The Goals Of Both Kanban And Mrp Include
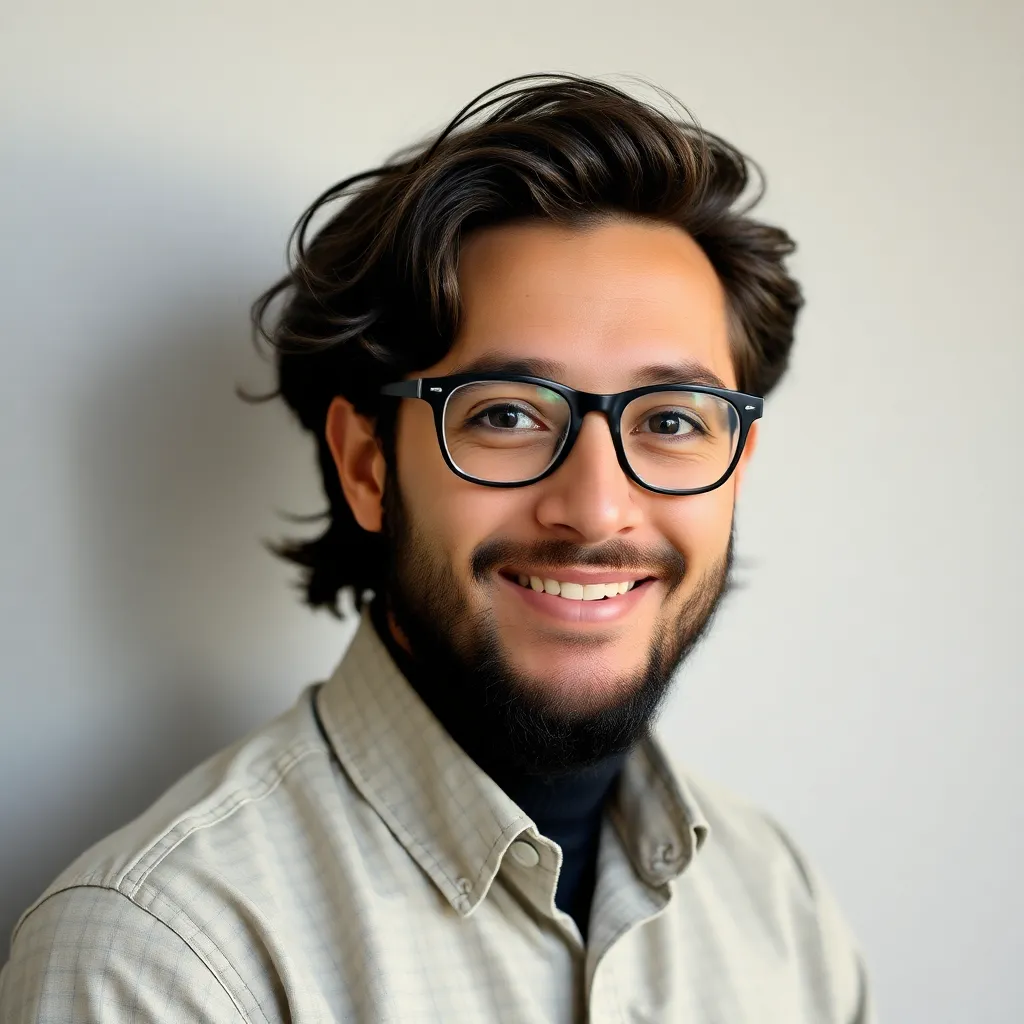
Holbox
May 13, 2025 · 7 min read
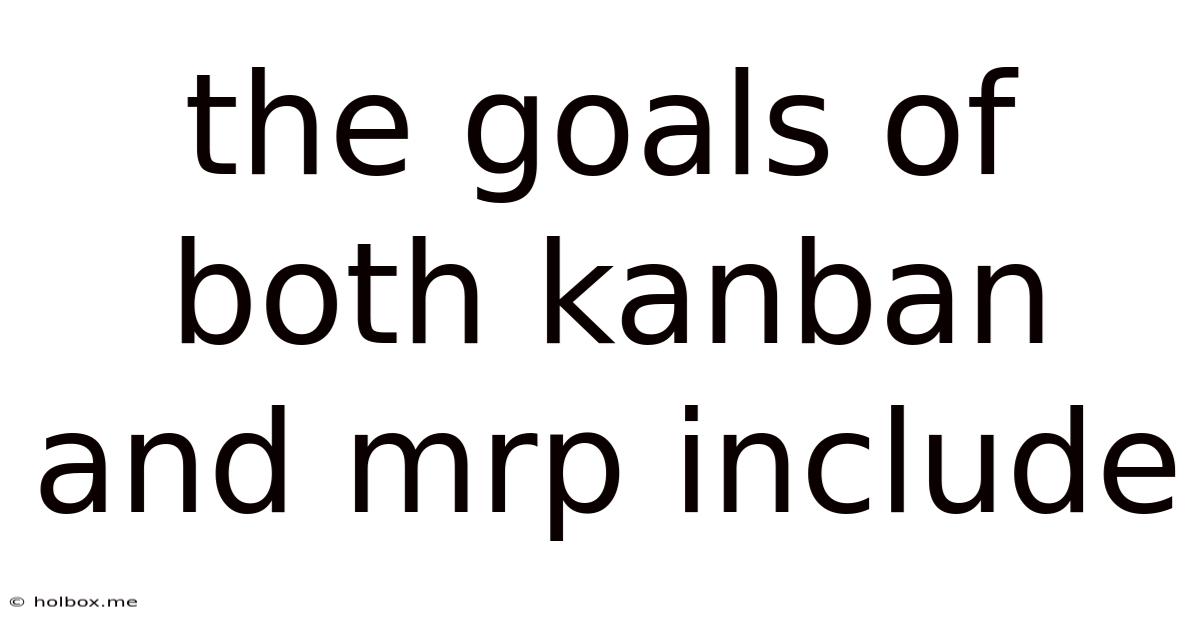
Table of Contents
- The Goals Of Both Kanban And Mrp Include
- Table of Contents
- The Goals of Both Kanban and MRP: A Comparative Analysis
- Kanban's Primary Goals: Optimizing Workflow and Reducing Waste
- 1. Visualizing Workflow: The Power of Transparency
- 2. Limiting Work in Progress (WIP): Enhancing Focus and Efficiency
- 3. Improving Flow: Optimizing the Entire Process
- 4. Continuous Improvement (Kaizen): Embracing a Culture of Learning
- MRP's Primary Goals: Managing Inventory and Production Planning
- 1. Accurate Inventory Control: Maintaining Optimal Stock Levels
- 2. Optimized Production Scheduling: Meeting Deadlines Efficiently
- 3. Reducing Production Costs: Minimizing Waste and Maximizing Efficiency
- 4. Enhanced Supply Chain Visibility: Understanding Material Flows
- Key Differences Between Kanban and MRP
- When to Use Kanban and When to Use MRP
- Combining Kanban and MRP: A Synergistic Approach
- Conclusion: Choosing the Right System for Your Needs
- Latest Posts
- Related Post
The Goals of Both Kanban and MRP: A Comparative Analysis
Both Kanban and Material Requirements Planning (MRP) are crucial tools for managing workflows and inventory, but they achieve their goals through different approaches and are best suited for different contexts. Understanding their core objectives is key to selecting the right system for your specific needs. This article delves deep into the goals of Kanban and MRP, highlighting their similarities and differences to provide a comprehensive understanding.
