Steam Flows Steadily Through An Adiabatic Turbine
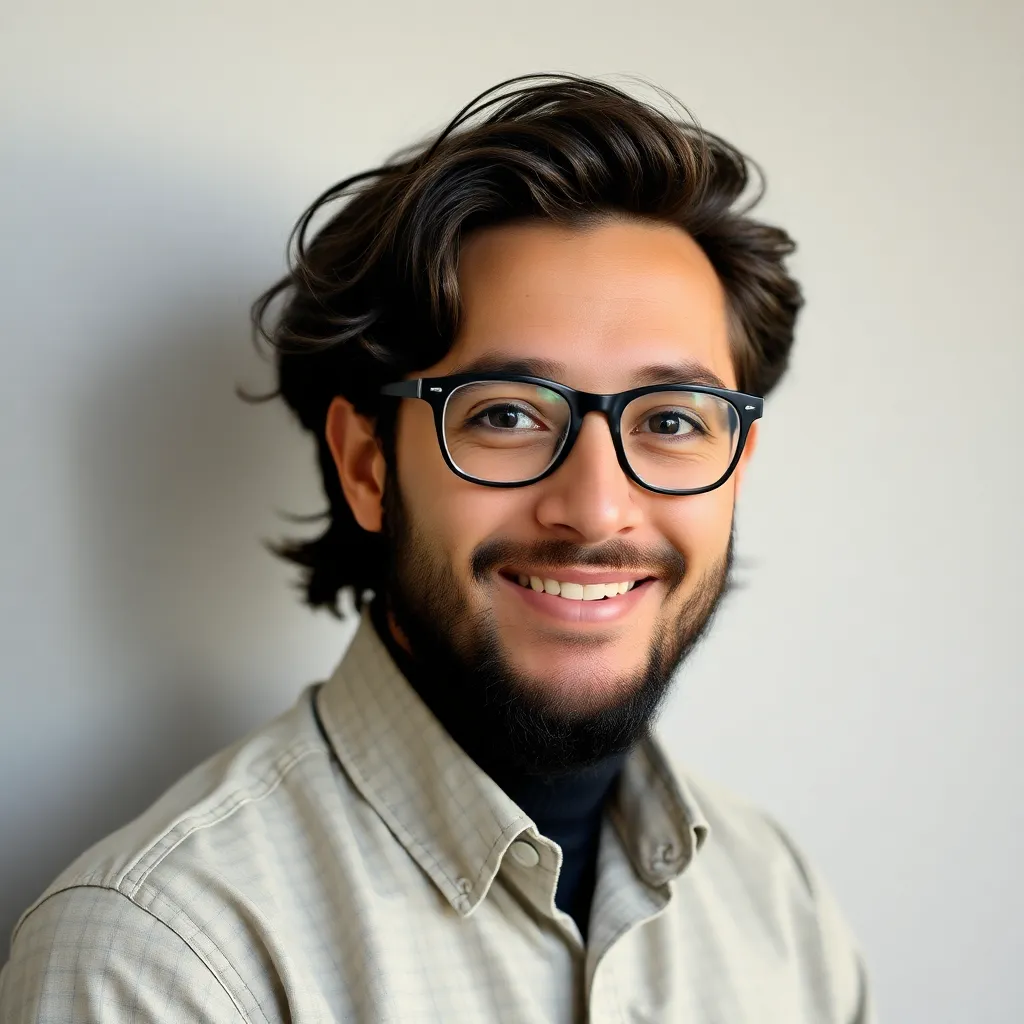
Holbox
Mar 29, 2025 · 6 min read
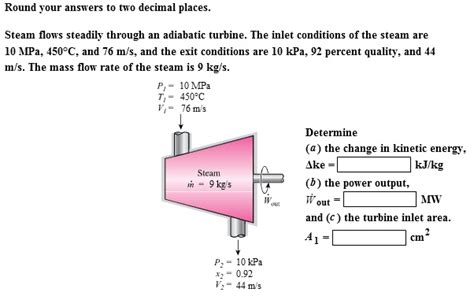
Table of Contents
- Steam Flows Steadily Through An Adiabatic Turbine
- Table of Contents
- Steam Flows Steadily Through an Adiabatic Turbine: A Comprehensive Analysis
- Understanding Adiabatic Processes
- Ideal vs. Real Adiabatic Processes
- Applying the Steady Flow Energy Equation (SFEE)
- Isentropic Efficiency and Turbine Performance
- Steam Properties and Thermodynamic Tables
- Impact of Pressure and Temperature
- Effect of Back Pressure
- Types of Steam Turbines
- Impulse Turbines
- Reaction Turbines
- Turbine Blade Design and Optimization
- Maintenance and Efficiency Monitoring
- Beyond the Adiabatic Assumption: Real-World Considerations
- Conclusion
- Latest Posts
- Latest Posts
- Related Post
Steam Flows Steadily Through an Adiabatic Turbine: A Comprehensive Analysis
Steam turbines, crucial components in power generation and various industrial processes, convert the thermal energy of high-pressure steam into mechanical work. Understanding the thermodynamics governing steam flow through these turbines is vital for optimizing efficiency and performance. This article delves deep into the intricacies of steady, adiabatic steam flow through a turbine, exploring key concepts, equations, and real-world implications.
