The Foundation For Managing Processes And Value Chains Is
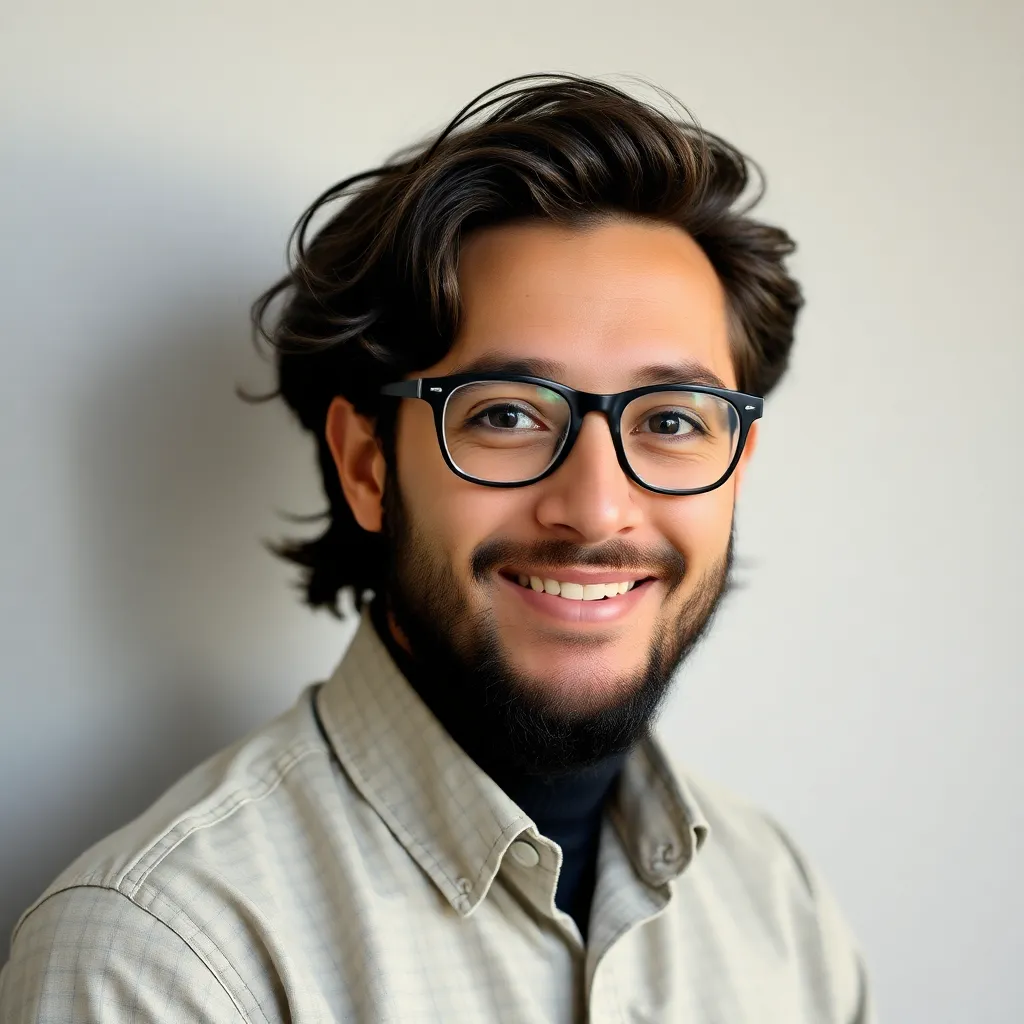
Holbox
May 12, 2025 · 7 min read
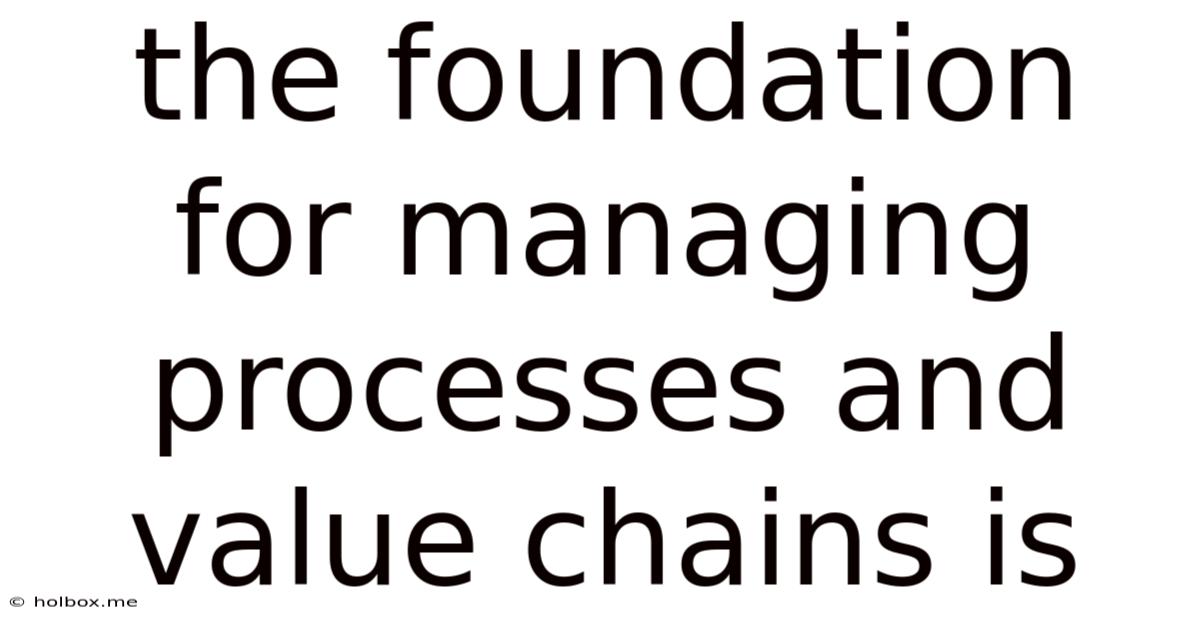
Table of Contents
- The Foundation For Managing Processes And Value Chains Is
- Table of Contents
- The Foundation for Managing Processes and Value Chains Is… Understanding
- 1. Clear Definition of Processes and Value Chains
- 1.1 Processes: A Detailed Look
- 1.2 Value Chains: Creating and Delivering Value
- 2. Data-Driven Process Analysis and Improvement
- 2.1 Data Collection and Analysis: The Cornerstone of Improvement
- 2.2 Identifying Bottlenecks and Waste
- 2.3 Implementing Improvements and Measuring Results
- 3. Technology's Role in Process and Value Chain Management
- 3.1 ERP Systems: Integrating Processes Across the Organization
- 3.2 Workflow Automation Tools: Streamlining Processes
- 3.3 Data Analytics and Business Intelligence: Driving Informed Decisions
- 4. People and Culture: The Human Element
- 4.1 Employee Engagement and Empowerment
- 4.2 Training and Development: Building Capabilities
- 4.3 Culture of Continuous Improvement: Embracing Change
- 5. Alignment with Business Strategy: A Holistic Approach
- 5.1 Linking Processes to Strategic Goals
- 5.2 Adaptability and Flexibility: Responding to Change
- 6. Measuring and Monitoring Performance: Continuous Improvement
- 6.1 Key Performance Indicators (KPIs): Tracking Progress
- 6.2 Regular Reviews and Adjustments: Adapting to Change
- Latest Posts
- Latest Posts
- Related Post
The Foundation for Managing Processes and Value Chains Is… Understanding
The foundation for effectively managing processes and value chains lies not in complex software or intricate methodologies, but in a deep, nuanced understanding of several key elements. This understanding forms the bedrock upon which successful process optimization, value creation, and sustainable competitive advantage are built. This article will delve into the crucial elements that constitute this foundation, exploring their interconnectedness and highlighting their importance for businesses of all sizes.
