Schedule Of Cost Of Goods Manufactured
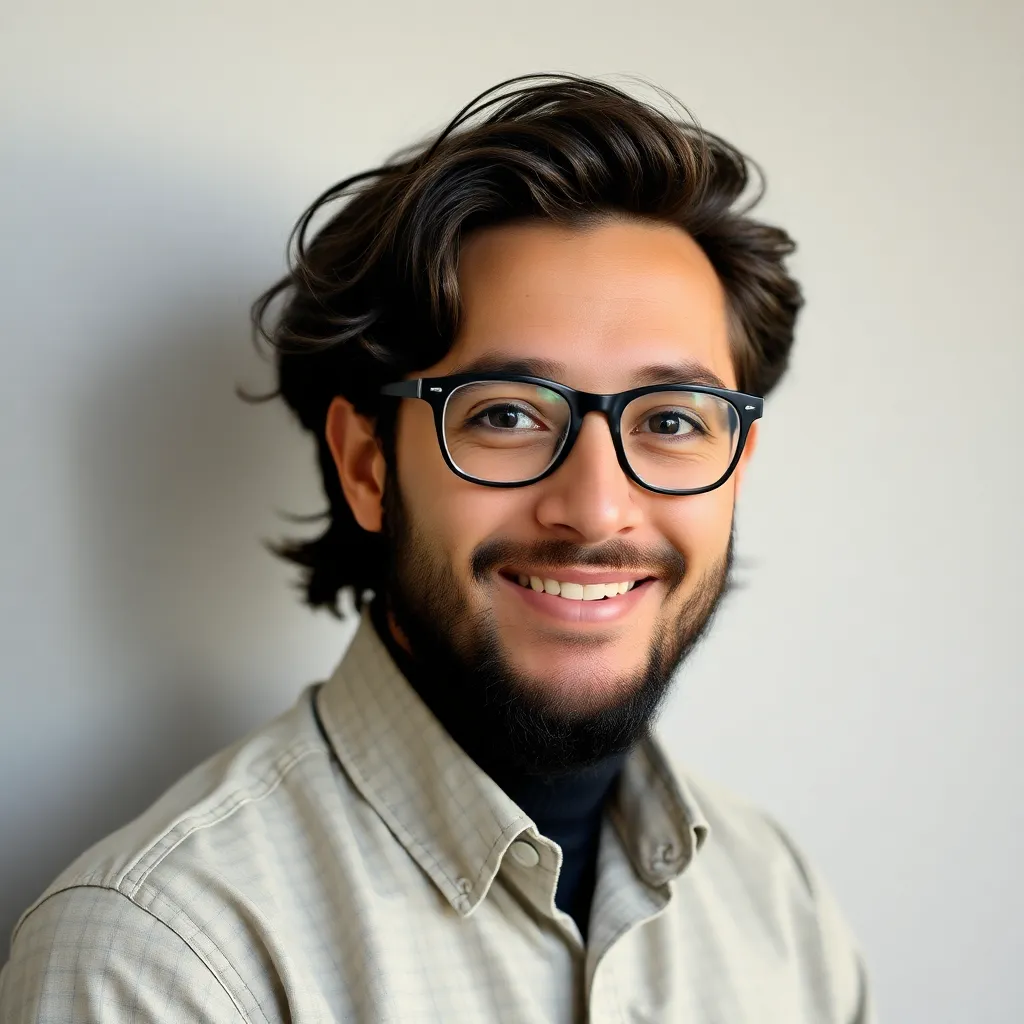
Holbox
Mar 30, 2025 · 7 min read
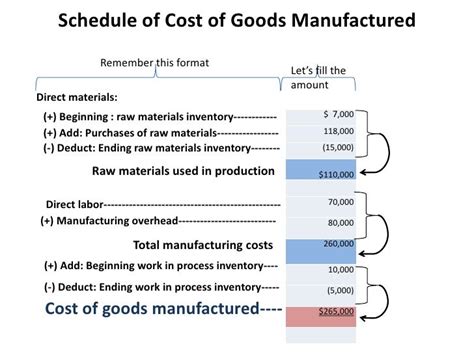
Table of Contents
- Schedule Of Cost Of Goods Manufactured
- Table of Contents
- Schedule of Cost of Goods Manufactured: A Comprehensive Guide
- Understanding the Components of the Schedule of Cost of Goods Manufactured
- 1. Direct Materials
- 2. Direct Labor
- 3. Manufacturing Overhead
- Calculating Cost of Goods Manufactured
- The Importance of the Schedule of Cost of Goods Manufactured
- Beyond the Basics: Advanced Considerations
- 1. Cost Accounting Systems: Job Order Costing vs. Process Costing
- 2. Joint Products and By-Products
- 3. Spoilage and Waste
- 4. Variances Analysis
- 5. Automation and Technology
- Using the COGM Schedule for Strategic Decision-Making
- Conclusion: The COGM Schedule – A Vital Business Tool
- Latest Posts
- Latest Posts
- Related Post
Schedule of Cost of Goods Manufactured: A Comprehensive Guide
The Schedule of Cost of Goods Manufactured (COGM) is a crucial internal accounting statement that details the costs involved in producing finished goods during a specific period. Unlike the cost of goods sold (COGS), which is reported on the income statement, the COGM schedule provides a granular breakdown of manufacturing costs, offering valuable insights for management decision-making and financial analysis. This comprehensive guide will delve into the intricacies of the COGM schedule, exploring its components, its importance, and practical applications.
