Poka-yoke Is Roughly Translated From Japanese As Avoid Mistakes.
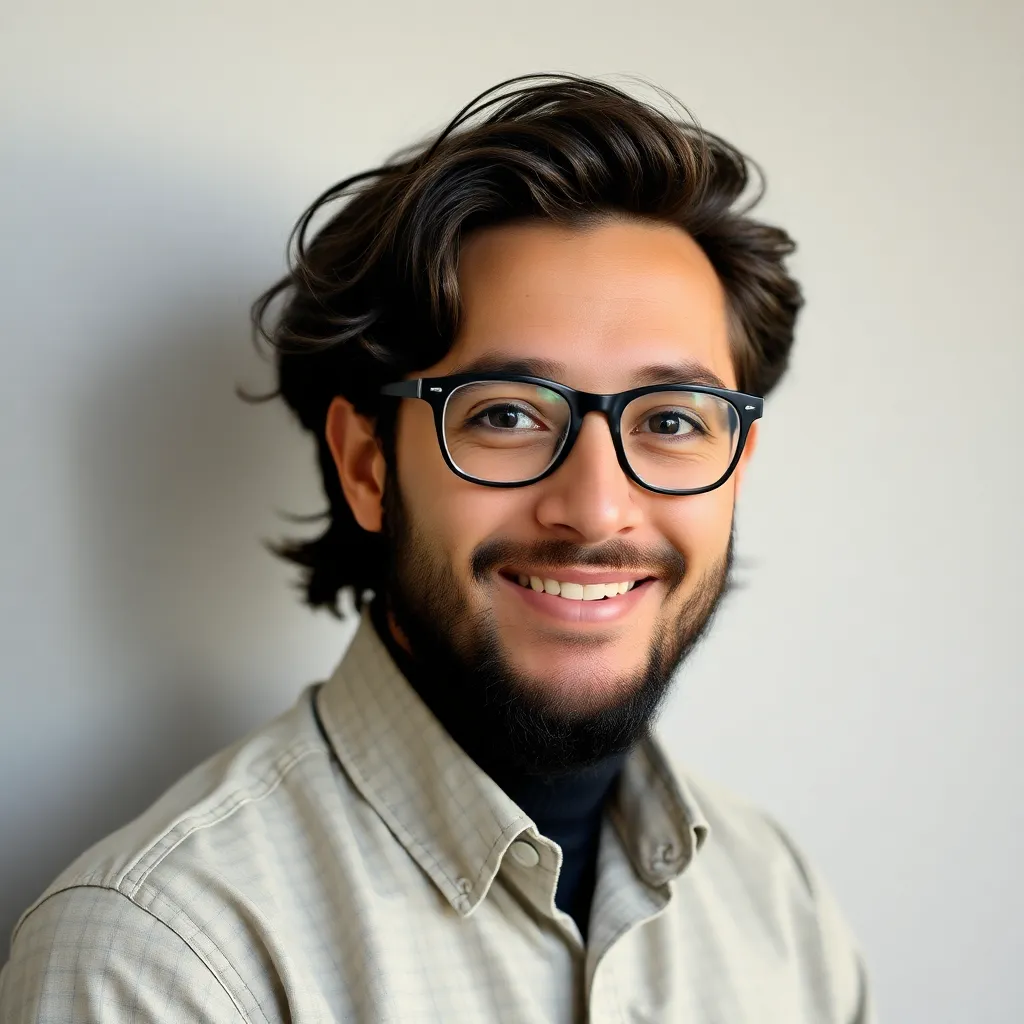
Holbox
Apr 08, 2025 · 6 min read

Table of Contents
- Poka-yoke Is Roughly Translated From Japanese As Avoid Mistakes.
