Steam Enters A Nozzle At 400
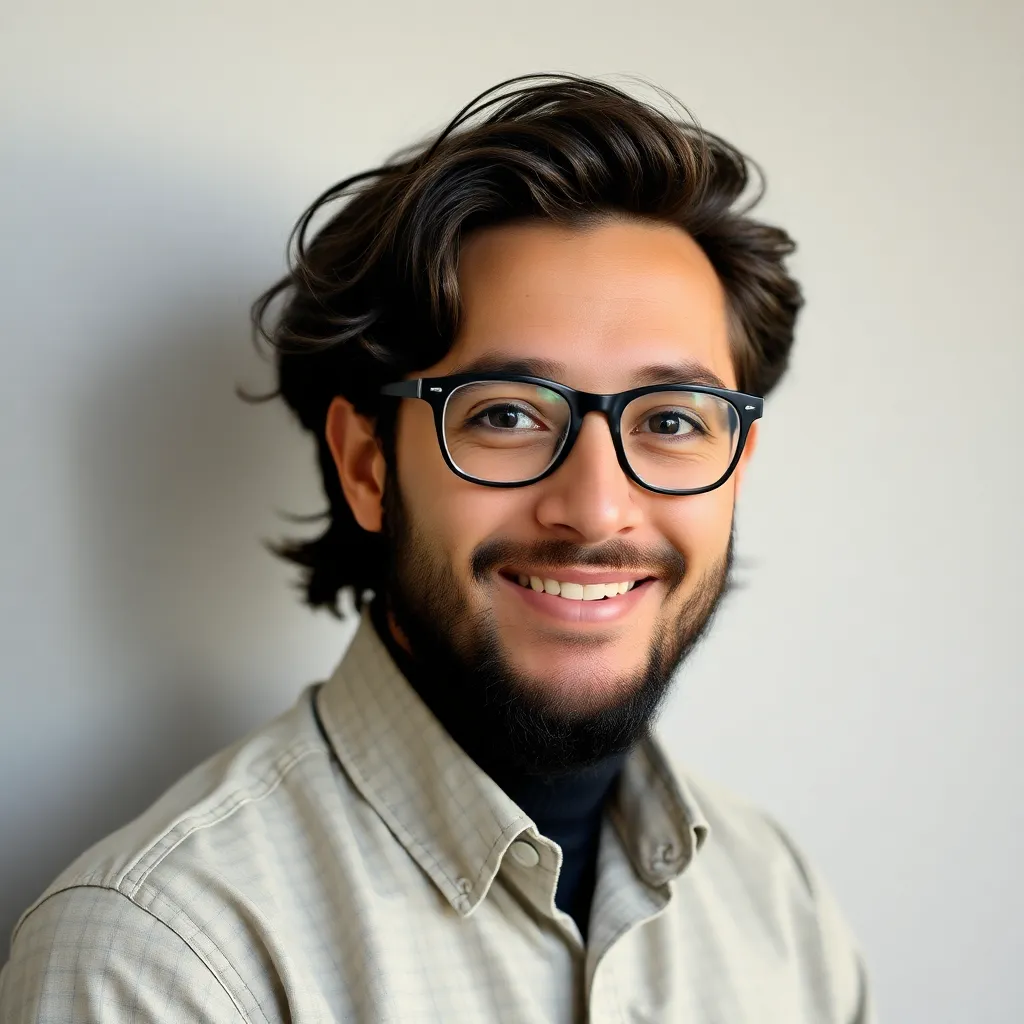
Holbox
Apr 05, 2025 · 6 min read

Table of Contents
- Steam Enters A Nozzle At 400
- Table of Contents
- Steam Enters a Nozzle at 400: A Deep Dive into Nozzle Flow Analysis
- Understanding Nozzle Flow Fundamentals
- 1. Initial Conditions: Pressure, Temperature, and Velocity
- 2. Nozzle Geometry: Converging, Diverging, and Converging-Diverging
- 3. Isentropic vs. Real Flow
- Analyzing Steam Flow through a Nozzle: A Thermodynamic Approach
- 1. Steady-Flow Energy Equation
- 2. Steam Property Relations
- 3. Determining the Final State of Steam
- Practical Applications and Considerations
- Advanced Considerations: CFD and Experimental Validation
- Conclusion
- Latest Posts
- Latest Posts
- Related Post
Steam Enters a Nozzle at 400: A Deep Dive into Nozzle Flow Analysis
The statement "steam enters a nozzle at 400" is incomplete without specifying the units (400 kPa? 400 °C? 400 m/s?). This ambiguity highlights the crucial role of precise initial conditions in analyzing nozzle flow. This article will explore the complexities of steam flow through a nozzle, covering various scenarios and employing thermodynamic principles to understand the expansion process. We'll examine different nozzle types, the impact of varying initial conditions, and the role of irreversibilities in determining the final steam state. We'll also delve into the practical applications of this analysis in various engineering fields.