Understanding the Components of the Schedule of Cost of Goods Manufactured
The COGM schedule meticulously tracks the flow of manufacturing costs, ultimately arriving at the total cost of goods manufactured during the accounting period. It systematically categorizes costs into three primary components:
1. Direct Materials
Direct materials represent the raw materials directly used in the production process. These are easily traceable to the finished goods and are a significant portion of the total manufacturing cost. Examples include:
- Raw materials: The basic materials used in production (e.g., wood for furniture, steel for automobiles, fabric for clothing).
- Packaging materials: Materials directly incorporated into the finished product packaging (e.g., boxes, labels, plastic wrapping).
- Freight-in: Transportation costs incurred to deliver raw materials to the manufacturing facility. Important Note: Freight-out, the cost of shipping finished goods to customers, is not included in COGM; it’s part of selling expenses.
2. Direct Labor
Direct labor encompasses the wages, salaries, and benefits paid to workers directly involved in the manufacturing process. This includes the time spent assembling, machining, or otherwise transforming raw materials into finished goods. It's crucial to distinguish between direct and indirect labor. Indirect labor, such as the salaries of supervisors or maintenance personnel, is included in manufacturing overhead.
3. Manufacturing Overhead
Manufacturing overhead represents all indirect costs associated with the production process. These costs are not easily traceable to specific products but are essential for the overall manufacturing operation. Key components of manufacturing overhead include:
- Indirect labor: Wages and benefits of employees not directly involved in production (e.g., supervisors, maintenance workers, quality control inspectors).
- Factory rent: Cost of leasing or owning the manufacturing facility.
- Utilities: Electricity, gas, water, and other utility costs related to the factory.
- Depreciation on factory equipment: Allocation of the cost of factory equipment over its useful life.
- Factory supplies: Consumable materials used in the manufacturing process (e.g., lubricants, cleaning supplies).
- Factory insurance: Insurance premiums covering the factory building and equipment.
- Property taxes: Taxes levied on the factory building and land.
Calculating Cost of Goods Manufactured
The calculation of the cost of goods manufactured involves several steps, systematically incorporating the three cost components mentioned above. A typical COGM schedule would look like this:
Schedule of Cost of Goods Manufactured
For the Year Ended [Date]
Item | Amount |
---|---|
Beginning Work in Process Inventory: | |
Direct Materials | $X |
Direct Labor | $Y |
Manufacturing Overhead | $Z |
Total Beginning WIP Inventory | $(X+Y+Z) |
Current Period Costs: | |
Direct Materials | $A |
Direct Labor | $B |
Manufacturing Overhead | $C |
Total Current Period Costs | $(A+B+C) |
Total Manufacturing Costs | $(X+Y+Z+A+B+C) |
Ending Work in Process Inventory | $(D) |
Cost of Goods Manufactured | $(X+Y+Z+A+B+C-D) |
Explanation:
- Beginning Work in Process (WIP) Inventory: This represents the cost of partially completed goods at the beginning of the accounting period.
- Current Period Costs: These are the direct materials, direct labor, and manufacturing overhead incurred during the current accounting period.
- Total Manufacturing Costs: This is the sum of beginning WIP inventory and current period costs.
- Ending Work in Process Inventory: This represents the cost of partially completed goods at the end of the accounting period.
- Cost of Goods Manufactured: This is the total cost of goods completed during the accounting period, ready for sale. It’s calculated by subtracting ending WIP inventory from total manufacturing costs.
