The Manufacturing Overhead Budget At Franklyn Corporation
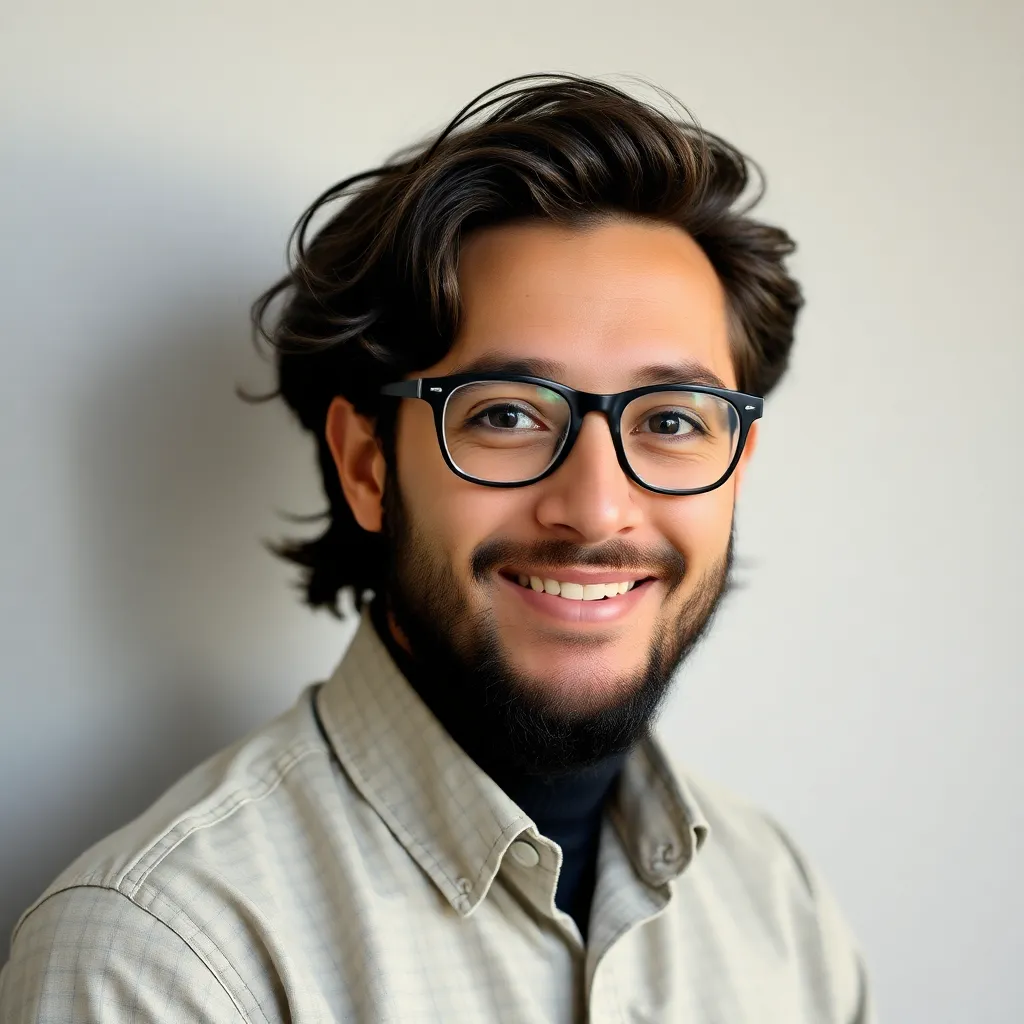
Holbox
Apr 03, 2025 · 6 min read

Table of Contents
- The Manufacturing Overhead Budget At Franklyn Corporation
- Table of Contents
- The Manufacturing Overhead Budget at Franklin Corporation: A Deep Dive
- Understanding Manufacturing Overhead
- Key Components of Manufacturing Overhead
- Franklin Corporation's Manufacturing Overhead Budget: A Detailed Breakdown
- 1. Forecasting Production Volume
- 2. Estimating Individual Overhead Costs
- 3. Allocating Overhead Costs
- 4. Preparing the Budget
- Potential Challenges in Budgeting Manufacturing Overhead
- 1. Inaccurate Cost Estimation
- 2. Difficulty in Allocating Overhead Costs
- 3. Fluctuating Production Volumes
- 4. External Factors
- Strategies for Effective Management of Manufacturing Overhead
- 1. Continuous Improvement Initiatives
- 2. Automation and Technology
- 3. Preventative Maintenance
- 4. Procurement Strategies
- 5. Activity-Based Costing (ABC)
- Conclusion
- Latest Posts
- Latest Posts
- Related Post
The Manufacturing Overhead Budget at Franklin Corporation: A Deep Dive
The manufacturing overhead budget is a crucial component of Franklin Corporation's overall financial planning. It's not just a line item; it's a strategic tool that influences production costs, profitability, and ultimately, the company's bottom line. This in-depth analysis will explore the intricacies of Franklin Corporation's manufacturing overhead budget, examining its key elements, potential challenges, and strategies for effective management.
