Manufacturing Processes For Engineering Materials 6th Edition
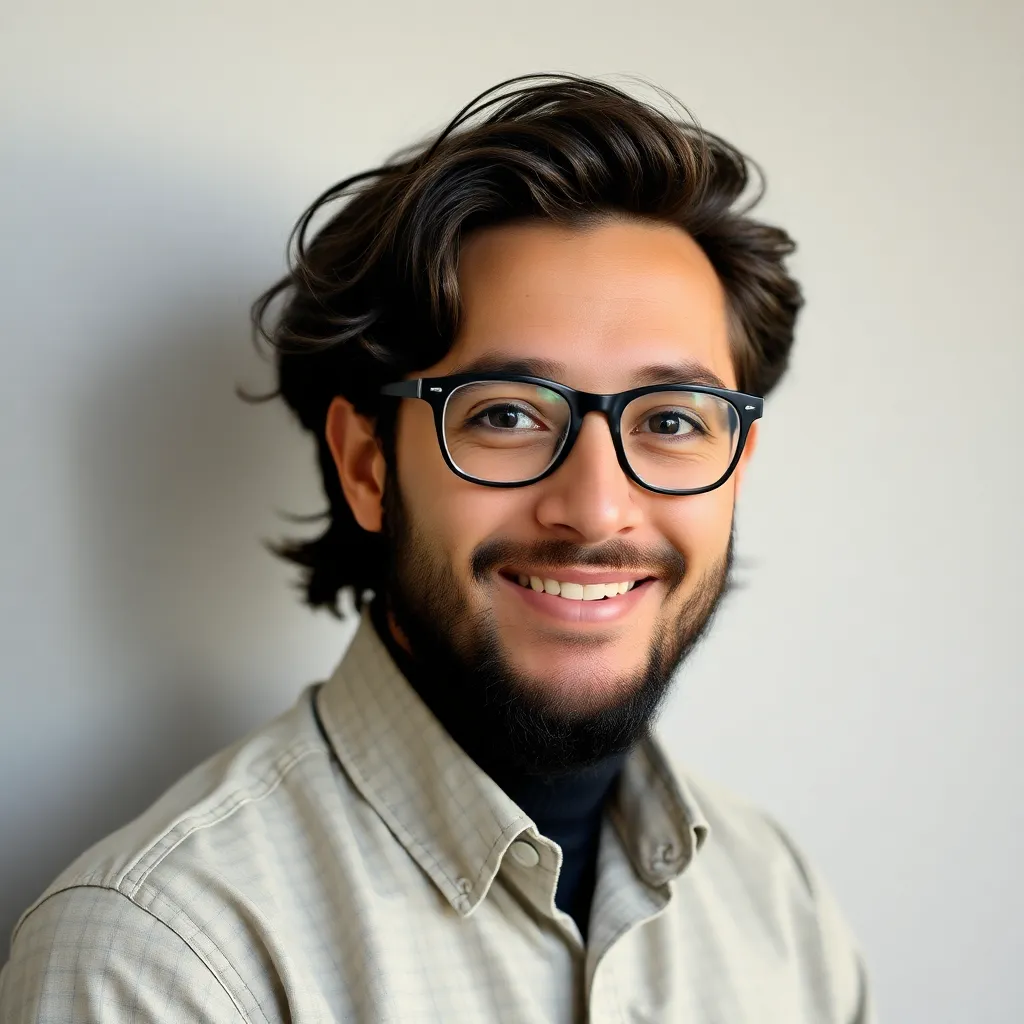
Holbox
May 11, 2025 · 7 min read
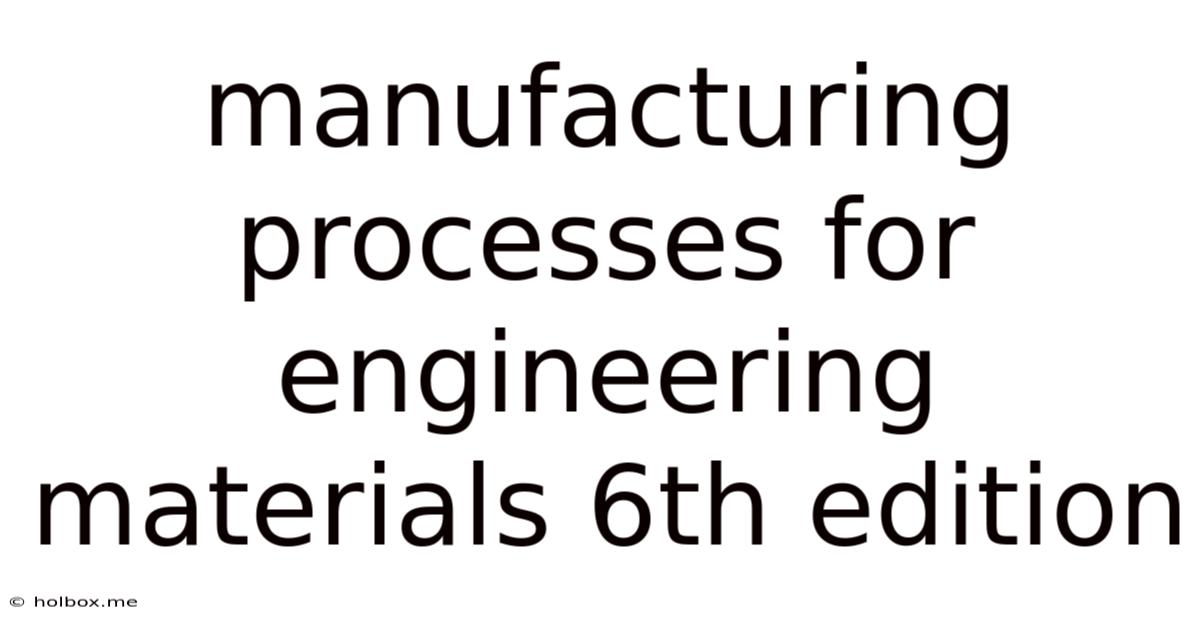
Table of Contents
- Manufacturing Processes For Engineering Materials 6th Edition
- Table of Contents
- Manufacturing Processes for Engineering Materials, 6th Edition: A Deep Dive
- Casting Processes: Shaping Materials from the Molten State
- Sand Casting: The Foundation of Casting
- Die Casting: High-Volume, High-Precision Production
- Investment Casting (Lost-Wax Casting): For Intricate Details
- Other Casting Methods: Expanding the Horizons
- Forming Processes: Shaping Materials Through Deformation
- Rolling: A Workhorse of Metal Forming
- Forging: Strengthening Materials Through Compression
- Extrusion: Producing Long, Shaped Profiles
- Drawing: Reducing the Cross-Section
- Sheet Metal Forming: Versatile Shaping Techniques
- Machining Processes: Removing Material to Achieve Precision
- Turning: Creating Cylindrical Shapes
- Milling: Generating Complex Shapes
- Drilling: Creating Holes
- Grinding: Achieving High Surface Finish
- Other Machining Processes
- Joining Processes: Connecting Materials Permanently
- Welding: Fusion of Materials
- Brazing and Soldering: Lower-Temperature Joining
- Adhesive Bonding: Joining with Adhesives
- Mechanical Fastening: Bolts, Screws, and Rivets
- Advanced Manufacturing Processes: Pushing the Boundaries
- Additive Manufacturing (3D Printing): Building Layer by Layer
- Rapid Prototyping: Accelerating Development
- Nanotechnology in Manufacturing: Miniaturizing Processes
- Conclusion: Mastering Manufacturing Processes
- Latest Posts
- Related Post
Manufacturing Processes for Engineering Materials, 6th Edition: A Deep Dive
The sixth edition of "Manufacturing Processes for Engineering Materials" remains a cornerstone text for students and professionals alike, offering a comprehensive overview of the diverse methods used to shape and transform engineering materials. This article delves into the key manufacturing processes discussed in the book, exploring their principles, applications, and the latest advancements. We'll cover topics ranging from casting and forming to machining and joining, highlighting the material properties and process parameters that influence the final product's quality and performance.
