The Control Devices Used In Pneumatics Are Called
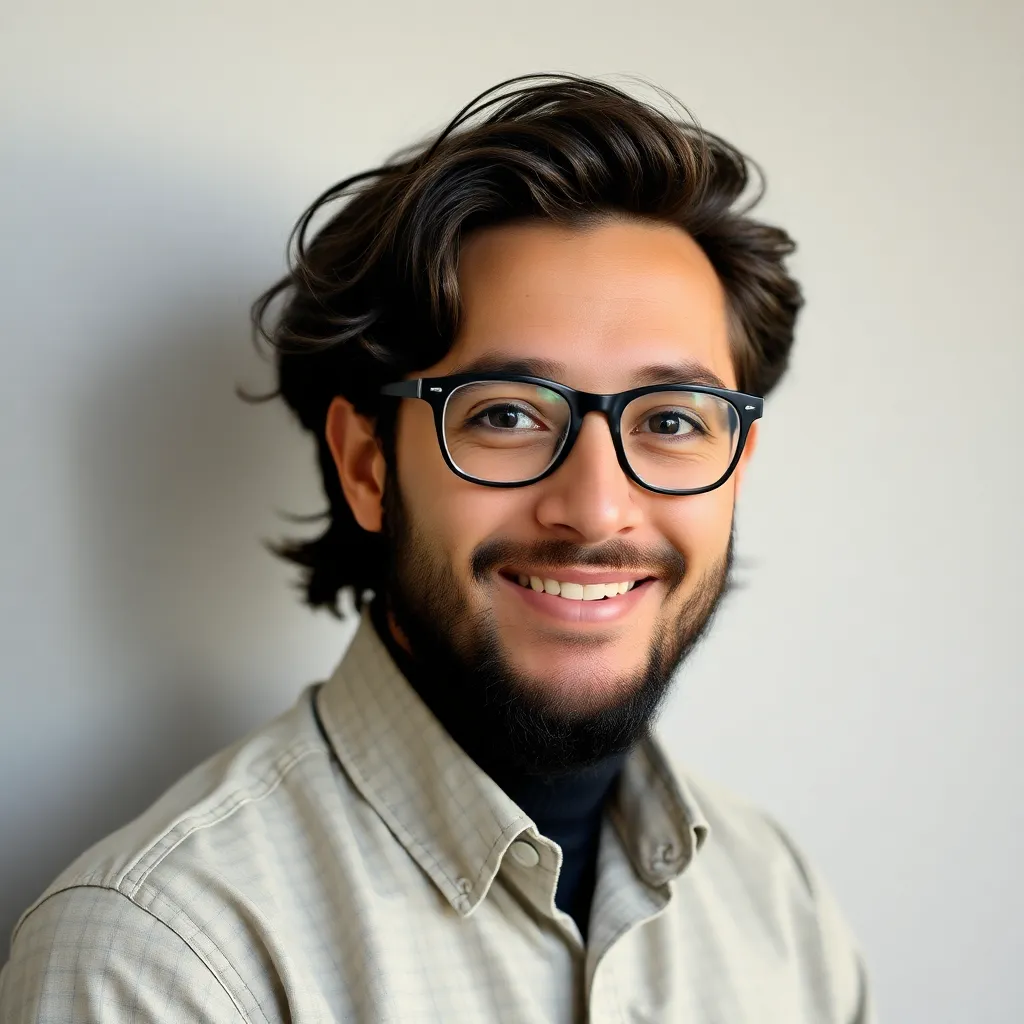
Holbox
Mar 19, 2025 · 7 min read
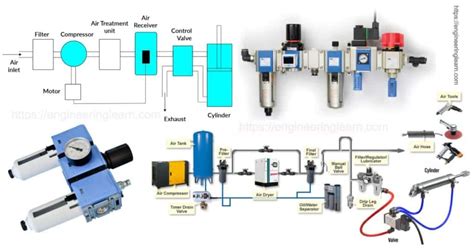
Table of Contents
The Control Devices Used in Pneumatics are Called… Pneumatic Control Valves!