Understanding Manufacturing Overhead
Before diving into Franklin Corporation's specifics, let's establish a foundational understanding of manufacturing overhead. Manufacturing overhead encompasses all indirect costs associated with the production process. These costs are not directly traceable to individual units of production, unlike direct materials and direct labor. Examples include:
Key Components of Manufacturing Overhead
- Indirect Labor: Salaries and wages of factory supervisors, maintenance personnel, quality control inspectors, and other support staff.
- Factory Supplies: Consumables such as lubricants, cleaning supplies, and small tools used in the production process.
- Depreciation: Allocation of the cost of factory equipment and machinery over their useful lives.
- Rent and Utilities: Costs associated with the factory building, including rent, electricity, gas, and water.
- Insurance: Premiums for property insurance covering the factory and its contents.
- Property Taxes: Taxes levied on the factory building and land.
- Maintenance and Repairs: Costs associated with maintaining and repairing factory equipment.
Franklin Corporation's Manufacturing Overhead Budget: A Detailed Breakdown
Franklin Corporation's manufacturing overhead budget is likely a comprehensive document, detailing expected costs for each category mentioned above. The budgeting process itself typically involves several key steps:
1. Forecasting Production Volume
The first step in preparing the manufacturing overhead budget is to forecast the expected production volume for the budgeting period. This forecast influences the amount of overhead costs that will be incurred. For instance, higher production volume might lead to increased indirect labor costs (more supervisors needed), higher utility consumption, and greater depreciation expense.
2. Estimating Individual Overhead Costs
Once the production volume is estimated, Franklin Corporation's budgeting team needs to estimate the individual overhead cost components. This requires careful analysis of past data, industry trends, and anticipated changes in operational factors. For example:
- Indirect Labor: The team might analyze historical data on indirect labor hours per unit of production and project future needs based on the projected production volume. They might also factor in any anticipated wage increases or changes in staffing levels.
- Factory Supplies: Past consumption patterns of various factory supplies can be used to estimate future needs, accounting for any planned changes in production processes or efficiency improvements.
- Depreciation: This is typically calculated based on the company's depreciation policy and the estimated useful life of its factory equipment.
- Rent and Utilities: These costs might be fixed or variable, depending on Franklin Corporation's contracts with landlords and utility providers. The budget should reflect this distinction.
- Insurance and Property Taxes: These are usually relatively predictable and can be estimated based on current rates and assessments.
- Maintenance and Repairs: Predicting these costs is more challenging and requires careful assessment of the condition of factory equipment and potential maintenance needs. This might involve consulting with maintenance personnel.
3. Allocating Overhead Costs
After estimating individual overhead costs, Franklin Corporation must determine how to allocate these costs to different products or production departments. Common allocation methods include:
- Direct Labor Hours: Allocates overhead based on the number of direct labor hours used in producing each product.
- Machine Hours: Allocates overhead based on the number of machine hours used in producing each product.
- Square Footage: Allocates overhead based on the space occupied by each production department.
The choice of allocation method impacts product costing and pricing decisions. Franklin Corporation should carefully consider which method best reflects the consumption of overhead resources by different products.
