Select The Best Definition Of Quality Control.
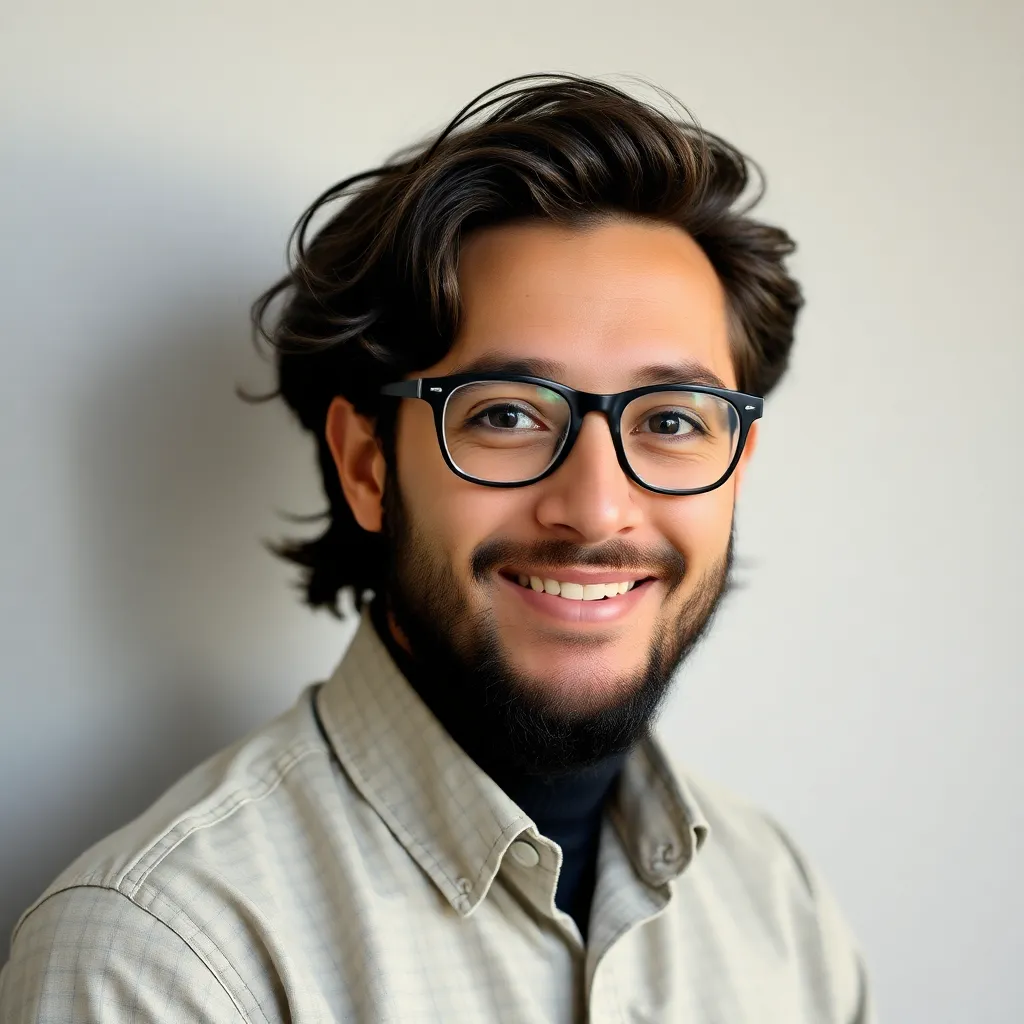
Holbox
May 13, 2025 · 6 min read
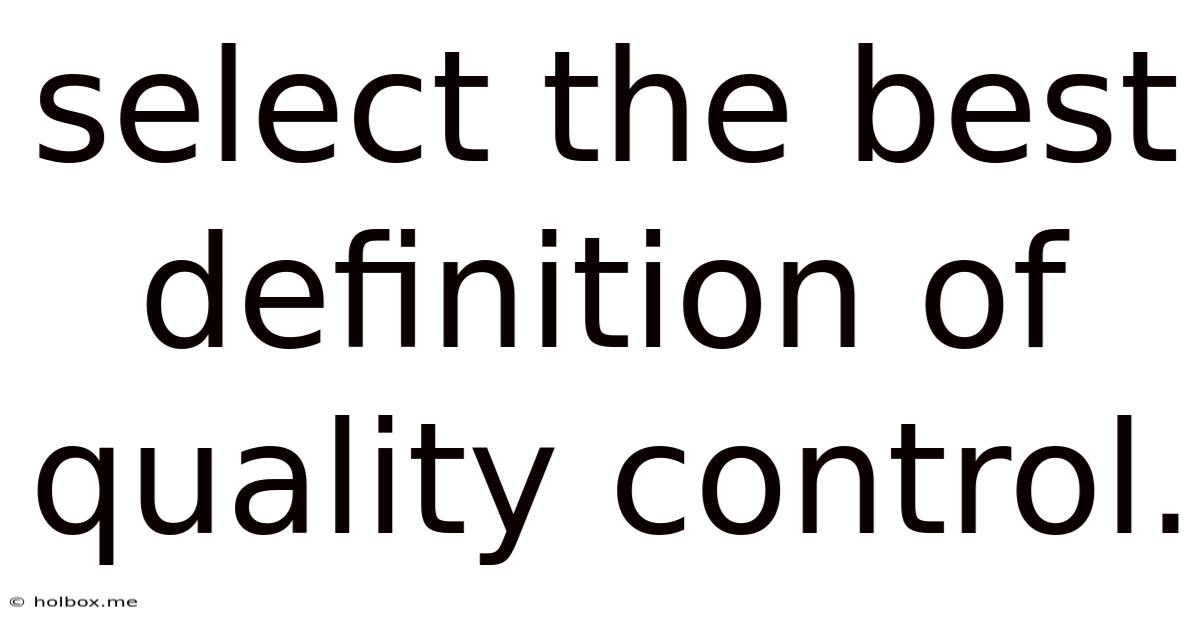
Table of Contents
- Select The Best Definition Of Quality Control.
