The Following Is A True Statement About Safety Stock
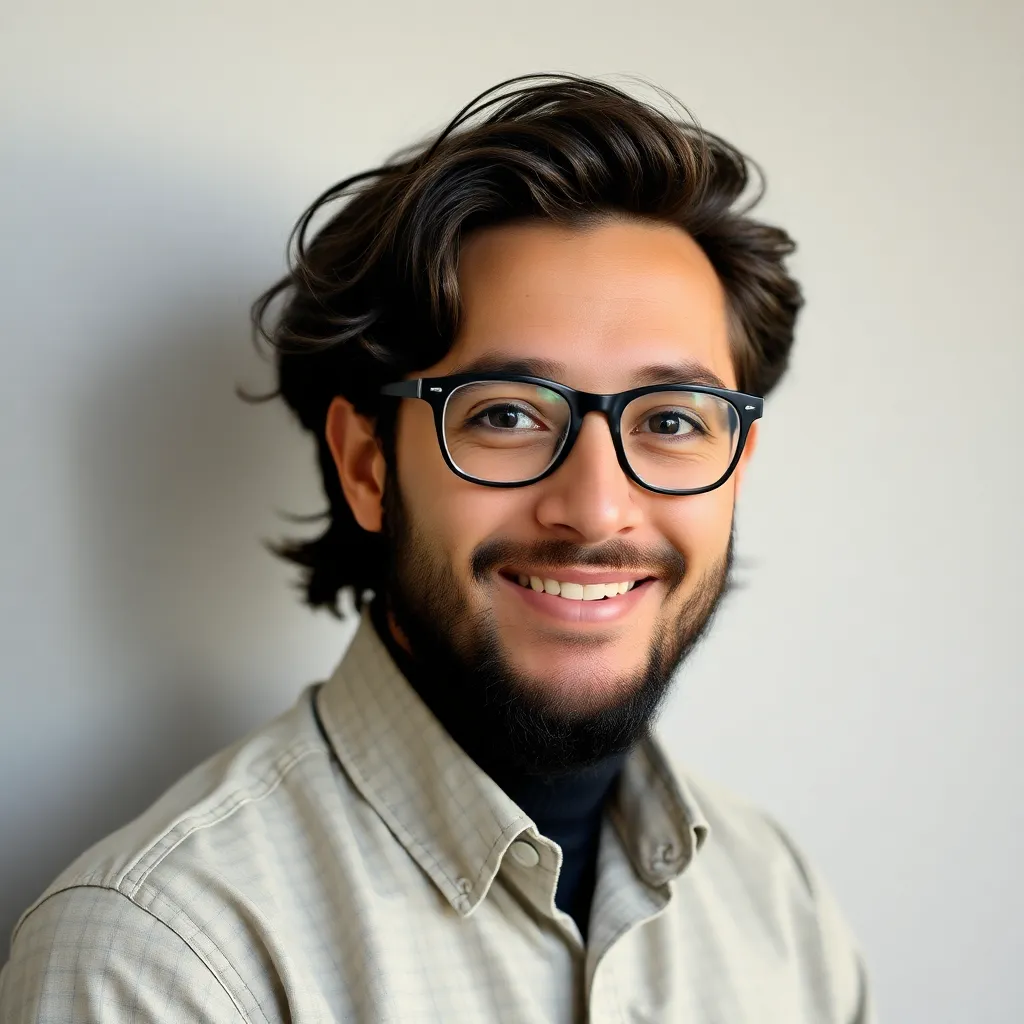
Holbox
Apr 03, 2025 · 6 min read

Table of Contents
- The Following Is A True Statement About Safety Stock
- Table of Contents
- The Truth About Safety Stock: A Comprehensive Guide for Inventory Management
- What is Safety Stock, Really?
- Why is Safety Stock Important?
