The 5ss Developed By The Japanese Do Not Include
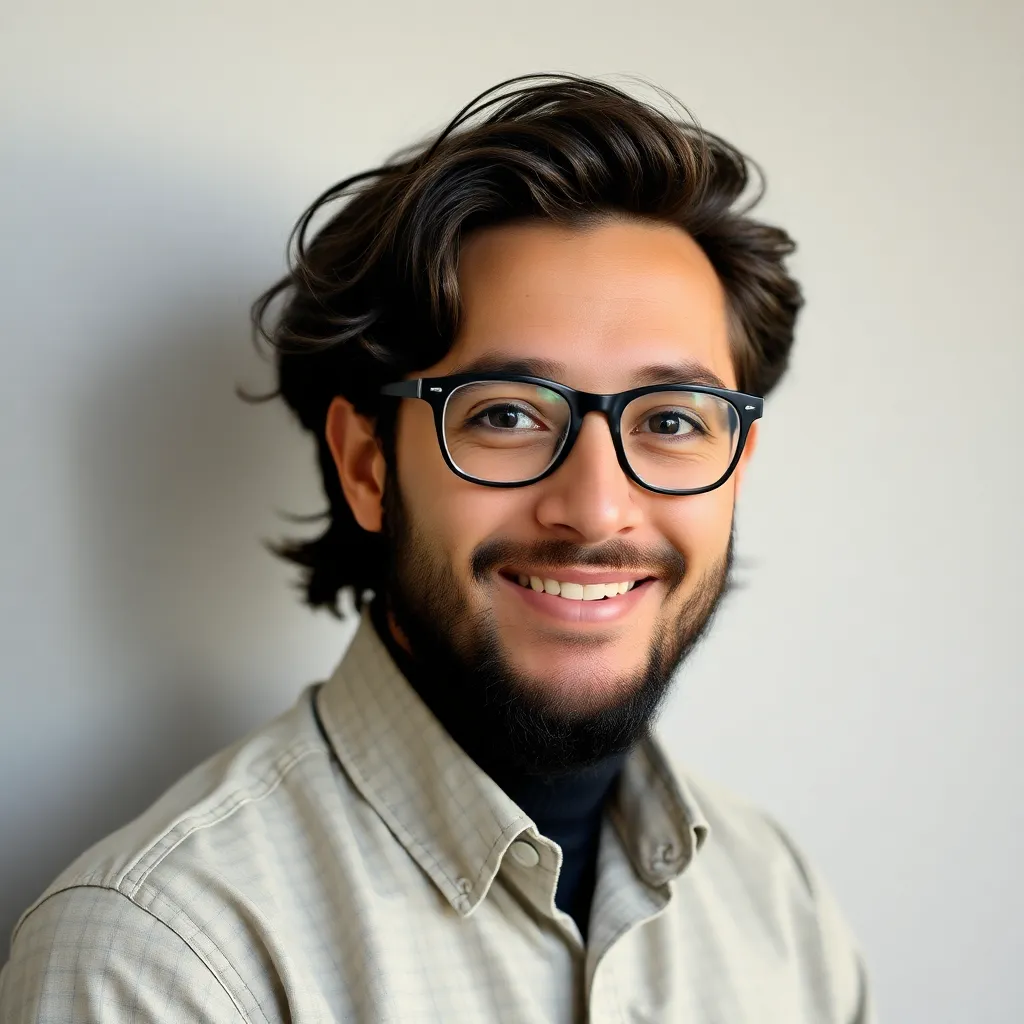
Holbox
Apr 24, 2025 · 6 min read
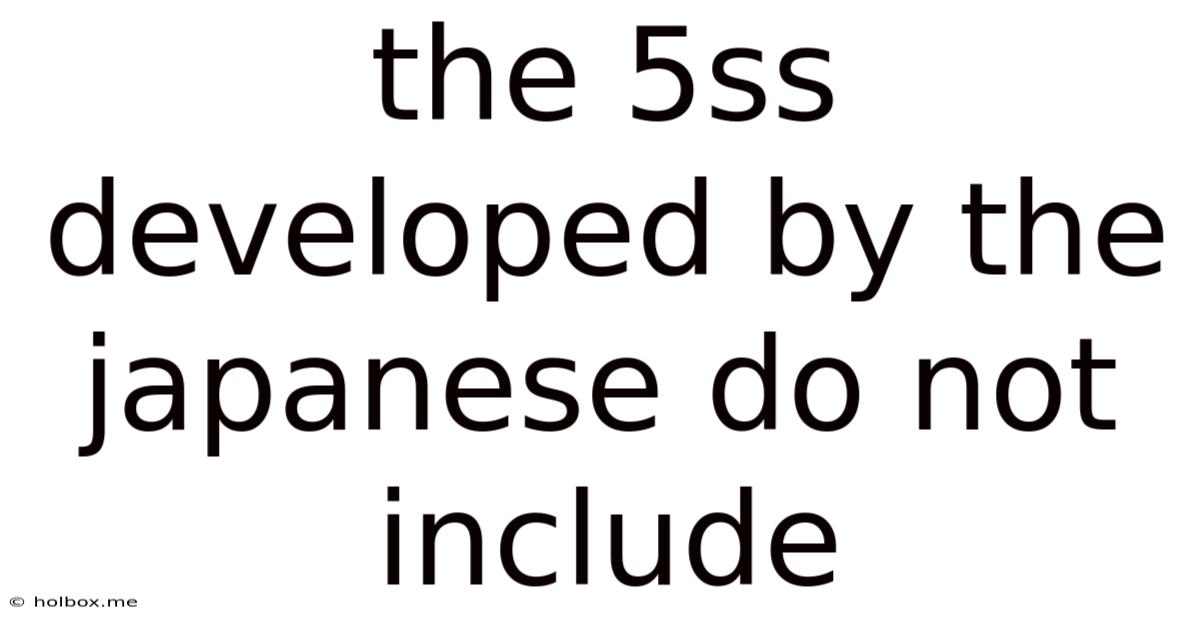
Table of Contents
- The 5ss Developed By The Japanese Do Not Include
- Table of Contents
- The 5S Methodology: What It Is and What It Isn't
- The Five Pillars of 5S: A Detailed Breakdown
- 1. Seiri (Sort): Eliminating the Unnecessary
- 2. Seiton (Set in Order): Organizing for Efficiency
- 3. Seisō (Shine): Maintaining Cleanliness
- 4. Seiketsu (Standardize): Maintaining Consistency
- 5. Shitsuke (Sustain): Habituating Good Practices
- The 5S Methodology: Addressing Common Misconceptions
- Misconception 1: 5S is only for Manufacturing
- Misconception 2: 5S is a One-Time Event
- Misconception 3: 5S is Only About Cleanliness
- Misconception 4: 5S is a Top-Down Initiative
- Misconception 5: 5S Doesn't Require Training
- Misconception 6: 5S is Just About Physical Space
- Misconception 7: 5S is a Quick Fix
- The 5S Methodology: Beyond the Misconceptions
- Latest Posts
- Latest Posts
- Related Post
The 5S Methodology: What It Is and What It Isn't
The 5S methodology, originating in Japan, is a powerful lean manufacturing technique aimed at optimizing workplace organization and efficiency. While widely adopted and adapted globally, misconceptions often arise about its precise components. This article delves deep into the 5S system, clarifying what it does include and, crucially, what it doesn't. Understanding these distinctions is key to effectively implementing 5S and reaping its numerous benefits.
The Five Pillars of 5S: A Detailed Breakdown
Before exploring the misconceptions, let's establish a solid foundation by outlining the core components of 5S:
1. Seiri (Sort): Eliminating the Unnecessary
Seiri, often translated as "Sort" or "Segregate," is the foundational step. It involves rigorously identifying and removing anything from the workspace that isn't essential for current operations. This includes:
- Unnecessary tools and equipment: Items that are outdated, broken, or rarely used.
- Obsolete documents and files: Paperwork, manuals, and digital files that are no longer relevant.