- Table of Contents
- Selecting the Best Definition of Quality Control
- Defining Quality Control: A Multifaceted Perspective
- Analyzing the Strengths and Weaknesses
- Selecting the Best Definition
- Implementing Effective Quality Control: Key Strategies
- 1. Define Clear Quality Standards
- 2. Implement Preventative Measures
- 3. Monitor and Measure Quality
- 4. Implement Corrective and Preventative Actions
- 5. Continuous Improvement
- Conclusion: Quality Control – The Cornerstone of Business Success
- Latest Posts
- Latest Posts
- Related Post
Selecting the Best Definition of Quality Control
Quality control (QC) is a multifaceted process crucial for any organization aiming for consistent product or service excellence. While a simple definition might suffice for everyday conversation, a comprehensive understanding requires delving deeper into its nuances and various interpretations. This article explores multiple definitions of quality control, analyzes their strengths and weaknesses, and ultimately selects the best definition based on its comprehensiveness and applicability across diverse industries.
Defining Quality Control: A Multifaceted Perspective
Before selecting the best definition, let's examine several common interpretations of quality control:
Definition 1: The process of inspecting finished products to ensure they meet pre-defined standards. This definition is simplistic, focusing solely on the end-product inspection. It overlooks the crucial preventative measures that form a substantial part of effective quality control. While inspection is a component of QC, relying solely on it is reactive and inefficient. Defects detected at the end of the production line are costly to rectify, often leading to waste and customer dissatisfaction.
Definition 2: A systematic process of monitoring and measuring quality throughout the production process to identify and correct deviations from standards. This is a more comprehensive definition, acknowledging the importance of continuous monitoring and proactive measures. It highlights the iterative nature of QC, emphasizing the continuous improvement aspect. However, it still lacks the scope to fully encompass the managerial and strategic elements often integrated into modern QC systems.
Definition 3: The process of ensuring that products or services consistently meet customer requirements and expectations. This customer-centric definition emphasizes the ultimate goal of QC: customer satisfaction. By focusing on fulfilling customer needs, this definition steers the process towards proactive problem-solving and continuous improvement driven by customer feedback. However, it may lack sufficient detail on the how of achieving this customer satisfaction.
Definition 4: A set of activities designed to prevent defects, identify and correct errors, and improve overall product or service quality. This definition incorporates the preventative aspects of QC, acknowledging the importance of proactive measures to minimize defects. It explicitly includes error correction and the broader goal of continuous quality improvement. This is a significant step towards a more complete understanding of QC.
Definition 5: A management system encompassing planning, implementation, monitoring, analysis, and improvement of processes to ensure consistent quality of products or services, meeting both internal and external customer requirements. This definition, while lengthy, is arguably the most comprehensive. It positions QC as a holistic management system, emphasizing proactive planning, continuous monitoring, data analysis, and iterative improvement. It acknowledges the importance of meeting both internal (e.g., employee satisfaction) and external (e.g., customer satisfaction) requirements, making it particularly robust and adaptable.
