Process Thinking Causes Managers To Address Critical Process Elements Including
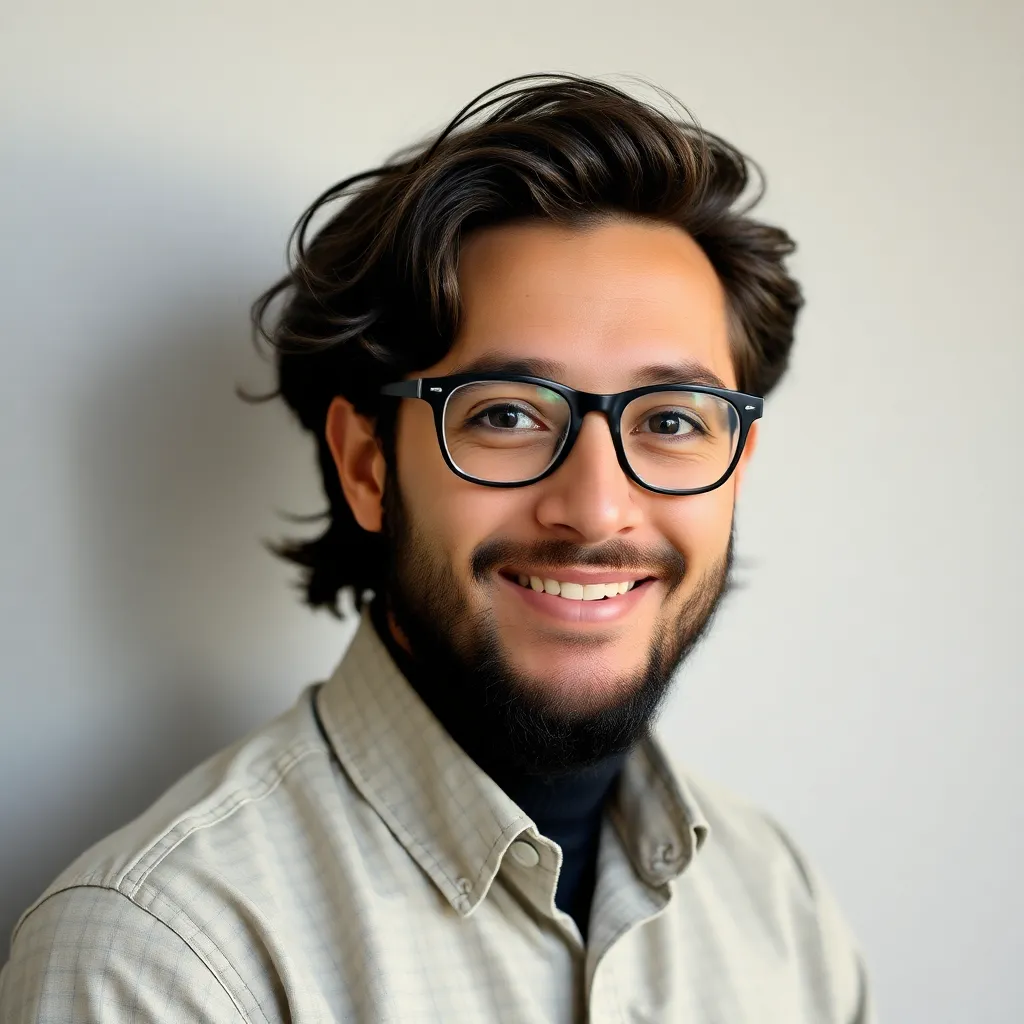
Holbox
Mar 28, 2025 · 6 min read
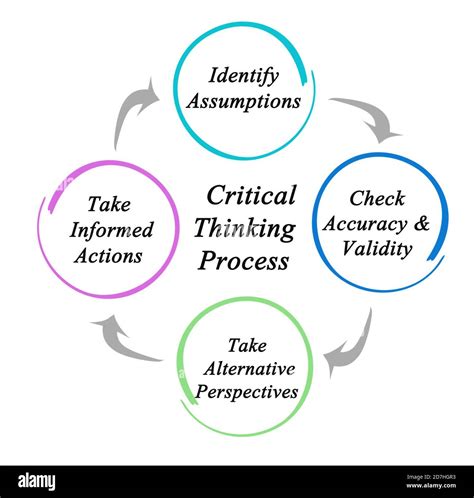
Table of Contents
- Process Thinking Causes Managers To Address Critical Process Elements Including
- Table of Contents
- Process Thinking: Addressing Critical Process Elements for Managerial Success
- Understanding the Core Principles of Process Thinking
- Key Components of Effective Process Thinking:
- How Process Thinking Causes Managers to Address Critical Process Elements
- 1. Identifying Bottlenecks and Constraints
- 2. Eliminating Waste and Non-Value-Added Activities
- 3. Enhancing Quality and Customer Satisfaction
- 4. Improving Communication and Collaboration
- 5. Measuring and Monitoring Performance
- 6. Fostering Continuous Improvement Culture
- The Benefits of Process Thinking for Managers and Organizations
- Conclusion: Embracing Process Thinking for Sustainable Success
- Latest Posts
- Latest Posts
- Related Post
Process Thinking: Addressing Critical Process Elements for Managerial Success
Process thinking is a crucial managerial skill that enables leaders to analyze and improve workflows within their organizations. It moves beyond simply reacting to problems to proactively identifying and addressing bottlenecks, inefficiencies, and potential areas for optimization. This holistic approach fosters a culture of continuous improvement, boosting productivity, enhancing quality, and ultimately driving organizational success. This article delves into the profound impact of process thinking, outlining how it compels managers to address critical process elements and achieve significant improvements.