Kanban's Primary Goals: Optimizing Workflow and Reducing Waste
Kanban, originating from Toyota's lean manufacturing principles, primarily focuses on visualizing workflow, limiting work in progress (WIP), and improving flow. Its goals center around streamlining processes and eliminating waste, leading to increased efficiency and improved quality. Let's break down the key objectives:
1. Visualizing Workflow: The Power of Transparency
A core goal of Kanban is to make the workflow completely transparent. This is achieved through visual Kanban boards, which depict the progress of tasks through different stages of the process. This visualization allows everyone involved to understand:
- Current Status: The board provides a real-time snapshot of where each task is in the process.
- Bottlenecks: Visualizing the workflow quickly highlights areas where tasks are piling up, indicating potential bottlenecks that need attention.
- Work in Progress (WIP): The Kanban board clearly shows how many tasks are currently being worked on, facilitating WIP limits.
- Lead Times: Tracking task progression enables a clear understanding of the time it takes for a task to move through the entire workflow.
This transparency fosters better collaboration, improved communication, and proactive problem-solving.
2. Limiting Work in Progress (WIP): Enhancing Focus and Efficiency
Kanban emphasizes limiting the amount of work in progress at any given time. By restricting WIP, teams focus their efforts on completing existing tasks before starting new ones. This leads to several benefits:
- Reduced Cycle Time: Focusing on fewer tasks concurrently accelerates the completion of individual tasks and reduces overall lead time.
- Improved Quality: Concentrated efforts minimize errors and rework, resulting in higher-quality outputs.
- Enhanced Predictability: By limiting WIP, teams gain better control over their workload, improving predictability and meeting deadlines more consistently.
- Reduced Context Switching: Constantly switching between multiple tasks diminishes efficiency. WIP limits help maintain focus and prevent the cognitive overhead associated with multitasking.
3. Improving Flow: Optimizing the Entire Process
Kanban aims to optimize the entire workflow, ensuring a smooth and continuous flow of work from beginning to end. This involves identifying and removing impediments to flow, such as:
- Bottlenecks: Addressing bottlenecks is crucial for maintaining a consistent flow. This often involves identifying and resolving root causes of delays.
- Waiting Times: Minimizing waiting times between stages of the workflow is essential. This may involve process improvements or better coordination between teams.
- Handoffs: Streamlining handoffs between different stages of the workflow minimizes delays and confusion.
- Defects: Identifying and rectifying defects early in the process prevents delays and rework later on.
By continuously improving flow, Kanban helps to maximize efficiency and minimize waste throughout the entire process.
4. Continuous Improvement (Kaizen): Embracing a Culture of Learning
Kanban isn't a static system; it emphasizes continuous improvement. Regular reviews and retrospectives are essential for identifying areas for enhancement and adapting the process to optimize performance. This constant feedback loop ensures continuous learning and adaptation, making Kanban a dynamic and ever-evolving system.
MRP's Primary Goals: Managing Inventory and Production Planning
Material Requirements Planning (MRP) focuses on efficient inventory management and production planning. Its goals are centered around ensuring that the right materials are available at the right time in the right quantities to meet production demands. This involves detailed planning and control over material flows. Let's explore the key objectives:
1. Accurate Inventory Control: Maintaining Optimal Stock Levels
MRP's primary goal is to maintain accurate inventory levels. This involves:
- Demand Forecasting: Accurately predicting future demand for finished goods is crucial for determining the required raw materials.
- Material Planning: Based on demand forecasts, MRP calculates the required quantities of each raw material, considering lead times and safety stock levels.
- Inventory Tracking: Maintaining accurate records of current inventory levels is crucial for efficient planning and control.
- Reorder Point Calculation: MRP determines the reorder point for each item, ensuring that sufficient inventory is available to meet production requirements without excessive stock.
Accurate inventory control minimizes storage costs, prevents stockouts, and optimizes the flow of materials.
2. Optimized Production Scheduling: Meeting Deadlines Efficiently
MRP aims to optimize production scheduling to ensure timely delivery of finished goods. This involves:
- Capacity Planning: Determining whether the available production capacity is sufficient to meet planned production levels.