Analyzing the Strengths and Weaknesses
Let's analyze the strengths and weaknesses of each definition:
Definition | Strengths | Weaknesses |
---|---|---|
1 | Simple and easy to understand | Overly simplistic; focuses only on end-product inspection; reactive approach |
2 | Acknowledges continuous monitoring and proactive measures | Lacks scope regarding managerial and strategic elements; less focus on customer needs |
3 | Customer-centric; emphasizes customer satisfaction | Lacks detail on the methods and processes involved; may not encompass all quality aspects |
4 | Includes preventative measures, error correction, and continuous improvement | Less emphasis on the managerial aspects and systematic approach |
5 | Comprehensive; holistic management system; includes all key aspects | More complex; may be challenging to grasp initially |
Selecting the Best Definition
Based on our analysis, Definition 5 – "A management system encompassing planning, implementation, monitoring, analysis, and improvement of processes to ensure consistent quality of products or services, meeting both internal and external customer requirements" – is the best definition of quality control.
This definition is superior because:
-
Holistic Approach: It views QC not merely as a set of activities but as a comprehensive management system. This perspective recognizes the interconnectedness of different processes and the importance of strategic planning.
-
Proactive and Reactive Measures: It encompasses both preventative measures (planning, implementation) and reactive measures (monitoring, analysis, improvement). This balance ensures both efficiency and responsiveness.
-
Continuous Improvement: The emphasis on continuous improvement fosters a culture of learning and adaptation, crucial for staying competitive in dynamic markets.
-
Customer Focus: The inclusion of both internal and external customer requirements underlines the importance of satisfying all stakeholders, leading to enhanced overall performance and reputation.
-
Data-Driven Decision Making: The emphasis on monitoring and analysis highlights the crucial role of data in identifying areas for improvement and making informed decisions.
Implementing Effective Quality Control: Key Strategies
Implementing a robust quality control system requires a strategic approach. Here are some key strategies:
1. Define Clear Quality Standards
Before initiating any QC process, it's crucial to define clear, measurable, achievable, relevant, and time-bound (SMART) quality standards. These standards should be aligned with both internal and external customer requirements. This involves establishing specific metrics for various aspects of the product or service, such as performance, functionality, reliability, and aesthetics. Clearly defined standards provide a benchmark against which actual performance can be measured.
2. Implement Preventative Measures
Preventative measures are crucial for minimizing defects and improving overall efficiency. This includes:
-
Process Design: Designing robust and efficient processes that minimize the potential for errors. This involves careful planning, risk assessment, and the use of appropriate tools and technologies.
-
Employee Training: Providing thorough training to employees on proper procedures and quality standards. Well-trained employees are less likely to make errors.
-
Regular Equipment Maintenance: Ensuring that equipment is regularly maintained and calibrated to prevent malfunctions and ensure consistent performance.
-
Supplier Management: Establishing strong relationships with suppliers and implementing stringent quality checks on incoming materials.
3. Monitor and Measure Quality
Continuous monitoring and measurement are essential for identifying deviations from standards and taking corrective actions. This can involve various techniques such as:
-
Statistical Process Control (SPC): Utilizing statistical methods to monitor process variability and identify potential problems before they escalate.
-
Regular Inspections: Conducting regular inspections of products or services at various stages of the production process.
-
Customer Feedback: Actively soliciting and analyzing customer feedback to identify areas for improvement.
-
Data Analysis: Employing data analysis techniques to identify trends and patterns in quality data, facilitating proactive problem-solving.
4. Implement Corrective and Preventative Actions
When deviations from standards are detected, immediate corrective actions must be taken to rectify the problem. Additionally, preventative actions should be implemented to prevent similar issues from recurring in the future. This involves root cause analysis, process improvement initiatives, and employee retraining.
5. Continuous Improvement
Quality control is not a one-time process; it's a continuous cycle of improvement. Regularly review and update quality standards, processes, and procedures to ensure they remain effective and aligned with evolving customer needs and market demands. Embracing continuous improvement principles, such as Kaizen or Six Sigma, can significantly enhance the effectiveness of the QC system.
Conclusion: Quality Control – The Cornerstone of Business Success
Selecting the right definition of quality control is the first step towards building a robust and effective quality management system. The best definition, as we've established, emphasizes a holistic management approach, encompassing preventative and reactive measures, continuous improvement, and a strong customer focus. By implementing the key strategies outlined above, organizations can create a culture of quality, leading to increased efficiency, reduced costs, enhanced customer satisfaction, and ultimately, sustainable business success. In today's competitive landscape, a commitment to quality is no longer a luxury – it's a necessity.
Latest Posts
Latest Posts
-
What Is 5 Percent Of 25
May 20, 2025
-
How Much Is 32 Oz In Litres
May 20, 2025
-
How Many Lbs Is 62 Kilos
May 20, 2025
-
How Many Gallons In 100 Liters
May 20, 2025
-
What Is 32 Kg In Pounds
May 20, 2025
Related Post
Thank you for visiting our website which covers about Select The Best Definition Of Quality Control. . We hope the information provided has been useful to you. Feel free to contact us if you have any questions or need further assistance. See you next time and don't miss to bookmark.