The Controllable Variance Is So Called Because It
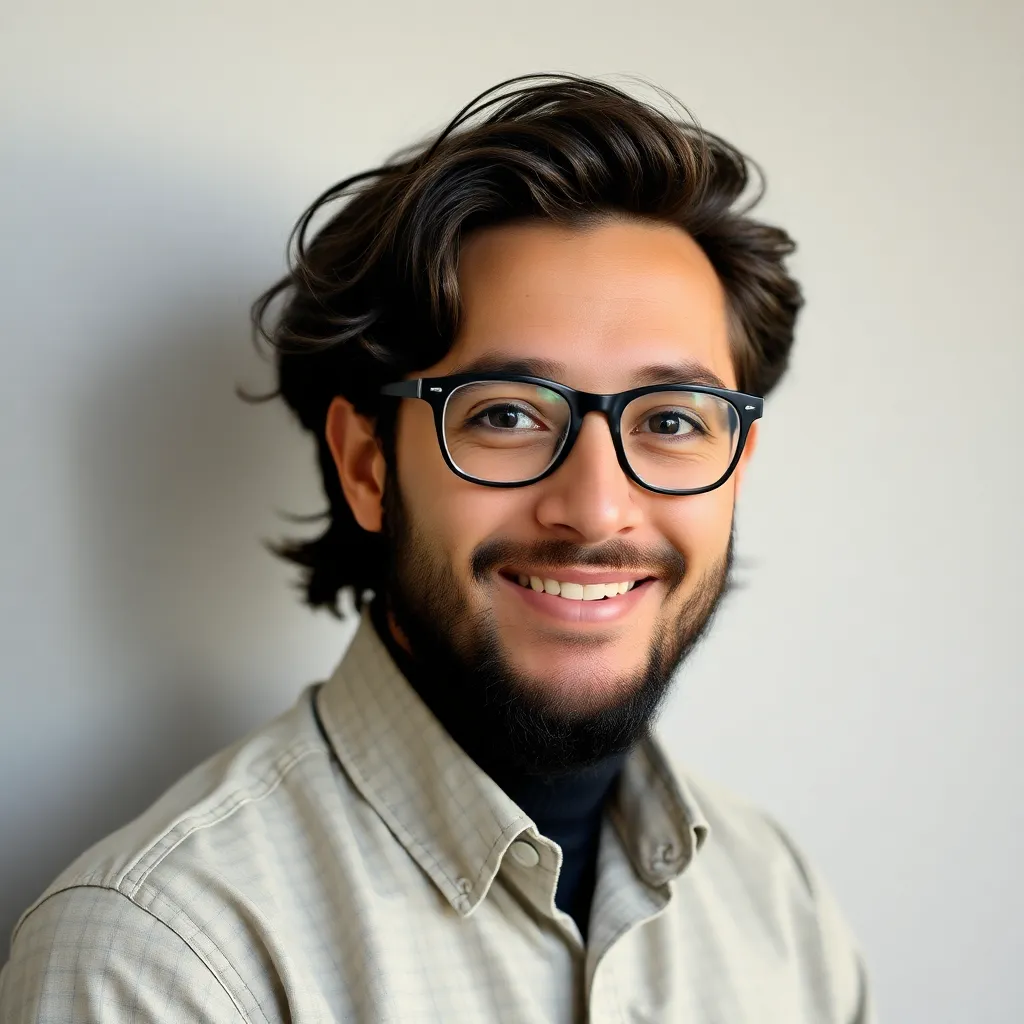
Holbox
Apr 02, 2025 · 6 min read

Table of Contents
- The Controllable Variance Is So Called Because It
- Table of Contents
- The Controllable Variance: Why It's Called "Controllable" and How to Master It
- What is Variance?
- Unpacking Controllable Variance
- Why is Identifying Controllable Variance Crucial?
- Examples of Controllable Variance
- Manufacturing
- Healthcare
- Customer Service
- Identifying and Controlling Controllable Variance: A Practical Guide
- Tools and Techniques for Managing Controllable Variance
- Conclusion: Mastering Controllable Variance for Success
- Latest Posts
- Latest Posts
- Related Post
The Controllable Variance: Why It's Called "Controllable" and How to Master It
Understanding variance is crucial for anyone involved in data analysis, process improvement, or business decision-making. But within the realm of variance lies a powerful subset: controllable variance. This article delves deep into the meaning, significance, and practical application of controllable variance, explaining why it's called "controllable" and offering strategies to effectively manage and leverage it.
What is Variance?
Before understanding controllable variance, let's establish a firm grasp on the concept of variance itself. In simple terms, variance measures the spread or dispersion of a dataset around its mean (average). A high variance indicates data points are widely scattered, while low variance signifies data points clustered closely around the mean.
Mathematically, variance is calculated by finding the average of the squared differences between each data point and the mean. This squaring ensures that both positive and negative deviations contribute positively to the overall variance, preventing cancellation.
Variance is a key component in statistical analysis, used to understand data variability, assess risk, and make informed predictions. However, not all variance is created equal.
Unpacking Controllable Variance
Controllable variance refers to the portion of total variance that can be influenced or modified through actions taken within a specific system or process. It's directly tied to factors that are within an organization's or individual's control. This is why it's called "controllable"—because you can control it.
This contrasts sharply with uncontrollable variance, which stems from external factors beyond the immediate reach of those involved. Uncontrollable variance might include unpredictable events like natural disasters, economic downturns, or shifts in consumer preferences. While you can’t directly control these factors, you can often mitigate their impact through careful planning and risk management.
Why is Identifying Controllable Variance Crucial?
Understanding and focusing on controllable variance offers significant advantages:
-
Improved Efficiency: By pinpointing and reducing controllable sources of variation, you streamline processes, reduce waste, and improve overall efficiency.