Understanding Nozzle Flow Fundamentals
Nozzles are converging or converging-diverging ducts designed to accelerate a fluid, in this case, steam. The acceleration is achieved by converting the thermal energy of the steam into kinetic energy. This conversion is governed by the principles of thermodynamics and fluid mechanics. Several key factors influence the performance of a nozzle:
1. Initial Conditions: Pressure, Temperature, and Velocity
The initial state of the steam (pressure, temperature, and velocity) at the nozzle inlet significantly impacts the subsequent expansion process. A higher initial pressure generally leads to higher exit velocity, assuming other parameters remain constant. The initial temperature also plays a crucial role, as it dictates the steam's enthalpy and specific volume. The initial velocity affects the overall energy balance and the final exit velocity.
2. Nozzle Geometry: Converging, Diverging, and Converging-Diverging
-
Converging Nozzles: These nozzles have a decreasing cross-sectional area along the flow path. They are suitable for subsonic flow, where the steam accelerates as it passes through the narrowing passage.
-
Diverging Nozzles: These nozzles have an increasing cross-sectional area. They are generally used for supersonic flow, where the steam expands and decelerates while maintaining supersonic speeds.
-
Converging-Diverging Nozzles (de Laval Nozzles): These nozzles combine converging and diverging sections. They're designed to accelerate the steam to supersonic velocities. The converging section accelerates the steam to sonic velocity (Mach 1) at the throat, and the diverging section further accelerates the flow to supersonic speeds. These are commonly used in steam turbines and rocket engines.
3. Isentropic vs. Real Flow
-
Isentropic Flow: This idealized case assumes adiabatic and reversible expansion. There are no heat losses or internal friction. Isentropic flow analysis provides a benchmark for comparison with real-world scenarios. It simplifies calculations, using equations derived from the conservation of mass, energy, and momentum.
-
Real Flow: Real nozzle flow deviates from the isentropic ideal due to several irreversibilities:
-
Friction: Friction between the steam and the nozzle walls causes energy loss, leading to a lower exit velocity than predicted by isentropic analysis.
-
Heat Transfer: Heat transfer between the steam and the surroundings also affects the expansion process, influencing the final temperature and velocity.
-
Shock Waves: In supersonic flow, shock waves can form, causing abrupt changes in pressure, temperature, and velocity. These shock waves represent significant energy losses.
-
Analyzing Steam Flow through a Nozzle: A Thermodynamic Approach
Analyzing steam flow requires applying the principles of thermodynamics. We'll focus on the steady-flow energy equation and the property relations for steam.
