Prepare A Cost Of Goods Manufactured Schedule
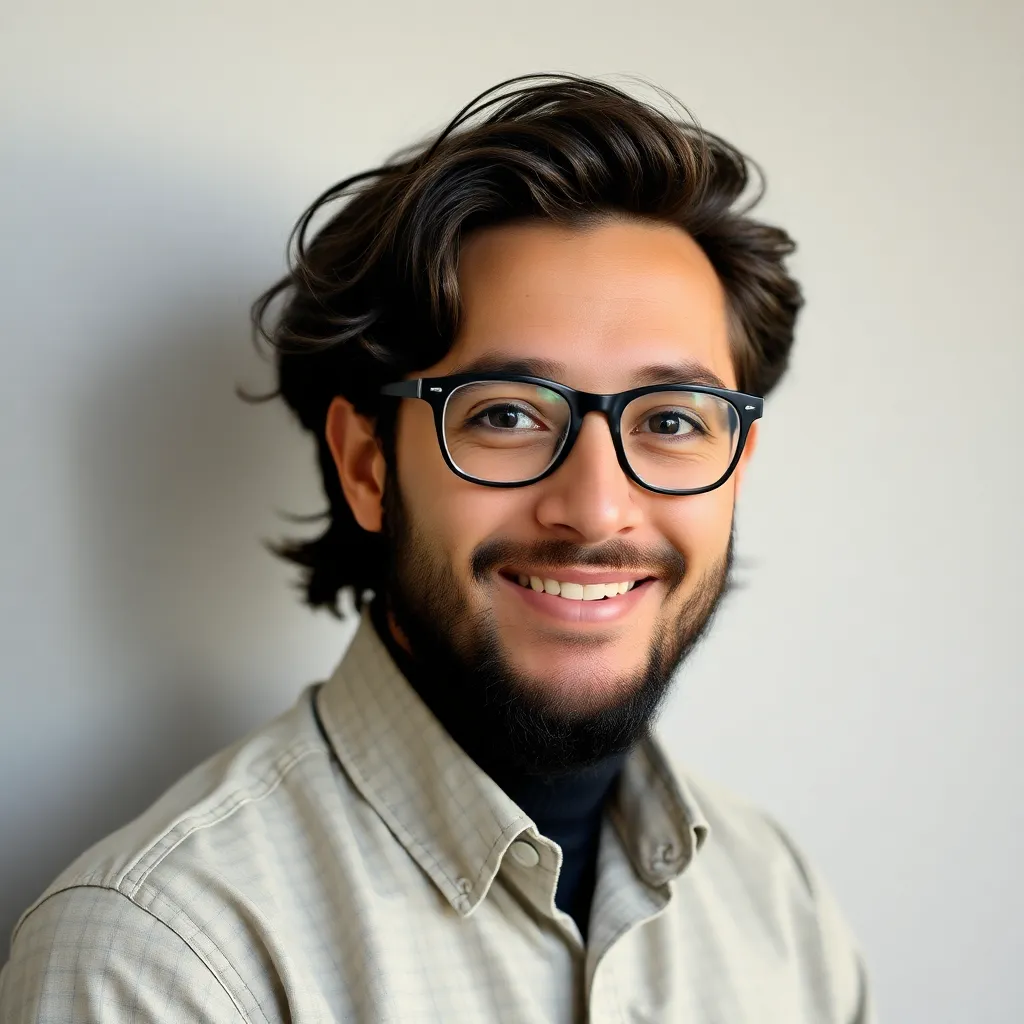
Holbox
Apr 08, 2025 · 7 min read
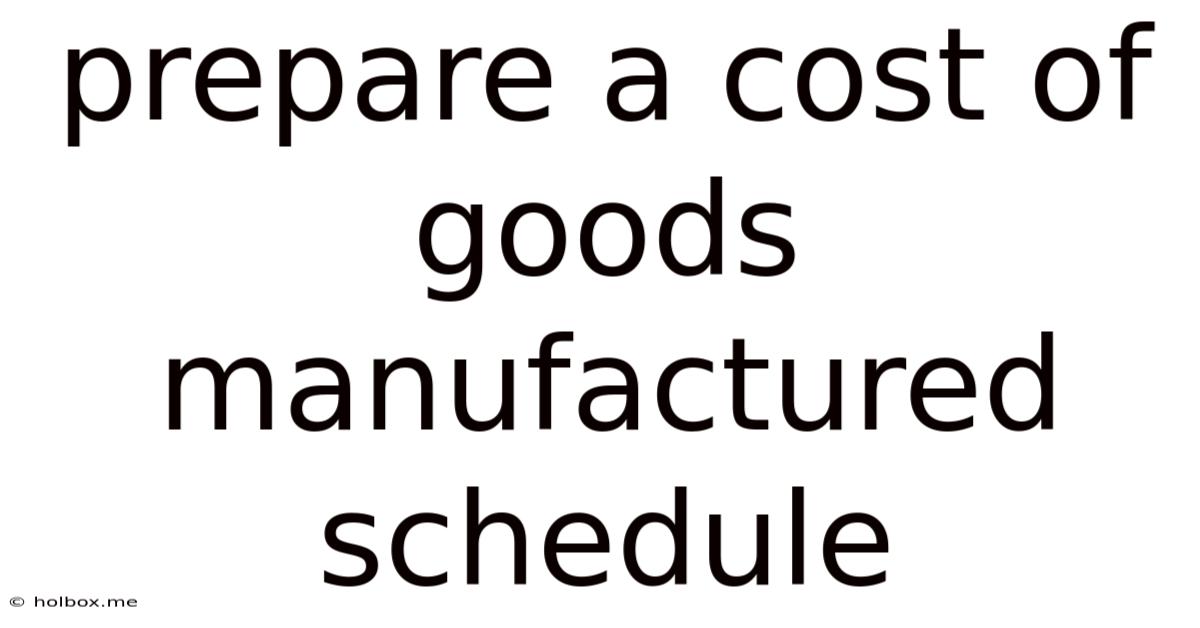
Table of Contents
- Prepare A Cost Of Goods Manufactured Schedule
- Table of Contents
- Preparing a Cost of Goods Manufactured (COGM) Schedule: A Comprehensive Guide
- What is a Cost of Goods Manufactured (COGM) Schedule?
- Key Components of the COGM Schedule
- 1. Direct Materials Used
- 2. Direct Labor
- 3. Manufacturing Overhead
- 4. Beginning Work in Process (WIP) Inventory
- 5. Ending Work in Process (WIP) Inventory
- Preparing the COGM Schedule: A Step-by-Step Guide
- The COGM Schedule Format
- Importance of Accurate COGM Calculation
- Common Errors to Avoid When Preparing a COGM Schedule
- Using the COGM Schedule for Business Improvement
- Conclusion
- Latest Posts
- Latest Posts
- Related Post
Preparing a Cost of Goods Manufactured (COGM) Schedule: A Comprehensive Guide
Understanding your Cost of Goods Manufactured (COGM) is crucial for any manufacturing business. It's a key component of your financial statements, offering vital insights into your production efficiency and profitability. This comprehensive guide will walk you through the process of preparing a COGM schedule, explaining each element and providing practical examples to ensure a thorough understanding. We'll delve into the importance of accuracy, common errors to avoid, and how to use the COGM schedule to improve your business decisions.
What is a Cost of Goods Manufactured (COGM) Schedule?
The COGM schedule is a detailed report that shows the total cost of finished goods manufactured during a specific period. It's not a standalone financial statement but rather a crucial supporting schedule used in calculating the Cost of Goods Sold (COGS) on the income statement. The COGM schedule summarizes all the costs directly associated with the production process, from raw materials to labor and factory overhead. This allows businesses to track the efficiency of their manufacturing process and identify areas for potential cost reduction.
