Match The Cost Variance Component To Its Definition
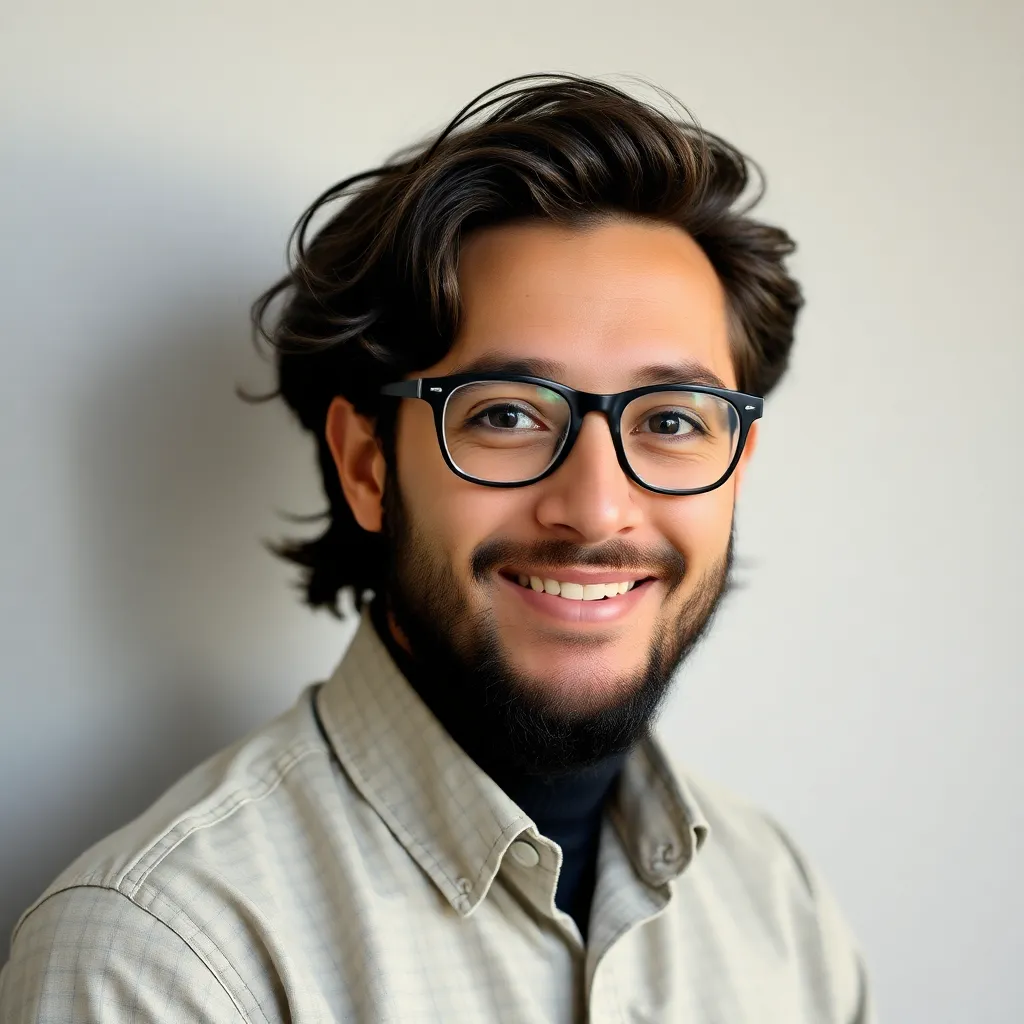
Holbox
Apr 04, 2025 · 7 min read

Table of Contents
- Match The Cost Variance Component To Its Definition
- Table of Contents
- Match the Cost Variance Component to Its Definition: A Deep Dive into Cost Accounting
- What are Cost Variances?
- Categorizing Cost Variances: A Framework
- Detailed Breakdown of Each Variance Component with Examples
- Interpreting and Utilizing Cost Variance Information
- Latest Posts
- Latest Posts
- Related Post
Match the Cost Variance Component to Its Definition: A Deep Dive into Cost Accounting
Understanding cost variances is crucial for effective business management. Whether you're a seasoned accountant or just starting to grapple with cost accounting principles, mastering the identification and interpretation of cost variances is paramount for profitability and efficient resource allocation. This comprehensive guide will meticulously explore the various components of cost variances, providing clear definitions and practical examples to solidify your understanding.
What are Cost Variances?
