The Goal Of Lean Manufacturing Is To
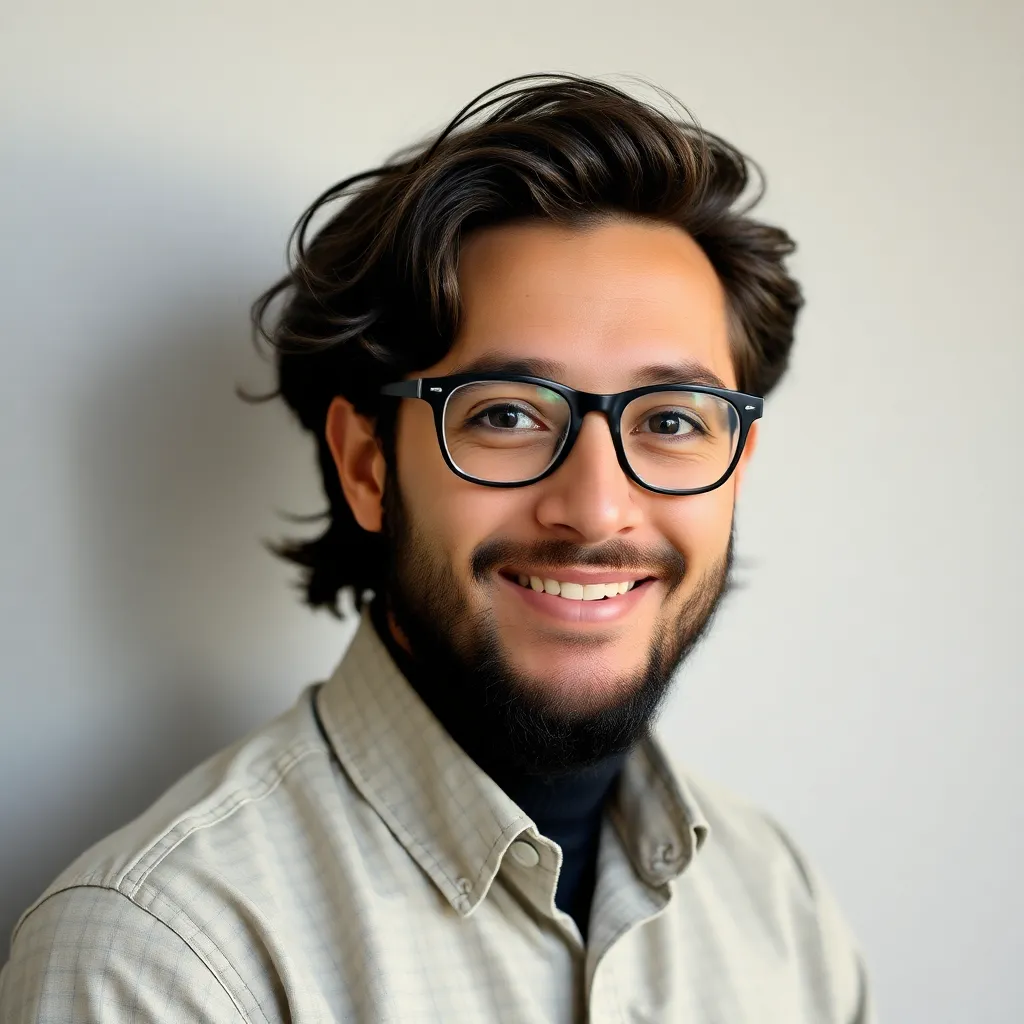
Holbox
May 08, 2025 · 7 min read
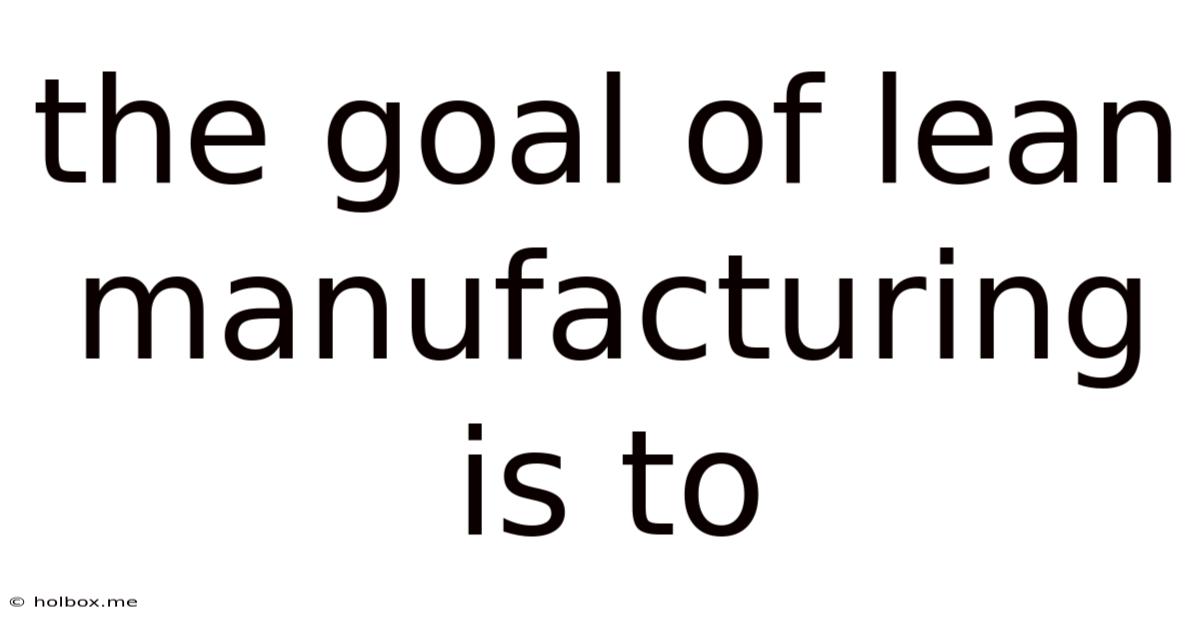
Table of Contents
- The Goal Of Lean Manufacturing Is To
- Table of Contents
- The Goal of Lean Manufacturing Is To… Eliminate Waste and Maximize Value
- Understanding the Seven Wastes (Muda)
- 1. Transportation: Unnecessary Movement of Materials
- 2. Inventory: Excess Materials and Work-in-Progress (WIP)
- 3. Motion: Unnecessary Movement of People
- 4. Waiting: Idle Time and Delays
- 5. Overproduction: Producing More Than Needed
- 6. Over-Processing: Unnecessary Steps in Production
- 7. Defects: Errors and Rework
- Beyond the Seven Wastes: Expanding the Lean Perspective
- Maximizing Value: The Other Side of the Coin
- Tangible Benefits of Lean Manufacturing
- Implementing Lean Manufacturing: A Step-by-Step Approach
- Conclusion: Embracing the Lean Philosophy for Sustainable Success
- Latest Posts
- Related Post
The Goal of Lean Manufacturing Is To… Eliminate Waste and Maximize Value
Lean manufacturing, a philosophy born from the Toyota Production System (TPS), has revolutionized how businesses approach production and operations. Its core goal isn't simply to produce more or reduce costs, though those are often outcomes. The overarching objective is far more nuanced and impactful: to eliminate waste and maximize value. This seemingly simple statement encompasses a profound shift in mindset and operational practices. Let's delve into this goal, exploring its various facets and how it translates into tangible benefits for businesses of all sizes.
Understanding the Seven Wastes (Muda)
The heart of lean manufacturing lies in identifying and eliminating waste, known in Japanese as muda. Lean practitioners traditionally focus on seven key types of waste:
1. Transportation: Unnecessary Movement of Materials
This waste encompasses the movement of materials between processes, storage locations, and departments. Inefficient layouts, excessive distances between workstations, and poorly planned material handling systems all contribute to transportation waste. Reducing this waste involves optimizing layouts, implementing efficient material handling techniques (like kanban), and strategically locating resources.
