The Principal Mineral Used In Making Glass Is
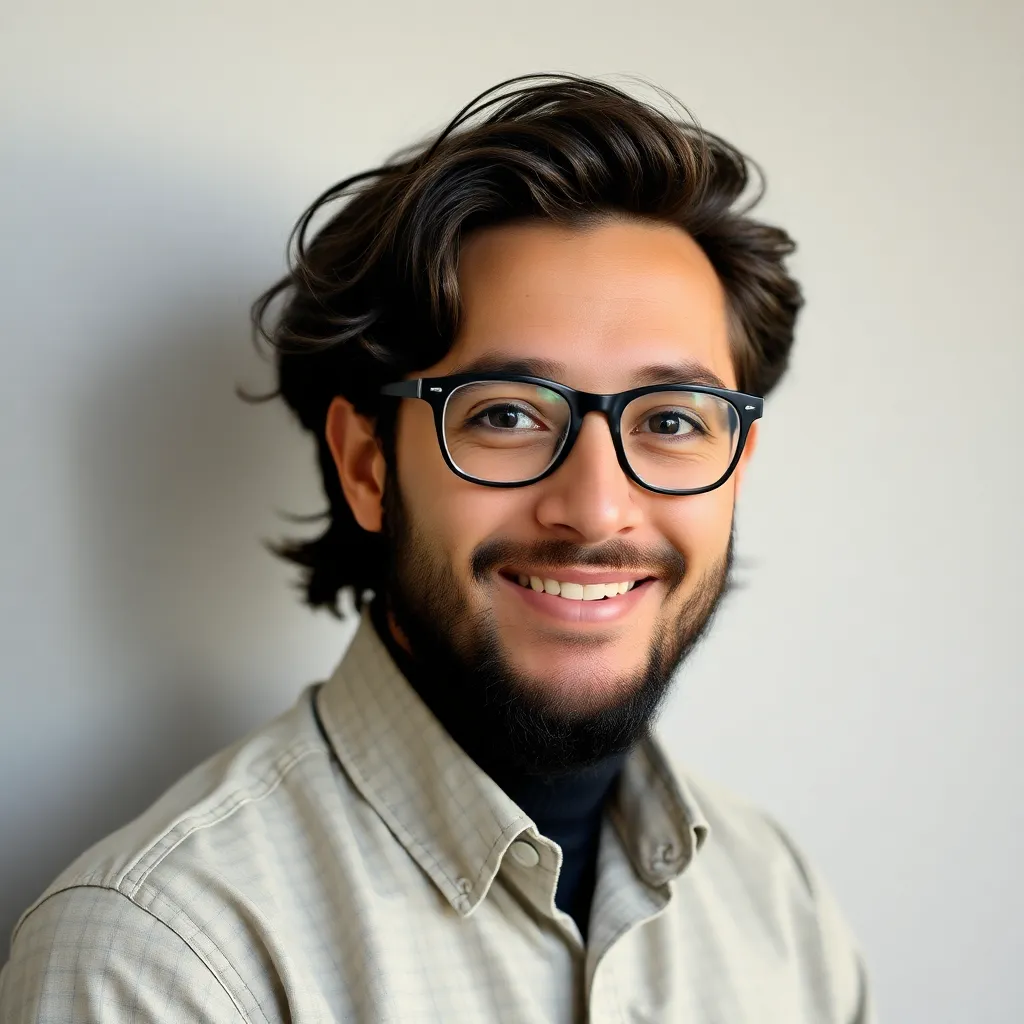
Holbox
May 10, 2025 · 6 min read
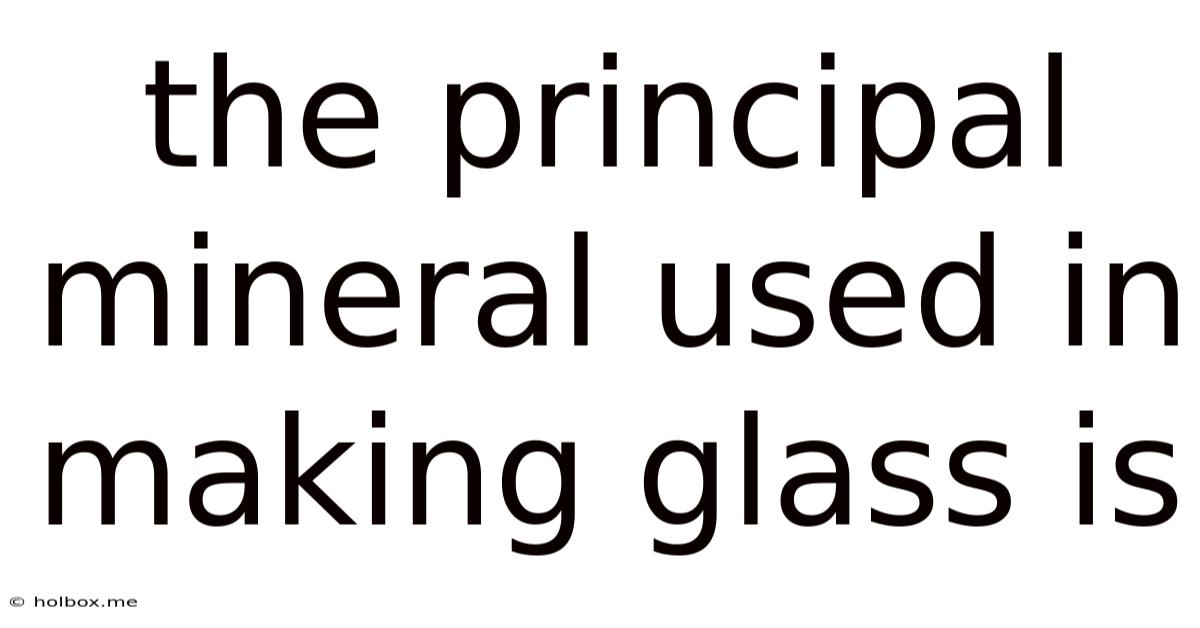
Table of Contents
- The Principal Mineral Used In Making Glass Is
- Table of Contents
- The Principal Mineral Used in Making Glass Is: Silica Sand – A Deep Dive into Glass Production
- What is Silica Sand?
- Key Properties of Silica Sand for Glassmaking:
- The Glassmaking Process: Silica Sand's Crucial Role
- 1. Batching:
- 2. Melting:
- 3. Shaping:
- 4. Annealing:
- 5. Finishing:
- Different Types of Glass and Silica Sand's Influence
- The Sustainability of Silica Sand in Glassmaking
- The Future of Silica Sand in Glass Production
- Latest Posts
- Related Post
The Principal Mineral Used in Making Glass Is: Silica Sand – A Deep Dive into Glass Production
The principal mineral used in making glass is silica sand, also known as quartz sand. This seemingly simple material is the fundamental building block of glass, responsible for its transparency, durability, and versatility. Understanding silica sand's properties and its role in glassmaking is crucial to appreciating the diverse world of glass products we encounter daily. This article will delve deep into the composition, properties, and processing of silica sand, exploring its indispensable role in the glass manufacturing process.
What is Silica Sand?
Silica sand, primarily composed of silicon dioxide (SiO2), is a naturally occurring granular material found abundantly around the world. Its purity and grain size are critical factors influencing its suitability for glassmaking. High-purity silica sand, with minimal impurities like iron oxide (which causes discoloration), is essential for producing high-quality, transparent glass. The grain size also impacts the melting process and the final product's properties. Too fine, and it may cause problems in melting; too coarse, and it may result in an uneven texture.
