Serial Problem Business Solutions Lo P3
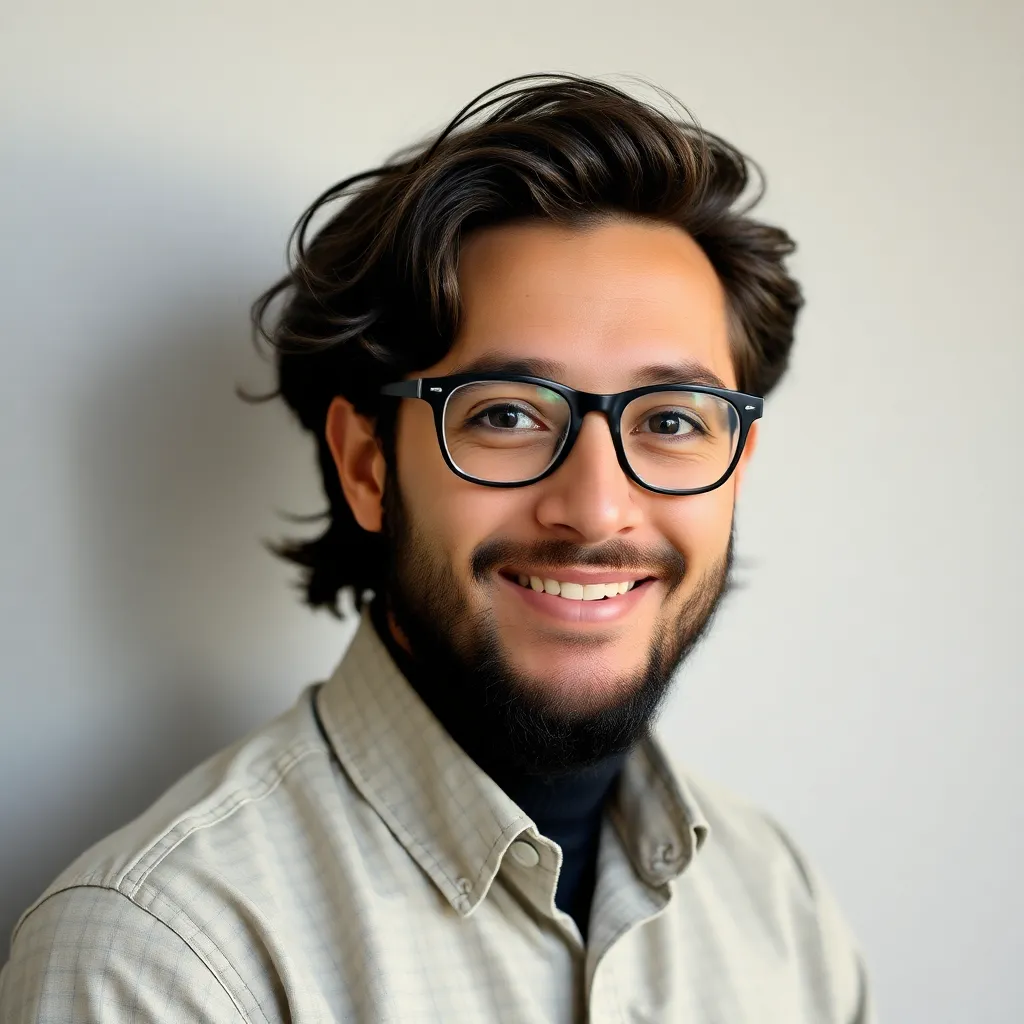
Holbox
Apr 10, 2025 · 6 min read
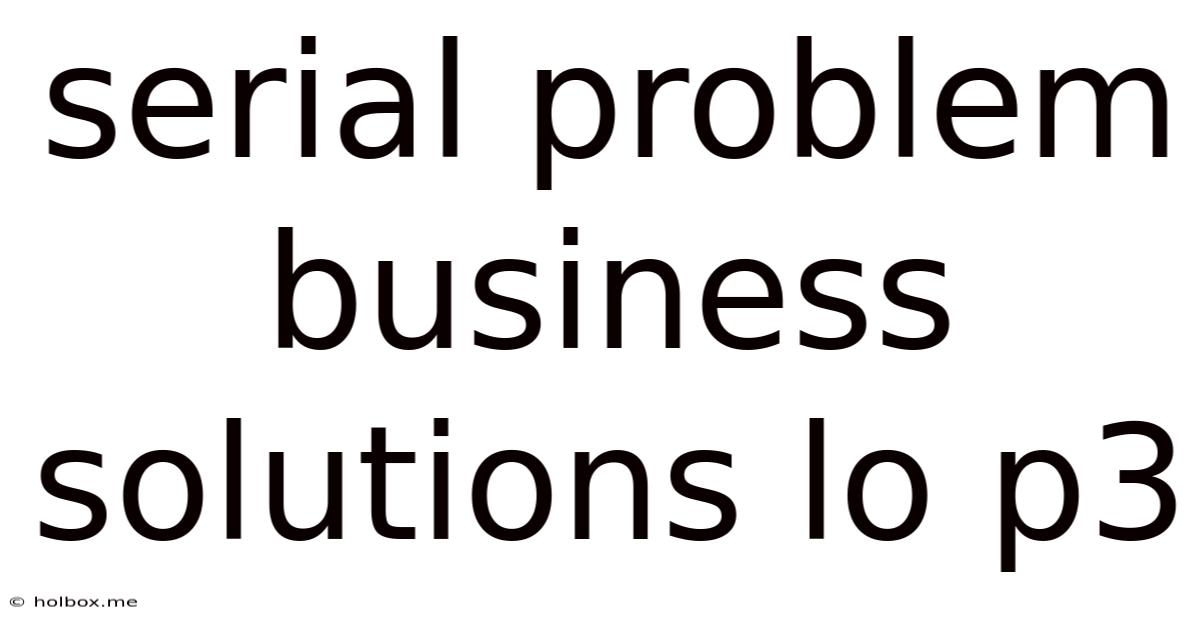
Table of Contents
- Serial Problem Business Solutions Lo P3
- Table of Contents
- Serial Problem Business Solutions: Lo P3 & Beyond
- Understanding the Nature of Serial Problems
- Deconstructing "Lo P3": A Hypothetical Case Study
- A Comprehensive Framework for Solving Serial Problems: The 5-Step Approach
- Step 1: Identification and Documentation
- Step 2: Root Cause Analysis
- Step 3: Solution Development and Prioritization
- Step 4: Implementation and Monitoring
- Step 5: Continuous Improvement and Prevention
- Applying the Framework to "Lo P3" Examples
- Conclusion: Sustainable Solutions for Serial Problems
- Latest Posts
- Latest Posts
- Related Post
Serial Problem Business Solutions: Lo P3 & Beyond
Serial problems in business represent a recurring challenge that significantly impacts profitability, efficiency, and overall success. These are issues that appear repeatedly, often stemming from deeper, underlying root causes rather than isolated incidents. Understanding and addressing these serial problems effectively is crucial for sustainable growth. This article delves into the complexities of serial problems, focusing specifically on "Lo P3" (a hypothetical example representing a common category of low-priority, persistently recurring problems) and offering a comprehensive framework for sustainable solutions.
Understanding the Nature of Serial Problems
Before tackling "Lo P3" specifically, it's important to grasp the general characteristics of serial problems in a business context. These problems are not merely isolated incidents; they exhibit several key features:
- Repetition: The defining characteristic is their recurring nature. They don't simply disappear after a single fix.
- Low Visibility: Often, they are not immediately glaring, appearing as minor inconveniences rather than major crises. This makes them easy to overlook or dismiss.
