The Number Of Surface Flaws In Plastic Panels
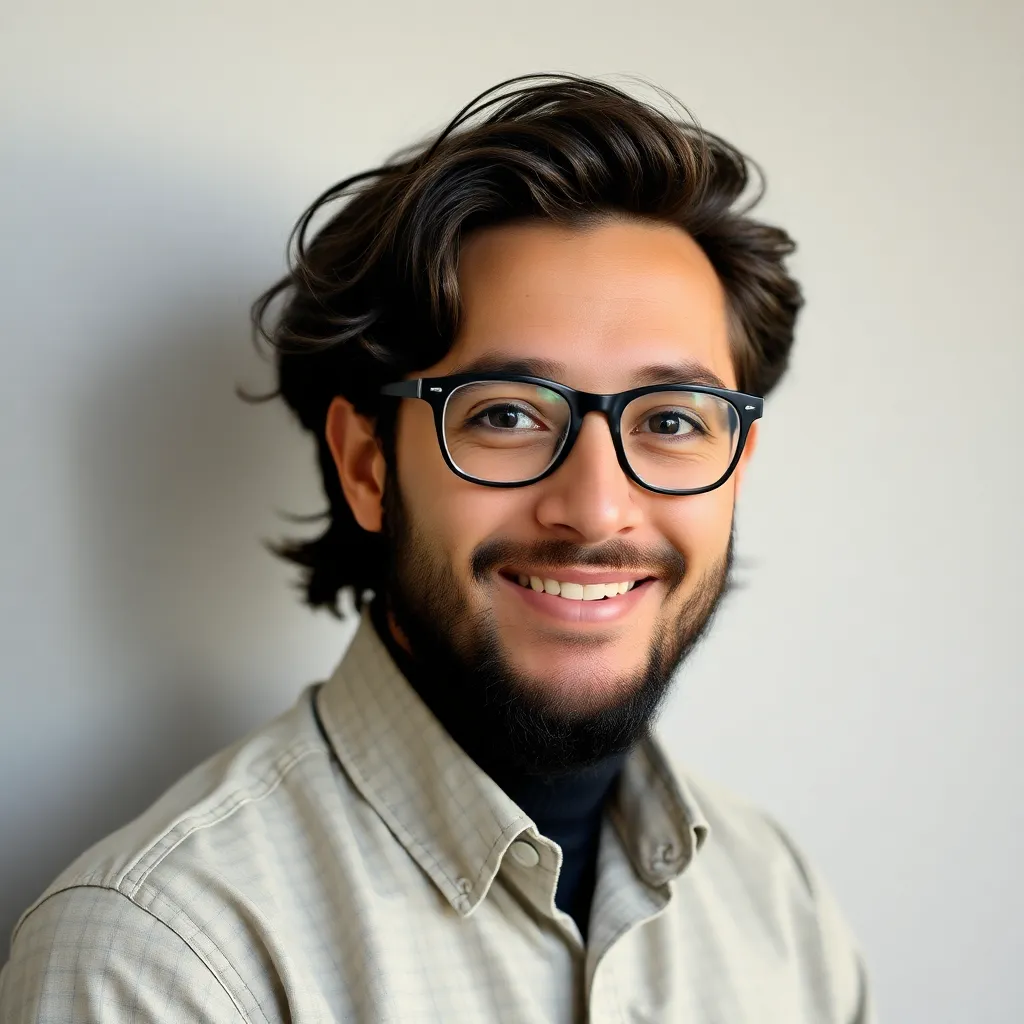
Holbox
May 09, 2025 · 6 min read
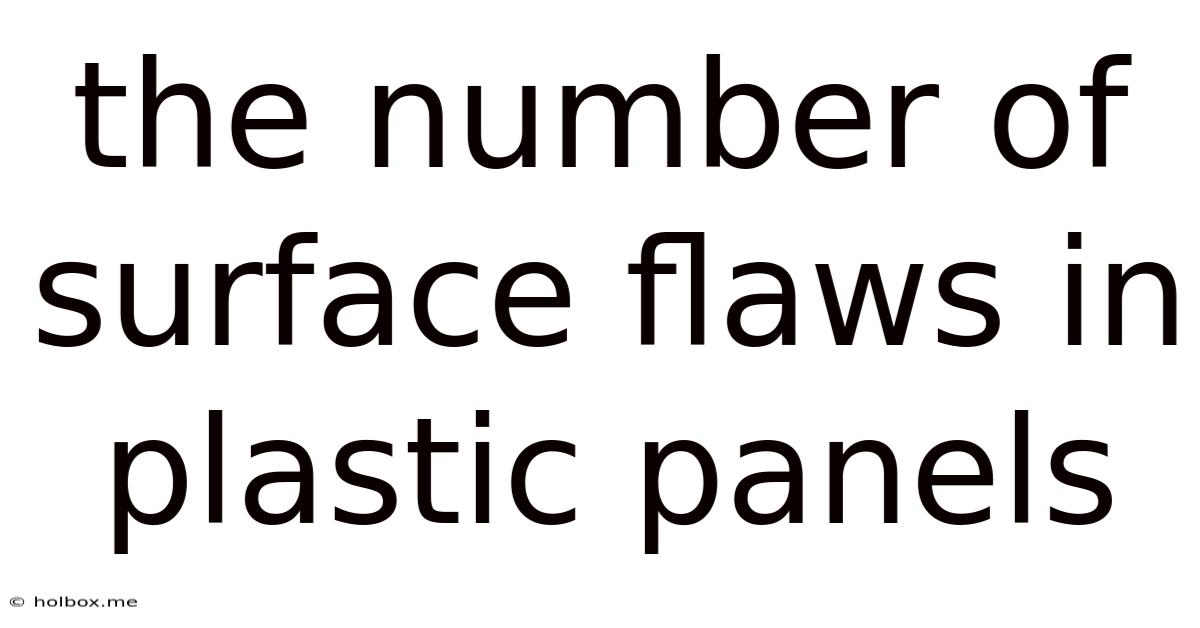
Table of Contents
- The Number Of Surface Flaws In Plastic Panels
- Table of Contents
- The Number of Surface Flaws in Plastic Panels: A Comprehensive Guide
- Understanding Surface Flaws: Types and Causes
- 1. Scratches and Abrasions:
- 2. Sinks and Short Shots:
- 3. Weld Lines:
- 4. Flow Marks:
- 5. Warpage and Distortion:
- 6. Contamination:
- 7. Burn Marks:
- 8. Fish Eyes:
- Quantifying Surface Flaws: Methods and Standards
- 1. Visual Inspection:
- 2. Automated Optical Inspection (AOI):
- 3. Tactile Inspection:
- 4. 3D Scanning:
- Standards and Specifications
- Impact of Surface Flaws on Product Performance and Aesthetics
- Aesthetic Impact:
- Functional Impact:
- Minimizing Surface Flaws: Preventative Measures
- 1. Raw Material Selection:
- 2. Mold Design and Maintenance:
- 3. Process Parameter Optimization:
- 4. Handling and Transportation:
- 5. Quality Control:
- Conclusion: Towards Flawless Plastic Panels
- Latest Posts
- Related Post
The Number of Surface Flaws in Plastic Panels: A Comprehensive Guide
The production of plastic panels, while efficient and cost-effective, is susceptible to the introduction of surface flaws. These imperfections, ranging from minor blemishes to significant defects, can significantly impact the aesthetic appeal, functional performance, and overall quality of the final product. Understanding the number and nature of these flaws is crucial for manufacturers aiming for high-quality output and for consumers making informed purchasing decisions. This comprehensive guide delves into the various aspects of surface flaws in plastic panels, exploring their causes, detection methods, and implications.