- Scheduling Optimization: Creating a production schedule that maximizes efficiency and minimizes lead times.
- Resource Allocation: Allocating available resources effectively to meet production demands.
- Order Sequencing: Optimizing the order in which production orders are processed to minimize delays and maximize efficiency.
Effective production scheduling reduces lead times, improves on-time delivery, and enhances overall production efficiency.
3. Reducing Production Costs: Minimizing Waste and Maximizing Efficiency
MRP contributes to cost reduction through:
- Reduced Inventory Holding Costs: Maintaining optimal stock levels minimizes storage costs, insurance, and obsolescence risks.
- Improved Production Efficiency: Optimized scheduling minimizes downtime and maximizes utilization of resources.
- Reduced Material Waste: Accurate planning minimizes excess materials and reduces waste.
- Better Purchasing Decisions: Efficient inventory management leads to better purchasing decisions, optimizing pricing and delivery times.
By minimizing waste and maximizing efficiency, MRP directly contributes to reducing overall production costs.
4. Enhanced Supply Chain Visibility: Understanding Material Flows
MRP provides a clear picture of the entire supply chain, highlighting potential issues and opportunities for improvement. This enhanced visibility allows for proactive adjustments and better management of material flows.
Key Differences Between Kanban and MRP
While both Kanban and MRP aim for efficiency, their approaches differ significantly:
Feature | Kanban | MRP |
---|---|---|
Focus | Workflow optimization, reducing waste | Inventory management, production planning |
Methodology | Evolutionary, iterative | Predictive, planning-driven |
Implementation | Relatively simple, visual | Complex, requires detailed data input |
Suitability | Small to medium-sized teams, software development, service industries | Manufacturing, large-scale production |
Inventory Control | Indirect; focuses on limiting WIP | Direct; core functionality |
Predictability | Adaptable to changing demands | Relies on accurate demand forecasts |
When to Use Kanban and When to Use MRP
The choice between Kanban and MRP depends heavily on the specific context and organizational needs.
Kanban is best suited for:
- Projects with uncertain requirements: Kanban's flexibility makes it ideal for projects where requirements may evolve over time.
- Small to medium-sized teams: Kanban's simplicity makes it easy to implement and manage in smaller teams.
- Service industries or software development: Kanban is highly effective in managing knowledge work.
- Situations where flexibility and responsiveness are paramount: Kanban adapts readily to change.
MRP is best suited for:
- Large-scale manufacturing operations: MRP is designed for managing complex production processes with many components.
- Industries with high inventory levels: MRP's focus on inventory control is essential in such situations.
- Situations requiring precise production planning: MRP provides detailed schedules and inventory projections.
- Environments with relatively stable demand forecasts: MRP's predictive nature requires reliable demand forecasts.
Combining Kanban and MRP: A Synergistic Approach
In some cases, a combination of Kanban and MRP can yield significant benefits. For example, Kanban can be used to manage the workflow within a specific production stage, while MRP manages the overall production planning and inventory control. This hybrid approach leverages the strengths of both systems, achieving a more robust and efficient system.
Conclusion: Choosing the Right System for Your Needs
Both Kanban and MRP are powerful tools for improving efficiency and productivity. However, their goals and approaches differ significantly. Understanding these differences is crucial for selecting the right system to meet your specific needs. By carefully considering the nature of your operations, the size of your team, and the level of predictability in your demand, you can choose the system that will best support your organizational goals. Remember that continuous improvement and adaptation are vital aspects of both methodologies, allowing for ongoing optimization and enhanced performance over time. Through careful implementation and ongoing refinement, both Kanban and MRP can significantly contribute to achieving operational excellence.
Latest Posts
Related Post
Thank you for visiting our website which covers about The Goals Of Both Kanban And Mrp Include . We hope the information provided has been useful to you. Feel free to contact us if you have any questions or need further assistance. See you next time and don't miss to bookmark.