- Table of Contents
- Poka-Yoke: Avoiding Mistakes Through Ingenious Design
- Understanding the Core Principles of Poka-Yoke
- Key Characteristics of Effective Poka-Yoke Systems:
- The Two Main Categories of Poka-Yoke Methods
- 1. Control Methods (Detection):
- 2. Prevention Methods (Elimination):
- Practical Applications of Poka-Yoke Across Industries
- Manufacturing:
- Healthcare:
- Information Technology:
- Customer Service:
- Implementing Poka-Yoke: A Step-by-Step Guide
- Beyond the Basics: Advanced Poka-Yoke Techniques
- The Benefits of Implementing Poka-Yoke
- Conclusion: Embracing a Culture of Error Prevention
- Latest Posts
- Latest Posts
- Related Post
Poka-Yoke: Avoiding Mistakes Through Ingenious Design
Poka-yoke, roughly translated from Japanese as "avoid mistakes," is a powerful methodology for error-proofing processes and preventing defects. It's a cornerstone of lean manufacturing and quality control, offering a proactive approach to minimizing human error—a frequent source of inefficiency and waste in various industries. This article delves deep into the principles, techniques, and applications of poka-yoke, illustrating its impact on enhancing productivity, improving product quality, and boosting overall efficiency.
Understanding the Core Principles of Poka-Yoke
At its heart, poka-yoke is about designing processes and systems that make it virtually impossible for errors to occur. Instead of relying on inspections to catch mistakes after they happen, poka-yoke focuses on preventing them before they occur. This proactive approach significantly reduces the need for rework, scrap, and costly quality control measures.
Key Characteristics of Effective Poka-Yoke Systems:
- Simplicity: Effective poka-yoke solutions are typically simple and easy to implement. They often involve straightforward mechanisms that are readily understood and used by all personnel.
- Proactive Prevention: The focus is always on preventing errors before they happen, rather than detecting them afterward.
- Cost-Effectiveness: While the initial investment might vary, the long-term cost savings from reduced defects and rework usually far outweigh the initial expense.
- Easy Implementation: Poka-yoke solutions are designed to be easily integrated into existing workflows, minimizing disruption to operations.
- Continuous Improvement: Poka-yoke is not a one-time fix; it's an ongoing process of identifying potential errors and developing creative solutions to prevent them.
The Two Main Categories of Poka-Yoke Methods
Poka-yoke strategies are generally classified into two main categories:
1. Control Methods (Detection):
These methods aim to detect errors as they happen and prevent them from propagating further. They often involve visual cues, alarms, or other signals that alert the operator to a potential problem. Think of the simple beeping sound in a car when you haven't fastened your seatbelt—a clear example of a control method. Examples include:
- Visual Controls: Color-coding, size differences, clear markings, and visual indicators that immediately highlight potential errors. For instance, using different colored wires for different circuits.
- Auditory Controls: Alarms, buzzers, or other audible signals that warn operators about potential errors. The beeping car seatbelt reminder is an ideal example.
- Tactile Controls: Physical feedback mechanisms that provide tactile cues to the operator. For example, a part that doesn't fit correctly might have a noticeable difference in texture or feel.
2. Prevention Methods (Elimination):
Prevention methods go a step further by eliminating the possibility of errors altogether. These methods are designed to make it physically impossible to make a mistake. Examples include:
- Physical Constraints: Using jigs, fixtures, or other physical restraints to guide parts into their correct positions. This is common in assembly lines where parts need to be precisely positioned before being joined.
- Process Simplification: Streamlining the workflow to remove unnecessary steps or complex procedures that increase the chances of error. This often involves eliminating redundancies and making the process more intuitive.
- Standardization: Establishing clear procedures and standards for every task, ensuring that tasks are performed consistently and correctly. This significantly reduces variability and the risk of errors.
- Fool-Proofing Designs: Designing products or equipment in a way that makes it impossible to use them incorrectly. A classic example is a USB connector that can only be plugged in one way.
Practical Applications of Poka-Yoke Across Industries
Poka-yoke's versatility makes it applicable across a vast range of industries and applications. Here are some examples:
Manufacturing:
- Assembly Lines: Preventing incorrect part placement, ensuring proper torque levels, and detecting missing components. Jigs, fixtures, and automated systems are widely used here.
- Packaging: Preventing incorrect labeling, ensuring correct quantities, and detecting damaged products. Automated inspection systems and visual controls play a crucial role.
- Quality Control: Reducing defects by preventing errors during the manufacturing process, thus minimizing rework and scrap.
Healthcare:
- Medication Dispensing: Preventing medication errors through barcoding, automated dispensing systems, and double-checking mechanisms.
- Surgical Procedures: Using checklists, safety protocols, and specialized instruments to minimize the risk of surgical errors.
