Sierra Company Manufactures Soccer Balls In Two Sequential Processes
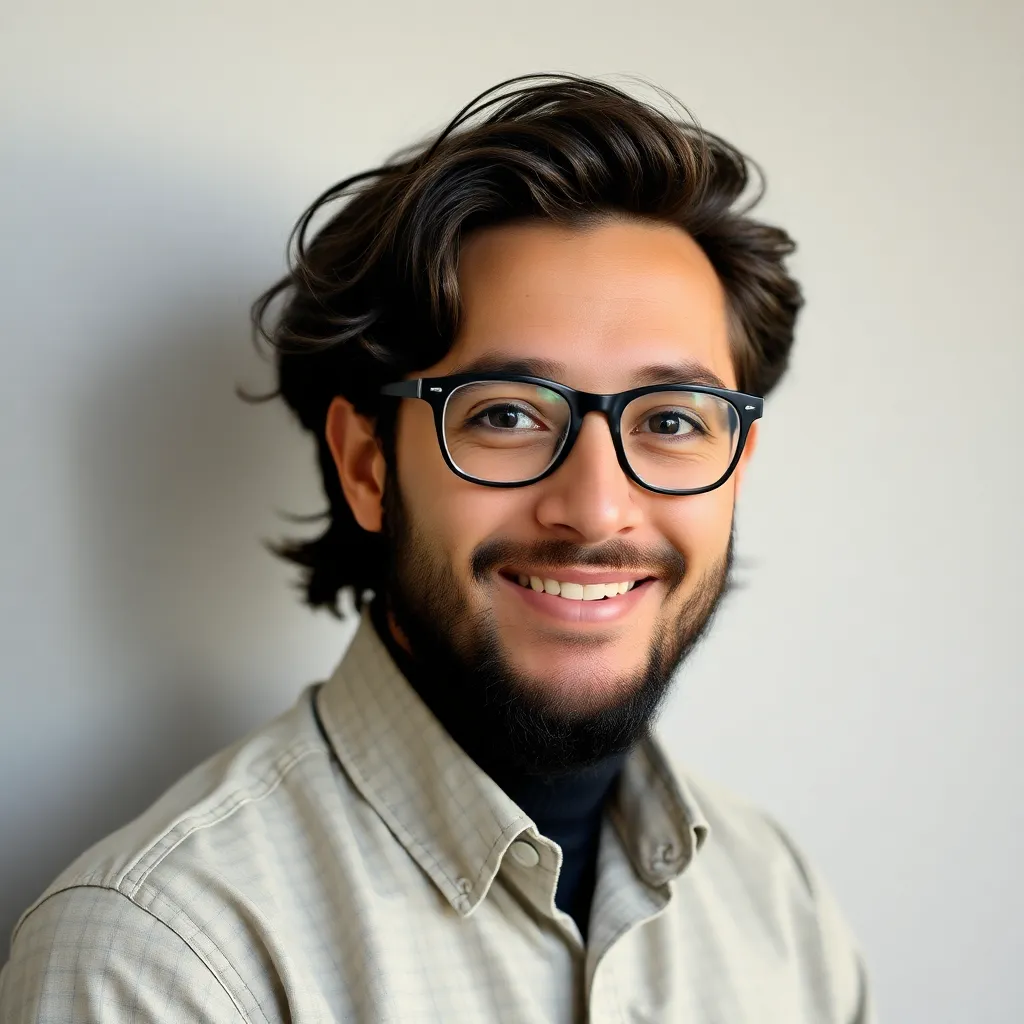
Holbox
Mar 28, 2025 · 6 min read
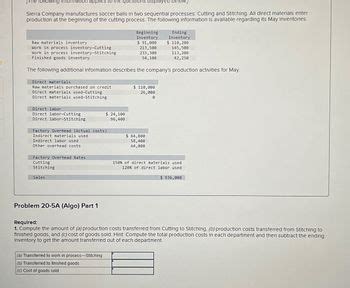
Table of Contents
- Sierra Company Manufactures Soccer Balls In Two Sequential Processes
- Table of Contents
- Sierra Company: Optimizing Soccer Ball Production Across Two Sequential Processes
- Stage 1: Cutting and Stitching – Precision and Efficiency
- 1.1 Material Procurement and Quality Control:
- 1.2 Pattern Cutting and Preparation:
- 1.3 Panel Stitching:
- 1.4 Initial Quality Check:
- Stage 2: Finishing and Inspection – Ensuring Perfection
- 2.1 Bladder Insertion and Inflation:
- 2.2 Surface Finishing:
- 2.3 Final Quality Control and Inspection:
- 2.4 Packaging and Distribution:
- Potential Bottlenecks and Improvement Strategies
- 2.1 Stitching Machine Capacity:
- 2.2 Quality Control Delays:
- 2.3 Bladder Insertion Issues:
- 2.4 Materials Handling and Logistics:
- Implementing Lean Manufacturing Principles
- Technology Integration for Enhanced Efficiency
- Conclusion: A Path to Optimized Soccer Ball Production
- Latest Posts
- Latest Posts
- Related Post
Sierra Company: Optimizing Soccer Ball Production Across Two Sequential Processes
Sierra Company, a leading manufacturer of soccer balls, prides itself on delivering high-quality products to its customers worldwide. Their production process involves two sequential stages: cutting and stitching, and finishing and inspection. Understanding the intricacies of this dual-process system is crucial to optimizing efficiency, minimizing costs, and maximizing output. This detailed analysis explores each stage, identifies potential bottlenecks, and proposes strategies for improvement.
