The Drawing Shows A Hydraulic Chamber With A Spring
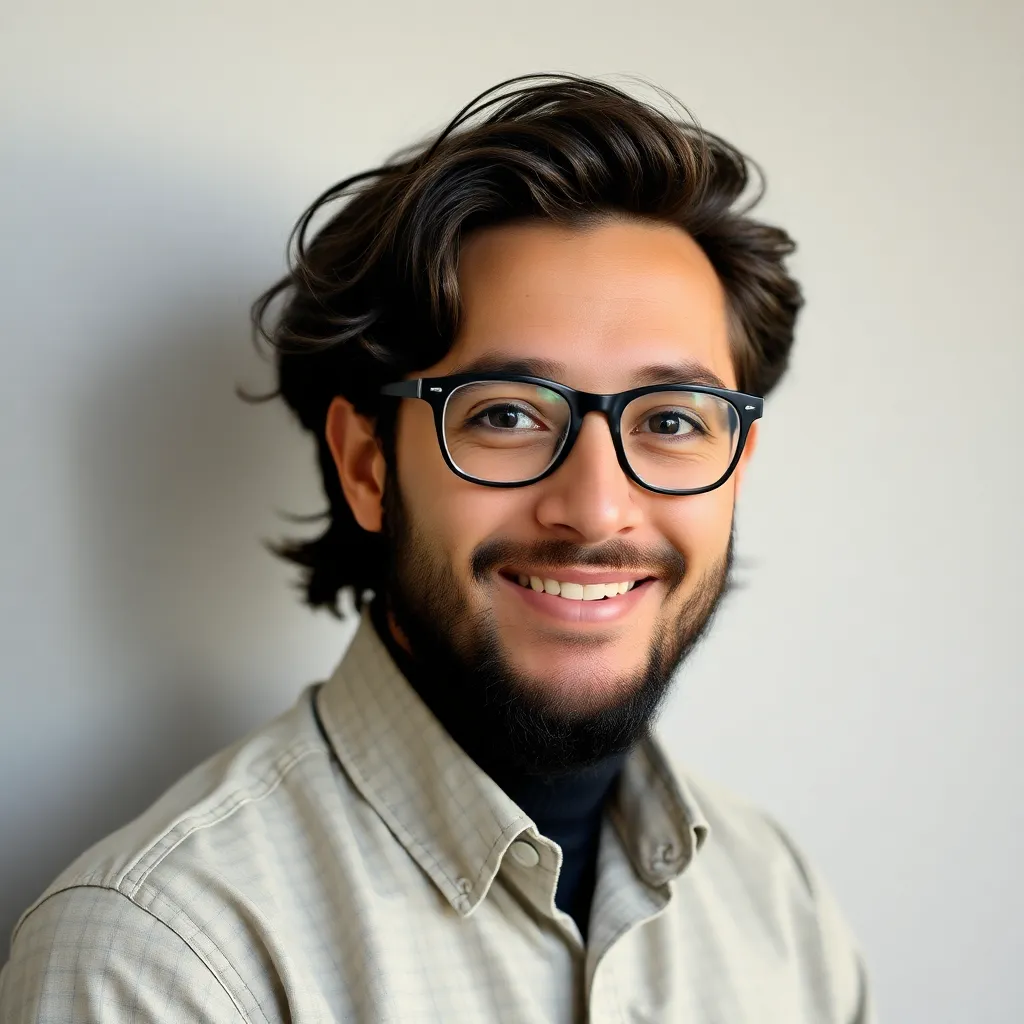
Holbox
Apr 05, 2025 · 6 min read

Table of Contents
- The Drawing Shows A Hydraulic Chamber With A Spring
- Table of Contents
- The Drawing Shows a Hydraulic Chamber with a Spring: A Deep Dive into Principles and Applications
- Understanding the Fundamentals: Hydraulics and Springs
- Hydraulic Systems: The Power of Fluids
- Springs: Energy Storage and Force Generation
- The Hydraulic Chamber with a Spring: A Synergistic Combination
- Diverse Applications: Where You’ll Find This Design
- 1. Automotive Industry:
- 2. Industrial Machinery:
- 3. Aerospace Engineering:
- 4. Medical Devices:
- 5. Consumer Products:
- Design Considerations: Optimizing Performance
- Advanced Concepts and Future Trends
- Conclusion: A Powerful Combination with Broad Applications
- Latest Posts
- Latest Posts
- Related Post
The Drawing Shows a Hydraulic Chamber with a Spring: A Deep Dive into Principles and Applications
This article delves into the fascinating world of hydraulic systems, specifically focusing on the common design element: a hydraulic chamber with a spring. We'll explore the underlying principles, diverse applications, and the crucial role springs play in optimizing system performance. This detailed analysis will cover various aspects, from basic mechanics to advanced engineering considerations. Understanding this seemingly simple combination unlocks a wealth of knowledge about complex engineering feats.
