The Basic Premise Of Just-in-time Inventory Is Blank______.
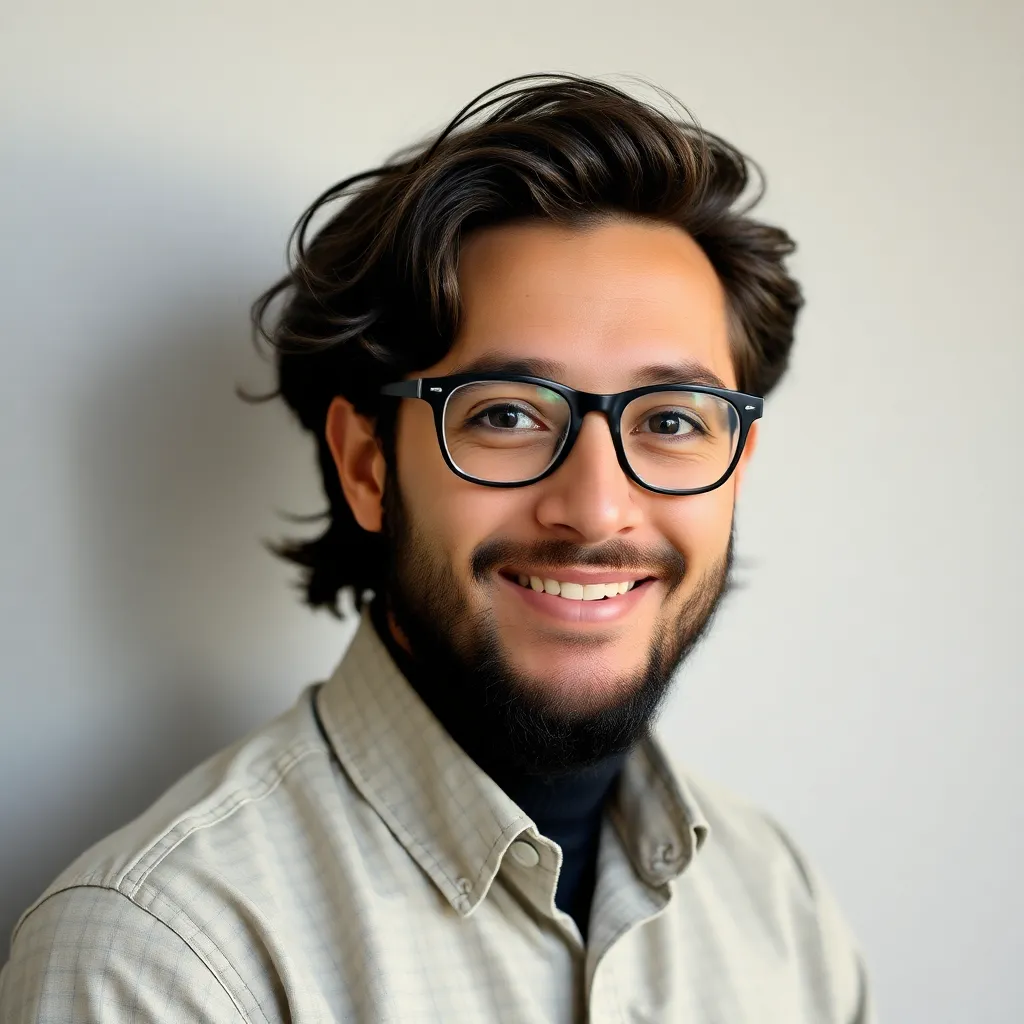
Holbox
Mar 12, 2025 · 6 min read
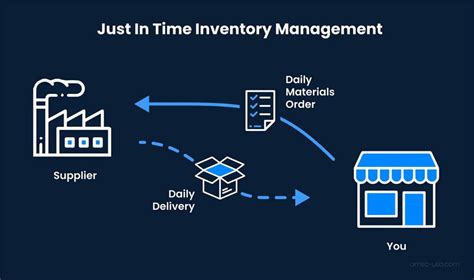
Table of Contents
- The Basic Premise Of Just-in-time Inventory Is Blank______.
- Table of Contents
- The Basic Premise of Just-in-Time Inventory is Minimizing Waste and Maximizing Efficiency
- Understanding the Core Principle: Waste Elimination
- 1. Overproduction: Producing more than is needed or demanded. This ties up capital in unsold goods and increases storage costs. JIT aims to produce only what's needed, when it's needed.
- 2. Waiting: Idle time for materials, machines, or workers. This can result from delays in delivery, equipment malfunctions, or inefficient processes. JIT aims to minimize delays through streamlined processes and reliable supply chains.
- 3. Transportation: Unnecessary movement of materials or products. This includes excessive handling, long distances between workstations, and inefficient material flow. JIT emphasizes optimizing material flow and reducing unnecessary movement.