1. Clear Definition of Processes and Value Chains
Before embarking on any process improvement or value chain optimization initiative, a crystal-clear understanding of what constitutes a process and a value chain is paramount. Many organizations struggle because they lack a consistent, well-defined terminology and approach.
1.1 Processes: A Detailed Look
A process is a series of interconnected activities designed to achieve a specific outcome. This outcome could range from manufacturing a product to onboarding a new client. Crucially, processes must be defined with specific inputs, outputs, activities, and metrics. Without clearly defined boundaries and measurable outcomes, process improvement efforts become futile. Consider these key elements for effective process definition:
- Inputs: What resources (materials, information, people) are required to initiate the process?
- Activities: What steps are involved in transforming the inputs into outputs?
- Outputs: What is the final product or service delivered by the process?
- Metrics: How will the success and efficiency of the process be measured? (e.g., cycle time, defect rate, customer satisfaction)
- Owners: Who is accountable for the performance of the process?
1.2 Value Chains: Creating and Delivering Value
A value chain represents the entire series of activities a company undertakes to create and deliver value to its customers. It encompasses all primary activities (directly involved in creating and delivering the product or service) and support activities (indirectly contributing to the creation and delivery of value). Understanding your value chain helps pinpoint areas for improvement, cost reduction, and differentiation. Key aspects to consider:
- Primary Activities: Inbound logistics (receiving, storing, and distributing inputs), operations (transforming inputs into outputs), outbound logistics (collecting, storing, and distributing outputs), marketing and sales, and service.
- Support Activities: Firm infrastructure, human resource management, technology development, and procurement.
- Value Proposition: What unique value does the company offer its customers? How does the value chain contribute to delivering this value proposition?
2. Data-Driven Process Analysis and Improvement
Once processes and value chains are clearly defined, the next crucial step involves analyzing their performance using data. This data-driven approach is fundamental to identifying areas for improvement and optimizing the overall efficiency and effectiveness.
2.1 Data Collection and Analysis: The Cornerstone of Improvement
Effective process management relies heavily on accurate and reliable data. Gathering data from various sources, such as operational systems, customer feedback, and employee surveys, is essential. Techniques like process mapping, value stream mapping, and statistical process control (SPC) are invaluable tools for analyzing this data and identifying bottlenecks, inefficiencies, and areas where value can be added or enhanced.
2.2 Identifying Bottlenecks and Waste
Through data analysis, organizations can identify bottlenecks that hinder the smooth flow of processes. Bottlenecks represent points of congestion or delay in the process, significantly impacting efficiency and throughput. Understanding the root causes of bottlenecks is critical for implementing effective solutions. Similarly, identifying and eliminating waste (activities that don't add value to the customer) is crucial for process optimization. Lean methodologies, such as Kaizen and Six Sigma, provide structured approaches for identifying and eliminating waste.
2.3 Implementing Improvements and Measuring Results
Once bottlenecks and waste are identified, implementing improvements requires careful planning and execution. The chosen improvement strategies should be data-driven and aligned with the organization's overall goals. Following implementation, measuring the impact of improvements is vital to assessing their effectiveness and making further adjustments. Key Performance Indicators (KPIs) play a critical role in tracking and measuring progress.
3. Technology's Role in Process and Value Chain Management
Technology plays an increasingly crucial role in managing processes and value chains. From Enterprise Resource Planning (ERP) systems to workflow automation tools, technological advancements offer significant opportunities to improve efficiency, reduce costs, and enhance customer satisfaction.
3.1 ERP Systems: Integrating Processes Across the Organization
ERP systems provide a centralized platform for managing various aspects of a business, including finance, human resources, and supply chain management. This integration allows for better visibility across different processes, enabling efficient resource allocation and collaboration.
