The Object Below Is Made Of Solid Plastic
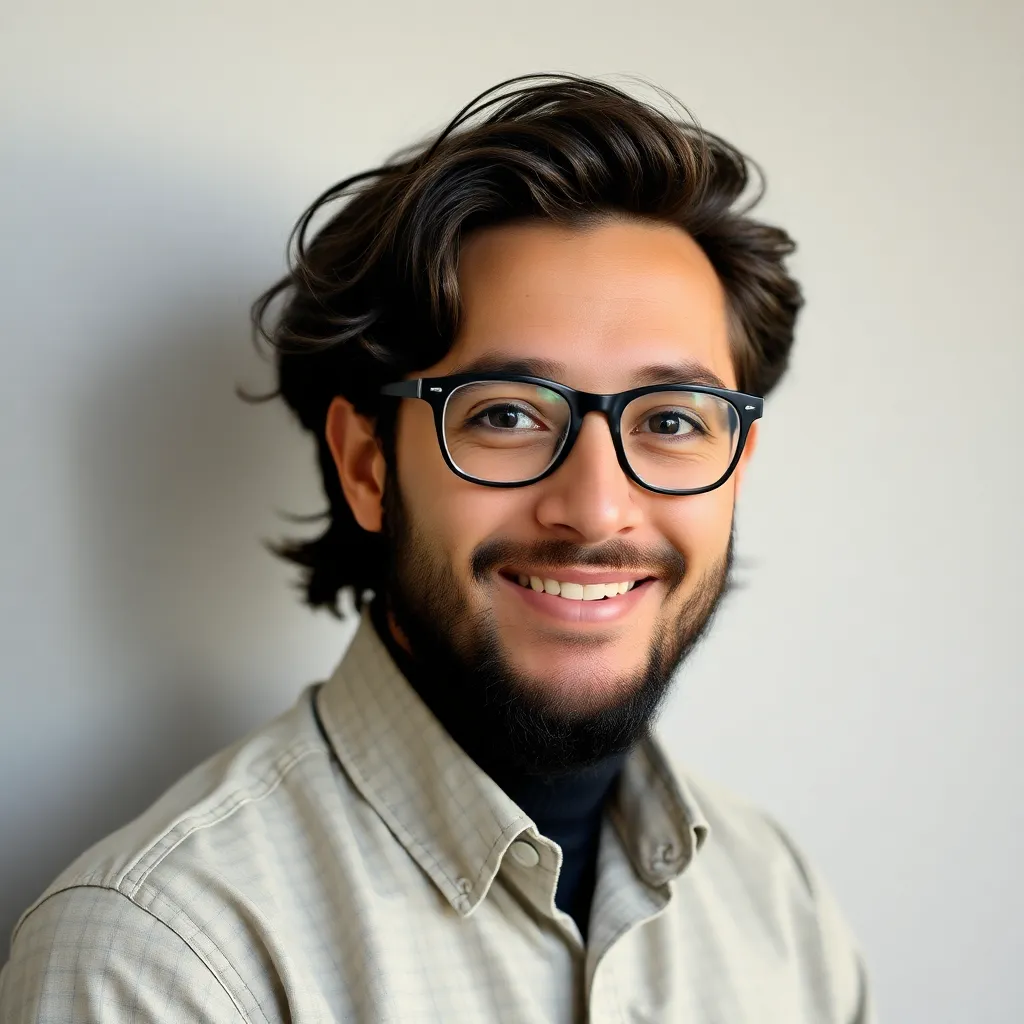
Holbox
May 09, 2025 · 7 min read
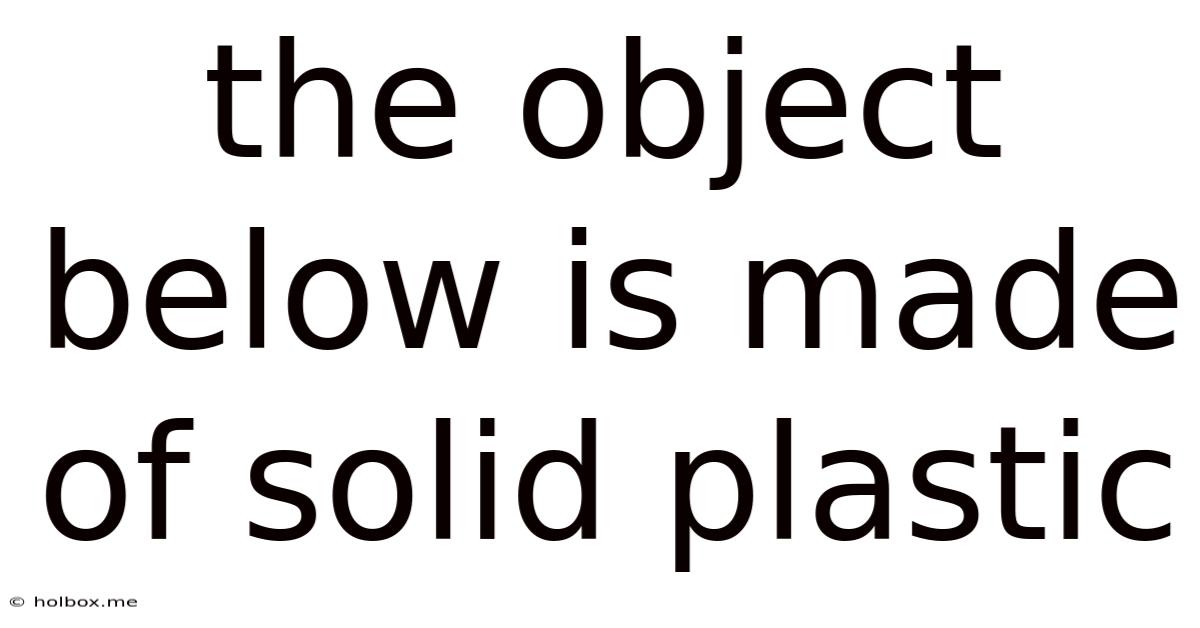
Table of Contents
- The Object Below Is Made Of Solid Plastic
- Table of Contents
- The Object Below is Made of Solid Plastic: Exploring the World of Plastic Fabrication
- Understanding Solid Plastics: A Material Deep Dive
- 1. Polymer Type:
- 2. Additives and Fillers:
- Manufacturing Processes for Solid Plastic Objects
- 1. Injection Molding:
- 2. Extrusion:
- 3. Thermoforming:
- 4. Rotational Molding:
- 5. 3D Printing (Additive Manufacturing):
- Design Considerations for Solid Plastic Objects
- 1. Part Geometry:
- 2. Wall Thickness:
- 3. Draft Angles:
- 4. Ribbing and Bossing:
- 5. Tolerances:
- 6. Surface Finish:
- Applications of Solid Plastic Objects: A Broad Spectrum
- Conclusion: The Unseen World of Solid Plastics
- Latest Posts
- Latest Posts
- Related Post
The Object Below is Made of Solid Plastic: Exploring the World of Plastic Fabrication
The seemingly simple statement, "The object below is made of solid plastic," opens a vast world of manufacturing processes, material properties, and design considerations. This statement implies a robustness, a certain level of durability, and a manufacturing pathway far removed from, say, a flimsy plastic film. Let's delve deeper into the implications of this statement, exploring the various types of solid plastics, their manufacturing processes, and the design choices that utilize their unique properties.
Understanding Solid Plastics: A Material Deep Dive
"Solid plastic" isn't a singular material; it encompasses a vast family of polymers, each with its own unique characteristics, strengths, weaknesses, and applications. The properties of a solid plastic object are directly determined by the type of plastic used in its fabrication. Some key factors to consider include:
1. Polymer Type:
This is the fundamental determinant of the plastic's properties. Common polymer types include:
-
Polyethylene (PE): Known for its flexibility, durability, and chemical resistance. Various densities (high-density polyethylene or HDPE, low-density polyethylene or LDPE) offer different performance characteristics. HDPE is often used for rigid containers, while LDPE finds use in flexible films and bags. In a solid object, HDPE would provide a stronger, more rigid structure.