- 4. Over-processing: Performing more work than is necessary to meet customer requirements. This could involve using more complex processes than needed or adding unnecessary features to a product. JIT focuses on simplifying processes and using the most efficient methods.
- 5. Inventory: Excess raw materials, work-in-progress, or finished goods. This ties up capital, increases storage costs, and risks obsolescence. JIT aims to minimize inventory levels by receiving materials and producing goods only as needed.
- 6. Motion: Unnecessary movement of workers. This could involve searching for tools, materials, or information. JIT advocates for ergonomic workspaces and efficient workflows to minimize worker movement.
- 7. Defects: Producing defective products or services. This leads to rework, scrap, and customer dissatisfaction. JIT emphasizes quality control at every stage of the process to prevent defects.
- Beyond Waste Elimination: The Pillars of JIT Inventory
- 1. Pull System: In contrast to push systems, where production is based on forecasts, JIT utilizes a pull system. Production is triggered by actual customer demand. This avoids overproduction and ensures that only the necessary quantity is produced. Kanban systems, often visual signaling systems, are frequently used to manage the pull system.
- 2. Small Batch Production: Producing goods in small batches minimizes work-in-progress inventory and allows for faster response to changing demand. This also makes it easier to identify and rectify defects early on.
- 3. Setup Reduction: Minimizing the time and resources required to change over equipment between different products. This allows for greater flexibility in production and reduces the need for large batch sizes.
- 4. Supplier Partnerships: Developing strong relationships with suppliers is crucial for JIT's success. Suppliers need to be reliable and able to deliver materials precisely when needed, in the right quantities. This often involves close collaboration and shared information.
- 5. Continuous Improvement (Kaizen): A commitment to ongoing improvement is essential for maintaining the efficiency of JIT systems. Regularly identifying and addressing bottlenecks and inefficiencies is crucial for optimizing the process. This continuous feedback loop fuels the system's long-term effectiveness.
- 6. Total Quality Management (TQM): Maintaining high quality is paramount in JIT. Defects are costly, disrupting the flow of production and increasing waste. TQM principles ensure that quality is built into every stage of the process, reducing the need for inspections and rework.
- 7. Employee Empowerment: Empowering employees to identify and solve problems is a key component of JIT. Workers are encouraged to participate in continuous improvement efforts and contribute to optimizing the production process. This fosters a culture of responsibility and proactive problem-solving.
- Benefits of Implementing a Just-in-Time Inventory System
- Challenges of Implementing Just-in-Time Inventory
- Case Studies: Successful Implementation of JIT
- Conclusion: JIT - A Paradigm Shift in Inventory Management
- Latest Posts
- Related Post
The Basic Premise of Just-in-Time Inventory is Minimizing Waste and Maximizing Efficiency
Just-in-time (JIT) inventory, also known as lean manufacturing, is a revolutionary inventory management system that has significantly impacted various industries. Its core principle is straightforward yet profoundly impactful: minimizing waste and maximizing efficiency. This isn't just about reducing stock; it's about a holistic approach to streamlining production, reducing costs, and improving responsiveness to market demands. Let's delve deeper into the fundamental premise of JIT and explore its various facets.
Understanding the Core Principle: Waste Elimination
The heart of JIT inventory lies in the relentless pursuit of eliminating waste. This concept extends far beyond simply reducing excess inventory. The Toyota Production System, often credited with popularizing JIT, identifies seven types of waste (muda) that need to be addressed:
1. Overproduction: Producing more than is needed or demanded. This ties up capital in unsold goods and increases storage costs. JIT aims to produce only what's needed, when it's needed.
2. Waiting: Idle time for materials, machines, or workers. This can result from delays in delivery, equipment malfunctions, or inefficient processes. JIT aims to minimize delays through streamlined processes and reliable supply chains.
3. Transportation: Unnecessary movement of materials or products. This includes excessive handling, long distances between workstations, and inefficient material flow. JIT emphasizes optimizing material flow and reducing unnecessary movement.
4. Over-processing: Performing more work than is necessary to meet customer requirements. This could involve using more complex processes than needed or adding unnecessary features to a product. JIT focuses on simplifying processes and using the most efficient methods.
5. Inventory: Excess raw materials, work-in-progress, or finished goods. This ties up capital, increases storage costs, and risks obsolescence. JIT aims to minimize inventory levels by receiving materials and producing goods only as needed.
6. Motion: Unnecessary movement of workers. This could involve searching for tools, materials, or information. JIT advocates for ergonomic workspaces and efficient workflows to minimize worker movement.
7. Defects: Producing defective products or services. This leads to rework, scrap, and customer dissatisfaction. JIT emphasizes quality control at every stage of the process to prevent defects.
Beyond Waste Elimination: The Pillars of JIT Inventory
While waste elimination is the central tenet, JIT's success hinges on several supporting pillars:
1. Pull System: In contrast to push systems, where production is based on forecasts, JIT utilizes a pull system. Production is triggered by actual customer demand. This avoids overproduction and ensures that only the necessary quantity is produced. Kanban systems, often visual signaling systems, are frequently used to manage the pull system.