- Calculating Safety Stock: Beyond the Basics
- Optimizing Safety Stock: Practical Strategies
- The Costs of Incorrect Safety Stock Levels
- Debunking Myths About Safety Stock
- Conclusion: A Balanced Approach to Safety Stock
- Latest Posts
- Latest Posts
- Related Post
The Truth About Safety Stock: A Comprehensive Guide for Inventory Management
Safety stock. The phrase itself conjures images of overflowing warehouses and tied-up capital. But understanding and effectively managing safety stock is crucial for any business that wants to avoid stockouts, maintain customer satisfaction, and optimize its supply chain. This isn't just about having enough; it's about having the right amount. This article delves deep into the complexities of safety stock, debunking myths and offering practical strategies to optimize its use.
What is Safety Stock, Really?
Safety stock isn't simply extra inventory; it's a buffer against the inevitable uncertainties in supply and demand. It protects against disruptions like:
- Supplier delays: Unexpected production issues, transportation problems, or simply late shipments can leave you short on inventory.
- Demand variability: Forecasting is an inexact science. Sudden spikes in demand, seasonal fluctuations, or unexpected marketing successes can quickly deplete your stock.
- Lead time variability: The time it takes to replenish your inventory can fluctuate. Longer lead times increase the risk of running out of stock.
- Forecasting errors: Even the most sophisticated forecasting models are prone to inaccuracies. These errors can lead to both overstocking and understocking.
Think of safety stock as your insurance policy against these unforeseen events. It ensures that you can continue to meet customer demand, even when things don't go exactly as planned.
Why is Safety Stock Important?
The importance of safety stock can't be overstated. A well-managed safety stock strategy contributes to:
- Improved customer service: By preventing stockouts, you maintain a high level of customer satisfaction, leading to increased loyalty and repeat business. Lost sales due to stockouts can be significantly more costly than carrying some safety stock.
- Reduced production downtime: If you rely on certain components or materials, a stockout can bring your entire production line to a grinding halt. Safety stock minimizes this risk.
- Increased efficiency: While carrying excess inventory ties up capital, a strategically calculated safety stock avoids the significant disruptions and costs associated with stockouts.
- Better risk management: Safety stock acts as a buffer against unforeseen events, providing stability during periods of uncertainty. This proactive approach reduces vulnerability to supply chain disruptions.
- Enhanced supply chain resilience: A robust safety stock strategy strengthens your supply chain's ability to withstand shocks and maintain its functionality even during crises.
Calculating Safety Stock: Beyond the Basics
Many businesses simply add a percentage to their forecasted demand to determine safety stock. This approach is simplistic and often inaccurate. A more robust approach considers factors like:
- Lead time: The longer the lead time to replenish your inventory, the more safety stock you'll need.
- Demand variability: The greater the fluctuation in demand, the larger your safety stock requirement.
- Service level: The desired probability of not experiencing a stockout. A higher service level (e.g., 99%) requires more safety stock than a lower service level (e.g., 95%).
- Standard deviation of demand: This statistical measure quantifies the variability in demand. A higher standard deviation indicates greater uncertainty and necessitates more safety stock.
Several methods exist for calculating safety stock, including:
-
The Simple Method: This method multiplies the average daily demand during lead time by the number of days of lead time and adds a safety factor (a percentage). It's easy to understand but doesn't account for demand variability adequately.
-
The Standard Deviation Method: This statistically sound method uses the standard deviation of demand during the lead time to calculate safety stock. It provides a more accurate estimate than the simple method, considering demand variability. The formula often involves a Z-score, representing the desired service level. The higher the desired service level, the higher the Z-score and consequently, the higher the safety stock.
-
Simulation Methods: For complex scenarios with multiple variables, simulation methods, such as Monte Carlo simulations, offer the most accurate safety stock calculations. These methods consider numerous factors and their interactions to generate a range of possible outcomes, providing a more nuanced understanding of the risks and rewards.
