Modifying Relay-type Process Control Circuits Usually Involves Changing The
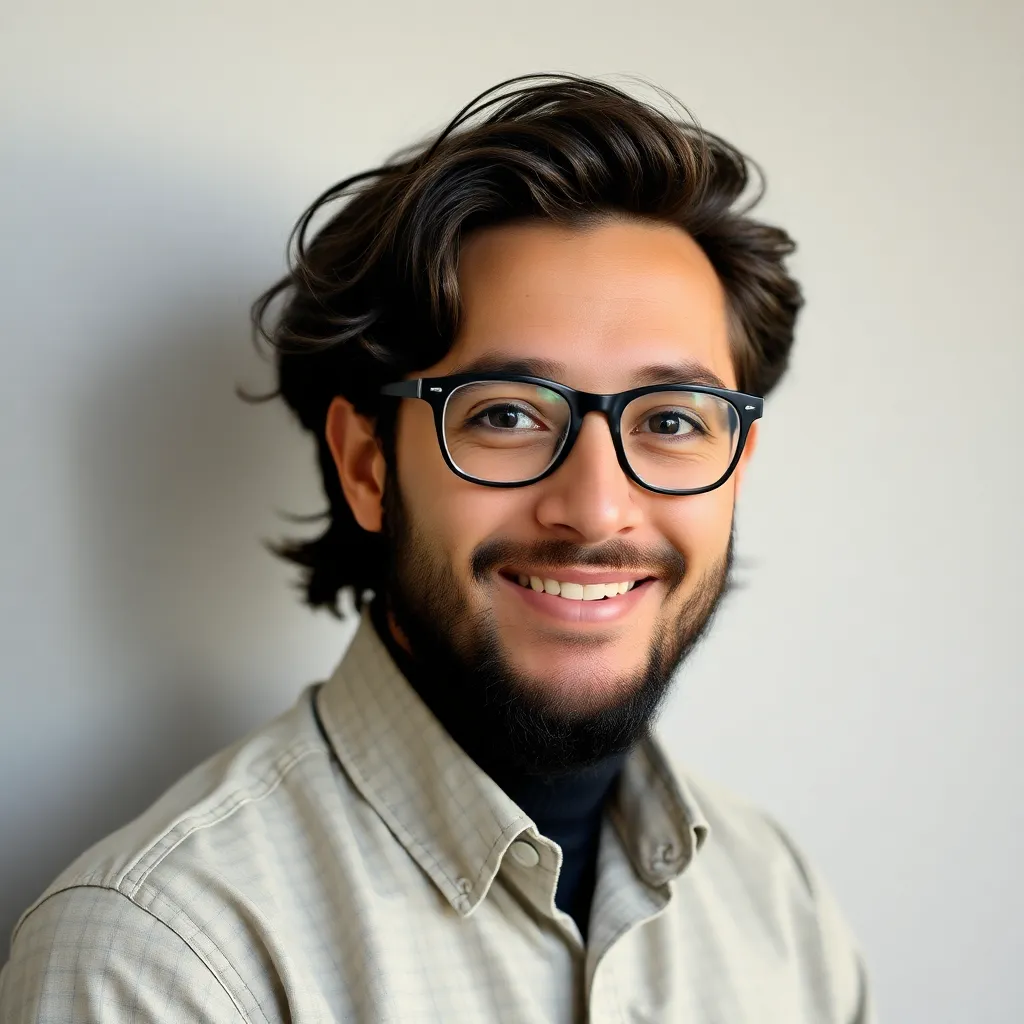
Holbox
May 07, 2025 · 7 min read
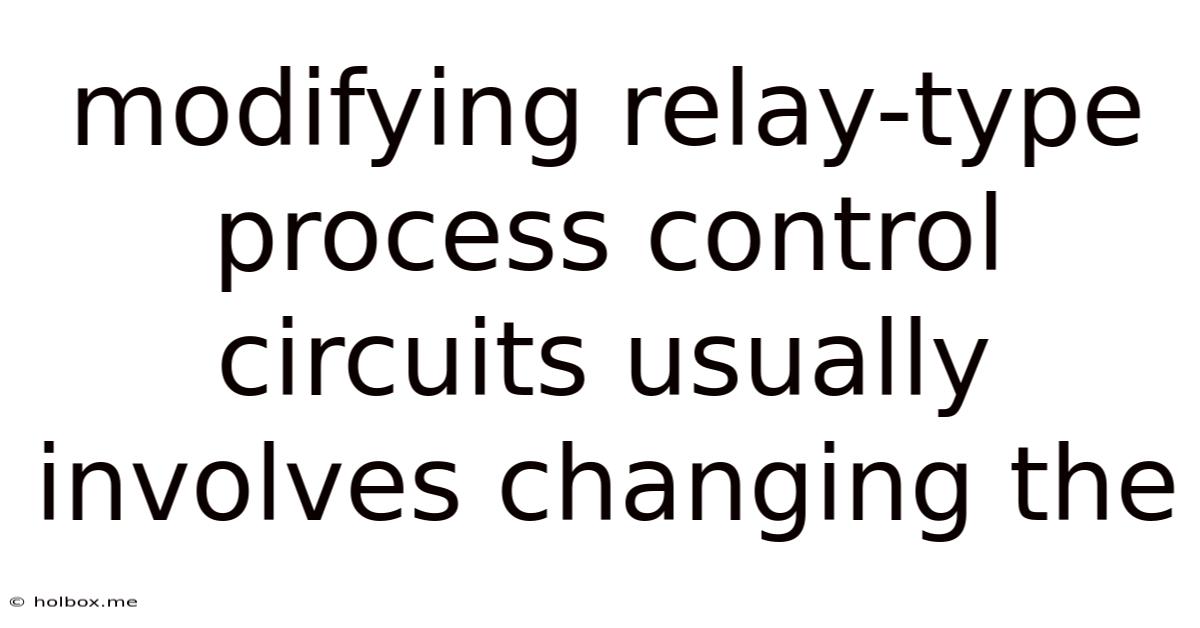
Table of Contents
- Modifying Relay-type Process Control Circuits Usually Involves Changing The
- Table of Contents
- Modifying Relay-Type Process Control Circuits: Understanding the Changes Involved
- Understanding Relay-Type Process Control Circuits
- 1. Sensors:
- 2. Relays:
- 3. Control Logic:
- 4. Actuators:
- 5. Power Supplies:
- Common Modifications to Relay-Type Process Control Circuits
- 1. Adding New Control Points:
- 2. Altering Control Logic:
- 3. Upgrading Components:
- 4. Implementing Safety Interlocks:
- 5. Integrating Programmable Logic Controllers (PLCs):
- Safety Precautions When Modifying Relay Circuits
- Troubleshooting Modified Relay-Type Circuits
- Using Ladder Logic Diagrams for Modification
- The Transition to Modern Control Systems
- Conclusion
- Latest Posts
- Related Post
Modifying Relay-Type Process Control Circuits: Understanding the Changes Involved
Modifying relay-type process control circuits requires a meticulous and systematic approach. These circuits, while seemingly simple, can be surprisingly complex, especially in larger industrial applications. Understanding the intricacies of these systems is crucial before attempting any modifications. This article delves into the various aspects of modifying relay-type process control circuits, focusing on the key components and procedures involved. We'll cover everything from safety considerations to troubleshooting modified systems.
Understanding Relay-Type Process Control Circuits
Before diving into modifications, it's essential to grasp the fundamental principles of relay-type process control circuits. These circuits use electromechanical relays to switch power to different parts of the system, based on input signals from sensors and other devices. The core components typically include:
1. Sensors:
These are the eyes and ears of the system, providing information about the process being controlled. Examples include temperature sensors (thermocouples, RTDs), pressure sensors, level sensors, and flow sensors. Their output signals, often analog voltages or currents, are converted into switching signals for the relays.