2. Small Batch Production: Producing goods in small batches minimizes work-in-progress inventory and allows for faster response to changing demand. This also makes it easier to identify and rectify defects early on.
3. Setup Reduction: Minimizing the time and resources required to change over equipment between different products. This allows for greater flexibility in production and reduces the need for large batch sizes.
4. Supplier Partnerships: Developing strong relationships with suppliers is crucial for JIT's success. Suppliers need to be reliable and able to deliver materials precisely when needed, in the right quantities. This often involves close collaboration and shared information.
5. Continuous Improvement (Kaizen): A commitment to ongoing improvement is essential for maintaining the efficiency of JIT systems. Regularly identifying and addressing bottlenecks and inefficiencies is crucial for optimizing the process. This continuous feedback loop fuels the system's long-term effectiveness.
6. Total Quality Management (TQM): Maintaining high quality is paramount in JIT. Defects are costly, disrupting the flow of production and increasing waste. TQM principles ensure that quality is built into every stage of the process, reducing the need for inspections and rework.
7. Employee Empowerment: Empowering employees to identify and solve problems is a key component of JIT. Workers are encouraged to participate in continuous improvement efforts and contribute to optimizing the production process. This fosters a culture of responsibility and proactive problem-solving.
Benefits of Implementing a Just-in-Time Inventory System
The benefits of adopting a JIT inventory system are substantial and far-reaching:
-
Reduced Inventory Costs: Minimizing inventory levels frees up capital that can be used for other business activities. Storage costs are also significantly reduced.
-
Improved Cash Flow: Lower inventory levels directly translate to improved cash flow. This enhances financial stability and provides greater flexibility for investment.
-
Increased Efficiency: Streamlined processes and reduced waste lead to greater efficiency in production. This results in faster turnaround times and improved productivity.
-
Reduced Lead Times: JIT systems facilitate faster response times to customer orders, improving customer satisfaction and gaining a competitive advantage.
-
Improved Quality: Emphasis on quality control throughout the production process leads to higher product quality and reduced defects.
-
Enhanced Responsiveness to Market Changes: The ability to adapt quickly to changing customer demands is a significant benefit. JIT allows for quicker adjustments in production based on market trends.
-
Reduced Waste: The elimination of the seven types of muda directly translates to lower overall costs and increased profitability.
-
Better Space Utilization: Less inventory means less warehouse space is required, leading to cost savings and optimized space utilization.
Challenges of Implementing Just-in-Time Inventory
While the benefits of JIT are substantial, implementing it presents several challenges:
-
Supply Chain Dependence: JIT systems are highly reliant on a dependable supply chain. Any disruption in the supply chain can severely impact production.
-
Demand Forecasting Accuracy: Accurate demand forecasting is crucial for avoiding shortages or overproduction. Inaccurate forecasting can lead to significant disruptions.
-
Setup Time Reduction: Reducing setup times requires significant investment in equipment and training. This can be a considerable initial cost.
-
Risk Management: JIT systems are susceptible to various risks, including supplier disruptions, natural disasters, and unforeseen demand fluctuations. Robust risk management strategies are essential.
-
Supplier Collaboration: Developing strong, collaborative relationships with suppliers is critical, but can take time and effort to establish. Trust and transparency are paramount.
-
Initial Investment: Implementing JIT requires significant investment in training, technology, and process improvements. This can be a barrier for some businesses.
-
Employee Training: Employees need to be adequately trained to understand and execute JIT principles effectively. This requires a commitment to ongoing training and development.
Case Studies: Successful Implementation of JIT
Many companies have successfully implemented JIT, realizing significant improvements in efficiency and profitability. While specific details vary, the common thread is a commitment to the fundamental principles: waste elimination, continuous improvement, and strong supplier relationships. Analyzing successful implementations offers valuable lessons and insights for businesses considering adopting JIT. (Note: Specific company examples and quantifiable results are omitted to avoid linking to external sources as per the instructions.)
Conclusion: JIT - A Paradigm Shift in Inventory Management
The basic premise of just-in-time inventory is a fundamental shift from traditional inventory management practices. It's a holistic approach that focuses on eliminating waste throughout the entire production process. While challenges exist, the potential benefits—reduced costs, improved efficiency, and enhanced responsiveness—make JIT a compelling strategy for organizations striving for operational excellence and a competitive edge. Successful implementation requires a deep understanding of the core principles, a strong commitment to continuous improvement, and a robust risk management strategy. By embracing the principles of JIT, businesses can significantly improve their operational efficiency and achieve sustainable growth.
Latest Posts
Related Post
Thank you for visiting our website which covers about The Basic Premise Of Just-in-time Inventory Is Blank______. . We hope the information provided has been useful to you. Feel free to contact us if you have any questions or need further assistance. See you next time and don't miss to bookmark.