Cost variances represent the difference between the budgeted (or planned) cost and the actual cost incurred in a specific period. These variances can be either favorable (positive, meaning actual costs are lower than budgeted) or unfavorable (negative, meaning actual costs are higher than budgeted). Analyzing these variances helps businesses pinpoint areas of inefficiency, identify potential problems, and make informed decisions for future planning and resource allocation. Understanding the why behind the variance is just as important as identifying the variance itself.
Categorizing Cost Variances: A Framework
Cost variances are typically categorized into various components depending on the cost accounting system used. We'll focus on a widely used categorization:
-
Material Variances: These variances arise from differences between the budgeted and actual costs of direct materials used in production. They are further broken down into:
- Material Price Variance: This variance highlights the difference between the actual price paid for materials and the standard (budgeted) price. A high price variance could indicate a need to renegotiate supplier contracts or explore alternative, more cost-effective materials.
- Material Usage Variance: This variance focuses on the difference between the actual quantity of materials used and the standard (budgeted) quantity allowed for the actual output. A high usage variance might suggest inefficiencies in the production process, requiring improvements in material handling or operational techniques.
- Material Yield Variance: This variance looks at the difference between the actual yield and the expected yield from a given amount of materials. It helps to identify potential issues in the production process that might lead to material waste.
-
Labor Variances: These variances arise from differences between the budgeted and actual costs of direct labor. The breakdown is similar to material variances:
- Labor Rate Variance: This variance is the difference between the actual labor rate paid and the standard (budgeted) labor rate. This could be influenced by factors like overtime pay, increased wages, or hiring more skilled (and expensive) labor.
- Labor Efficiency Variance: This variance reflects the difference between the actual hours worked and the standard (budgeted) hours allowed for the actual output. A large unfavorable variance suggests inefficiencies in the labor process, potentially due to inadequate training, poor production planning, or machine breakdowns.
-
Variable Overhead Variances: These variances relate to the variable portion of manufacturing overhead costs. Similar to material and labor variances, we see:
- Variable Overhead Spending Variance: This variance compares the actual variable overhead costs to the budgeted variable overhead costs. This can be impacted by changes in utility prices, supply costs, or unexpected repairs.
- Variable Overhead Efficiency Variance: This variance reflects the difference between the actual hours worked (or machine hours) and the standard (budgeted) hours allowed for the actual output. It’s very similar to the labor efficiency variance, focusing on the efficiency of using variable overhead resources.
-
Fixed Overhead Variances: These variances relate to the fixed portion of manufacturing overhead costs. These are often analyzed differently due to the inherent nature of fixed costs.
- Fixed Overhead Spending Variance: The difference between the actual fixed overhead costs and the budgeted fixed overhead costs. This variance might indicate issues with budget control or unexpected expenses.
- Fixed Overhead Volume Variance: This variance is unique to fixed overhead. It compares the budgeted fixed overhead costs based on the actual level of output to the budgeted fixed overhead based on the planned level of output. It highlights the impact of differing production levels on fixed overhead costs. A significant variance might indicate underutilization of capacity.
-
Sales Variances: These variances arise from differences between the actual sales revenue and the budgeted sales revenue. While not directly a cost variance, it's closely linked to cost performance and profitability.
- Sales Price Variance: The difference between actual selling price and the budgeted selling price. This variance is influenced by market demand, competitive pricing, and sales promotions.
- Sales Volume Variance: The difference between actual sales volume and the budgeted sales volume. This reflects market demand and the effectiveness of sales and marketing strategies.
Detailed Breakdown of Each Variance Component with Examples
Let's delve deeper into each variance component with specific examples to illustrate their calculation and interpretation.
1. Material Price Variance:
- Formula: (Actual Quantity Purchased × Actual Price) – (Actual Quantity Purchased × Standard Price)
- Example: A company budgeted to purchase 10,000 units of raw material at $5 per unit. They actually purchased 12,000 units at $6 per unit.
- Material Price Variance = (12,000 × $6) – (12,000 × $5) = $12,000 (Unfavorable) This indicates that the company paid $12,000 more than budgeted due to higher material prices.
2. Material Usage Variance:
- Formula: (Standard Price × Actual Quantity Used) – (Standard Price × Standard Quantity Allowed)
- Example: Using the same example, assume the standard quantity allowed for the actual production was 11,000 units.
- Material Usage Variance = ($5 × 11,000) – ($5 × 10,000) = $5,000 (Unfavorable) This shows that 1,000 more units were used than expected.
3. Material Yield Variance: This variance is more complex and often requires more detailed production data relating to inputs and outputs.