Stage 1: Cutting and Stitching – Precision and Efficiency
The first stage, cutting and stitching, is arguably the most crucial. This process involves several key steps:
1.1 Material Procurement and Quality Control:
Sierra Company's commitment to quality begins with the selection of raw materials. High-quality leather or synthetic materials are carefully sourced, ensuring consistent texture, durability, and color. Rigorous quality control checks are implemented at this early stage to minimize defects and prevent costly rework later in the process. This includes checking for inconsistencies in material thickness, blemishes, and color variations. Advanced material inspection technologies, such as automated optical inspection systems, could further enhance efficiency and accuracy at this crucial step.
1.2 Pattern Cutting and Preparation:
Precise pattern cutting is essential for creating panels that perfectly fit together. Sierra uses advanced cutting machines, potentially CNC (Computer Numerical Control) cutters, which ensure accuracy and consistency. These machines are programmed with precise patterns based on the specific soccer ball design. Minimizing material waste is a key objective here, and optimizing the cutting patterns through advanced software can significantly reduce costs and improve resource utilization.
1.3 Panel Stitching:
This stage involves meticulously stitching together the individual leather or synthetic panels to form the soccer ball's spherical shape. The stitching must be strong and consistent to withstand the rigors of gameplay. This often involves specialized stitching machines capable of handling the material's thickness and texture. The choice of thread, its strength and durability, is another critical factor affecting the final product quality. Regular maintenance and calibration of stitching machines is paramount to maintaining the quality and speed of this critical process.
1.4 Initial Quality Check:
After stitching, a preliminary quality check is performed. Inspectors carefully examine the soccer balls for any stitching flaws, uneven seams, or panel misalignments. This early detection of defects helps prevent further processing of flawed products, reducing waste and improving overall efficiency. Implementing advanced image processing techniques combined with AI-powered defect detection systems can potentially automate and improve this phase.
Stage 2: Finishing and Inspection – Ensuring Perfection
The second stage, finishing and inspection, focuses on preparing the soccer balls for packaging and distribution.
2.1 Bladder Insertion and Inflation:
This involves carefully inserting the inner bladder into the stitched soccer ball shell. The bladder, typically made of butyl rubber, needs to be correctly positioned to ensure proper inflation and retention of air. Automated bladder insertion systems can enhance speed and consistency, reducing the risk of human error and ensuring consistent inflation. Proper inflation pressure is critical for the ball’s performance and needs careful control.
2.2 Surface Finishing:
This step involves any necessary surface treatments, like coating or polishing, to improve the ball’s durability, waterproofness, and aesthetic appeal. The type of treatment depends on the materials used and the desired level of performance. For high-end soccer balls, specialized coatings might be applied to enhance durability and water resistance. Automation in this area could involve robotic systems capable of applying coatings evenly and consistently across the soccer ball's surface.
2.3 Final Quality Control and Inspection:
A rigorous final quality control inspection is paramount. Inspectors meticulously examine the finished soccer balls for any defects, inconsistencies, or imperfections in the overall structure, stitching, bladder integrity, and surface finish. Automated systems can leverage computer vision and other advanced technologies to enhance the accuracy and speed of this process. Defective balls are removed, and the process continually refined based on the data collected from the inspection.