- Patient Identification: Utilizing unique identifiers and verification systems to prevent mistakes in patient identification.
Information Technology:
- Data Entry: Using input validation rules, data type checks, and other techniques to prevent data entry errors.
- Software Development: Implementing automated testing, code reviews, and other quality assurance measures to prevent software bugs.
- Cybersecurity: Employing authentication measures, access controls, and intrusion detection systems to prevent unauthorized access and cyber threats.
Customer Service:
- Order Processing: Using automated systems to ensure accurate order entry and processing.
- Complaint Handling: Establishing clear procedures for handling complaints and resolving customer issues.
- Communication: Using standardized scripts and communication channels to ensure consistent and accurate messaging.
Implementing Poka-Yoke: A Step-by-Step Guide
Implementing poka-yoke effectively requires a systematic approach. Here's a step-by-step guide:
- Identify Potential Errors: Conduct a thorough analysis of the process to pinpoint areas prone to errors. This may involve observing the process, analyzing data, and gathering input from employees.
- Determine Error Types: Categorize the errors as either control errors (incorrect actions) or omission errors (missed steps).
- Select Appropriate Poka-Yoke Methods: Choose the most suitable methods based on the types of errors identified and the characteristics of the process.
- Design and Implement the Solution: Develop a detailed plan for implementing the chosen poka-yoke methods. This might involve designing new equipment, modifying existing procedures, or training employees.
- Test and Evaluate: Thoroughly test the implemented solution to ensure its effectiveness and identify any unforeseen issues.
- Monitor and Improve: Continuously monitor the process to identify any remaining errors and refine the poka-yoke system over time.
Beyond the Basics: Advanced Poka-Yoke Techniques
While the fundamental principles of poka-yoke remain consistent, advanced techniques offer more sophisticated solutions for complex processes. These techniques often leverage technology and data analysis:
- Statistical Process Control (SPC): Using statistical methods to monitor process variation and identify potential problems before they lead to errors.
- Automated Inspection Systems: Using automated systems to inspect products and detect defects automatically.
- Data Analytics: Utilizing data analytics to identify patterns and trends in errors, allowing for proactive interventions.
- Artificial Intelligence (AI): Employing AI-powered systems to detect anomalies and predict potential errors.
The Benefits of Implementing Poka-Yoke
The benefits of implementing poka-yoke extend far beyond simply reducing errors. It contributes to:
- Improved Quality: Minimizing defects and ensuring consistent product quality.
- Increased Productivity: Reducing rework, scrap, and downtime.
- Reduced Costs: Lowering the costs associated with quality control and defect correction.
- Enhanced Employee Morale: Empowering employees to prevent errors and improving job satisfaction.
- Improved Safety: Minimizing the risk of accidents and injuries caused by human error.
- Increased Customer Satisfaction: Delivering high-quality products and services that meet customer expectations.
Conclusion: Embracing a Culture of Error Prevention
Poka-yoke is more than just a set of techniques; it's a philosophy that emphasizes proactive error prevention and continuous improvement. By embracing a culture of error prevention and implementing poka-yoke principles, organizations can significantly enhance their operational efficiency, improve product quality, and build a stronger foundation for sustainable success. The journey towards a more error-free environment begins with a commitment to understanding and applying the principles of poka-yoke, fostering a proactive approach to quality and efficiency across all aspects of the business. Implementing poka-yoke isn’t merely about fixing problems; it’s about preventing them from ever arising in the first place – a truly transformative approach to quality management.
Latest Posts
Latest Posts
-
Which Element Is More Likely To Become A Anion
Apr 24, 2025
-
In Addition To Pregnant Women Fetuses And Neonates
Apr 24, 2025
-
Which Of The Following Is A Correct Statement About Mrna
Apr 24, 2025
-
Monopolies Are Socially Inefficient Because The Price They Charge Is
Apr 24, 2025
-
Creating A Competitive Advantage Requires Management To
Apr 24, 2025
Related Post
Thank you for visiting our website which covers about Poka-yoke Is Roughly Translated From Japanese As Avoid Mistakes. . We hope the information provided has been useful to you. Feel free to contact us if you have any questions or need further assistance. See you next time and don't miss to bookmark.