The Importance of the Schedule of Cost of Goods Manufactured
The COGM schedule plays a vital role in several aspects of financial accounting and management:
- Accurate Costing: It provides a precise calculation of the cost of producing finished goods, facilitating accurate inventory valuation and cost accounting.
- Inventory Management: By tracking the flow of manufacturing costs, it helps optimize inventory levels, minimizing storage costs and preventing stockouts.
- Pricing Decisions: Understanding the true cost of production is crucial for setting competitive prices that ensure profitability.
- Performance Evaluation: The COGM schedule allows management to assess the efficiency of the manufacturing process, identifying areas for improvement and cost reduction.
- Financial Reporting: The COGM schedule is essential for preparing the income statement, where the cost of goods sold is a key component.
- Budgeting and Forecasting: It provides historical cost data that can be used to create accurate budgets and forecasts for future production.
- Internal Control: A detailed COGM schedule enhances internal controls by providing a clear audit trail of manufacturing costs.
Beyond the Basics: Advanced Considerations
While the basic COGM schedule provides a solid foundation, several advanced considerations can refine its accuracy and provide deeper insights:
1. Cost Accounting Systems: Job Order Costing vs. Process Costing
The method used to accumulate manufacturing costs significantly impacts the COGM schedule.
- Job order costing: This system tracks costs for individual jobs or projects. It's suitable for companies producing unique or customized products. The COGM schedule will show costs allocated to each specific job.
- Process costing: This system averages costs across large production runs of identical products. It’s more efficient for mass production environments. The COGM schedule will reflect average unit costs.
2. Joint Products and By-Products
When multiple products are produced from a single production process, the allocation of costs among joint products requires careful consideration. Allocation methods such as market value, physical quantities, or net realizable value are commonly used. By-products, less significant products resulting from the main production process, require appropriate accounting treatment as well.
3. Spoilage and Waste
The cost of spoiled or wasted materials and labor during the production process needs to be appropriately accounted for in the COGM schedule. These costs can be separated and presented as a separate line item or allocated to good units produced.
4. Variances Analysis
Comparing budgeted costs with actual costs revealed in the COGM schedule allows for variance analysis. This helps identify deviations and pinpoint areas where cost control measures are needed. Understanding these variances can dramatically improve profitability.
5. Automation and Technology
The increasing use of automation and technology in manufacturing necessitates adjustments to the COGM schedule. Depreciation on automated equipment, software costs, and maintenance of sophisticated systems must be accurately incorporated into manufacturing overhead.
Using the COGM Schedule for Strategic Decision-Making
The COGM schedule is more than just a bookkeeping tool; it’s a powerful instrument for strategic decision-making. By analyzing the data, businesses can:
- Identify Cost Drivers: Pinpoint the factors significantly impacting manufacturing costs. This might reveal areas needing process improvement or cost-saving initiatives.
- Optimize Production Processes: By analyzing direct labor and manufacturing overhead costs, businesses can streamline operations and reduce waste.
- Evaluate New Technologies: Assess the cost-effectiveness of investing in new technologies by projecting their impact on the COGM schedule.
- Improve Pricing Strategies: Understand the true cost of goods to set competitive yet profitable prices.
- Enhance Inventory Control: Optimize inventory levels by accurately forecasting demand based on past production costs and sales.
Conclusion: The COGM Schedule – A Vital Business Tool
The Schedule of Cost of Goods Manufactured is a cornerstone of accurate financial reporting and effective management decision-making within manufacturing businesses. Its detailed breakdown of manufacturing costs provides invaluable insights into operational efficiency, profitability, and cost control. By mastering the intricacies of the COGM schedule and incorporating advanced considerations, businesses can significantly enhance their financial performance and achieve sustainable growth. Understanding and utilizing this crucial schedule is essential for any organization engaged in manufacturing activities. Its power lies not just in the calculation itself, but in the strategic analysis that follows, driving improvements and informed decision-making across the entire organization.
Latest Posts
Latest Posts
-
A Nurse Is Caring For A Client Who Has Osteoporosis
Apr 03, 2025
-
Fire Doors Also Called Smoke Barrier Doors Should
Apr 03, 2025
-
The Vals Framework Segments Consumers Based On
Apr 03, 2025
-
Match The Periodization Type With Its Corresponding Description
Apr 03, 2025
-
Consider The Phase Diagram For Carbon Dioxide
Apr 03, 2025
Related Post
Thank you for visiting our website which covers about Schedule Of Cost Of Goods Manufactured . We hope the information provided has been useful to you. Feel free to contact us if you have any questions or need further assistance. See you next time and don't miss to bookmark.