Understanding the Core Principles of Process Thinking
Process thinking isn't merely about understanding individual tasks; it's about grasping the interconnectedness of those tasks and how they contribute to the overall objective. It involves viewing the organization as a system of interconnected processes, rather than a collection of isolated departments or functions. This perspective shift is fundamental to effective process management.
Key Components of Effective Process Thinking:
- Holistic View: Managers adopting process thinking take a holistic view of the organization, understanding how different processes interact and impact each other. This avoids siloed thinking and promotes collaboration across departments.
- Customer Focus: A critical element is understanding the customer's needs and expectations. Processes should be designed to deliver value and satisfaction to the end customer, whether internal or external.
- Data-Driven Decisions: Effective process thinking relies on data analysis to identify areas for improvement. Metrics are used to track performance, pinpoint bottlenecks, and measure the success of implemented changes.
- Continuous Improvement: Process thinking is not a one-time exercise; it's an ongoing cycle of improvement. Managers continuously monitor, analyze, and refine processes to enhance efficiency and effectiveness.
- Collaboration and Communication: Successful process improvement requires strong collaboration and open communication between different teams and individuals involved in the process.
How Process Thinking Causes Managers to Address Critical Process Elements
Process thinking forces managers to scrutinize every aspect of their organization's operations, leading to the identification and resolution of critical process elements. This includes:
1. Identifying Bottlenecks and Constraints
A major benefit of process thinking is its ability to pinpoint bottlenecks. These are points in the process where work slows down or stops, creating delays and impacting overall efficiency. By analyzing process flow, managers can identify these bottlenecks, understand their root causes, and develop strategies to alleviate them. This might involve:
- Streamlining tasks: Reducing unnecessary steps or simplifying complex procedures.
- Investing in technology: Automating repetitive tasks or using software to improve workflow management.
- Redesigning processes: Completely restructuring a process to improve efficiency and effectiveness.
- Resource allocation: Optimizing the allocation of resources (personnel, equipment, budget) to alleviate pressure points.
Example: In a manufacturing setting, a bottleneck might be a machine that operates at a slower pace than other parts of the production line. Process thinking would involve analyzing this bottleneck, perhaps investing in a faster machine or modifying the workflow to address the imbalance.
2. Eliminating Waste and Non-Value-Added Activities
Process thinking highlights waste in all its forms – anything that doesn't add value to the final product or service. This includes:
- Defects: Products or services that don't meet quality standards.
- Overproduction: Producing more than is needed or demanded.
- Waiting: Time spent waiting for materials, information, or approvals.
- Transportation: Unnecessary movement of materials or information.
- Inventory: Excessive storage of materials or finished goods.
- Motion: Unnecessary movement of people or equipment.
- Over-processing: Performing more work than necessary.
By identifying and eliminating these forms of waste, organizations can significantly improve efficiency and reduce costs.
Example: A service-based business might find that excessive paperwork and bureaucratic processes create significant waste. Process thinking would lead to the streamlining of paperwork, potentially through digitalization and automation.