- Cumulative Impact: While individually insignificant, their cumulative effect over time can be substantial, leading to significant losses in productivity, resources, and morale.
- Root Cause Complexity: They frequently stem from interconnected factors, making diagnosis and resolution more challenging. Addressing surface-level symptoms without tackling the root cause leads to the problem reappearing.
- Systemic Issues: Serial problems often indicate flaws in business processes, systems, or organizational structures.
Deconstructing "Lo P3": A Hypothetical Case Study
Let's consider "Lo P3," a hypothetical category representing low-priority, persistently recurring problems. These might include:
- Minor equipment malfunctions: Frequent paper jams in printers, intermittent internet connectivity issues, or software glitches requiring minor troubleshooting.
- Recurring administrative tasks: Repeated data entry errors, inefficient filing systems leading to lost documents, or poorly defined processes resulting in duplicated efforts.
- Communication breakdowns: Missed deadlines due to unclear communication, inconsistent messaging between departments, or a lack of feedback mechanisms.
- Small-scale customer service issues: Repeated inquiries about the same product or service, minor billing discrepancies, or difficulties with online order tracking.
While seemingly minor individually, these "Lo P3" problems collectively drain resources, frustrate employees, and diminish customer satisfaction.
A Comprehensive Framework for Solving Serial Problems: The 5-Step Approach
Addressing serial problems effectively requires a structured approach. The following 5-step framework can be applied to "Lo P3" problems and other recurring issues:
Step 1: Identification and Documentation
This crucial first step involves systematically identifying and documenting all instances of "Lo P3" problems. This might involve:
- Data Collection: Implement tracking mechanisms (spreadsheets, databases, dedicated software) to record every occurrence of the problem, including date, time, nature of the problem, and impact.