Understanding Surface Flaws: Types and Causes
Surface flaws in plastic panels manifest in diverse forms, each with its unique characteristics and origins. Categorizing these flaws helps in identifying root causes and implementing effective preventative measures. Here are some key types:
1. Scratches and Abrasions:
These are common flaws resulting from physical contact during manufacturing, handling, or transportation. Causes include improper handling, contact with sharp objects, inadequate protection during shipping, and friction from tooling during the molding process. The severity ranges from minor surface scratches barely visible to the naked eye to deep gouges affecting the structural integrity of the panel.
2. Sinks and Short Shots:
These flaws are characterized by depressions or incomplete filling of the mold cavity during the injection molding process. Causes include insufficient injection pressure, inadequate melt temperature, or issues with the mold design itself, such as insufficient venting. Sinks often appear as dimples or indentations, while short shots leave portions of the panel unfilled.
3. Weld Lines:
These occur when two separate streams of molten plastic merge during the molding process. The resulting line is often visible as a slightly raised ridge or discoloration. Causes include the merging of flows from multiple injection points or poor mold flow design. The prominence of weld lines depends heavily on the type of plastic and the molding parameters.
4. Flow Marks:
These are visible lines or patterns on the surface indicating the flow of the molten plastic during molding. While not always considered defects, pronounced flow marks can detract from the aesthetic appeal. Causes include uneven filling of the mold cavity, slow cooling rates, or improper mold design.