-
Polypropylene (PP): Similar to PE but with higher melting points and greater strength. It's often chosen for its resistance to fatigue and chemicals, making it suitable for durable parts and applications requiring repeated stress. A solid object made of PP would exhibit good impact resistance and be relatively heat-resistant.
-
Polyvinyl Chloride (PVC): A versatile plastic known for its strength, durability, and resistance to weathering. It's often used in pipes, window frames, and other applications requiring long-term exposure to the elements. A solid PVC object would be resistant to degradation from UV light and moisture.
-
Polystyrene (PS): A relatively inexpensive plastic, known for its lightness and ease of molding. It's commonly used in disposable food containers and packaging. While a solid object made from PS might be lightweight, it lacks the strength and durability of other options.
-
Acrylonitrile Butadiene Styrene (ABS): A strong, rigid, and impact-resistant plastic often used in automotive parts, appliances, and toys. A solid ABS object would be robust, durable, and able to withstand significant impacts.
-
Polycarbonate (PC): A high-performance plastic known for its exceptional strength, impact resistance, and transparency. It's frequently used in safety glasses, protective shields, and other applications demanding high levels of impact resistance. A solid polycarbonate object would be exceptionally strong and resistant to shattering.
2. Additives and Fillers:
The properties of solid plastics can be significantly altered by the addition of various additives and fillers. These additions might:
-
Increase strength and rigidity: Fillers such as glass fibers or talc can significantly improve the mechanical strength and stiffness of the plastic.
-
Enhance impact resistance: Certain rubbery additives can increase the ability of the plastic to absorb impacts without fracturing.
-
Improve thermal stability: Additives can raise the melting point and reduce the plastic's susceptibility to warping or deformation at elevated temperatures.
-
Enhance UV resistance: Additives protect the plastic from degradation caused by exposure to ultraviolet light.
-
Improve flame retardancy: Additives can reduce the flammability of the plastic, making it safer for certain applications.