- Employee Input: Conduct surveys, interviews, or brainstorming sessions to gather insights from employees who directly encounter these problems. Encourage open communication.
- Customer Feedback Analysis: Analyze customer feedback channels (surveys, reviews, support tickets) to identify recurring issues from the customer perspective.
Keyword Optimization: serial problem identification, problem tracking, data collection methods, employee feedback, customer feedback analysis
Step 2: Root Cause Analysis
Once the problem is clearly defined and documented, the next step is to identify its underlying root cause. This may involve using techniques such as:
- 5 Whys: Repeatedly asking "Why?" to uncover the underlying cause of the problem.
- Fishbone Diagram (Ishikawa Diagram): A visual tool to identify potential causes categorized by category (people, methods, materials, machines, environment, measurement).
- Pareto Analysis: Identifying the 20% of causes that account for 80% of the problems.
Keyword Optimization: root cause analysis, 5 whys, fishbone diagram, ishikawa diagram, pareto analysis, problem solving techniques
Step 3: Solution Development and Prioritization
Based on the root cause analysis, develop potential solutions. Prioritize solutions based on factors like:
- Impact: Solutions that address problems with the greatest impact should be prioritized.
- Feasibility: Consider the resources, time, and expertise required for implementation.
- Cost-effectiveness: Evaluate the cost of implementation against the potential benefits.
Keyword Optimization: solution development, solution prioritization, cost-benefit analysis, resource allocation, implementation planning
Step 4: Implementation and Monitoring
Implement the chosen solution(s), carefully monitoring their effectiveness. This involves:
- Pilot Testing: Test the solution on a small scale before full implementation.
- Regular Monitoring: Track key metrics to assess the impact of the solution on the frequency and severity of the problem.
- Adjustments: Be prepared to make adjustments based on monitoring results.
Keyword Optimization: solution implementation, pilot testing, monitoring effectiveness, performance metrics, process improvement
Step 5: Continuous Improvement and Prevention
Once a solution is implemented, focus on preventing future occurrences. This might involve:
- Process Improvement: Refine existing processes to minimize the likelihood of the problem recurring.
- Employee Training: Provide training to employees on best practices to prevent the problem.
- Technological Solutions: Consider implementing technology to automate tasks or improve efficiency.
- Regular Review: Regularly review the effectiveness of implemented solutions and make further improvements as needed.
Keyword Optimization: continuous improvement, process optimization, employee training, technology solutions, preventative maintenance
Applying the Framework to "Lo P3" Examples
Let's illustrate how this framework can be applied to some of the "Lo P3" examples:
Example 1: Frequent Paper Jams in Printers:
- Identification: Track the frequency, time of day, and type of paper causing the jams.
- Root Cause: Could be low-quality paper, incorrect paper loading, or a malfunctioning printer component.
- Solution: Purchase higher-quality paper, provide training on proper paper loading, or schedule printer maintenance.
- Implementation: Monitor the number of paper jams after implementing the solution.
- Prevention: Establish a regular printer maintenance schedule.
Example 2: Recurring Data Entry Errors:
- Identification: Track the types of errors, the employees making them, and the time of day they occur.
- Root Cause: Could be inadequate training, poor data entry procedures, or a cumbersome data entry system.
- Solution: Provide additional training, revise data entry procedures to be more user-friendly, or implement data validation tools.
- Implementation: Monitor the error rate after implementing the solution.
- Prevention: Implement a system of regular data checks and audits.
Conclusion: Sustainable Solutions for Serial Problems
Serial problems, even those seemingly insignificant like "Lo P3," pose a significant threat to business efficiency and profitability. By adopting a systematic approach to identification, root cause analysis, solution development, implementation, and continuous improvement, businesses can effectively tackle these recurring issues and build a more robust and resilient operational environment. The framework outlined above provides a practical roadmap for achieving sustainable solutions and minimizing the negative impacts of serial problems on business performance. Remember that proactive problem-solving is key to long-term success. Consistent monitoring and adapting to evolving situations will ensure that the solutions remain effective and that new problems are addressed promptly. Prioritizing the identification and resolution of serial problems is a strategic investment that pays off significantly in improved efficiency, reduced costs, and enhanced customer satisfaction.
Latest Posts
Latest Posts
-
Essential Environment The Science Behind The Stories
May 02, 2025
-
Draw One Enantiomer Of The Major Product
May 02, 2025
-
Count The Significant Digits In Each Of These Measurements
May 02, 2025
-
The Muscles That Extend The Forearm Are Located
May 02, 2025
-
Whats Your Learning Style Is An Appropriately Worded
May 02, 2025
Related Post
Thank you for visiting our website which covers about Serial Problem Business Solutions Lo P3 . We hope the information provided has been useful to you. Feel free to contact us if you have any questions or need further assistance. See you next time and don't miss to bookmark.