The Pipe Assembly Is Subjected To The 80-n Force
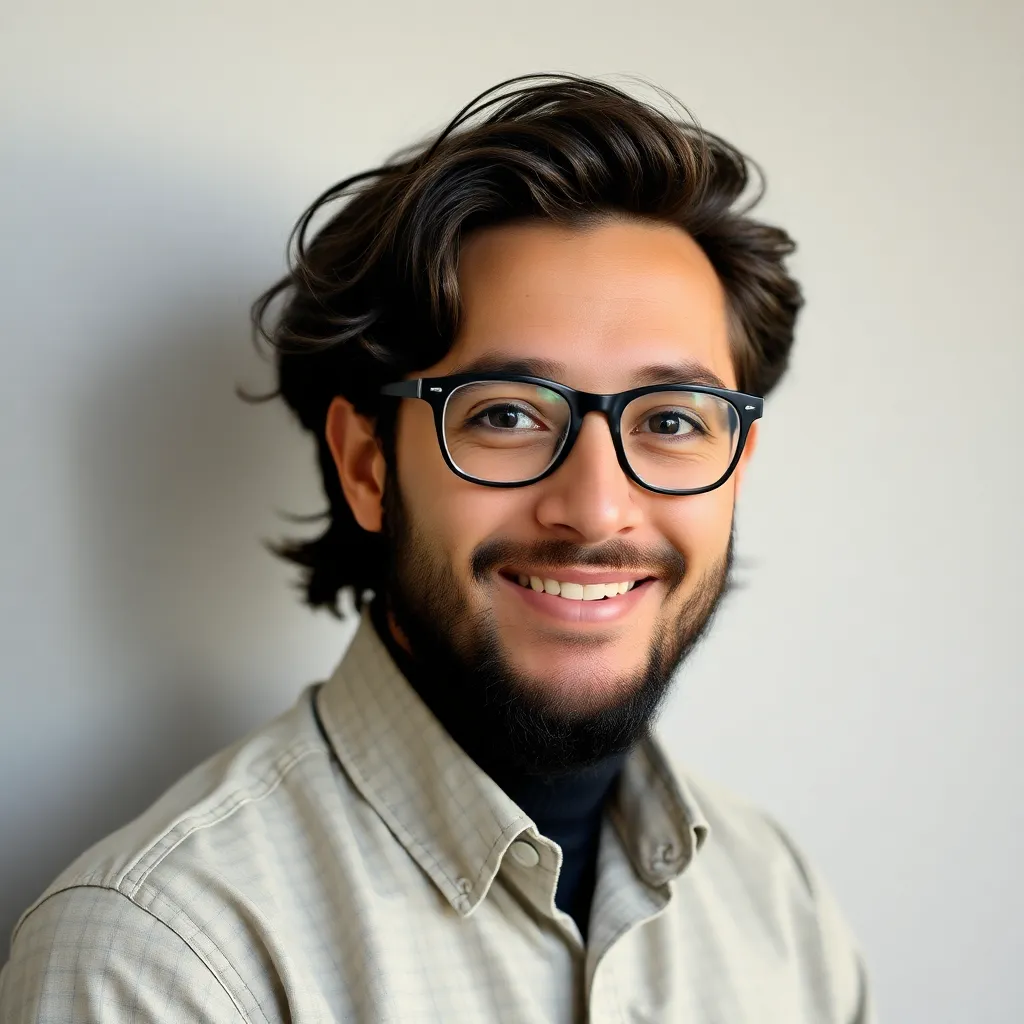
Holbox
Apr 03, 2025 · 6 min read

Table of Contents
- The Pipe Assembly Is Subjected To The 80-n Force
- Table of Contents
- The Pipe Assembly Subjected to an 80-N Force: A Comprehensive Analysis
- Understanding the Fundamentals
- Forces and Loads:
- Stress and Strain:
- Types of Stress:
- Failure Theories:
- Analyzing the Pipe Assembly
- Free Body Diagram:
- Shear Force and Bending Moment Diagrams:
- Stress Calculation:
- Strain Calculation:
- Deflection Calculation:
- Failure Analysis:
- Advanced Considerations
- Material Properties:
- Pipe Geometry:
- Boundary Conditions:
- Dynamic Loading:
- Fatigue:
- Corrosion and Degradation:
- Conclusion
- Latest Posts
- Latest Posts
- Related Post
The Pipe Assembly Subjected to an 80-N Force: A Comprehensive Analysis
This article delves into the complexities of analyzing a pipe assembly subjected to an 80-N force. We'll explore various aspects, from fundamental concepts to advanced techniques, providing a comprehensive understanding of stress, strain, and potential failure modes. This in-depth analysis will be beneficial for engineers, students, and anyone interested in structural mechanics.
Understanding the Fundamentals
Before diving into the specifics of an 80-N force on a pipe assembly, let's review some essential concepts:
Forces and Loads:
A force is a vector quantity characterized by magnitude and direction. In the context of a pipe assembly, forces can be applied in various ways: axial (along the pipe's longitudinal axis), transverse (perpendicular to the axis), or torsional (twisting). The 80-N force in our scenario needs further definition to accurately analyze its impact. Is it axial, transverse, or a combination? Knowing the point of application is also critical.
Stress and Strain:
When a force acts on a pipe assembly, it induces internal stresses. Stress is defined as the force per unit area (σ = F/A). The material responds to this stress by deforming, a phenomenon known as strain (ε = ΔL/L). The relationship between stress and strain is described by the material's constitutive model, often a linear elastic model (Hooke's Law: σ = Eε, where E is Young's modulus).