Casting Processes: Shaping Materials from the Molten State
Casting, one of the oldest manufacturing processes, involves pouring molten material into a mold, allowing it to solidify, and then removing the solidified part. This method is highly versatile, capable of producing complex shapes with intricate details, often in a single operation. The sixth edition likely expands on the various types of casting processes, including:
Sand Casting: The Foundation of Casting
Sand casting remains a prevalent method due to its simplicity and cost-effectiveness. The process uses sand molds, which are disposable, making it suitable for low-volume production. However, surface finish and dimensional accuracy might be less precise compared to other methods. The text likely details improvements in sand casting technology, including the use of resin-bonded sands and advanced mold-making techniques.
Die Casting: High-Volume, High-Precision Production
Die casting, using reusable metal molds (dies), excels in producing high-volume, high-precision parts. The high pressures involved result in superior dimensional accuracy and surface finish. The book likely discusses the two main types: hot-chamber and cold-chamber die casting, differentiating their applications based on the material being cast (e.g., zinc alloys for hot-chamber, aluminum alloys for cold-chamber).
Investment Casting (Lost-Wax Casting): For Intricate Details
Investment casting, also known as lost-wax casting, is ideal for producing intricate components with excellent surface finish. A wax pattern is created, coated with a ceramic shell, and the wax is melted out, leaving a cavity for molten metal. The shell is then destroyed after casting, hence the "lost-wax" terminology. The book likely covers advancements in ceramic shell technology and wax pattern creation techniques for improved precision and efficiency.
Other Casting Methods: Expanding the Horizons
The sixth edition probably expands on other casting methods, including:
- Centrifugal Casting: Used for producing hollow cylindrical parts with uniform wall thickness.
- Continuous Casting: An efficient process for producing long, continuous lengths of metal, frequently used in steel and aluminum production.
- Pressure Die Casting: A variation of die casting using higher pressures for improved density and mechanical properties.
Understanding the influence of various parameters – like mold design, pouring temperature, cooling rate, and alloy composition – on the final casting quality is crucial, and the book likely dedicates significant sections to this.
Forming Processes: Shaping Materials Through Deformation
Forming processes involve shaping materials by applying external forces, causing plastic deformation without melting. These processes are energy-efficient and can produce parts with excellent mechanical properties. The text likely covers a wide array of forming techniques:
Rolling: A Workhorse of Metal Forming
Rolling is a fundamental process used to reduce the thickness of metal sheets or produce bars and rods. Hot rolling and cold rolling are discussed, highlighting the differences in their applications based on the desired properties and surface finish. The book likely delves into roll design, rolling schedules, and the influence of rolling parameters on the material's microstructure and mechanical properties.
Forging: Strengthening Materials Through Compression
Forging, involving shaping metal using compressive forces, creates parts with exceptional strength and durability. The various forging methods, such as open-die forging, closed-die forging, and impression-die forging, are likely detailed, with explanations of their respective advantages and limitations. The influence of forging parameters (e.g., temperature, deformation rate) on the final microstructure and mechanical properties is an important aspect, likely covered in depth.
Extrusion: Producing Long, Shaped Profiles
Extrusion forces material through a die to produce long, shaped profiles. Hot extrusion and cold extrusion are covered, along with their respective applications. The book might discuss the design of extrusion dies, the influence of friction, and the properties of extruded products.
Drawing: Reducing the Cross-Section
Drawing involves pulling material through a die to reduce its cross-sectional area. Wire drawing, tube drawing, and rod drawing are likely explored in detail, highlighting the process parameters and their effects on the material’s properties.
Sheet Metal Forming: Versatile Shaping Techniques
Sheet metal forming encompasses a range of processes, including:
- Bending: Forming sheet metal into desired angles or curves.
- Deep Drawing: Forming cup-shaped parts from sheet metal.
- Stamping: Producing parts using punches and dies.
- Spinning: Forming axisymmetric parts by rotating a sheet metal blank against a rotating tool.
The sixth edition likely details the design of dies and tools, the selection of appropriate materials, and the influence of process parameters on the final product quality.
