The Brass Bar And The Aluminum Bar In The Drawing
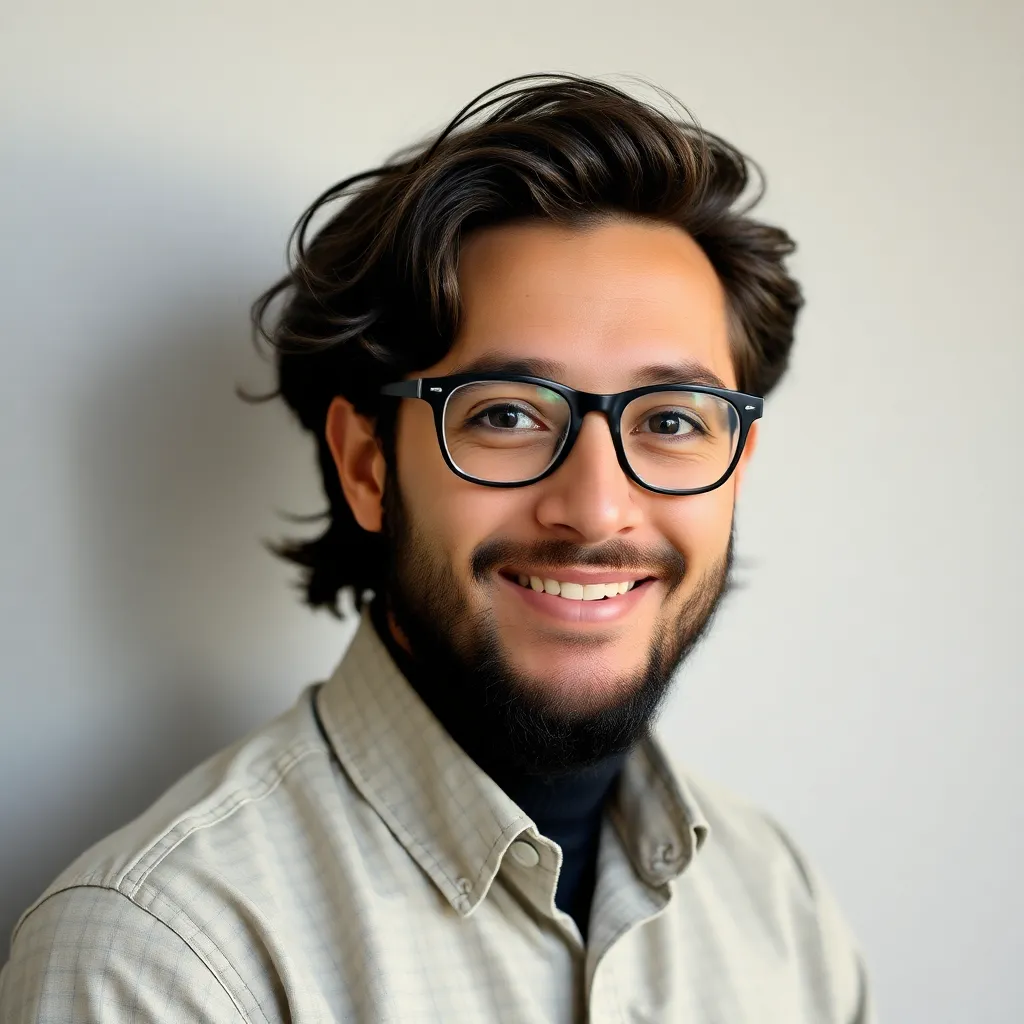
Holbox
Mar 27, 2025 · 6 min read
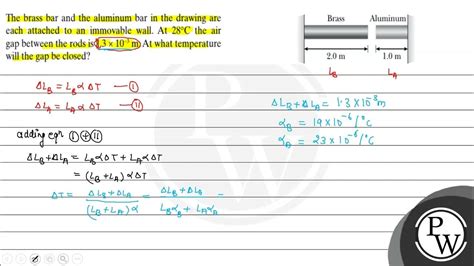
Table of Contents
- The Brass Bar And The Aluminum Bar In The Drawing
- Table of Contents
- The Brass Bar and the Aluminum Bar in the Drawing: A Deep Dive into Material Selection and Design Considerations
- Understanding the Properties of Brass and Aluminum
- Brass: A Versatile Alloy
- Aluminum: The Lightweight Champion
- Comparing Brass and Aluminum: A Head-to-Head Analysis
- Design Implications and Considerations
- Case Studies: Real-World Applications
- Conclusion: Informed Decision-Making is Key
- Latest Posts
- Latest Posts
- Related Post
The Brass Bar and the Aluminum Bar in the Drawing: A Deep Dive into Material Selection and Design Considerations
The seemingly simple inclusion of a brass bar and an aluminum bar in a technical drawing belies a complex decision-making process. Material selection is a critical aspect of engineering design, impacting everything from functionality and durability to cost and manufacturability. This article delves deep into the considerations behind choosing brass and aluminum, exploring their respective properties, applications, and the potential design implications of incorporating them within a larger project.