5. Warpage and Distortion:
These flaws involve uneven deformation of the plastic panel, resulting in bending, twisting, or buckling. Causes include uneven cooling, internal stresses within the material, or issues with the mold design leading to uneven shrinkage. Warpage can significantly affect the functionality and fit of the panel.
6. Contamination:
Foreign particles embedded in the surface of the panel during manufacturing constitute contamination. Causes include dust, debris, or other contaminants introduced into the molding process. The size and type of contaminant influence the severity of the flaw.
7. Burn Marks:
These appear as dark or discolored areas resulting from excessive heat during the molding process. Causes include high melt temperatures, prolonged exposure to heat, or inadequate cooling. Burn marks indicate a potential problem with the molding machinery or process parameters.
8. Fish Eyes:
These are small, transparent, blister-like formations on the surface of the panel. Causes include the entrapment of volatile gases or moisture within the molten plastic during molding. These are often difficult to prevent completely.
Quantifying Surface Flaws: Methods and Standards
Quantifying the number of surface flaws is essential for quality control and process optimization. Various methods are employed, depending on the type of flaw and the desired level of detail.
1. Visual Inspection:
This is the simplest and most common method, involving a trained inspector visually examining the panel for flaws. While subjective, visual inspection is effective for identifying readily visible defects.
2. Automated Optical Inspection (AOI):
AOI systems use cameras and image processing software to automatically detect and classify surface flaws. These systems provide a more objective and consistent assessment than manual inspection, particularly for high-volume production.
3. Tactile Inspection:
This method employs probes or other tactile sensors to detect surface irregularities. Tactile inspection is useful for identifying flaws not easily detectable by visual inspection alone.
4. 3D Scanning:
Advanced 3D scanning techniques capture detailed surface topography, allowing for precise quantification of flaw size, depth, and location. This method is valuable for detailed analysis and process optimization.
Standards and Specifications
Various industry standards and specifications define acceptable levels of surface flaws for specific applications. These standards often specify the maximum permissible number of flaws per unit area or the maximum allowable size of individual flaws. Adherence to these standards is crucial for ensuring product quality and meeting customer expectations. Examples include ISO standards applicable to plastics manufacturing.
Impact of Surface Flaws on Product Performance and Aesthetics
The presence of surface flaws can negatively impact both the aesthetic appeal and functional performance of plastic panels.
Aesthetic Impact:
Even minor surface flaws can detract from the overall appearance of a product, especially in applications where visual appeal is paramount. Scratches, discoloration, and other blemishes can make a panel appear less attractive and potentially reduce its market value.
Functional Impact:
Depending on the severity and location of the flaw, surface imperfections can compromise the functional performance of the panel. For example, deep scratches or cracks can weaken the structural integrity, while warpage can prevent proper fitting or assembly. In applications requiring precise tolerances, even minor deviations from the desired surface profile can be unacceptable.
Minimizing Surface Flaws: Preventative Measures
Preventing surface flaws requires a multifaceted approach encompassing all stages of the manufacturing process.
1. Raw Material Selection:
Using high-quality raw materials with consistent properties is crucial. Impurities or inconsistencies in the raw material can lead to a higher incidence of flaws.
2. Mold Design and Maintenance:
Proper mold design is critical for ensuring consistent and defect-free molding. Regular mold maintenance, including cleaning and polishing, helps prevent the introduction of scratches and other defects.
3. Process Parameter Optimization:
Precise control over process parameters, such as injection pressure, melt temperature, and cooling rates, minimizes the occurrence of various types of flaws.
4. Handling and Transportation:
Careful handling and adequate protection during transportation are essential for preventing scratches and other damage.
5. Quality Control:
Implementing robust quality control procedures, including regular inspection and testing, helps identify and address potential problems early in the manufacturing process.
Conclusion: Towards Flawless Plastic Panels
The number of surface flaws in plastic panels is a critical indicator of product quality and manufacturing efficiency. Understanding the types, causes, and detection methods of these flaws is crucial for manufacturers and consumers alike. By implementing preventative measures and employing effective quality control strategies, manufacturers can significantly reduce the incidence of surface flaws, thereby enhancing product quality, improving customer satisfaction, and maintaining a strong competitive edge in the market. Continuous improvement in manufacturing processes, coupled with advanced inspection technologies, paves the way for producing high-quality, aesthetically pleasing, and functionally reliable plastic panels. The pursuit of minimizing surface flaws is an ongoing endeavor, driven by the demand for high-quality products in various industries.
Latest Posts
Related Post
Thank you for visiting our website which covers about The Number Of Surface Flaws In Plastic Panels . We hope the information provided has been useful to you. Feel free to contact us if you have any questions or need further assistance. See you next time and don't miss to bookmark.