Key Components of the COGM Schedule
The COGM schedule typically includes the following key components:
1. Direct Materials Used
This represents the cost of raw materials directly consumed in the manufacturing process. Calculating this involves considering:
- Beginning Raw Materials Inventory: The value of raw materials on hand at the start of the period.
- Purchases of Raw Materials: The cost of all raw materials acquired during the period.
- Ending Raw Materials Inventory: The value of raw materials remaining at the end of the period.
Formula: Beginning Raw Materials Inventory + Purchases of Raw Materials - Ending Raw Materials Inventory = Direct Materials Used
2. Direct Labor
This refers to the wages and benefits paid to workers directly involved in the production process. This includes assembly line workers, machine operators, and other personnel whose time can be directly traced to specific products. It's essential to accurately track labor hours and associated costs.
3. Manufacturing Overhead
This encompasses all indirect costs associated with the manufacturing process. Unlike direct materials and labor, these costs are not easily traceable to individual products. Examples include:
- Indirect Labor: Wages paid to factory supervisors, maintenance personnel, and other support staff.
- Factory Rent: Costs associated with leasing or owning the manufacturing facility.
- Utilities: Electricity, water, and gas consumed in the factory.
- Depreciation: The allocation of the cost of factory equipment over its useful life.
- Factory Supplies: Consumable items used in the production process.
- Insurance: Premiums paid for factory insurance.
4. Beginning Work in Process (WIP) Inventory
This is the value of partially completed goods at the beginning of the accounting period. It represents the costs incurred on products that were not yet finished at the start of the period.
5. Ending Work in Process (WIP) Inventory
This is the value of partially completed goods remaining at the end of the accounting period. It represents the costs incurred on products that are still under production at the period's end.
Preparing the COGM Schedule: A Step-by-Step Guide
Let's illustrate the preparation of a COGM schedule with a practical example. Assume the following data for XYZ Manufacturing Company for the year ended December 31, 2023:
- Beginning Raw Materials Inventory: $10,000
- Purchases of Raw Materials: $50,000
- Ending Raw Materials Inventory: $15,000
- Direct Labor: $30,000
- Manufacturing Overhead: $20,000
- Beginning Work in Process (WIP) Inventory: $5,000
- Ending Work in Process (WIP) Inventory: $8,000
Step 1: Calculate Direct Materials Used
$10,000 (Beginning Raw Materials) + $50,000 (Purchases) - $15,000 (Ending Raw Materials) = $45,000 (Direct Materials Used)
Step 2: Calculate Total Manufacturing Costs
$45,000 (Direct Materials Used) + $30,000 (Direct Labor) + $20,000 (Manufacturing Overhead) = $95,000 (Total Manufacturing Costs)
Step 3: Calculate Cost of Goods Manufactured (COGM)
$5,000 (Beginning WIP Inventory) + $95,000 (Total Manufacturing Costs) - $8,000 (Ending WIP Inventory) = $92,000 (Cost of Goods Manufactured)
The COGM Schedule Format
The COGM schedule can be presented in a clear and concise format, making it easy to understand and interpret. Here's a sample format:
XYZ Manufacturing Company
Cost of Goods Manufactured Schedule
For the Year Ended December 31, 2023
Item | Amount |
---|---|
Beginning Work in Process Inventory | $5,000 |
Direct Materials Used: | |
Beginning Raw Materials Inventory | $10,000 |
Purchases of Raw Materials | $50,000 |
Ending Raw Materials Inventory | ($15,000) |
Total Direct Materials Used | $45,000 |
Direct Labor | $30,000 |
Manufacturing Overhead | $20,000 |
Total Manufacturing Costs | $95,000 |
Total Work in Process | $100,000 |
Ending Work in Process Inventory | ($8,000) |
Cost of Goods Manufactured | $92,000 |
Importance of Accurate COGM Calculation
Accurate COGM calculation is critical for several reasons:
- Accurate Income Statement: An incorrect COGM directly impacts the accuracy of your Cost of Goods Sold (COGS) on the income statement, leading to misstated profits.