2.4 Packaging and Distribution:
Once the final inspection is complete, the soccer balls are carefully packaged for shipping and distribution. This includes appropriate labeling, protection during transit, and adherence to all relevant regulations. Optimized packaging design can minimize shipping costs and reduce damage during transport. Efficient warehouse management systems are crucial to ensure timely and accurate order fulfillment.
Potential Bottlenecks and Improvement Strategies
Several potential bottlenecks can affect the efficiency of Sierra Company’s production process. Identifying and addressing these is crucial for optimizing overall output.
2.1 Stitching Machine Capacity:
Inefficient stitching machines can create a bottleneck in the first stage. Upgrading to faster, more reliable machines, or optimizing stitching processes, can significantly increase throughput. Investing in preventative maintenance programs for stitching machines is key to minimize downtime and increase productivity.
2.2 Quality Control Delays:
Slow or inefficient quality control procedures can delay the entire process. Implementing automated inspection systems can speed up this phase, and improving training for quality control personnel can improve accuracy and efficiency.
2.3 Bladder Insertion Issues:
Problems with bladder insertion can cause significant delays. Introducing automated bladder insertion systems can help improve consistency and speed. Careful selection and consistent quality of the bladder itself are also critical.
2.4 Materials Handling and Logistics:
Inefficient materials handling and logistics can lead to delays and increased costs. Implementing lean manufacturing principles and streamlining materials flow can significantly improve efficiency. Utilizing advanced inventory management systems ensures timely procurement and reduces stockouts.
Implementing Lean Manufacturing Principles
Adopting lean manufacturing principles can significantly improve efficiency and reduce waste in Sierra Company's production process. This involves:
- Value Stream Mapping: Creating a visual map of the entire production process to identify areas of waste and inefficiency.
- Kaizen Events: Organizing short, focused events to identify and implement rapid improvements in specific areas of the production process.
- 5S Methodology: Organizing the workspace to improve efficiency and reduce waste (Sort, Set in Order, Shine, Standardize, Sustain).
- Just-in-Time Inventory: Minimizing inventory levels to reduce storage costs and improve efficiency.
- Continuous Improvement (Kaizen): Adopting a culture of continuous improvement where employees are empowered to identify and implement improvements.
Technology Integration for Enhanced Efficiency
Investing in advanced technologies can significantly enhance Sierra Company's production process. This includes:
- Automated Cutting Machines: CNC cutting machines offer precision and efficiency in cutting leather or synthetic panels.
- Automated Stitching Machines: Faster and more reliable stitching machines can significantly increase output.
- Automated Bladder Insertion Systems: Reduce the risk of human error and improve consistency.
- Automated Inspection Systems: Improve accuracy and speed of quality control processes.
- Data Analytics and Predictive Maintenance: Utilize data to predict potential equipment failures and schedule maintenance proactively, minimizing downtime.
Conclusion: A Path to Optimized Soccer Ball Production
Sierra Company's success depends on its ability to efficiently produce high-quality soccer balls. By carefully analyzing its two-stage production process, identifying potential bottlenecks, and implementing lean manufacturing principles and advanced technologies, Sierra can optimize its operations, reduce costs, and meet growing customer demand. A commitment to continuous improvement, employee training, and technological innovation will ensure Sierra Company remains a leading manufacturer in the global soccer ball market. The integration of data analytics and predictive maintenance offers a significant opportunity for proactive problem-solving and the optimization of resource utilization, furthering the company's overall efficiency and competitiveness. By embracing these strategies, Sierra can solidify its position as a global leader, producing high-quality soccer balls with unmatched efficiency and precision.
Latest Posts
Latest Posts
-
One Violent Incident Within A Relationship Qualifies As Domestic Violence
Apr 01, 2025
-
Select All The Statements About Symbolist Literature
Apr 01, 2025
-
A Companys Rites And Rituals Might Include
Apr 01, 2025
-
Drag The Labels To Steps And Products In Spermatogenesis
Apr 01, 2025
-
What Is The Voltage Across A Membrane Called
Apr 01, 2025
Related Post
Thank you for visiting our website which covers about Sierra Company Manufactures Soccer Balls In Two Sequential Processes . We hope the information provided has been useful to you. Feel free to contact us if you have any questions or need further assistance. See you next time and don't miss to bookmark.