Key Properties of Silica Sand for Glassmaking:
- High Silica Content: A high percentage of SiO2 is paramount. This ensures the formation of a stable, glassy structure upon melting. Impurities can significantly affect the quality and color of the final product.
- Grain Size Distribution: The ideal grain size distribution promotes uniform melting and prevents the formation of unwanted bubbles or defects. Careful control of this factor is crucial for consistent glass production.
- Low Impurity Levels: Iron oxide, alumina, and other impurities can introduce color and weaken the glass structure. Minimizing these impurities is vital for producing clear, strong glass.
- Chemical Inertness: Silica sand's resistance to chemical reactions makes it ideal for various applications, as it doesn't easily react with other substances in the melting process or during the lifespan of the glass product.
The Glassmaking Process: Silica Sand's Crucial Role
The journey from silica sand to a finished glass product involves several key steps, each relying heavily on the properties of the sand.
1. Batching:
This initial stage involves carefully weighing and mixing the silica sand with other raw materials. The precise proportions of these materials determine the final glass's properties, such as its color, refractive index, and durability. Besides silica sand, the batch typically includes:
- Soda Ash (Sodium Carbonate - Na₂CO₃): Reduces the melting point of silica sand, making the process more energy-efficient.
- Limestone (Calcium Carbonate - CaCO₃): Increases the glass's chemical durability and resistance to weathering.