-
Enhanced Quality: Lowering controllable variance leads to more consistent and predictable outcomes, resulting in improved product or service quality.
-
Cost Reduction: Minimizing variations often translates to lower costs associated with rework, scrap, and customer dissatisfaction.
-
Increased Profitability: Efficiency gains, higher quality, and reduced costs collectively contribute to improved profitability.
-
Better Decision-Making: A clear understanding of controllable variance allows for data-driven decision-making, leading to more effective strategies and resource allocation.
-
Competitive Advantage: Organizations adept at controlling variance gain a competitive edge through superior processes, consistently high-quality outputs, and cost-effectiveness.
Examples of Controllable Variance
Let’s illustrate with practical examples across different fields:
Manufacturing
-
Machine Variability: Inconsistent performance of manufacturing equipment can lead to variations in product dimensions or quality. Regular maintenance, calibration, and operator training can significantly reduce this controllable variance.
-
Raw Material Differences: Variations in the quality or composition of raw materials can impact the final product. Stricter quality control measures in sourcing and consistent supplier selection can minimize this controllable variance.
-
Process Parameters: Variations in temperature, pressure, or speed during manufacturing can affect product consistency. Precise control and monitoring of these process parameters are vital in reducing controllable variance.
Healthcare
-
Medication Dosage Errors: Variations in medication dosage due to human error contribute to patient safety risks. Improved training protocols, automated dispensing systems, and double-checking procedures can reduce this controllable variance.
-
Treatment Protocol Adherence: Inconsistent application of established treatment protocols by healthcare providers can impact patient outcomes. Standardized guidelines, training, and regular audits can help reduce this controllable variance.
-
Waiting Times: Variations in patient waiting times are often linked to scheduling inefficiencies or staffing issues. Optimized scheduling systems and adequate staffing levels can help minimize controllable variance.
Customer Service
-
Response Time Variability: Inconsistencies in response times to customer inquiries can affect customer satisfaction. Implementing efficient case management systems and providing adequate training to customer service representatives can reduce this controllable variance.
-
Resolution Time Variability: Variations in the time it takes to resolve customer issues can damage customer relationships. Streamlining processes, providing better training, and improving access to information can all help reduce controllable variance.
-
Customer Satisfaction Scores: Variations in customer satisfaction ratings highlight areas where processes need improvement. Targeted surveys and feedback mechanisms, coupled with analysis of controllable variance, can identify areas for process improvement and optimization.
Identifying and Controlling Controllable Variance: A Practical Guide
The process of identifying and controlling controllable variance often involves these key steps:
-
Data Collection: Gather comprehensive data related to the process or system being analyzed. This might involve collecting measurements, observations, or feedback from various sources.
-
Data Analysis: Use statistical methods to analyze the data and identify sources of variation. Tools such as control charts, histograms, and scatter plots can help visualize and quantify variance.
-
Variance Identification: Distinguish between controllable and uncontrollable sources of variance. This requires careful consideration of the factors influencing the process.
-
Root Cause Analysis: For each identified source of controllable variance, conduct a thorough root cause analysis to understand the underlying reasons behind the variation. Techniques like the "5 Whys" method can be helpful here.
-
Control Implementation: Develop and implement control measures to reduce or eliminate the identified sources of controllable variance. These controls might involve process improvements, training programs, or new technologies.
-
Monitoring and Evaluation: Continuously monitor the process and evaluate the effectiveness of the implemented controls. Make adjustments as needed to maintain control over variance.
-
Continuous Improvement: Embrace a culture of continuous improvement, constantly seeking ways to refine processes and further reduce controllable variance.
Tools and Techniques for Managing Controllable Variance
Several tools and techniques can significantly aid in managing controllable variance:
-
Control Charts: Visual tools for monitoring process variation over time. They help detect shifts in the mean or increases in variability.
-
Statistical Process Control (SPC): A collection of statistical methods used to monitor and control processes. It aims to reduce variability and improve process capability.
-
Six Sigma: A data-driven methodology focused on minimizing defects and variability in processes. It utilizes statistical tools and methodologies to achieve near-perfect quality.
-
Lean Manufacturing: A philosophy focused on eliminating waste and improving efficiency. It emphasizes continuous improvement and reducing variability in processes.
-
Design of Experiments (DOE): A systematic approach to designing experiments that allows for the efficient identification of factors contributing to variability.
-
Root Cause Analysis (RCA): A problem-solving technique aimed at identifying the underlying causes of problems, particularly those contributing to process variation. Methods include the 5 Whys, Fishbone diagrams (Ishikawa diagrams), and Fault Tree Analysis.
Conclusion: Mastering Controllable Variance for Success
Controllable variance, by its very name, signifies opportunity. It's the portion of variation within your grasp, the area where focused effort yields significant returns. By diligently following the strategies outlined above, you can harness the power of controllable variance, improving efficiency, quality, and profitability within your organization. Remember, the journey to mastering controllable variance is one of continuous improvement – a commitment to ongoing analysis, adaptation, and refinement. The rewards, however, are well worth the effort.
Latest Posts
Latest Posts
-
A Companys Strategy Stands A Better Chance Of Succeeding When
Apr 05, 2025
-
Order The Events In Which Telomerase Maintains
Apr 05, 2025
-
Jia Is Considering Whether To Go Out To Dinner
Apr 05, 2025
-
The Image Shows An Expanded Circular Flow Diagram
Apr 05, 2025
-
Identify An Advantage Of Centralized Processing
Apr 05, 2025
Related Post
Thank you for visiting our website which covers about The Controllable Variance Is So Called Because It . We hope the information provided has been useful to you. Feel free to contact us if you have any questions or need further assistance. See you next time and don't miss to bookmark.