Understanding the Fundamentals: Hydraulics and Springs
Before diving into the specifics of a hydraulic chamber with a spring, let's establish a foundational understanding of each component individually.
Hydraulic Systems: The Power of Fluids
Hydraulic systems leverage the power of pressurized fluids, typically oils, to transmit force and perform mechanical work. Pascal's principle is the cornerstone of hydraulics: pressure applied to a confined fluid is transmitted equally and undiminished throughout the fluid. This principle enables the amplification of force, allowing small inputs to generate substantial outputs.
Key Components of a Hydraulic System:
- Reservoir: Stores the hydraulic fluid.
- Pump: Provides the necessary pressure.
- Control Valves: Regulate fluid flow and pressure.
- Actuator (Cylinder): Converts hydraulic pressure into mechanical movement.
- Piping and Fittings: Connect the components and ensure fluid transfer.
Springs: Energy Storage and Force Generation
Springs are mechanical components that store and release elastic potential energy. Their ability to exert a force proportional to their deformation makes them invaluable in diverse applications. Different types of springs exist, each with unique characteristics:
- Coil Springs: Helical springs offering high flexibility and energy storage.
- Leaf Springs: Flat springs used for load support and shock absorption.
- Torsion Springs: Designed to store energy in torsion (twisting).
- Compression Springs: Resist compressive forces.
- Extension Springs: Resist tensile forces.
The Hydraulic Chamber with a Spring: A Synergistic Combination
The integration of a spring within a hydraulic chamber creates a dynamic system with enhanced functionality. The spring’s role is often to:
- Pre-load the System: Applying an initial force to the hydraulic system, ensuring immediate responsiveness and preventing slack. This is crucial in applications requiring precise control and immediate action.
- Dampen Shock and Vibration: Absorbing sudden impacts and oscillations, enhancing system stability and longevity. The spring helps mitigate harsh shocks that could damage other components.
- Provide a Return Mechanism: Enabling the hydraulic actuator to retract or return to its original position after the pressure is relieved. This eliminates the need for separate return mechanisms in some applications.
- Adjust System Sensitivity: Altering the spring’s stiffness can fine-tune the responsiveness of the hydraulic system, optimizing its performance for a specific task. A stiffer spring results in a less sensitive system.
- Store Energy for Subsequent Use: The spring can store energy during one phase of the system's operation and release it later, improving efficiency and reducing energy consumption.
Diverse Applications: Where You’ll Find This Design
The versatile nature of a hydraulic chamber with a spring makes it applicable in a wide range of industries and applications:
1. Automotive Industry:
- Brake Systems: Springs assist in returning brake pedals and components to their original positions after braking.
- Suspension Systems: Springs work in conjunction with hydraulic shock absorbers to provide a comfortable and controlled ride. They absorb bumps and vibrations, contributing to driving safety.
- Power Steering Systems: Springs help center the steering wheel, providing a more natural feel and improving driver control.
2. Industrial Machinery:
- Presses and Forming Machines: Springs provide a return force to the actuator, ensuring efficient operation and precise control.