Example: A manufacturing plant where raw materials need to be transported across the facility multiple times before reaching the final assembly line. Lean principles would suggest reorganizing the layout to minimize these movements.
2. Inventory: Excess Materials and Work-in-Progress (WIP)
Holding excessive inventory ties up capital, increases storage costs, masks problems within the production process, and risks obsolescence or damage. Lean aims to reduce inventory to the absolute minimum necessary, only holding what's needed for immediate production. This requires accurate forecasting, improved production planning, and just-in-time (JIT) inventory systems.
Example: A retailer holding excessive stock of slow-moving items, tying up valuable capital and risking markdown losses. Lean principles would suggest improved forecasting and closer collaboration with suppliers.
3. Motion: Unnecessary Movement of People
This refers to wasted movement by workers, often due to poor workstation design, inefficient processes, or a lack of ergonomic considerations. Minimizing motion involves optimizing workstation layout, streamlining processes to reduce unnecessary steps, and investing in ergonomic equipment and tools.
Example: A factory worker constantly reaching and bending to access parts located in awkward positions. Lean principles would suggest redesigning the workstation to minimize unnecessary movements and improve ergonomics.
4. Waiting: Idle Time and Delays
Waiting time is a significant source of waste, whether it involves workers waiting for materials, machines waiting for processing, or customers waiting for service. Eliminating waiting requires carefully synchronizing processes, reducing bottlenecks, and implementing systems to ensure a smooth flow of work.
Example: A production line where workers are frequently idle because of delays in receiving materials. Lean principles would suggest implementing a pull system and better supply chain management.
