Process Costing Is Not Used When
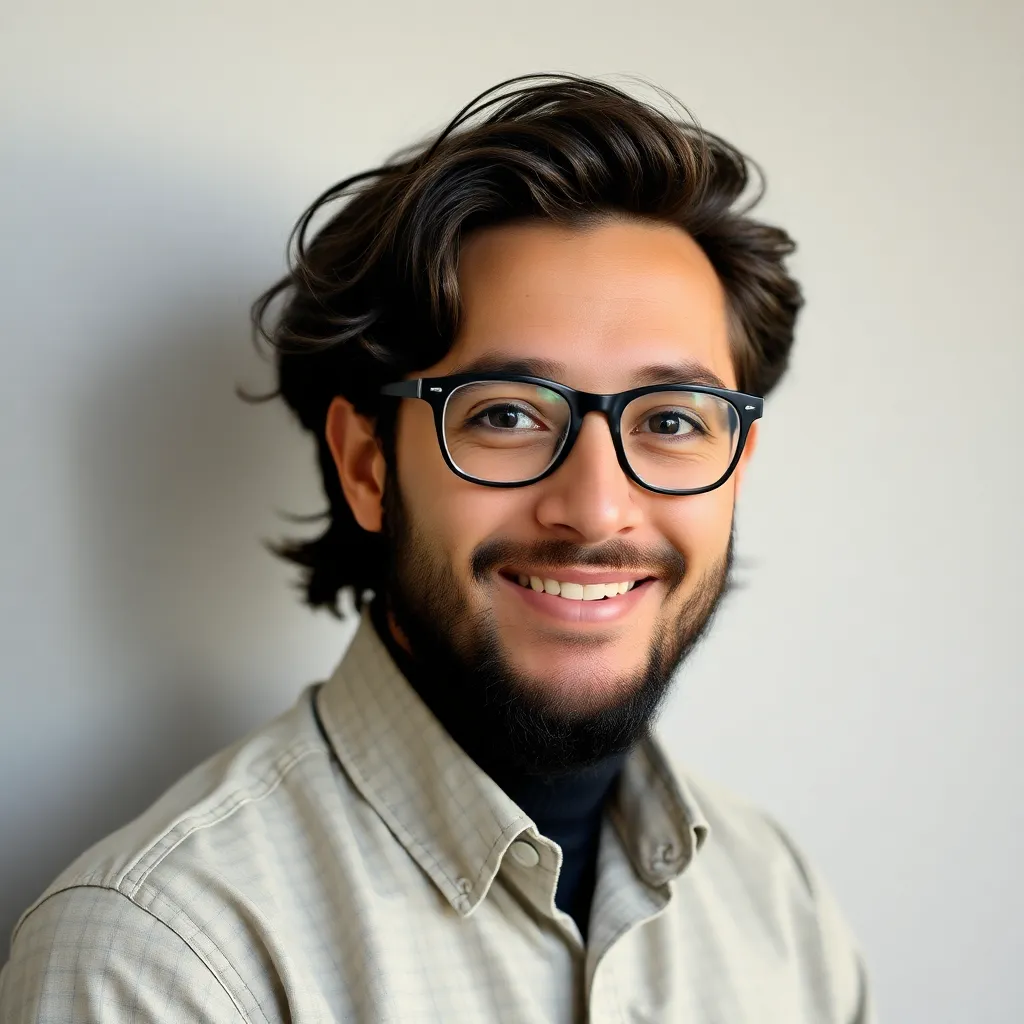
Holbox
May 07, 2025 · 5 min read
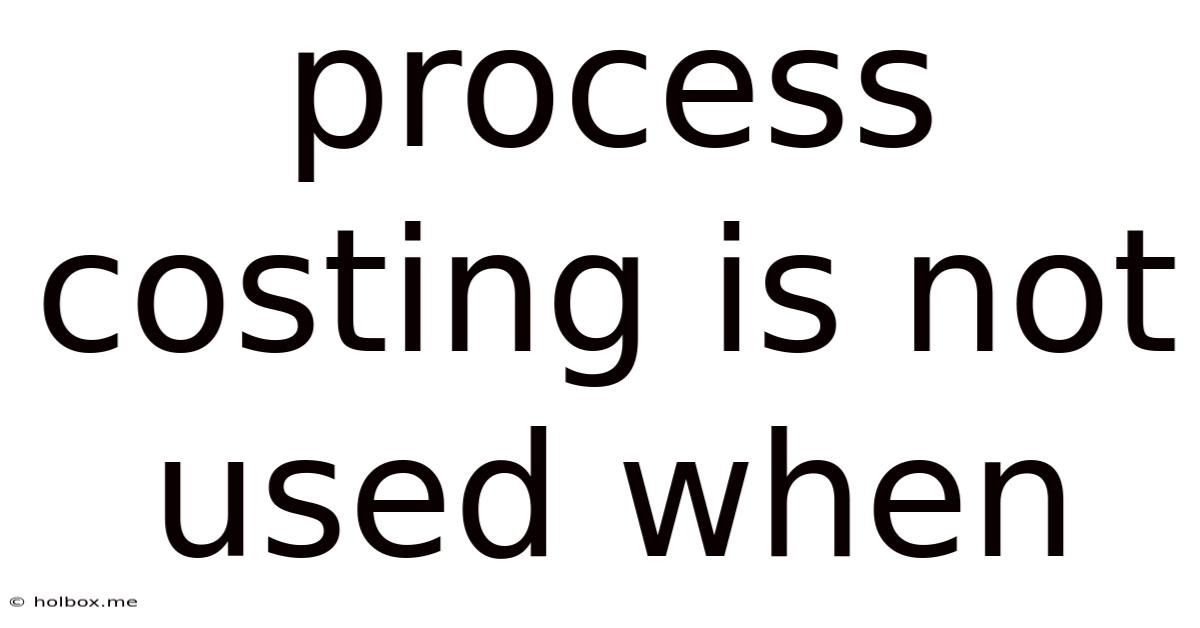
Table of Contents
- Process Costing Is Not Used When
- Table of Contents
- Process Costing: When It's Not the Right Fit
- When Process Costing Falls Short: Key Scenarios
- 1. Unique or Customized Products: The Case for Job Order Costing
- 2. Production Processes with Significant Variation: Addressing Heterogeneity
- 3. Small Batch Production: The Inefficiency of Averaging
- 4. Significant Work-in-Process (WIP) Inventory: Complexity and Inaccuracy
- 5. Intangible Products and Services: The Challenge of Measurement
- Choosing the Right Costing Method: A Strategic Approach
- Latest Posts
- Latest Posts
- Related Post
Process Costing: When It's Not the Right Fit
Process costing, a crucial costing method in manufacturing, offers a streamlined approach to assigning costs to homogenous products produced in mass quantities. However, its simplicity comes with limitations. This comprehensive guide delves into the situations where process costing is simply not the appropriate choice, highlighting alternative costing methods better suited for specific production environments. Understanding these limitations is vital for businesses aiming for accurate cost accounting and informed decision-making.
When Process Costing Falls Short: Key Scenarios
Process costing's core strength – its efficiency in handling large volumes of identical units – becomes its weakness when dealing with diverse products, unique projects, or complex production flows. Let's examine these scenarios in detail:
1. Unique or Customized Products: The Case for Job Order Costing
Process costing thrives on uniformity. When dealing with highly customized products or individual projects, each requiring unique materials, labor, and overhead, process costing's averaging approach breaks down. Imagine a bespoke tailor creating unique garments – each piece requires different fabric, patterns, and time investment, making it impractical to average these costs across multiple garments.
Instead, job order costing shines in such situations. This method tracks costs associated with each individual job or project, providing a detailed cost breakdown for each unique product or service. This ensures accurate pricing and allows businesses to understand the profitability of each unique offering.
Consider these examples:
- Construction projects: Each building project is unique, demanding specific materials, labor skills, and project durations.
- Custom software development: Software projects vary significantly in scope, features, and complexity, rendering process costing inadequate.
- Legal services: Cases differ dramatically in complexity and time requirements, making job order costing necessary for accurate cost allocation.
2. Production Processes with Significant Variation: Addressing Heterogeneity
Process costing struggles when the production process itself is highly variable. If significant differences exist in the materials, labor, or machine time required for different units within the same production batch, averages become distorted and inaccurate. Substantial variances would lead to unreliable cost figures, ultimately hindering informed pricing and decision-making.