3.2 Workflow Automation Tools: Streamlining Processes
Workflow automation tools help automate repetitive and time-consuming tasks, freeing up employees to focus on higher-value activities. This automation can significantly reduce processing time, improve accuracy, and minimize errors.
3.3 Data Analytics and Business Intelligence: Driving Informed Decisions
Data analytics and business intelligence tools provide valuable insights into process performance and customer behavior. These insights can be used to make data-driven decisions, optimize processes, and improve overall business performance.
4. People and Culture: The Human Element
While technology plays a critical role, the human element is equally important in successfully managing processes and value chains. Engaging employees, fostering a culture of continuous improvement, and providing appropriate training are essential for long-term success.
4.1 Employee Engagement and Empowerment
Employees at all levels should be actively involved in process improvement initiatives. Empowering them to identify problems, suggest solutions, and implement changes fosters a sense of ownership and increases the likelihood of successful implementation.
4.2 Training and Development: Building Capabilities
Providing employees with the necessary training and development opportunities is critical for ensuring they have the skills and knowledge to effectively manage and improve processes. This training should cover process improvement methodologies, relevant technologies, and best practices.
4.3 Culture of Continuous Improvement: Embracing Change
A culture of continuous improvement should be fostered throughout the organization. This culture encourages employees to continuously seek ways to improve processes, optimize performance, and adapt to change.
5. Alignment with Business Strategy: A Holistic Approach
Process and value chain management should not be viewed as isolated activities but rather as integral components of the overall business strategy. Processes and value chains must be aligned with the organization's strategic goals and objectives to ensure they contribute to the achievement of its long-term vision.
5.1 Linking Processes to Strategic Goals
Each process and value chain activity should be evaluated against the organization's strategic goals. Those that do not contribute to the achievement of these goals should be either improved or eliminated.
5.2 Adaptability and Flexibility: Responding to Change
The business environment is constantly changing. Processes and value chains must be designed to be adaptable and flexible enough to respond effectively to these changes. This adaptability ensures the organization can maintain its competitive advantage in the face of evolving market conditions.
6. Measuring and Monitoring Performance: Continuous Improvement
Regularly measuring and monitoring the performance of processes and value chains is crucial for identifying areas needing improvement and assessing the effectiveness of implemented changes. This monitoring process should be continuous and data-driven, providing ongoing insights into the health and efficiency of the organization's operations.
6.1 Key Performance Indicators (KPIs): Tracking Progress
KPIs are critical for tracking the performance of processes and value chains. They provide quantifiable measures of progress and help identify areas where improvements are needed. KPIs should be aligned with the organization's strategic goals and should be regularly monitored and reviewed.
6.2 Regular Reviews and Adjustments: Adapting to Change
Regular reviews of process and value chain performance should be conducted to identify areas for improvement. These reviews should involve stakeholders from across the organization and should lead to actionable plans for improvement.
In conclusion, the foundation for managing processes and value chains rests on a comprehensive understanding of processes, value chains, data-driven analysis, technology integration, human capital, strategic alignment, and continuous monitoring. By focusing on these key elements, organizations can build robust and efficient operations, deliver superior customer value, and achieve sustainable competitive advantage in today's dynamic business environment. It’s a continuous journey, requiring commitment, adaptation, and a consistent focus on improvement.
Latest Posts
Latest Posts
-
How Many Pounds Is 56 Kilos
May 19, 2025
-
How Many Kg In 170 Lbs
May 19, 2025
-
130 Square Meters To Square Feet
May 19, 2025
-
How Many Kg Is 170 Pounds
May 19, 2025
-
How Many Litres Is 6 Gallons
May 19, 2025
Related Post
Thank you for visiting our website which covers about The Foundation For Managing Processes And Value Chains Is . We hope the information provided has been useful to you. Feel free to contact us if you have any questions or need further assistance. See you next time and don't miss to bookmark.