- Dolomite (Calcium Magnesium Carbonate - CaMg(CO₃)₂): Similar to limestone, enhancing durability and other properties.
- Cullet (Recycled Glass): Adding recycled glass reduces the energy consumption and raw material usage.
- Other Additives: These are added depending on the desired properties of the final product, such as colorants, opacifiers, and fining agents (to reduce bubbles).
2. Melting:
The carefully batched mixture is then fed into a furnace, typically at temperatures exceeding 1500°C (2732°F). At this intense heat, the raw materials melt and fuse together, forming a molten glass. The silica sand's role here is crucial; its high melting point provides the structural integrity of the molten glass. The melting process requires precise temperature and time control to achieve the desired viscosity and homogeneity. Insufficient heating may lead to incomplete melting and a heterogeneous product, while excessive heating can cause unwanted chemical reactions.
3. Shaping:
Once molten, the glass must be shaped into its final form. Various techniques are used, including:
- Blowing: Used for creating hollow glass objects, such as bottles and jars.
- Pressing: Used for forming flat glass and other shaped objects.
- Drawing: Used for producing flat glass sheets, such as window panes.
- Casting: Used for making large glass objects and specialty glass products.
The shaping process requires precise control of the glass's viscosity, which is directly influenced by the silica sand's properties and the other components in the batch.
4. Annealing:
After shaping, the glass is slowly cooled in a controlled manner called annealing. This process relieves internal stresses within the glass structure, preventing cracking or spontaneous breakage later. Improper annealing can lead to significant defects and reduce the product's lifespan.
5. Finishing:
The final step involves finishing processes like cutting, polishing, coating, and decorating, depending on the desired final product.
Different Types of Glass and Silica Sand's Influence
The type of silica sand used and the specific proportions of other raw materials significantly impact the final glass type. Different glass types possess unique properties, suitable for various applications:
- Soda-Lime Glass: This is the most common type of glass, used in windows, bottles, and containers. It's relatively inexpensive to produce and has good durability.
- Borosilicate Glass (Pyrex): Known for its high resistance to thermal shock, this type of glass is used in cookware, laboratory glassware, and other applications requiring resistance to temperature changes.
- Lead Glass (Crystal Glass): Adding lead oxide improves the glass's refractive index, giving it a brilliant sparkle and clarity. It's used in high-quality glassware and decorative items.
- Fused Silica Glass: This specialized type of glass is made almost entirely from high-purity silica sand, resulting in exceptional thermal and chemical resistance. It's used in high-temperature applications and specialized optical components.
The Sustainability of Silica Sand in Glassmaking
The abundance of silica sand might suggest a limitless resource, but responsible sourcing and recycling are crucial for sustainable glass production. Environmental considerations include:
- Silica Sand Mining: Mining practices must minimize environmental impact, including habitat destruction and water pollution. Responsible mining companies employ environmentally friendly techniques and strive to restore affected lands.
- Energy Consumption: Glassmaking is an energy-intensive process. Innovations focused on improving energy efficiency, such as using recycled cullet, are vital for reducing the industry's carbon footprint.
- Waste Management: Proper handling and disposal of waste materials generated during glass manufacturing are essential for minimizing environmental pollution. Recycling glass greatly reduces the need for new raw materials and lowers energy consumption.
The Future of Silica Sand in Glass Production
Research and development continue to explore innovative ways to improve silica sand's utilization in glassmaking. This includes:
- Improving Sand Quality: Developing techniques to enhance the purity and consistency of silica sand, leading to improved glass quality and reduced energy consumption.
- Alternative Raw Materials: Exploring alternative sources of silica, potentially including industrial byproducts, to reduce reliance on mined sand.
- Advanced Glass Manufacturing Techniques: Developing more efficient melting and shaping processes, minimizing energy use and waste generation.
- Recycling Innovations: Improving the collection, processing, and utilization of recycled glass, furthering the circular economy approach.
In conclusion, silica sand is far more than just a raw material; it's the cornerstone of the glass industry. Its unique properties, along with careful processing and innovative techniques, underpin the diverse range of glass products we use daily. Understanding the importance of responsible sourcing, recycling, and continuous improvement in glass manufacturing is crucial to ensure the continued sustainability and innovation of this essential material. From the simple window pane to sophisticated optical fibers, silica sand's contribution to our modern world is undeniable.
Latest Posts
Related Post
Thank you for visiting our website which covers about The Principal Mineral Used In Making Glass Is . We hope the information provided has been useful to you. Feel free to contact us if you have any questions or need further assistance. See you next time and don't miss to bookmark.