Principles Of Scientific Management Include All Of These Except:
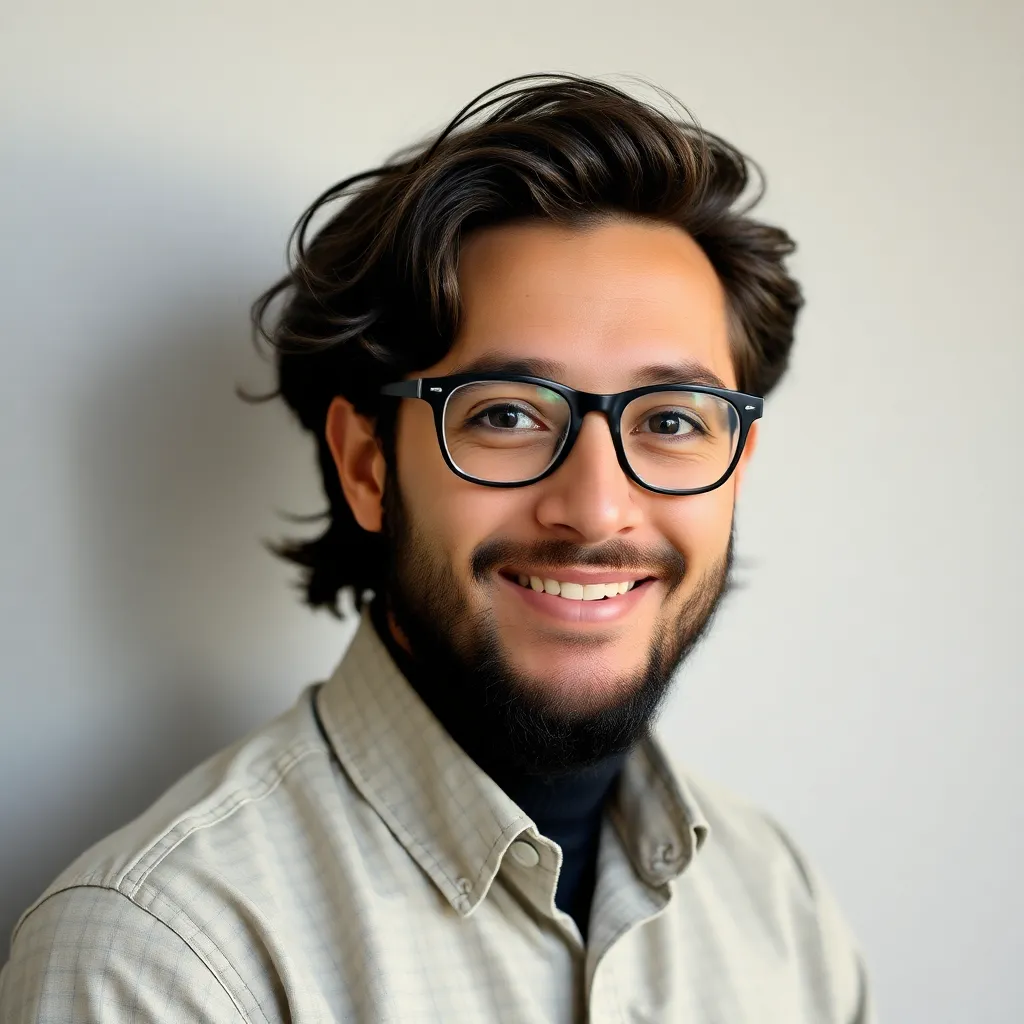
Holbox
Apr 07, 2025 · 6 min read

Table of Contents
- Principles Of Scientific Management Include All Of These Except:
- Table of Contents
- Principles of Scientific Management: Including All Except…
- The Core Principles of Scientific Management
- 1. Science, Not Rule of Thumb:
- 2. Harmony, Not Discord:
- 3. Cooperation, Not Individualism:
- 4. Development of Each and Every Person to His or Her Greatest Efficiency and Prosperity:
- What Scientific Management Excludes: The Missing Pieces
- The Evolution of Management Thought Beyond Scientific Management
- Conclusion: A Legacy of Efficiency and a Call for Humanism
- Latest Posts
- Latest Posts
- Related Post
Principles of Scientific Management: Including All Except…
Scientific management, also known as Taylorism, revolutionized industrial processes in the early 20th century. Developed by Frederick Winslow Taylor, its core principles aimed to increase efficiency and productivity through systematic analysis and optimization of workflows. Understanding these principles is crucial for anyone involved in management, engineering, or business operations. This article delves into the core tenets of scientific management, highlighting what it includes and, importantly, what it excludes.