3. Enhancing Quality and Customer Satisfaction
Process thinking emphasizes the importance of quality throughout the entire process. By focusing on consistent execution and continuous improvement, organizations can enhance the quality of their products or services. This directly impacts customer satisfaction and loyalty. Specific actions might include:
- Implementing quality control measures: Regularly checking for defects and ensuring consistent adherence to standards.
- Gathering customer feedback: Actively seeking feedback from customers to understand their needs and identify areas for improvement.
- Developing robust error-prevention mechanisms: Designing processes to minimize the likelihood of errors and defects.
- Empowering employees: Giving employees the authority and responsibility to identify and resolve quality issues.
4. Improving Communication and Collaboration
Process thinking necessitates clear communication and effective collaboration between different teams and individuals. This is essential for identifying problems, sharing information, and implementing solutions. Managers employing process thinking will:
- Establish clear roles and responsibilities: Ensuring that everyone understands their role in the process.
- Facilitate open communication: Creating an environment where team members can openly share information and concerns.
- Use collaborative tools: Leveraging technology to facilitate communication and information sharing.
- Foster a culture of teamwork: Promoting collaboration and mutual support among team members.
5. Measuring and Monitoring Performance
Process thinking is data-driven. Managers use metrics to track performance, identify areas for improvement, and measure the success of implemented changes. Effective monitoring involves:
- Defining key performance indicators (KPIs): Identifying the metrics that are most important for measuring process success.
- Collecting and analyzing data: Gathering data on key performance indicators and analyzing it to identify trends and patterns.
- Using dashboards and reports: Presenting performance data in a clear and concise manner.
- Regularly reviewing performance: Monitoring progress and making adjustments as needed.
6. Fostering Continuous Improvement Culture
Process thinking is not a one-time project; it's an ongoing process of improvement. Managers who embrace process thinking create a culture of continuous improvement, encouraging employees to identify and suggest improvements. This might involve:
- Implementing lean methodologies: Adopting principles of lean manufacturing or lean service to eliminate waste and improve efficiency.
- Using process improvement tools: Utilizing tools such as Six Sigma or Kaizen to systematically improve processes.
- Encouraging employee participation: Creating opportunities for employees to contribute to process improvement.
- Regularly reviewing processes: Scheduling periodic reviews to assess the effectiveness of existing processes and identify areas for improvement.
The Benefits of Process Thinking for Managers and Organizations
The adoption of process thinking yields numerous benefits for both managers and their organizations. These include:
- Increased efficiency and productivity: By eliminating waste, streamlining workflows, and optimizing resource allocation, organizations can significantly improve their efficiency and productivity.
- Improved quality and customer satisfaction: A focus on quality throughout the entire process leads to higher-quality products and services, resulting in enhanced customer satisfaction and loyalty.
- Reduced costs: By eliminating waste and improving efficiency, organizations can significantly reduce their operating costs.
- Enhanced innovation: Process thinking fosters a culture of continuous improvement, encouraging innovation and the development of new and improved processes.
- Improved decision-making: Data-driven decision-making leads to more informed and effective decisions.
- Stronger employee engagement: Empowering employees to participate in process improvement fosters increased engagement and job satisfaction.
- Increased competitive advantage: Organizations that effectively manage their processes gain a significant competitive advantage in the marketplace.
Conclusion: Embracing Process Thinking for Sustainable Success
Process thinking is not a mere management fad; it's a fundamental approach to organizational effectiveness. By adopting a process-oriented mindset, managers can significantly improve efficiency, quality, and customer satisfaction while fostering a culture of continuous improvement. The benefits extend beyond immediate gains, leading to sustainable growth and a stronger competitive position in the long term. In today's dynamic business environment, the ability to effectively analyze, optimize, and manage processes is paramount for success. Managers who embrace process thinking are equipping themselves and their organizations with the tools necessary to navigate complexity, adapt to change, and achieve lasting prosperity.
Latest Posts
Latest Posts
-
According To The Law Of Demand
Apr 01, 2025
-
Conectarse A Internet Cuando Eran Ni A Os
Apr 01, 2025
-
Match The Capital Budgeting Method To Its Specific Characteristic
Apr 01, 2025
-
Match The Following Items To The Correct Description
Apr 01, 2025
-
Hp Laptop Dependable Performance Thoughtful Design
Apr 01, 2025
Related Post
Thank you for visiting our website which covers about Process Thinking Causes Managers To Address Critical Process Elements Including . We hope the information provided has been useful to you. Feel free to contact us if you have any questions or need further assistance. See you next time and don't miss to bookmark.