- Inventory Valuation: The COGM schedule helps determine the value of your finished goods inventory, impacting your balance sheet.
- Pricing Decisions: Understanding your COGM allows you to accurately price your products to ensure profitability.
- Performance Evaluation: Tracking your COGM over time helps monitor your manufacturing efficiency and identify areas for improvement.
- Financial Reporting: Accurate COGM figures are essential for complying with accounting standards and presenting reliable financial reports to stakeholders.
Common Errors to Avoid When Preparing a COGM Schedule
Several common mistakes can lead to inaccuracies in your COGM schedule. Here are some to watch out for:
- Incorrect Classification of Costs: Ensure that all costs are properly classified as either direct or indirect. Misclassification can significantly distort your COGM.
- Inaccurate Inventory Counts: Inaccurate physical inventory counts of raw materials and work in process will lead to errors in calculating direct materials used and WIP inventory.
- Omission of Costs: Ensure that all relevant costs, both direct and indirect, are included in the calculation. Overlooking costs will result in an understated COGM.
- Misallocation of Overhead Costs: Manufacturing overhead costs should be allocated fairly across products. Inaccurate allocation can distort the cost of individual products.
- Ignoring Spoilage and Waste: The costs associated with spoilage and waste should be included in the COGM calculation, especially in industries with significant material waste.
Using the COGM Schedule for Business Improvement
The COGM schedule is more than just a reporting tool. It provides valuable information for strategic decision-making. By analyzing the data within the schedule, businesses can:
- Identify Cost Reduction Opportunities: By comparing COGM figures over time and across different products, businesses can pinpoint areas where costs can be reduced. This might involve negotiating better prices with suppliers, improving production efficiency, or reducing waste.
- Improve Production Efficiency: Tracking COGM can reveal bottlenecks in the production process. Identifying and addressing these bottlenecks can significantly improve efficiency and reduce costs.
- Optimize Inventory Management: Analyzing the COGM schedule, in conjunction with inventory turnover ratios, can help optimize inventory levels, reducing storage costs and minimizing the risk of obsolescence.
- Enhance Pricing Strategies: Accurate COGM data provides a sound basis for setting prices that ensure profitability while remaining competitive. By understanding the true cost of production, businesses can make informed pricing decisions.
- Support Strategic Planning: The COGM schedule is a valuable tool for forecasting future costs and making informed business decisions related to capacity planning, investments in new equipment, and expansion plans.
Conclusion
Preparing a Cost of Goods Manufactured schedule is a fundamental process for any manufacturing business. By understanding the key components, following the steps outlined, and avoiding common errors, businesses can ensure the accuracy and usefulness of their COGM data. This data provides valuable insights into production costs, efficiency, and profitability, ultimately supporting better decision-making and improving the overall financial health of the business. Regularly reviewing and analyzing your COGM schedule will empower you to make data-driven decisions that optimize your operations and drive growth.
Latest Posts
Latest Posts
-
Choose All Functions Typically Carried Out By Membrane Proteins
Apr 25, 2025
-
Which Of The Following Statements Regarding Sharps Is Correct
Apr 25, 2025
-
Identify The Sole Product Of The Following Reaction
Apr 25, 2025
-
Which Of The Following Hitches Are Not Allowed
Apr 25, 2025
-
The Table Displays The Price Per Widget
Apr 25, 2025
Related Post
Thank you for visiting our website which covers about Prepare A Cost Of Goods Manufactured Schedule . We hope the information provided has been useful to you. Feel free to contact us if you have any questions or need further assistance. See you next time and don't miss to bookmark.