- Excess inventory: Materials and supplies exceeding immediate needs.
- Personal items: Belongings unrelated to work, such as personal photographs or snacks.
The goal of Seiri is to declutter the workspace, creating a more streamlined and efficient environment. This often involves a thorough assessment of every item, asking the crucial question: "Does this item add value to our work?" If the answer is no, it's removed.
2. Seiton (Set in Order): Organizing for Efficiency
Seiton, meaning "Set in Order" or "Systematize," focuses on organizing the remaining items for optimal accessibility and workflow. Key aspects include:
- Logical placement: Positioning frequently used items within easy reach, while less frequently used items are stored systematically.
- Clear labeling: Every item should be clearly labeled and identifiable, improving findability and reducing search time.
- Visual management: Employing visual cues such as color-coding, shadow boards, and kanban systems to enhance organization and quickly identify missing items.
- Designated storage: Creating dedicated storage locations for tools, materials, and equipment, preventing clutter and facilitating quick retrieval.
The ultimate aim of Seiton is to minimize wasted time searching for items and ensure a smooth, uninterrupted workflow.
3. Seisō (Shine): Maintaining Cleanliness
Seisō, translated as "Shine" or "Clean," focuses on maintaining a consistently clean and orderly workspace. This goes beyond basic tidiness; it involves:
- Regular cleaning: Implementing a schedule for routine cleaning tasks, ensuring the workspace is free from dust, dirt, and debris.
- Defect detection: Using cleaning as an opportunity to identify potential problems, such as leaks, wear and tear, or safety hazards.
- Preventive maintenance: Addressing minor issues promptly to prevent them from escalating into more significant problems.
- Team involvement: Engaging all team members in cleaning responsibilities, fostering a shared sense of ownership and responsibility.
Seisō aims to create a safer and more hygienic work environment, preventing accidents and equipment malfunctions.