Understanding Adiabatic Processes
Before diving into the specifics of steam turbine operation, let's clarify the term "adiabatic." An adiabatic process is one where there is no heat transfer between the system (the steam) and its surroundings. This doesn't mean the temperature remains constant; instead, temperature changes are solely due to work done by or on the system. In a steam turbine, the adiabatic assumption simplifies analysis, although in reality, some heat loss always occurs. However, for many practical purposes, the adiabatic model provides an excellent approximation.
Ideal vs. Real Adiabatic Processes
It’s important to differentiate between an ideal and a real adiabatic process. An ideal adiabatic process assumes no heat transfer and no internal irreversibilities (like friction). This leads to an isentropic process, where entropy remains constant. A real adiabatic process, on the other hand, accounts for irreversibilities, leading to an increase in entropy. The difference between these two is crucial for assessing turbine efficiency.
Applying the Steady Flow Energy Equation (SFEE)
The cornerstone of analyzing steady flow through a turbine is the Steady Flow Energy Equation (SFEE). For an adiabatic turbine, the SFEE simplifies considerably because the heat transfer term (Q) becomes zero. The equation can be expressed as:
h₁ + (V₁²/2g) + gz₁ = h₂ + (V₂²/2g) + gz₂ + W
Where:
- h₁ and h₂: Specific enthalpy at the inlet and outlet, respectively.
- V₁ and V₂: Inlet and outlet velocities.
- g: Acceleration due to gravity.
- z₁ and z₂: Inlet and outlet elevations.
- W: Work done per unit mass of steam.
In many turbine applications, the changes in kinetic and potential energy ((V₁²/2g) + gz₁ and (V₂²/2g) + gz₂) are negligible compared to the enthalpy change. This simplifies the SFEE to:
h₁ = h₂ + W
This simplified equation highlights the fundamental principle: the decrease in enthalpy of the steam directly translates into the work output of the turbine.
Isentropic Efficiency and Turbine Performance
As mentioned earlier, real adiabatic processes are not isentropic due to irreversibilities within the turbine. These irreversibilities include:
- Friction losses: Internal friction within the steam flow and between the steam and turbine blades.
- Blade imperfections: Deviations from ideal blade geometry and manufacturing tolerances.
- Leakage: Steam leakage past seals and around the blades.
To account for these losses, we introduce the concept of isentropic efficiency (ηᵢs). This efficiency compares the actual work output of the turbine to the work output that would be obtained if the process were isentropic:
ηᵢs = (Actual work output) / (Isentropic work output)
ηᵢs = (h₁ - h₂)/(h₁ - h₂s)
Where:
- h₂: Actual specific enthalpy at the outlet.
- h₂s: Specific enthalpy at the outlet if the process were isentropic.
A higher isentropic efficiency indicates a more efficient turbine with lower energy losses.