Optimizing Safety Stock: Practical Strategies
Simply calculating safety stock isn't enough; optimizing it is key to maximizing efficiency and minimizing costs. Strategies for optimization include:
-
Accurate Demand Forecasting: Invest in robust forecasting techniques and utilize historical data, seasonal patterns, and market trends to predict demand more accurately. Regularly review and refine your forecasting models.
-
Supplier Relationship Management: Develop strong relationships with your suppliers to ensure timely deliveries and transparent communication regarding potential disruptions. Consider diversifying your supplier base to reduce reliance on a single source.
-
Efficient Inventory Management Systems: Implement a robust inventory management system (IMS) that provides real-time visibility into inventory levels, demand patterns, and lead times. An IMS can automate reordering processes and alert you to potential stockouts.
-
Regular Inventory Reviews: Conduct regular inventory reviews to identify slow-moving items and obsolete stock. Analyze your inventory turnover rate to identify areas for improvement.
-
Lean Inventory Principles: Incorporate lean inventory principles to minimize waste and reduce excess inventory. Focus on just-in-time (JIT) inventory management where possible, reducing the need for large safety stock levels.
-
Collaboration Across the Supply Chain: Engage in collaborative planning, forecasting, and replenishment (CPFR) with your suppliers and customers to improve demand forecasting and optimize inventory levels across the entire supply chain.
-
Technology Adoption: Leverage advanced technologies like AI-powered forecasting tools, predictive analytics, and blockchain solutions to enhance inventory management, improve forecast accuracy and streamline supply chain operations.
The Costs of Incorrect Safety Stock Levels
Getting safety stock wrong has significant consequences:
-
Excess Safety Stock: This ties up capital that could be invested elsewhere in the business. It also increases storage costs, insurance costs, and the risk of obsolescence. This is a significant hidden cost, often overlooked in basic calculations.
-
Insufficient Safety Stock: This leads to stockouts, lost sales, dissatisfied customers, and potential damage to your brand reputation. The cost of lost sales can far outweigh the cost of carrying extra inventory. Furthermore, production delays and disruptions add to these expenses.
Debunking Myths About Safety Stock
Several misconceptions surround safety stock:
-
Myth 1: More is always better: This is false. Excessive safety stock is costly and inefficient. The goal is to find the optimal balance between protection against stockouts and minimizing inventory holding costs.
-
Myth 2: Safety stock eliminates risk: Safety stock reduces risk, but it doesn't eliminate it entirely. Unexpected events can still occur, even with substantial safety stock.
-
Myth 3: It's a one-time calculation: Safety stock needs to be reviewed and adjusted regularly based on changing market conditions, demand patterns, and supplier performance.
Conclusion: A Balanced Approach to Safety Stock
Safety stock is a critical component of a well-functioning inventory management system. It's not about eliminating risk; it's about mitigating it effectively. By understanding the factors that influence safety stock requirements, employing accurate calculation methods, and implementing optimization strategies, businesses can ensure they have the right amount of inventory to meet customer demand while minimizing costs and maximizing efficiency. The key is finding the delicate balance between protecting against stockouts and avoiding the pitfalls of excessive inventory. A well-managed safety stock strategy contributes significantly to a resilient and profitable business. Regular review and adaptation to changing circumstances are paramount to maintain this balance and ensure continued success.
Latest Posts
Latest Posts
-
The Ankle Is To The Knee
Apr 08, 2025
-
Economics Is The Study Of How Society Manages Its
Apr 08, 2025
-
Inductors In Parallel Add Like Resistors In
Apr 08, 2025
-
Classify The Characteristics Of Triacylglycerols And Phosphoglycerides
Apr 08, 2025
-
A Caseworkers Client Who Struggles With Depression And Anxiety
Apr 08, 2025
Related Post
Thank you for visiting our website which covers about The Following Is A True Statement About Safety Stock . We hope the information provided has been useful to you. Feel free to contact us if you have any questions or need further assistance. See you next time and don't miss to bookmark.