The Core Principles of Scientific Management
Taylor’s scientific management rests on four fundamental principles:
1. Science, Not Rule of Thumb:
This principle emphasizes replacing traditional, often arbitrary methods with scientifically-developed, standardized processes. Instead of relying on guesswork or ingrained habits ("rule of thumb"), Taylor advocated for meticulous study of tasks, using time-and-motion studies, to determine the most efficient way to perform them. This involved breaking down complex jobs into smaller, simpler components, analyzing each step for potential improvements, and then establishing best practices. The goal was to eliminate wasted movements, optimize tool usage, and ultimately, maximize output.
Example: Instead of letting workers choose their own tools and methods for assembling a product, scientific management would involve carefully selecting the optimal tools, designing the workspace for ergonomic efficiency, and establishing a precise sequence of movements for each step in the assembly process. This approach ensures consistency and minimizes errors.
2. Harmony, Not Discord:
Taylor stressed the importance of collaboration between management and workers. He believed that a spirit of cooperation, rather than conflict, was essential for achieving maximum productivity. This involved fair compensation systems that incentivized workers to achieve higher output while also ensuring management understood and addressed worker concerns. Open communication and mutual respect were key elements in fostering this harmonious relationship.
Example: Implementing a piece-rate system, where workers are paid based on the number of units they produce, can align the interests of both management and workers. This encourages workers to increase their productivity, while simultaneously benefiting the company by increasing overall output.
3. Cooperation, Not Individualism:
This principle focuses on teamwork and collaboration. Taylor recognized that individual efforts alone were insufficient for maximizing efficiency. Instead, he advocated for a carefully structured system where workers collaborated closely with management, sharing their expertise and working together to achieve common goals. This involved clear communication channels, defined roles and responsibilities, and a shared understanding of the overall objectives.
Example: The assembly line, a hallmark of mass production, embodies this principle. Workers specialize in specific tasks, working together in a coordinated manner to produce a finished product. Each worker's contribution is crucial, and their collective efforts lead to significantly higher productivity than individual efforts.
4. Development of Each and Every Person to His or Her Greatest Efficiency and Prosperity:
This principle emphasizes the importance of worker training and development. Taylor recognized that workers' skills and knowledge directly impacted productivity. He advocated for systematic training programs to equip workers with the necessary skills to perform their jobs efficiently. This also included providing opportunities for advancement and promoting a culture of continuous improvement. The ultimate goal was to maximize both individual and organizational success.
Example: Providing workers with specialized training on new equipment or techniques, coupled with performance-based incentives, motivates workers to enhance their skills and contribute to improved efficiency. This investment in human capital benefits both the worker and the organization.
What Scientific Management Excludes: The Missing Pieces
While Taylor's principles were groundbreaking for their time, they also lacked certain elements that are considered crucial in modern management theory. Scientific management, in its purest form, often excludes:
-
Worker Autonomy and Job Satisfaction: Taylor's emphasis on standardization and efficiency often led to highly repetitive and monotonous tasks. The focus was on maximizing output, sometimes at the expense of worker job satisfaction and autonomy. Workers were often treated as interchangeable parts in a larger machine, with little consideration for their individual needs or desires. Modern management emphasizes the importance of employee engagement and empowerment.