Steam Properties and Thermodynamic Tables
Analyzing steam flow requires a thorough understanding of steam properties and their relationships. Steam tables provide crucial data, such as specific enthalpy, entropy, and specific volume, as functions of pressure and temperature. These tables are essential for calculating the enthalpy changes and determining the isentropic efficiency. Software and online calculators are also readily available to simplify these calculations.
Impact of Pressure and Temperature
The pressure and temperature of the steam significantly affect turbine performance. Higher inlet pressure and temperature lead to a larger enthalpy drop, resulting in higher work output. However, material limitations and safety considerations restrict the operating pressures and temperatures. Careful optimization is necessary to balance high performance with operational safety and equipment lifespan.
Effect of Back Pressure
The pressure at the turbine outlet (back pressure) also influences performance. Lower back pressure increases the pressure difference across the turbine, leading to a higher enthalpy drop and consequently, more work output. However, the choice of back pressure depends on the downstream system requirements and the overall plant efficiency.
Types of Steam Turbines
Several types of steam turbines are employed in power generation and industry, each with specific design features and applications.
Impulse Turbines
In impulse turbines, the steam expands in nozzles before striking the turbine blades. The pressure remains essentially constant across the blades. These turbines are generally used for high-pressure, low-volume steam applications.
Reaction Turbines
Reaction turbines use a combination of pressure drop and velocity increase across the blades to produce work. The steam expands both in the nozzles and across the blades. These turbines are typically used for lower-pressure, higher-volume steam.
Turbine Blade Design and Optimization
The design of turbine blades is crucial for efficiency and durability. Blade profiles are carefully optimized to minimize losses due to friction and shock waves. Factors such as blade angle, length, and material properties significantly impact performance. Advanced computational fluid dynamics (CFD) techniques are extensively used in modern turbine blade design.
Maintenance and Efficiency Monitoring
Regular maintenance and performance monitoring are essential for maintaining optimal turbine efficiency. This includes inspection for blade erosion, wear, and leakage, as well as regular cleaning and lubrication. Data acquisition systems continuously monitor key operating parameters, allowing for early detection of potential issues and timely maintenance interventions. Efficiency monitoring enables optimization of operating conditions and proactive measures to prevent performance degradation.
Beyond the Adiabatic Assumption: Real-World Considerations
While the adiabatic assumption simplifies the analysis, real-world steam turbines experience some heat loss. This heat loss, although often small, reduces the efficiency. Advanced models incorporate heat transfer calculations to achieve more precise performance predictions. Other factors not fully captured by the simplified adiabatic model include:
- Moisture content: As steam expands, it can condense, leading to increased erosion and reduced efficiency.
- Non-uniform flow: Variations in flow velocity and pressure within the turbine can affect performance.
- Blade vibration: Vibration can cause fatigue and damage to turbine blades, negatively impacting efficiency.
Accounting for these factors in detailed simulations leads to more accurate assessments and optimized designs.
Conclusion
Steady, adiabatic flow through a steam turbine provides a fundamental framework for understanding turbine operation. Applying the steady flow energy equation, analyzing steam properties, and considering isentropic efficiency are crucial steps in evaluating turbine performance. While the adiabatic assumption offers simplification, incorporating real-world factors such as heat loss, moisture content, and non-uniform flow leads to more realistic models. Continuous advancements in turbine blade design, materials science, and computational modeling contribute to increasingly efficient and reliable steam turbines, playing a vital role in power generation and numerous industrial processes. A comprehensive understanding of the principles outlined in this article is essential for engineers involved in the design, operation, and maintenance of these critical components. Continued research and development aim to push the boundaries of steam turbine technology, maximizing efficiency and minimizing environmental impact.
Latest Posts
Latest Posts
-
An Elderly Widower You Care For
Apr 02, 2025
-
Medical Language For Modern Health Care
Apr 02, 2025
-
In September 2009 The Sea Surface Temperature Was
Apr 02, 2025
-
An Improvement In Production Technology Will
Apr 02, 2025
-
Problems In Balance May Follow Trauma To Which Nerve
Apr 02, 2025
Related Post
Thank you for visiting our website which covers about Steam Flows Steadily Through An Adiabatic Turbine . We hope the information provided has been useful to you. Feel free to contact us if you have any questions or need further assistance. See you next time and don't miss to bookmark.