4. Labor Rate Variance:
- Formula: (Actual Hours Worked × Actual Rate) – (Actual Hours Worked × Standard Rate)
- Example: A company budgeted for a labor rate of $20 per hour. They actually worked 500 hours at an average rate of $22 per hour.
- Labor Rate Variance = (500 × $22) – (500 × $20) = $1,000 (Unfavorable) This indicates the company paid $1,000 more than expected due to higher labor rates.
5. Labor Efficiency Variance:
- Formula: (Standard Rate × Actual Hours Worked) – (Standard Rate × Standard Hours Allowed)
- Example: Assume the standard hours allowed for the actual output was 400 hours.
- Labor Efficiency Variance = ($20 × 500) – ($20 × 400) = $2,000 (Unfavorable) This means 100 more hours were worked than expected, indicating inefficiency in labor utilization.
6. Variable Overhead Spending Variance:
- Formula: Actual Variable Overhead Costs – Budgeted Variable Overhead Costs
- Example: The company budgeted $5,000 for variable overhead. Actual costs were $6,000.
- Variable Overhead Spending Variance = $6,000 - $5,000 = $1,000 (Unfavorable)
7. Variable Overhead Efficiency Variance: This calculation mirrors the labor efficiency variance, substituting variable overhead cost drivers (e.g., machine hours) for labor hours.
8. Fixed Overhead Spending Variance:
- Formula: Actual Fixed Overhead Costs – Budgeted Fixed Overhead Costs
- Example: The company budgeted $10,000 for fixed overhead. Actual costs were $11,000.
- Fixed Overhead Spending Variance = $11,000 - $10,000 = $1,000 (Unfavorable)
9. Fixed Overhead Volume Variance:
- Formula: Budgeted Fixed Overhead – (Budgeted Fixed Overhead / Budgeted Output) × Actual Output
- Example: Assume budgeted fixed overhead was $10,000 for a budgeted output of 1,000 units. Actual output was 900 units.
- Fixed Overhead Volume Variance = $10,000 – ($10,000 / 1,000) × 900 = $1,000 (Unfavorable) This shows that the fixed overhead was under-absorbed due to lower than expected production.
10. Sales Price Variance:
- Formula: (Actual Units Sold × Actual Selling Price) – (Actual Units Sold × Budgeted Selling Price)
- Example: The company sold 1,000 units at $30 per unit, whereas the budgeted price was $35 per unit.
- Sales Price Variance = (1,000 × $30) – (1,000 × $35) = -$5,000 (Unfavorable)
11. Sales Volume Variance:
- Formula: (Actual Units Sold × Budgeted Selling Price) – (Budgeted Units Sold × Budgeted Selling Price)
- Example: The budgeted sales were 1,200 units.
- Sales Volume Variance = (1,000 × $35) – (1,200 × $35) = -$7,000 (Unfavorable)
Interpreting and Utilizing Cost Variance Information
Analyzing cost variances is only half the battle. The real value lies in understanding the reasons behind the variances. This requires investigation and often involves collaboration between different departments within the organization. For instance, a significant unfavorable material usage variance could necessitate a review of the production process, employee training programs, or even the quality of raw materials.
Effective variance analysis involves:
- Investigating root causes: Don't just identify the variance; delve into the underlying reasons. Were there supply chain disruptions? Was there equipment malfunction? Was there a lack of skilled labor?
- Implementing corrective actions: Once the root cause is identified, implement corrective actions to prevent similar variances in the future.
- Regular monitoring and review: Regularly monitor cost variances and review the effectiveness of implemented corrective actions.
- Using variance analysis for continuous improvement: Use variance analysis as a tool for continuous improvement, constantly striving for greater efficiency and cost reduction.
By systematically analyzing cost variances and addressing their root causes, businesses can significantly improve their operational efficiency, enhance profitability, and achieve a sustainable competitive advantage. This detailed understanding of cost variances is essential for informed decision-making and successful business management.
Latest Posts
Latest Posts
-
A Flexible Budget Has Which Of The Following Characteristics
Apr 08, 2025
-
Which Is True Of Providing Oral Care For Patients
Apr 08, 2025
-
If You Experience Weightlessness This Means That
Apr 08, 2025
-
Draw The Moment Diagram For The Beam
Apr 08, 2025
-
More Than Half Of The Solution To Any Problem Is
Apr 08, 2025
Related Post
Thank you for visiting our website which covers about Match The Cost Variance Component To Its Definition . We hope the information provided has been useful to you. Feel free to contact us if you have any questions or need further assistance. See you next time and don't miss to bookmark.