-
Individual Differences and Creativity: Scientific management often assumes that all workers are the same and will respond identically to standardized procedures. It often fails to accommodate individual differences in skill, aptitude, and creativity. Contemporary management recognizes the value of diverse perspectives and talents, encouraging innovation and adaptability.
-
Social and Psychological Factors: Taylor's model largely ignores the social and psychological aspects of the workplace. It doesn't adequately account for factors like worker morale, team dynamics, and the impact of social interactions on productivity. Modern management incorporates elements of organizational behavior and psychology to understand and manage the human side of the workplace.
-
Ethical Considerations: While Taylor aimed for a harmonious relationship between management and workers, the implementation of scientific management sometimes led to exploitation. The relentless pursuit of efficiency could lead to increased workload, reduced job security, and unfair treatment of workers. Modern management emphasizes ethical considerations, ensuring fair compensation, safe working conditions, and respect for worker rights.
-
Adaptability and Flexibility: The rigid standardization inherent in scientific management can make it difficult to adapt to changing market conditions or technological advancements. The focus on pre-determined best practices can stifle innovation and hinder the ability to respond to unexpected challenges. Modern management stresses the importance of flexibility, agility, and continuous adaptation.
The Evolution of Management Thought Beyond Scientific Management
Scientific management laid the groundwork for many modern management techniques, but it's far from the complete picture. Subsequent management theories have built upon Taylor's work, incorporating elements of human relations, behavioral science, and systems thinking. These newer approaches recognize the limitations of a purely mechanistic view of the workplace and emphasize the importance of considering human factors, ethical considerations, and adaptability.
Here are some key developments that have expanded upon and refined the principles of scientific management:
-
Human Relations Movement: This movement emphasized the importance of social factors in the workplace, recognizing that worker morale, motivation, and social interactions significantly impact productivity. The Hawthorne studies played a crucial role in highlighting the influence of social dynamics on performance.
-
Behavioral Science Approach: This approach integrates principles from psychology and sociology to understand human behavior in the workplace. It uses scientific methods to study motivation, leadership styles, group dynamics, and organizational culture.
-
Systems Theory: This approach views the organization as a complex system with interconnected parts. It emphasizes the importance of understanding the interactions between various components of the organization and its environment.
-
Contingency Theory: This theory recognizes that there is no "one best way" to manage. The optimal management approach depends on various factors, including the organization's size, industry, technology, and culture.
-
Total Quality Management (TQM): This approach focuses on continuous improvement and customer satisfaction. It emphasizes the importance of teamwork, employee empowerment, and a commitment to quality in all aspects of the organization.
Conclusion: A Legacy of Efficiency and a Call for Humanism
Scientific management's legacy is undeniable. Its principles, particularly the emphasis on efficiency and standardization, have significantly impacted industrial processes and mass production. However, it’s crucial to acknowledge its limitations and the need for a more holistic approach to management that integrates the best elements of scientific management with contemporary insights into human behavior, ethical considerations, and adaptability. The ideal management approach balances the pursuit of efficiency with a genuine commitment to worker well-being, fostering a workplace that is both productive and fulfilling. By understanding both the strengths and weaknesses of scientific management, we can build upon its contributions while avoiding its potential pitfalls. The ultimate goal is to create organizations that are not only efficient and profitable but also equitable, just, and supportive of their employees.
Latest Posts
Latest Posts
-
Which Of The Following Statements About Platform Business Is True
Apr 15, 2025
-
The Graph Illustrates A Monopoly With Constant Marginal Cost
Apr 15, 2025
-
Understanding Rhetoric A Graphic Guide To Writing
Apr 15, 2025
-
7 77 Draw The Shear And Moment Diagrams For The Beam
Apr 15, 2025
-
Arrange The Amines In Order Of Boiling Point
Apr 15, 2025
Related Post
Thank you for visiting our website which covers about Principles Of Scientific Management Include All Of These Except: . We hope the information provided has been useful to you. Feel free to contact us if you have any questions or need further assistance. See you next time and don't miss to bookmark.