Machining Processes: Removing Material to Achieve Precision
Machining processes involve removing material from a workpiece using cutting tools to achieve precise dimensions and surface finishes. This section would cover the fundamental machining operations:
Turning: Creating Cylindrical Shapes
Turning involves rotating a workpiece against a cutting tool to create cylindrical shapes. Different turning operations, such as facing, chamfering, and grooving, are likely covered. The book likely emphasizes tool geometry, cutting speeds, and feed rates, and their influence on surface finish and tool life.
Milling: Generating Complex Shapes
Milling uses a rotating cutter to remove material from a workpiece, capable of producing a wide range of complex shapes. The various milling operations (e.g., face milling, end milling, peripheral milling) are likely detailed. The text would likely discuss cutter geometry, cutting parameters, and the choice of cutting fluids to optimize machining performance.
Drilling: Creating Holes
Drilling involves creating holes using a rotating drill bit. Different types of drills and drilling operations are likely explained, covering factors influencing hole quality and accuracy.
Grinding: Achieving High Surface Finish
Grinding uses abrasive wheels to remove small amounts of material, achieving high surface finish and precision. Different grinding methods (e.g., surface grinding, cylindrical grinding) are likely described, along with the selection of grinding wheels and grinding fluids.
Other Machining Processes
The book likely includes other machining operations like:
- Reaming: Enlarging and finishing holes to precise dimensions.
- Boring: Enlarging existing holes.
- Broaching: Generating internal or external shapes using a multiple-tooth cutting tool.
Joining Processes: Connecting Materials Permanently
Joining processes connect materials permanently, often crucial for creating assemblies. The sixth edition likely covers:
Welding: Fusion of Materials
Welding techniques, such as arc welding, resistance welding, and laser welding, are likely extensively covered, detailing the principles of each process and their suitability for different materials. The book likely discusses weld quality, defects, and non-destructive testing methods.
Brazing and Soldering: Lower-Temperature Joining
Brazing and soldering involve joining materials using a filler metal with a lower melting point than the base materials. The differences between brazing and soldering, along with their applications, are likely clearly explained.
Adhesive Bonding: Joining with Adhesives
Adhesive bonding uses adhesives to join materials, offering advantages in joining dissimilar materials and creating lightweight structures. The selection of appropriate adhesives and bonding processes is likely discussed.
Mechanical Fastening: Bolts, Screws, and Rivets
Mechanical fastening uses mechanical elements like bolts, screws, rivets, and pins to join parts. The selection of fasteners and their applications are likely detailed.
Advanced Manufacturing Processes: Pushing the Boundaries
The sixth edition likely includes sections on advanced manufacturing processes that are gaining traction in modern manufacturing:
Additive Manufacturing (3D Printing): Building Layer by Layer
Additive manufacturing, also known as 3D printing, builds parts layer by layer from a digital design. Different additive manufacturing techniques (e.g., fused deposition modeling (FDM), selective laser melting (SLM), stereolithography (SLA)) are likely explained, along with their capabilities and limitations.
Rapid Prototyping: Accelerating Development
Rapid prototyping techniques allow for quick creation of prototypes, facilitating faster product development cycles. The various rapid prototyping methods and their applications in different industries are likely covered.
Nanotechnology in Manufacturing: Miniaturizing Processes
The book might include a section on the applications of nanotechnology in manufacturing, including the creation of nano-structured materials and the development of nano-scale manufacturing processes.
Conclusion: Mastering Manufacturing Processes
"Manufacturing Processes for Engineering Materials, 6th Edition" equips readers with a comprehensive understanding of the vast array of manufacturing processes used to shape and transform engineering materials. By mastering these processes, engineers can optimize designs, improve product quality, and enhance manufacturing efficiency. The book's detailed explanations, combined with practical examples and illustrations, makes it an invaluable resource for students and professionals alike seeking to excel in the field of manufacturing engineering. This deep dive into the content highlights the key areas covered, emphasizing the practical applications and the latest advancements within each manufacturing process. Continuous learning and staying updated on the newest developments in this ever-evolving field are essential for success.
Latest Posts
Related Post
Thank you for visiting our website which covers about Manufacturing Processes For Engineering Materials 6th Edition . We hope the information provided has been useful to you. Feel free to contact us if you have any questions or need further assistance. See you next time and don't miss to bookmark.