- Material Handling Equipment: Springs assist in maintaining tension and smooth movement in conveyors and other material handling systems.
- Robotics: Springs are used to provide compliance and damping in robotic arms, improving precision and safety.
3. Aerospace Engineering:
- Landing Gear Systems: Springs help absorb the impact during landing, protecting the aircraft's structure. Hydraulic systems control the extension and retraction of the landing gear. The combined system ensures a smooth landing.
- Flight Control Systems: Springs provide a return mechanism for flight control surfaces, ensuring that they return to a neutral position when the hydraulic system is deactivated.
4. Medical Devices:
- Surgical Instruments: Precise and controlled movements are crucial, and springs often play a role in delivering that precision.
- Prosthetics: Springs aid in mimicking natural movement and providing compliance.
5. Consumer Products:
- Hydraulic Jacks: A spring may be incorporated to ensure a controlled lowering of the jack.
- Shock Absorbers in Bicycles: These are a classic example of a spring and hydraulic damper working together to provide a smooth and controlled ride.
Design Considerations: Optimizing Performance
The design of a hydraulic chamber with a spring requires careful consideration of several factors:
- Spring Stiffness: Selecting the appropriate spring stiffness is crucial to achieving the desired system response. Too stiff a spring can lead to harshness, while too soft a spring may not provide sufficient support.
- Spring Material: Material selection impacts durability, fatigue resistance, and overall lifespan. Common materials include steel, stainless steel, and various alloys.
- Chamber Design: The chamber must be designed to accommodate the spring and hydraulic fluid, ensuring proper sealing and preventing leakage.
- Seal Selection: Reliable seals are essential to prevent fluid leakage and maintain system pressure. Seal material compatibility with the hydraulic fluid must be considered.
- Fluid Selection: The choice of hydraulic fluid depends on factors such as operating temperature, viscosity, and compatibility with system components.
Advanced Concepts and Future Trends
The field of hydraulics is constantly evolving, with ongoing research and development pushing the boundaries of what's possible. Some advanced concepts and future trends include:
- Electro-hydraulic Systems: Integrating electronic controls to provide precise and programmable control over hydraulic systems. This allows for more complex and sophisticated movements.
- Smart Hydraulic Systems: Utilizing sensors and data analysis to optimize system performance, predict maintenance needs, and enhance efficiency. This approach focuses on preventative maintenance and maximizing uptime.
- Bio-inspired Hydraulic Systems: Mimicking the natural hydraulic systems found in living organisms to develop more efficient and sustainable designs. This area explores new ways to replicate natural mechanisms, using biomimicry as a source of inspiration.
- Nanofluidics: Employing nanotechnology to create extremely small and precise hydraulic systems for applications in microelectronics and other advanced fields. This is a rapidly developing area with potential for revolutionary advancements.
Conclusion: A Powerful Combination with Broad Applications
The seemingly simple combination of a hydraulic chamber and a spring unlocks a world of sophisticated engineering solutions. Understanding the fundamental principles, design considerations, and diverse applications of this design is key to appreciating its versatility and impact across numerous industries. From automotive braking systems to advanced robotics, this design showcases the power of simple yet effective mechanical systems. As technology continues to advance, the integration of springs and hydraulics promises to deliver further breakthroughs, shaping the future of engineering and design.
Latest Posts
Latest Posts
-
Glucagon Secretion Is Stimulated When Blood Glucose Concentration Decreases
Apr 11, 2025
-
To Safeguard Against Hacking Practicing Situational Awareness Means
Apr 11, 2025
-
Identify The Precautions To Take With Exits In The Lab
Apr 11, 2025
-
Draw The Neutral Product Of Oxymercuration
Apr 11, 2025
-
The Smallest And Most Significant Taxon Is
Apr 11, 2025
Related Post
Thank you for visiting our website which covers about The Drawing Shows A Hydraulic Chamber With A Spring . We hope the information provided has been useful to you. Feel free to contact us if you have any questions or need further assistance. See you next time and don't miss to bookmark.