2. Relays:
These are the crucial switching elements. An input signal (typically a small current) energizes the relay coil, activating a switch that closes or opens a higher-power circuit. This allows a small signal to control a larger load, such as a motor, heater, or valve. Different relay types exist, including electromechanical relays, solid-state relays (SSRs), and programmable logic controllers (PLCs) that can mimic relay logic. Understanding the relay's specifications, including voltage, current, and contact ratings, is paramount.
3. Control Logic:
This determines the system's response to sensor inputs. In relay-type circuits, the logic is implemented using a network of interconnected relays, creating a ladder logic diagram that visualizes the system's operation. This diagram displays the flow of signals and the relationships between different components. Modifying the control logic often involves adding, removing, or reconnecting relays to achieve the desired changes.
4. Actuators:
These are the muscles of the system, performing the actions dictated by the control logic. Examples include motors (for pumps, valves, and conveyors), heaters, and solenoids (for valves). Modifying the circuit might involve changing the actuator, its power supply, or the relay controlling it.
5. Power Supplies:
These provide the necessary power for the relays and actuators. The power supply's voltage and current capacity must be sufficient to handle the load. Incorrectly sizing the power supply can lead to malfunction and damage. Always ensure your power supply is adequately rated.
Common Modifications to Relay-Type Process Control Circuits
Modifications to relay-type process control circuits are typically driven by changes in process requirements, improved control strategies, or fault remediation. Some common modifications include:
1. Adding New Control Points:
This could involve adding a new sensor to monitor a specific parameter or incorporating a new actuator to perform an additional function. This requires adding new relays and wiring to integrate the new components into the existing control logic. Careful planning and meticulous wiring are crucial to avoid introducing errors.