Understanding the Properties of Brass and Aluminum
Before comparing the two materials, let's establish a foundational understanding of their individual characteristics. This will provide a crucial context for analyzing their suitability within a specific design.
Brass: A Versatile Alloy
Brass is an alloy primarily composed of copper and zinc, with variations in the zinc content influencing its properties. Its characteristic golden-yellow hue is immediately recognizable. Key properties of brass include:
-
High Strength and Durability: Brass offers excellent tensile strength and resistance to wear, making it ideal for components requiring longevity and resistance to deformation. This durability is particularly relevant in applications subject to friction or repeated stress.
-
Excellent Machinability: Brass is relatively easy to machine, making it a cost-effective material for complex shapes and intricate details. This ease of machining reduces manufacturing time and costs compared to some harder metals.
-
Corrosion Resistance: Brass exhibits good corrosion resistance, particularly in atmospheric conditions. Its resistance to oxidation makes it suitable for outdoor applications and environments with moderate humidity. However, the level of corrosion resistance depends on the specific brass alloy composition. Some alloys exhibit superior resistance to specific corrosive agents than others.
-
Electrical Conductivity: While not as conductive as copper or aluminum, brass still possesses respectable electrical conductivity, making it suitable for certain electrical applications, particularly those requiring mechanical strength in addition to conductivity.
-
Aesthetic Appeal: The golden color and lustrous finish of brass contribute to its aesthetic appeal, often making it a preferred choice in decorative applications or where visual appeal is a significant design factor.
Aluminum: The Lightweight Champion
Aluminum is a lightweight, silvery-white metal renowned for its versatility and strength-to-weight ratio. Its properties include:
-
Lightweight: Aluminum's low density makes it an ideal choice where weight reduction is a priority, such as in aerospace, automotive, and portable applications. This reduced weight can translate to improved fuel efficiency or enhanced portability.
-
High Strength-to-Weight Ratio: Despite its lightness, aluminum offers impressive strength, making it suitable for structural applications requiring both strength and minimal weight. Advanced aluminum alloys exhibit even higher strength characteristics.
-
Excellent Corrosion Resistance: Aluminum forms a protective oxide layer that shields it from further corrosion, offering excellent resistance to atmospheric corrosion and many chemicals. This inherent protective layer makes aluminum a highly durable material for outdoor and corrosive environments.
-
High Electrical Conductivity: Aluminum possesses high electrical conductivity, making it a common choice for electrical wiring and transmission lines. Its conductivity is second only to copper amongst widely used metals.
-
Good Thermal Conductivity: Aluminum's excellent thermal conductivity makes it suitable for heat sinks, cooking utensils, and other applications requiring efficient heat transfer. This property is vital in managing thermal stresses within a design.
-
Recyclability: Aluminum is highly recyclable, making it an environmentally friendly material choice. Recycling aluminum requires significantly less energy compared to producing it from raw bauxite ore.
Comparing Brass and Aluminum: A Head-to-Head Analysis
Now that we understand the individual properties, let's compare brass and aluminum directly. This comparison will highlight the key differences and help determine which material is best suited for a given application.