Manufacturing Processes for Solid Plastic Objects
The creation of a solid plastic object hinges on the chosen manufacturing process. Several key methods are employed:
1. Injection Molding:
This is the most widely used method for producing high-volume, complex-shaped solid plastic parts. Molten plastic is injected into a precisely engineered mold cavity under high pressure, where it cools and solidifies. The solidified part is then ejected from the mold. Injection molding allows for high precision, repeatability, and efficient mass production. Many everyday objects, from bottle caps to car parts, are manufactured using this method.
2. Extrusion:
Extrusion is suitable for producing long, continuous profiles of solid plastic, such as pipes, rods, and sheets. Molten plastic is continuously pushed through a die of the desired shape, solidifying as it exits. Extrusion is highly efficient for manufacturing consistent, long lengths of solid plastic materials.
3. Thermoforming:
This process involves heating a plastic sheet until it's pliable and then forming it into a desired shape using a mold. Thermoforming is often used for creating complex shapes or shallow draws in a cost-effective manner. It's suitable for producing both hollow and solid plastic objects.
4. Rotational Molding:
This method is ideal for producing large, hollow plastic parts with relatively thick walls. A powdered or liquid plastic material is placed inside a mold, which is then rotated in a heated oven. The plastic melts and distributes itself evenly across the interior of the mold, solidifying to create a hollow part. While often used for hollow objects, modifications allow for the creation of solid plastic components as well, by using more material or creating internal structural supports.
5. 3D Printing (Additive Manufacturing):
3D printing technologies, such as Fused Deposition Modeling (FDM) and Stereolithography (SLA), are increasingly used to create solid plastic prototypes and custom parts. These processes build the object layer by layer from a 3D digital model, allowing for intricate designs and customized geometries. While often slower than traditional methods, 3D printing offers unmatched design flexibility.
Design Considerations for Solid Plastic Objects
The design of a solid plastic object must consider the material's properties, manufacturing process, and intended application. Key aspects include:
1. Part Geometry:
The shape and size of the object will dictate the choice of manufacturing process and the overall cost. Simple shapes are generally easier and cheaper to produce than complex ones. Undercuts and internal features may require more complex molding techniques.
2. Wall Thickness:
Adequate wall thickness is crucial for ensuring the structural integrity of the object. Too thin a wall might lead to breakage or deformation, while excessively thick walls add unnecessary weight and cost. The chosen plastic type also influences the minimum required wall thickness.
3. Draft Angles:
Draft angles are slight tapers incorporated into the design to facilitate the removal of the part from the mold. Without adequate draft angles, the finished part may become stuck within the mold, hindering the manufacturing process.
4. Ribbing and Bossing:
Ribs and bosses are structural features added to increase the strength and rigidity of the part without significantly increasing its weight. These features are especially important for larger or thinner-walled objects.
5. Tolerances:
Manufacturing processes have inherent variations. Tolerances specify the acceptable range of deviations from the design dimensions. Understanding and specifying appropriate tolerances is crucial for ensuring the proper functioning of the finished object.
6. Surface Finish:
The surface finish of a solid plastic object can impact its aesthetics and performance. Different manufacturing processes yield different surface finishes. Post-processing techniques, such as polishing or texturing, can further refine the surface finish.
Applications of Solid Plastic Objects: A Broad Spectrum
The versatility of solid plastics translates into a nearly limitless range of applications across diverse industries. Examples include:
- Automotive: Bumpers, dashboards, interior components, and exterior trim.
- Electronics: Housings, casings, internal components, and connectors.
- Medical: Medical devices, surgical instruments, and equipment housings.
- Consumer Goods: Toys, packaging, household appliances, and furniture.
- Construction: Pipes, fittings, and window frames.
- Industrial: Machinery components, protective equipment, and conveyor systems.
Conclusion: The Unseen World of Solid Plastics
The seemingly simple phrase, "The object below is made of solid plastic," reveals a complex interplay of material science, manufacturing processes, and design considerations. Understanding the intricacies of different plastic types, manufacturing techniques, and design principles is key to creating functional, durable, and aesthetically pleasing solid plastic objects. The ubiquity of solid plastics in our daily lives underscores their significance and the ongoing evolution of their applications in an ever-changing technological landscape. The ongoing research and development in polymer science continue to push the boundaries of what's possible, leading to even more innovative and sustainable applications in the future. From the microscopic details of polymer chains to the macroscopic shapes of everyday objects, the world of solid plastics is a testament to human ingenuity and our ability to shape materials to meet our needs.
Latest Posts
Latest Posts
-
How Many Miles Is 75 Kilometers
May 20, 2025
-
How Many Pints In 7 Litres
May 20, 2025
-
75 Cm Is What In Inches
May 20, 2025
-
How Many Days Are In 40 Years
May 20, 2025
-
How Many Pounds In 14 Stones
May 20, 2025
Related Post
Thank you for visiting our website which covers about The Object Below Is Made Of Solid Plastic . We hope the information provided has been useful to you. Feel free to contact us if you have any questions or need further assistance. See you next time and don't miss to bookmark.