Types of Stress:
Several types of stress can be present in a pipe assembly:
- Axial Stress: Occurs due to axial forces, causing elongation or compression.
- Bending Stress: Caused by transverse loads, leading to bending moments and curvature.
- Shear Stress: Results from forces parallel to the cross-sectional area, causing deformation by slippage.
- Torsional Stress: Arises from twisting forces, producing angular deformation.
Understanding these stress types is crucial for accurate analysis and predicting potential failure points.
Failure Theories:
To determine if a pipe assembly will fail under an 80-N force, we need to apply appropriate failure theories. These theories predict failure based on the combination of stresses present:
- Maximum Shear Stress Theory (Tresca): Predicts failure when the maximum shear stress reaches the material's shear strength.
- Maximum Distortion Energy Theory (von Mises): Considers the combined effect of all stress components, predicting failure when the distortion energy reaches a critical value.
- Maximum Principal Stress Theory (Rankine): Based on the maximum principal stress reaching the material's tensile strength.
The choice of failure theory depends on the material's properties and the type of failure being considered (ductile or brittle).
Analyzing the Pipe Assembly
Let's assume, for the sake of this analysis, that the 80-N force is a transverse load applied at the midpoint of a simply supported pipe. This scenario allows us to demonstrate a common engineering problem.
Free Body Diagram:
The first step is to create a free body diagram (FBD) of the pipe assembly. This diagram shows all external forces and reactions acting on the pipe. For a simply supported pipe with a central 80-N load, we'll have two vertical support reactions of 40 N each at either end.
Shear Force and Bending Moment Diagrams:
Next, we'll determine the shear force and bending moment diagrams. These diagrams graphically represent the shear force and bending moment at different points along the pipe's length. For our simply supported pipe with a central load, the shear force will be constant (40 N) from each support to the center, and the bending moment will be maximum at the center.
Stress Calculation:
Using the bending moment diagram, we can calculate the maximum bending stress (σ_b) using the flexure formula:
σ_b = My/I
where:
- M is the maximum bending moment
- y is the distance from the neutral axis to the outermost fiber of the pipe
- I is the area moment of inertia of the pipe's cross-section
The area moment of inertia (I) depends on the pipe's geometry (outer and inner diameters). For a circular pipe, the formula for I is:
I = π(D_o⁴ - D_i⁴) / 64
where D_o and D_i are the outer and inner diameters, respectively.
Strain Calculation:
Once the stress is calculated, we can determine the strain using Hooke's Law:
ε = σ/E
where E is the Young's modulus of the pipe material.
Deflection Calculation:
The deflection of the pipe under the 80-N load can be calculated using various methods, including the double integration method or using standard formulas for simply supported beams with central loads. This calculation provides insights into the pipe's deformation under load.
Failure Analysis:
Finally, using the calculated stresses and the chosen failure theory, we can determine if the pipe assembly will fail under the 80-N load. If the calculated stresses exceed the material's yield strength or ultimate strength, failure is predicted.
Advanced Considerations
The analysis presented above is a simplified model. Several factors can significantly influence the pipe assembly's behavior under load:
Material Properties:
The material's properties (Young's modulus, yield strength, ultimate strength, Poisson's ratio) are crucial in determining stress, strain, and failure. Different materials exhibit different responses to loads.
Pipe Geometry:
The pipe's dimensions (diameter, wall thickness, length) directly affect its stiffness and strength. Changes in geometry significantly alter stress distribution.
Boundary Conditions:
The support conditions at the pipe's ends influence the reactions and stress distribution. Different support types (fixed, hinged, roller) lead to different bending moments and shear forces.
Dynamic Loading:
The analysis above assumes static loading. If the 80-N force is applied dynamically (e.g., impact), the stresses and strains will be significantly higher, requiring more complex dynamic analysis techniques.
Fatigue:
Repeated loading can lead to fatigue failure, even if the stress levels are below the material's yield strength. Fatigue analysis requires considering stress cycles and material fatigue properties.
Corrosion and Degradation:
Over time, corrosion or other degradation mechanisms can weaken the pipe material, reducing its load-bearing capacity.
Conclusion
Analyzing a pipe assembly subjected to an 80-N force requires a methodical approach, encompassing fundamental concepts, calculations, and consideration of various influencing factors. Accurate analysis requires careful consideration of the force's type, point of application, pipe geometry, material properties, and boundary conditions. Advanced techniques may be necessary for dynamic loading and fatigue analysis. A thorough understanding of these factors is crucial for ensuring the structural integrity and safety of pipe assemblies in various engineering applications. Remember to always consult relevant engineering codes and standards for design and safety. This detailed analysis provides a strong foundation for understanding and addressing similar engineering challenges.
Latest Posts
Latest Posts
-
Experiment 14 Heat Effects And Calorimetry
Apr 08, 2025
-
What Distinguishes A Memo From Other Types Of Business Documents
Apr 08, 2025
-
Design A Synthesis Of 3 Phenylpropene From Benzene And Propene
Apr 08, 2025
-
Location Based Targeting Is Most Effective When Combined With
Apr 08, 2025
-
Select The True Statements About Protein Secondary Structure
Apr 08, 2025
Related Post
Thank you for visiting our website which covers about The Pipe Assembly Is Subjected To The 80-n Force . We hope the information provided has been useful to you. Feel free to contact us if you have any questions or need further assistance. See you next time and don't miss to bookmark.