1. Steady-Flow Energy Equation
For a steady-flow process through a nozzle, the steady-flow energy equation can be expressed as:
h₁ + (V₁²/2) + gz₁ = h₂ + (V₂²/2) + gz₂ + W
where:
h₁
andh₂
are the specific enthalpies at the inlet and outlet, respectively.V₁
andV₂
are the velocities at the inlet and outlet, respectively.z₁
andz₂
are the elevations at the inlet and outlet, respectively.W
represents work done, which is usually negligible in a nozzle.g
is the acceleration due to gravity.
2. Steam Property Relations
Steam properties (enthalpy, entropy, specific volume) are crucial for accurately predicting its behavior in a nozzle. These properties are typically obtained from steam tables or using specialized software. The steam's state (saturated, superheated, or wet) significantly influences the calculations.
3. Determining the Final State of Steam
To determine the final state of the steam at the nozzle exit, we need to consider the following:
-
Initial Conditions: As mentioned earlier, the inlet pressure, temperature, and velocity are critical. For example, if steam enters at 400 kPa and 200°C, we need to determine its specific enthalpy and specific volume from steam tables.
-
Nozzle Efficiency: The nozzle efficiency accounts for irreversibilities. It's defined as the ratio of the actual kinetic energy gain to the isentropic kinetic energy gain. The lower the efficiency, the greater the losses due to friction and heat transfer.
-
Type of Nozzle: The type of nozzle (converging, diverging, or converging-diverging) significantly impacts the final velocity and pressure.
-
Back Pressure: The pressure at the nozzle exit (back pressure) plays a crucial role in determining the flow regime (subsonic or supersonic). If the back pressure is too high, the flow might become choked, limiting the mass flow rate.
Practical Applications and Considerations
The analysis of steam flow through nozzles has wide-ranging applications across various engineering disciplines:
-
Steam Turbines: Nozzles are integral components of steam turbines, accelerating steam to high velocities before it strikes the turbine blades, generating power.
-
Rocket Propulsion: In rocket engines, nozzles accelerate hot gases to supersonic speeds, generating thrust.
-
Power Generation: Steam nozzles are vital in power plants, converting the thermal energy of steam into mechanical energy for electricity generation.
-
Chemical Processing: Nozzles are used in various chemical processes, such as spraying liquids and atomizing fluids.
Advanced Considerations: CFD and Experimental Validation
Advanced computational fluid dynamics (CFD) simulations can provide detailed insights into complex nozzle flow phenomena, including the formation of shock waves and boundary layer effects. These simulations can handle intricate nozzle geometries and non-isentropic flow conditions. However, CFD results should be validated through experimental measurements. Experimental data provides a crucial benchmark for assessing the accuracy of CFD models and ensuring reliable predictions.
Conclusion
Analyzing steam flow through a nozzle involves applying fundamental thermodynamic and fluid mechanics principles. The initial conditions, nozzle geometry, and the presence of irreversibilities all play critical roles in determining the final steam state. Accurate analysis requires considering isentropic and real flow conditions and using appropriate steam property data. By understanding these concepts, engineers can design and optimize nozzles for various applications, maximizing efficiency and performance. This detailed analysis, coupled with advanced numerical techniques like CFD, provides a powerful toolkit for solving complex nozzle flow problems across diverse engineering fields. Remember, the statement "steam enters a nozzle at 400" requires further clarification to initiate a meaningful analysis. Always ensure that all initial conditions are precisely defined before embarking on any calculations.
Latest Posts
Latest Posts
-
The Ministry Of Misallocation Has Decreed
Apr 09, 2025
-
The Polaris Company Uses A Job Order
Apr 09, 2025
-
The Effectiveness Of Direct Mail Advertising Suffers From
Apr 09, 2025
-
Presidential Candidates In The 1960s Compared With Today
Apr 09, 2025
-
Art Labeling Activity Levels Of Protein Structure Answer Key
Apr 09, 2025
Related Post
Thank you for visiting our website which covers about Steam Enters A Nozzle At 400 . We hope the information provided has been useful to you. Feel free to contact us if you have any questions or need further assistance. See you next time and don't miss to bookmark.