4. Preparing the Budget
Finally, Franklin Corporation compiles all the estimated overhead costs into a comprehensive budget. This budget typically presents a detailed breakdown of expected overhead costs by category and allocation method. It also usually includes a variance analysis section to compare actual costs to budgeted costs. This variance analysis is critical for identifying areas of cost overruns or savings and making necessary adjustments.
Potential Challenges in Budgeting Manufacturing Overhead
Budgeting manufacturing overhead is not without its challenges. Franklin Corporation's budgeting team might encounter the following difficulties:
1. Inaccurate Cost Estimation
Estimating overhead costs accurately can be difficult, particularly for items like maintenance and repairs. Unexpected equipment failures or changes in utility rates can significantly impact actual costs. To mitigate this risk, Franklin Corporation should use robust forecasting techniques and regularly review and adjust the budget as new information becomes available.
2. Difficulty in Allocating Overhead Costs
Allocating overhead costs fairly and accurately across different products or departments can be complex. The chosen allocation method can significantly impact product costs and pricing decisions. Franklin Corporation should carefully select an allocation method that accurately reflects the consumption of overhead resources.
3. Fluctuating Production Volumes
Unpredictable changes in production volume can make it challenging to accurately estimate overhead costs. Unexpected surges or declines in demand can lead to significant variances between budgeted and actual costs. Franklin Corporation should incorporate contingency planning into its budget to accommodate potential fluctuations in production volume.
4. External Factors
External factors such as economic conditions, inflation, and changes in government regulations can also impact manufacturing overhead costs. Franklin Corporation needs to consider these external factors when preparing its budget and incorporate contingency plans for unforeseen circumstances.
Strategies for Effective Management of Manufacturing Overhead
Effective management of manufacturing overhead is crucial for Franklin Corporation's profitability. The following strategies can help enhance overhead control:
1. Continuous Improvement Initiatives
Implementing lean manufacturing principles and continuous improvement initiatives can help reduce waste and improve efficiency, leading to lower overhead costs. Regularly evaluating processes and identifying areas for improvement is key.
2. Automation and Technology
Investing in automation and advanced technologies can streamline production processes, reduce labor costs, and improve efficiency. This could involve implementing robotics, advanced software, or other technologies to automate repetitive tasks.
3. Preventative Maintenance
Regular preventative maintenance on factory equipment can help minimize costly breakdowns and repairs. A well-maintained facility will experience fewer disruptions and reduced maintenance costs over the long term.
4. Procurement Strategies
Effective procurement strategies can help reduce the cost of factory supplies and other materials. Negotiating favorable contracts with suppliers, implementing inventory management techniques, and exploring alternative suppliers can all contribute to cost savings.
5. Activity-Based Costing (ABC)
Implementing ABC costing can provide a more accurate and detailed picture of manufacturing overhead costs. ABC costing assigns overhead costs based on specific activities rather than simply using blanket allocation methods. This leads to more precise cost information for decision-making.
Conclusion
The manufacturing overhead budget at Franklin Corporation is a vital financial planning tool that affects its profitability and competitiveness. By carefully forecasting costs, selecting appropriate allocation methods, and implementing effective management strategies, Franklin Corporation can control its overhead expenses and maintain a healthy bottom line. Continuous monitoring, analysis, and adaptation of the budget are crucial to its effectiveness in achieving the company's overall financial goals. The challenges associated with overhead budgeting are substantial, but with proactive planning and the strategic implementation of cost-saving measures, Franklin Corporation can optimize its operations and thrive in a competitive marketplace.
Latest Posts
Latest Posts
-
Which Of The Following Statements Regarding Rebound Tenderness Is Correct
Apr 09, 2025
-
Using Family Suffixes To Name Organic Compounds
Apr 09, 2025
-
Every Society Faces Economic Trade Offs This Means
Apr 09, 2025
-
Textbook Of Adult Gerontology Primary Care Nursing
Apr 09, 2025
-
Who Is Most At Risk For Perpetrating Type 2 Violence
Apr 09, 2025
Related Post
Thank you for visiting our website which covers about The Manufacturing Overhead Budget At Franklyn Corporation . We hope the information provided has been useful to you. Feel free to contact us if you have any questions or need further assistance. See you next time and don't miss to bookmark.