to inconsistency.
Example: A customer service department experiencing widely fluctuating call resolution times might use Six Sigma to analyze the contributing factors, such as inadequate training, inefficient systems, or unclear procedures. Identifying and addressing these variations can lead to improved customer service and reduced frustration.
3. High Defect Rates or Errors
Obvious situations for Six Sigma implementation are those with high defect rates or error percentages. Whether it's manufacturing defects, software bugs, or errors in administrative processes, Six Sigma provides the tools to systematically reduce these flaws. By identifying and eliminating the root causes of defects, Six Sigma helps organizations achieve higher quality and lower costs.
Example: A software development team facing numerous bugs in a released product could employ Six Sigma to analyze the development process, identify the root causes of the bugs, and implement preventative measures in future projects.
4. Need for Measurable Improvement
Six Sigma thrives on measurable results. Its data-driven approach requires quantifiable metrics to track progress and demonstrate success. If you need to demonstrate tangible improvements, whether it's reduced costs, increased efficiency, or improved customer satisfaction, Six Sigma's emphasis on data analysis is a significant advantage.
Example: A company seeking to reduce customer churn might use Six Sigma to analyze customer feedback, identify contributing factors to churn, and implement targeted improvements, with clear metrics to track the effectiveness of these changes.
5. Desire for a Culture of Continuous Improvement
Implementing Six Sigma isn't just about fixing immediate problems; it's about fostering a long-term culture of continuous improvement. The methodology encourages regular process reviews, data analysis, and ongoing refinement. If your organization is committed to long-term improvement and ongoing optimization, Six Sigma can be a powerful tool to establish this culture.
Example: A hospital seeking to consistently improve patient care and reduce medical errors might implement Six Sigma across various departments, creating a culture of continuous improvement and proactive problem-solving.
6. Complex Problems Requiring a Structured Approach
Six Sigma excels in handling complex problems that require a structured, systematic approach. The DMAIC methodology provides a clear roadmap to navigate through complex challenges, breaking them down into manageable steps and ensuring a thorough analysis.
Example: A supply chain experiencing frequent disruptions due to multiple contributing factors might benefit from a Six Sigma approach. The structured methodology facilitates a comprehensive analysis of the entire supply chain, identifying bottlenecks and implementing solutions.
7. Need for Cross-Functional Collaboration
Six Sigma often requires collaboration across different departments or teams. The methodology emphasizes teamwork and shared responsibility for process improvement. If your problem involves multiple departments or functional areas, Six Sigma's collaborative nature ensures all stakeholders are involved in the solution.
Example: A company experiencing delays in product launches might use Six Sigma to bring together teams from design, engineering, manufacturing, and marketing to identify bottlenecks and streamline the process.
8. Limited Resources and Need for Efficiency
While Six Sigma implementation might initially require investment, in the long run, it can lead to significant cost savings and improved efficiency. If your organization is facing resource constraints, the long-term benefits of improved efficiency and reduced waste make Six Sigma a worthy investment.
Example: A small business experiencing high operational costs can use Six Sigma to optimize its processes, reduce waste, and enhance productivity without needing to significantly increase its workforce.
When Six Sigma Might Not Be the Best Choice
Despite its numerous benefits, Six Sigma isn't always the ideal solution. Consider these scenarios:
- Simple, straightforward problems: For minor issues that can be easily addressed with simple solutions, implementing the full Six Sigma methodology might be overkill.
- Lack of management support: Successful Six Sigma implementation requires strong commitment and support from top management. Without this support, the initiative is likely to fail.
- Insufficient data: Six Sigma relies heavily on data. If you lack access to sufficient, reliable data, it will be challenging to conduct effective analysis and draw meaningful conclusions.
- Rapidly changing environment: In rapidly evolving industries or markets, the time required for a complete Six Sigma project might be too long. Agile methodologies might be better suited for dynamic environments.
- Resistance to change: Six Sigma often necessitates changes in processes and workflows. If there's significant resistance to change within the organization, implementation will be difficult.
Conclusion: Strategic Decision Making
Choosing whether or not to implement the Six Sigma process improvement method is a strategic decision. By carefully considering the factors discussed above, you can determine if Six Sigma aligns with your organization's specific needs and goals. Remember, while Six Sigma offers a powerful framework for process improvement, it's crucial to assess its suitability within the context of your unique circumstances. A thorough understanding of your challenges, resources, and organizational culture is paramount to making an informed decision. The power of Six Sigma lies in its ability to systematically address complexity and drive sustainable improvements, but only when applied strategically and thoughtfully.
Latest Posts
Latest Posts
-
Choose All That Would Cause Postsynaptic Stimulation To End
Mar 13, 2025
-
Which Type Of Electron Is The Highest In Energy
Mar 13, 2025
-
Match The Description With The Concept Being Demonstrated
Mar 13, 2025
-
Darrel Needs To Fire A Manager
Mar 13, 2025
-
Both Hcl And Hbr Are Added To 8 Ethyldecan 5 Ol At 100oc
Mar 13, 2025
Related Post
Thank you for visiting our website which covers about The Six Sigma Process Improvement Method Should Be Chosen When . We hope the information provided has been useful to you. Feel free to contact us if you have any questions or need further assistance. See you next time and don't miss to bookmark.