Pneumatics, the technology harnessing compressed air for power and motion, relies heavily on a sophisticated array of control devices to manage the flow, pressure, and direction of this pressurized air. These devices, collectively known as pneumatic control valves, are the brains of any pneumatic system, dictating how and when compressed air is utilized to perform specific tasks. Understanding these valves is crucial for anyone working with pneumatic systems, whether for maintenance, design, or troubleshooting. This comprehensive guide dives deep into the world of pneumatic control valves, exploring their various types, functionalities, and applications.
Understanding the Core Functionality of Pneumatic Control Valves
Before delving into the specific types, let's establish the fundamental role of pneumatic control valves. They are essentially flow control devices that regulate the movement of compressed air within a pneumatic circuit. This regulation can manifest in several ways:
-
Starting and Stopping Airflow: The most basic function is controlling whether air flows or not. Think of a simple on/off valve.
-
Directing Airflow: Many valves direct the flow of compressed air to different parts of the system, enabling the actuation of multiple pneumatic components sequentially or simultaneously.
-
Regulating Air Pressure: Some pneumatic control valves precisely adjust the air pressure, allowing for fine control over the speed or force of a pneumatic actuator.
-
Maintaining Air Pressure: Pressure regulating valves maintain a consistent air pressure despite fluctuations in the supply pressure.
The core principle behind most pneumatic control valves is the use of a control signal to actuate the valve. This signal can take several forms:
-
Manual Control: The simplest form, where the operator directly controls the valve's position.
-
Electrical Control: Solenoids, commonly used in automated systems, use an electrical current to shift the valve's internal components.
-
Pneumatic Control: One pneumatic signal controls the position of another valve, enabling complex sequencing and control strategies.
Categorizing Pneumatic Control Valves: A Comprehensive Overview
Pneumatic control valves are categorized in several ways, primarily based on their function and actuation method. Let's explore the most common types:
1. Based on Function:
-
Directional Control Valves (DCVs): These are the workhorses of pneumatic systems. They control the direction of airflow, often switching between multiple ports. They are further categorized based on the number of ports and positions they offer. Common configurations include:
- 2/2-way valves: Two ports, two positions (open or closed). These are simple on/off valves.
- 3/2-way valves: Three ports, two positions. These are commonly used to control the actuation of single-acting cylinders.
- 4/2-way valves: Four ports, two positions. Ideal for controlling double-acting cylinders, allowing for both extension and retraction.
- 5/2-way valves: Five ports, two positions. Offer greater flexibility for complex pneumatic systems.
- 5/3-way valves: Five ports, three positions. Provide additional control options beyond simple on/off functions.
-
Flow Control Valves: These valves regulate the flow rate of compressed air. They are crucial for controlling the speed of pneumatic actuators. Types include:
- Needle Valves: Provide precise flow adjustment through a small needle-like orifice.
- Throttle Valves: Offer a broader range of flow adjustment compared to needle valves.
- Flow Restrictors: Limit the flow rate to a specific value.
-
Pressure Control Valves: These valves maintain or regulate the pressure of compressed air within a pneumatic system. Key types include:
- Pressure Regulators: Reduce and maintain a constant downstream pressure despite fluctuations in the supply pressure.
- Pressure Relief Valves: Protect the system from excessive pressure by releasing excess air.
- Pressure Reducing Valves: Reduce the supply pressure to a predetermined level.
-
Shut-off Valves: These valves simply stop or start the flow of compressed air. They are often manually operated but can also be integrated with other control mechanisms. Examples include ball valves, globe valves, and gate valves.
2. Based on Actuation Method:
-
Manually Operated Valves: These valves are controlled directly by the operator using a lever, knob, or handle. Simple and reliable but unsuitable for automated systems.
-
Solenoid Valves: These are electrically actuated valves that use a solenoid to shift the internal components and control airflow. They are widely used in automated pneumatic systems due to their fast response time and compatibility with PLC controllers.
-
Pneumatically Operated Valves: These valves use compressed air to control their operation. They offer advantages in applications requiring high power or where electrical components are unsuitable.
-
Hydraulically Operated Valves: While less common in pneumatic systems, these valves use hydraulic pressure to actuate the valve mechanism. They are typically used in high-pressure applications.