For example, imagine a factory producing both standard and premium versions of the same product. While the core process is similar, the premium version involves higher-quality materials, specialized labor, and additional quality control checks. Averaging these costs would mask the true cost differences, leading to inaccurate pricing and potentially unprofitable decisions. Here, a more nuanced costing method like activity-based costing (ABC) would offer a more granular and accurate cost analysis.
ABC allocates costs based on activities rather than volume, pinpointing the specific cost drivers within the production process. This method is more suitable for complex processes with significant variations in resource consumption.
3. Small Batch Production: The Inefficiency of Averaging
Process costing's effectiveness diminishes when dealing with small production batches. The overhead allocation in process costing is often based on volume. In small batches, the overhead allocation per unit becomes significantly higher, leading to inaccurate cost calculations. In essence, the administrative overhead associated with managing process costing itself may outweigh its benefits when dealing with smaller quantities.
Consider these cases:
- Specialized manufacturing: Producing niche products or prototypes often involves small-scale production runs.
- Custom furniture: Individualized furniture pieces are typically produced in small batches, making process costing inefficient.
- Handcrafted goods: Artisanal items are inherently low-volume products unsuitable for the averaging approach of process costing.
In these scenarios, alternative methods like backflush costing or even simpler techniques focused on direct cost tracking might be more effective and less administratively burdensome. Backflush costing is particularly useful in high-volume, automated settings where the tracking of individual costs is less crucial.
4. Significant Work-in-Process (WIP) Inventory: Complexity and Inaccuracy
Process costing assumes a relatively smooth and continuous production flow. When the production process involves substantial work-in-process (WIP) inventory and frequent interruptions, accurate cost allocation becomes challenging. Tracking and valuing the WIP inventory precisely can be time-consuming and complex, leading to inaccuracies in the final cost calculations.
Consider these industries:
- Construction: Long project durations lead to significant WIP inventory, making cost tracking challenging.
- Aerospace manufacturing: Complex production processes with lengthy lead times often result in substantial WIP inventory.
- Shipbuilding: Large-scale projects spanning multiple years generate extensive WIP inventory, demanding detailed cost tracking methods.
For industries with substantial WIP inventory, alternative methods such as lean accounting principles, focusing on waste reduction and continuous improvement, or more detailed job order costing adapted to incorporate elements of process costing might be beneficial.
5. Intangible Products and Services: The Challenge of Measurement
Process costing is primarily designed for tangible products with easily measurable inputs and outputs. When dealing with intangible products or services, cost allocation becomes more subjective and complex. It is challenging to directly measure and quantify the inputs associated with services like consulting, software design, or marketing.
For intangible services, activity-based costing (ABC) offers a better approach by focusing on activities and their associated costs, providing a more meaningful cost allocation than simply averaging over units.
Choosing the Right Costing Method: A Strategic Approach
The selection of an appropriate costing method should be a strategic decision tailored to the unique characteristics of the production environment. Understanding the limitations of process costing allows businesses to choose the best fit, ensuring accurate cost data, enabling informed decision-making, and optimizing profitability. Consider the following factors:
- Product homogeneity: High homogeneity favors process costing; significant variations necessitate alternatives.
- Production volume: Large volumes benefit from process costing; small batches may be better served by other methods.
- Production complexity: Simple processes align well with process costing; complex processes require more nuanced methods.
- WIP inventory levels: Low WIP inventory simplifies process costing; high levels necessitate adaptations or alternative approaches.
- Cost of implementation and administration: Consider the administrative burden associated with each method.
By carefully considering these factors and the specific circumstances of their production processes, businesses can make informed decisions about the most effective costing method to deploy, ultimately leading to more accurate cost data and better business decisions. Remember, the goal is not simply to apply a specific costing method but to choose the one that best aligns with the unique characteristics of the business and leads to the most accurate and insightful cost information.
Latest Posts
Latest Posts
-
How Many Ounces In 1000 Ml
May 19, 2025
-
How Tall Is 184 Cm In Feet
May 19, 2025
-
How Many Ml Is 48 Ounces
May 19, 2025
-
How Much Is 45k Per Hour
May 19, 2025
-
How Many Days Is 900 Hours
May 19, 2025
Related Post
Thank you for visiting our website which covers about Process Costing Is Not Used When . We hope the information provided has been useful to you. Feel free to contact us if you have any questions or need further assistance. See you next time and don't miss to bookmark.