Feature | Brass | Aluminum |
---|---|---|
Density | Higher | Lower |
Strength | High | High (depending on alloy) |
Corrosion Resistance | Good | Excellent |
Machinability | Excellent | Good (depends on alloy and temper) |
Electrical Conductivity | Moderate | High |
Thermal Conductivity | Moderate | High |
Cost | Generally higher than aluminum | Generally lower than brass |
Appearance | Golden-yellow, lustrous | Silvery-white, matte or polished |
Design Implications and Considerations
The choice between brass and aluminum significantly impacts several aspects of the design process:
-
Functionality: The mechanical properties of each material dictate its suitability for specific functional requirements. High-stress applications may necessitate brass's higher strength, while weight-sensitive designs might favor aluminum's lightness.
-
Manufacturing: Brass's excellent machinability can simplify the manufacturing process, reducing costs and lead times. Aluminum's machinability also generally falls under ‘good’, but it depends heavily on the specific alloy and its temper.
-
Cost: Aluminum typically offers a lower initial material cost compared to brass. However, the manufacturing processes, including potential surface treatments, should be factored into the overall cost analysis.
-
Aesthetics: The distinct appearances of brass and aluminum influence the final product's aesthetic appeal. Brass contributes to a classic, sophisticated look, whereas aluminum presents a more modern, industrial appearance.
-
Environmental Impact: Aluminum's high recyclability makes it an environmentally responsible choice. The environmental footprint of brass production, while not insignificant, is largely dependent on the sourcing and manufacturing processes.
-
Joining Methods: The selection of joining methods (welding, brazing, adhesive bonding, etc.) will vary depending on the chosen metal. Aluminum welding, for instance, requires specialized techniques and equipment compared to brass.
Case Studies: Real-World Applications
Let's explore some real-world examples to illustrate the practical application of brass and aluminum in different contexts:
Scenario 1: Musical Instruments
Brass is often preferred for certain musical instrument components due to its acoustic properties and attractive appearance. The resonant qualities of brass contribute to the rich tone of instruments like trumpets and trombones.
Scenario 2: Automotive Industry
Aluminum plays a crucial role in the automotive industry due to its lightweight properties, enabling improved fuel efficiency. Aluminum alloys are used extensively in vehicle bodies, engine components, and wheels.
Scenario 3: Electrical Connectors
Brass is utilized in electrical connectors due to its good electrical conductivity and excellent machinability. The intricate designs of many connectors benefit from brass's ease of machining.
Scenario 4: Heat Sinks
Aluminum's exceptional thermal conductivity makes it the material of choice for heat sinks in electronic devices. Its ability to efficiently dissipate heat is crucial in preventing overheating.
Scenario 5: Architectural Applications
Both brass and aluminum find applications in architectural design. Brass is often used for decorative elements, while aluminum is frequently selected for structural components due to its strength-to-weight ratio and corrosion resistance.
Conclusion: Informed Decision-Making is Key
The choice between a brass bar and an aluminum bar in a drawing is not arbitrary; it's a carefully considered decision based on a thorough understanding of each material's properties and their implications for the overall design. Factors such as functionality, cost, aesthetics, manufacturability, and environmental considerations all play crucial roles in determining the optimal material for a specific application. By meticulously evaluating these factors, engineers and designers can ensure the selection of the most suitable material for optimal performance and long-term success. Remember, understanding the nuances of material properties and their impact on the design process is paramount to creating effective and efficient products. The seemingly simple choice between a brass bar and an aluminum bar underscores the intricate complexities of material selection in engineering design.
Latest Posts
Latest Posts
-
Label The Planes Of The Body
Mar 31, 2025
-
Select All The Events Unique To Endochondral Ossification
Mar 31, 2025
-
All Of The Following Are Anxiety Disorders Except
Mar 31, 2025
-
Authorized Common Stock Refers To The Total Number Of Shares
Mar 31, 2025
-
Match The Type Of Simple Epithelium With Its Description
Mar 31, 2025
Related Post
Thank you for visiting our website which covers about The Brass Bar And The Aluminum Bar In The Drawing . We hope the information provided has been useful to you. Feel free to contact us if you have any questions or need further assistance. See you next time and don't miss to bookmark.