Choosing the Right Pneumatic Control Valve: Factors to Consider
Selecting the appropriate pneumatic control valve involves considering several crucial factors:
-
System Requirements: The overall design of the pneumatic system dictates the type and number of valves required. Consider the number of actuators, the required flow rates, pressure levels, and sequencing requirements.
-
Actuation Method: The choice between manual, solenoid, pneumatic, or hydraulic actuation depends on the level of automation, environmental conditions, and system complexity.
-
Flow Rate and Pressure: The valve must handle the required flow rate and pressure without causing excessive pressure drop or compromising performance.
-
Materials and Durability: Consider the compatibility of the valve's materials with the compressed air and the surrounding environment. Look for valves constructed from materials that can withstand the operating pressures and temperatures.
-
Maintenance Requirements: Choose valves that are easy to maintain and replace, minimizing downtime. Consider factors like accessibility, ease of disassembly, and the availability of spare parts.
-
Cost: Balance cost with performance and longevity. While cheaper valves might seem attractive, they may lack the durability and reliability of higher-quality options, potentially leading to increased maintenance costs in the long run.
Advanced Pneumatic Control Valve Configurations and Applications
Beyond the basic types discussed, advanced configurations and specialized valves enhance the capabilities of pneumatic systems:
-
Proportional Valves: These valves offer precise control over airflow, allowing for smooth and adjustable movements of pneumatic actuators. They are often used in applications requiring fine control, such as robotics and precision manufacturing.
-
Servo Valves: These are high-performance valves that provide precise and rapid response to control signals. They are crucial for demanding applications requiring high speed and accuracy.
-
Pilot Operated Valves: These valves use a small pilot signal to control the main flow path. They are often used to amplify a small control signal to operate larger valves.
-
Modular Valves: These valves incorporate multiple functions into a single compact unit, simplifying design and reducing installation complexity.
Troubleshooting Common Pneumatic Control Valve Issues
Troubleshooting pneumatic control valves often involves systematically checking several aspects:
-
Power Supply: Ensure the power supply (electrical or pneumatic) is adequate and functioning correctly.
-
Wiring/Tubing: Inspect the wiring or tubing for damage, leaks, or loose connections.
-
Valve Components: Check for internal damage, wear, or debris that could be obstructing airflow.
-
Pilot Signal: For pilot-operated valves, verify the pilot signal is correct and strong enough to actuate the valve.
-
Air Pressure: Ensure the air pressure is within the specified operating range.
The Future of Pneumatic Control Valves
The field of pneumatics is constantly evolving, with ongoing advancements in valve technology driving improvements in efficiency, precision, and control. This includes the increasing integration of smart sensors, data analytics, and digital technologies into pneumatic systems. This trend fosters:
-
Improved System Monitoring: Real-time monitoring of valve performance, pressure, and flow rates enables proactive maintenance and reduces downtime.
-
Enhanced Control Precision: Integration of advanced control algorithms improves the accuracy and responsiveness of pneumatic systems.
-
Greater Automation: Smart valves can seamlessly integrate into automated production lines and industrial processes.
-
Remote Diagnostics: Remote monitoring and diagnostics capabilities simplify maintenance and reduce the need for on-site interventions.
In conclusion, the control devices used in pneumatics are indeed pneumatic control valves, a diverse family of crucial components enabling the precise manipulation of compressed air. By understanding their functionalities, types, and applications, engineers and technicians can design, operate, and maintain efficient and reliable pneumatic systems across numerous industries. The continual advancement of pneumatic control valve technology promises to further enhance the capabilities and versatility of pneumatic systems in the years to come.
Latest Posts
Latest Posts
-
You Are Reviewing Personnel Records Containing Pii
Mar 19, 2025
-
Precalculus With Limits 1st Edition Answers
Mar 19, 2025
-
One Difference Between A Renaissance Mass And A Motet Is
Mar 19, 2025
-
A Uniform Rigid Rod Rests On A Level Frictionless Surface
Mar 19, 2025
-
One Of The Challenges Of Running A Home Based Business Is
Mar 19, 2025
Related Post
Thank you for visiting our website which covers about The Control Devices Used In Pneumatics Are Called . We hope the information provided has been useful to you. Feel free to contact us if you have any questions or need further assistance. See you next time and don't miss to bookmark.