4. Seiketsu (Standardize): Maintaining Consistency
Seiketsu, meaning "Standardize" or "Cleanliness," aims to institutionalize the practices established in the previous three steps. This involves:
- Documenting procedures: Creating clear and concise documentation of cleaning, organization, and maintenance procedures.
- Training and education: Providing comprehensive training to all team members to ensure consistent adherence to the established standards.
- Regular audits: Implementing regular audits to verify adherence to standards and identify areas for improvement.
- Continuous improvement: Continuously refining processes and procedures to optimize efficiency and effectiveness.
Seiketsu ensures that the gains achieved through Seiri, Seiton, and Seisō are maintained over the long term, preventing a relapse into disorganization and inefficiency.
5. Shitsuke (Sustain): Habituating Good Practices
Shitsuke, often translated as "Sustain" or "Discipline," is the final and arguably most crucial step. It focuses on embedding the 5S principles into the company culture:
- Continuous improvement: Fostering a culture of continuous improvement, where team members are encouraged to identify and address inefficiencies.
- Self-discipline: Developing self-discipline among team members to adhere to the established standards consistently.
- Positive reinforcement: Recognizing and rewarding individuals and teams who consistently demonstrate adherence to 5S principles.
- Regular review and adjustment: Periodically reviewing and adjusting 5S procedures to adapt to changing needs and circumstances.
Shitsuke ensures that 5S becomes more than just a program; it becomes a way of life within the organization.
The 5S Methodology: Addressing Common Misconceptions
While the 5S methodology is relatively straightforward, several misconceptions often hinder its effective implementation. Understanding what 5S doesn't encompass is crucial for successful execution.
Misconception 1: 5S is only for Manufacturing
Reality: While 5S originated in manufacturing, its principles are universally applicable. It's effectively used in offices, hospitals, schools, and virtually any environment seeking improved organization, efficiency, and safety. Adapting the principles to different contexts is key. For example, an office might focus on digital file organization within Seiton, whereas a hospital would prioritize sterile environments within Seisō.
Misconception 2: 5S is a One-Time Event
Reality: 5S is not a one-time cleaning spree. It's an ongoing process of continuous improvement. Seiri might involve initial significant decluttering, but regular reviews and adjustments are crucial to maintain the gains achieved. Shitsuke, the emphasis on sustaining the system, highlights this continuous nature. It's about integrating the practices into daily routines.
Misconception 3: 5S is Only About Cleanliness
Reality: While cleanliness (Seisō) is a vital component, 5S encompasses much more than just tidiness. It's a holistic approach that integrates organization, standardization, and discipline to optimize overall efficiency and productivity. Cleanliness is a byproduct of the overall system, not the primary goal.
Misconception 4: 5S is a Top-Down Initiative
Reality: While leadership buy-in is essential, successful 5S implementation requires the active participation of all team members. It's crucial to foster a sense of shared ownership and responsibility. Empowering employees to contribute their ideas and participate in the process is vital for long-term success.
Misconception 5: 5S Doesn't Require Training
Reality: Effective 5S implementation requires thorough training and education for all team members. This training should not just focus on the theoretical aspects of 5S but also involve practical application and hands-on experience. Regular refresher training can reinforce the practices and ensure continued adherence to standards.
Misconception 6: 5S is Just About Physical Space
Reality: While 5S addresses the physical workspace, it can also be applied to improve digital organization. This might involve streamlining digital files, optimizing software interfaces, and improving the overall digital workflow. Many organizations now incorporate digital aspects into their 5S programs.
Misconception 7: 5S is a Quick Fix
Reality: Implementing 5S effectively takes time, dedication, and commitment. It's a process of gradual improvement, not a quick fix. It requires consistent effort and regular review to maintain and optimize the system. Expecting immediate and drastic results can lead to disappointment and hinder long-term success.
The 5S Methodology: Beyond the Misconceptions
Understanding what 5S is not allows for a clearer understanding of its true power. It is not a quick fix, a one-time event, or merely about cleanliness. Instead, it's a comprehensive system focused on continuous improvement, sustained through team commitment and meticulous attention to detail. By correctly implementing 5S and avoiding common misconceptions, organizations can transform their workspaces into highly efficient, organized, and productive environments. This ultimately leads to increased safety, reduced waste, enhanced quality, and improved overall performance. The true success of 5S lies not in the initial implementation but in the consistent application and continuous improvement that follow.
Latest Posts
Latest Posts
-
Correctly Label The Following Structures Related To The Parathyroid Gland
May 10, 2025
-
You Recently Decreased Your Average Number
May 10, 2025
-
How Do You Cite A Webinar In Apa
May 10, 2025
-
Determine The Maturity Date And Compute Interest For Each Note
May 10, 2025
-
Match Each Film Movement To Its Contemporaneous Historical Event
May 10, 2025
Related Post
Thank you for visiting our website which covers about The 5ss Developed By The Japanese Do Not Include . We hope the information provided has been useful to you. Feel free to contact us if you have any questions or need further assistance. See you next time and don't miss to bookmark.