5. Overproduction: Producing More Than Needed
Overproduction is arguably the worst form of waste, as it leads to increased inventory, storage costs, potential obsolescence, and ultimately, wasted resources. Lean focuses on producing only what is needed, when it is needed. This often involves implementing just-in-time (JIT) production systems and closely coordinating with customers to meet demand precisely.
Example: A manufacturer producing large batches of goods in anticipation of demand, only to find that actual demand is lower than projected. Lean principles would suggest adopting a more flexible, demand-driven production model.
6. Over-Processing: Unnecessary Steps in Production
This waste refers to performing more work than is actually necessary to meet customer requirements. Lean aims to simplify processes, removing unnecessary steps and focusing on value-added activities. This might involve streamlining workflows, automating tasks, or improving process design.
Example: A manufacturing process that includes several unnecessary steps that add no value to the final product. Lean principles would suggest streamlining the process and eliminating non-value-added activities.
7. Defects: Errors and Rework
Defects lead to rework, scrap, customer dissatisfaction, and increased costs. Lean emphasizes quality control throughout the production process, aiming to prevent defects rather than correcting them later. This often involves implementing quality checks at each stage of production, empowering employees to identify and address problems, and using statistical process control (SPC).
Example: A production line producing defective products that need to be scrapped or reworked. Lean principles would suggest implementing robust quality control measures to prevent defects from occurring in the first place.
Beyond the Seven Wastes: Expanding the Lean Perspective
While the seven wastes are foundational, a comprehensive lean approach also considers other forms of waste, including:
- Underutilization of Employees: Failing to fully utilize the skills and talents of employees, leading to decreased morale and missed opportunities for innovation.
- Extra Inventory of Information: Accumulation of unnecessary data or information that hinders decision-making and increases processing time.
- Extra Inventory of Equipment: Holding excess equipment that is rarely used or maintained, leading to increased costs and potential safety hazards.
Maximizing Value: The Other Side of the Coin
Eliminating waste is only half the equation. Lean manufacturing is equally concerned with maximizing value, which means delivering products and services that meet customer needs and expectations efficiently and effectively. This involves:
- Understanding Customer Needs: Lean emphasizes a deep understanding of customer requirements, ensuring that only value-added activities are performed.
- Continuous Improvement (Kaizen): Lean is a dynamic process, not a static endpoint. Continuous improvement is fundamental to identifying and eliminating further waste and enhancing value.
- Respect for People: Lean recognizes the importance of empowering employees, fostering teamwork, and creating a positive work environment.
- Value Stream Mapping: This powerful tool helps visualize the entire production process, identifying areas where waste can be eliminated and value can be enhanced.
Tangible Benefits of Lean Manufacturing
Implementing lean principles can lead to significant improvements across various aspects of a business:
- Reduced Costs: Eliminating waste directly translates to lower production costs, including materials, labor, and overhead.
- Improved Quality: Preventing defects and emphasizing quality control results in higher-quality products and increased customer satisfaction.
- Increased Efficiency: Streamlining processes and optimizing workflows leads to greater efficiency and faster production times.
- Enhanced Productivity: By eliminating waste and improving workflows, workers become more productive and engaged.
- Improved Customer Satisfaction: Delivering higher-quality products on time and at a competitive price leads to increased customer loyalty.
- Increased Flexibility: Lean systems are often more adaptable to changing market demands and can respond quickly to customer needs.
- Improved Safety: A cleaner, more organized workplace, and improved processes often lead to a safer working environment.
Implementing Lean Manufacturing: A Step-by-Step Approach
Implementing lean manufacturing is a journey, not a destination. It requires a systematic approach, including:
- Leadership Commitment: Successful lean implementation requires buy-in from top management.
- Teamwork and Collaboration: Lean relies on cross-functional teams working together to identify and eliminate waste.
- Training and Education: Employees need to be trained on lean principles and techniques.
- Data-Driven Decision Making: Lean relies on data to identify areas for improvement and track progress.
- Continuous Improvement: Kaizen, or continuous improvement, is an ongoing process.
- Measurement and Evaluation: Regularly measuring key performance indicators (KPIs) is essential to track progress and identify areas needing attention.
Conclusion: Embracing the Lean Philosophy for Sustainable Success
The goal of lean manufacturing is not simply about reducing costs or increasing production; it's about creating a sustainable, value-driven business model that benefits both the company and its customers. By focusing on eliminating waste and maximizing value, organizations can achieve significant improvements in efficiency, quality, and profitability, establishing a competitive advantage in today's dynamic marketplace. The journey towards lean requires commitment, collaboration, and a constant pursuit of improvement, but the rewards are well worth the effort. Embracing the lean philosophy is not just about implementing tools and techniques; it's about cultivating a culture of continuous improvement and respect for people, paving the way for long-term success and sustainability.
Latest Posts
Related Post
Thank you for visiting our website which covers about The Goal Of Lean Manufacturing Is To . We hope the information provided has been useful to you. Feel free to contact us if you have any questions or need further assistance. See you next time and don't miss to bookmark.