2. Altering Control Logic:
This might be necessary to implement a different control strategy, refine the system's response, or correct a fault in the original design. This modification could involve adding, removing, or re-wiring relays to alter the signal flow and the logical relationships between the components. Thorough understanding of the existing logic and the desired changes is essential.
3. Upgrading Components:
Replacing older, less reliable components with newer, more efficient ones can improve the system's performance and reliability. This could involve replacing outdated relays with modern equivalents or upgrading sensors for improved accuracy. Always ensure compatibility between the new components and the existing circuitry.
4. Implementing Safety Interlocks:
Adding safety interlocks is crucial to prevent accidents and protect personnel. This could involve incorporating emergency stops, limit switches, or other safety devices that interrupt the system's operation under unsafe conditions. Safety interlocks are non-negotiable in industrial applications. Improperly implemented safety features can result in catastrophic failure.
5. Integrating Programmable Logic Controllers (PLCs):
In some cases, it might be beneficial to integrate a PLC to replace a complex network of relays. PLCs offer more flexible control capabilities, easier programming, and enhanced monitoring features. This involves removing the existing relays and wiring, and connecting the sensors and actuators to the PLC's input and output modules. This is a more involved modification requiring specialized knowledge.
Safety Precautions When Modifying Relay Circuits
Modifying any electrical circuit carries inherent risks. Relay-type circuits, while less complex than advanced systems, still require strict adherence to safety procedures.
- Lockout/Tagout (LOTO): Before any modification, completely de-energize the circuit by using a lockout/tagout procedure. This prevents accidental energization during maintenance.
- Double-Check Wiring Diagrams: Verify that the wiring diagram accurately reflects the existing circuit before making any changes.
- Use Appropriate Tools: Use insulated tools and follow proper grounding techniques to avoid electrical shock.
- Properly Label Wires: Clearly label all wires to avoid confusion and errors.
- Test Thoroughly: After modifications, thoroughly test the circuit to ensure it functions correctly and safely. Never bypass safety features.
- Consult Experts: If you're unsure about any aspect of the modification process, consult with a qualified electrician or control systems engineer.
Troubleshooting Modified Relay-Type Circuits
After making modifications, it's crucial to thoroughly test the circuit and troubleshoot any issues that might arise. Common problems include:
- Incorrect Wiring: This is a frequent cause of malfunctions. Double-check all connections and refer to the wiring diagram.
- Relay Failures: Relays can fail due to age, wear, or overload. Replace faulty relays with appropriate replacements.
- Sensor Malfunctions: Sensors might fail due to damage, aging, or environmental factors. Test and replace faulty sensors.
- Power Supply Issues: An insufficient power supply can lead to erratic operation or component damage. Verify the power supply's voltage and current capacity.
- Control Logic Errors: Incorrect implementation of the control logic can cause unexpected behavior. Review the logic diagram and verify its accuracy.
Using Ladder Logic Diagrams for Modification
Ladder logic diagrams are crucial for understanding and modifying relay-type control circuits. These diagrams visually represent the circuit's logic, allowing for easier identification of components and signal flow. When modifying a circuit, it's essential to:
- Understand the Existing Logic: Carefully examine the existing ladder logic diagram to fully grasp the circuit's operation before making any changes.
- Plan the Modifications: Develop a new ladder logic diagram reflecting the desired changes. This allows for thorough planning and minimizes errors.
- Implement the Changes: Implement the changes systematically, following the revised ladder logic diagram.
- Document the Changes: Thoroughly document all modifications, including the revised ladder logic diagram and any other relevant information.
The Transition to Modern Control Systems
While relay-type control circuits are still found in many older industrial applications, modern control systems using PLCs and other programmable devices are increasingly prevalent. Modifying existing relay circuits often presents an opportunity to consider a transition to a more modern system. PLCs offer significant advantages, including:
- Improved Flexibility: Easier to reprogram and adapt to changing process requirements.
- Enhanced Diagnostics: Provides extensive diagnostics and fault detection capabilities.
- Better Monitoring: Allows for remote monitoring and data logging.
- Increased Reliability: Modern components generally offer greater reliability.
However, transitioning to a PLC-based system is a significant undertaking requiring specialized knowledge and often involves substantial investment.
Conclusion
Modifying relay-type process control circuits requires a blend of technical expertise, systematic planning, and a strong focus on safety. Understanding the components, logic, and potential challenges is essential for successful modification. While these circuits can be effectively modified to meet evolving needs, it's crucial to prioritize safety and consider the potential benefits of transitioning to more modern, flexible control systems. Remember that meticulous planning, careful execution, and thorough testing are paramount to ensure the reliable and safe operation of the modified system.
Latest Posts
Related Post
Thank you for visiting our website which covers about Modifying Relay-type Process Control Circuits Usually Involves Changing The . We hope the information provided has been useful to you. Feel free to contact us if you have any questions or need further assistance. See you next time and don't miss to bookmark.