Logisctix Company Had The Following Tiems
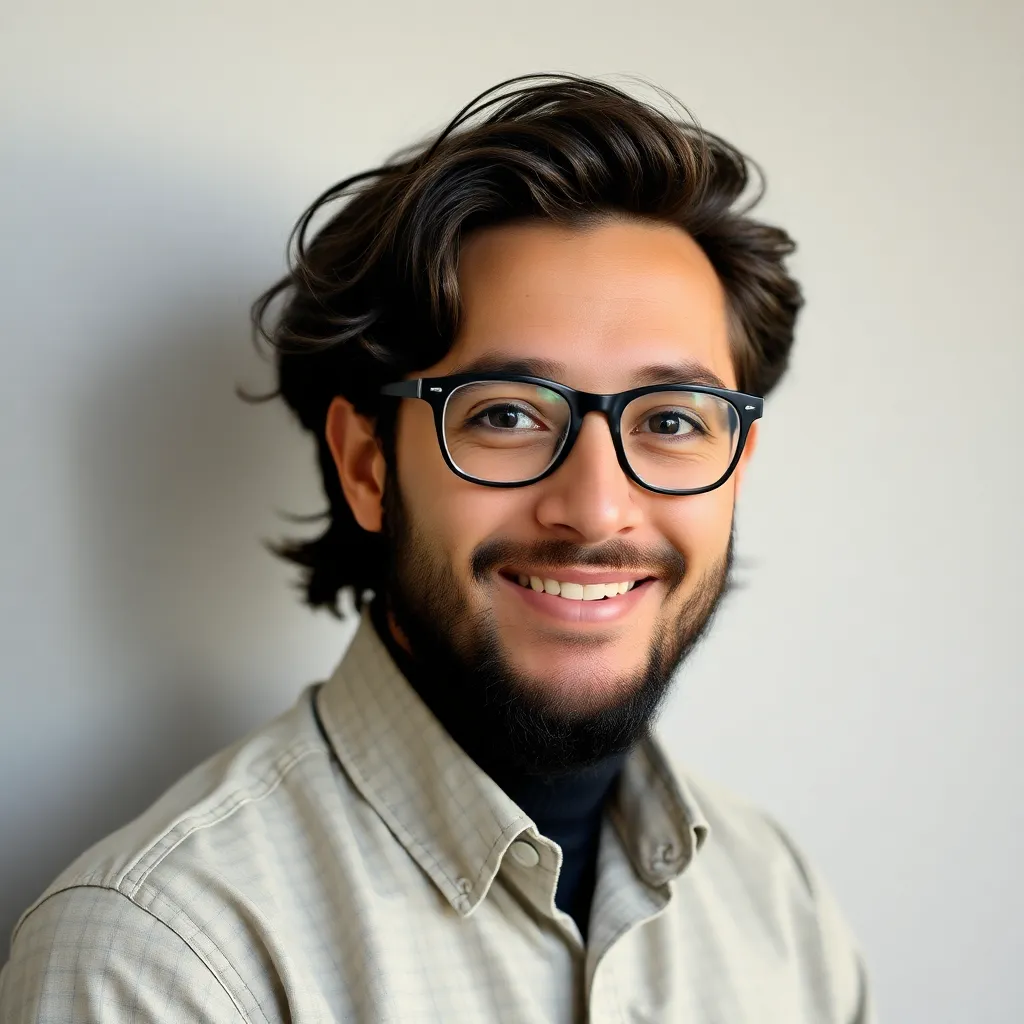
Holbox
Mar 13, 2025 · 6 min read
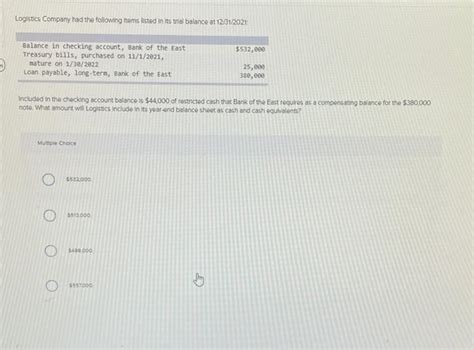
Table of Contents
- Logisctix Company Had The Following Tiems
- Table of Contents
- Logistix Company: Inventory Management and Optimization Strategies
- Understanding Logistix Company's Inventory Needs
- 1. Inventory Types:
- 2. Demand Forecasting:
- 3. Inventory Costs:
- Implementing Inventory Optimization Strategies
- 1. Economic Order Quantity (EOQ):
- 2. Just-in-Time (JIT) Inventory:
- 3. Vendor-Managed Inventory (VMI):
- 4. Safety Stock:
- 5. ABC Analysis:
- 6. Inventory Turnover Ratio:
- Technology and Automation in Inventory Management
- 1. Warehouse Management Systems (WMS):
- 2. Radio Frequency Identification (RFID):
- 3. Enterprise Resource Planning (ERP) Systems:
- 4. Demand Planning Software:
- 5. Inventory Optimization Software:
- Continuous Improvement and Monitoring
- Latest Posts
- Related Post
Logistix Company: Inventory Management and Optimization Strategies
Logistix Company, a hypothetical entity for this example, faces the common challenge of effectively managing its inventory. This article delves into various strategies Logistix can implement to optimize its inventory control, reduce costs, and improve overall efficiency. We will explore various aspects, from forecasting demand to implementing advanced technologies.
Understanding Logistix Company's Inventory Needs
Before diving into specific strategies, it's crucial to understand the specific needs of Logistix Company. This involves analyzing several key factors:
1. Inventory Types:
- Raw Materials: These are the basic inputs required for production. Understanding the lead times, storage requirements, and potential for spoilage is vital. For example, perishable raw materials need specific storage conditions and a faster turnover rate.
- Work-in-Progress (WIP): This represents partially finished goods. Effective tracking of WIP is crucial to monitor production flow and identify bottlenecks.
- Finished Goods: These are the completed products ready for sale. Efficient storage and distribution are key to minimizing warehousing costs and meeting customer demand.
- Maintenance, Repair, and Operations (MRO) Inventory: These are items used to maintain equipment and facilities. Overstocking MRO items can tie up capital, while understocking can lead to costly downtime.
2. Demand Forecasting:
Accurate demand forecasting is the cornerstone of effective inventory management. Logistix needs to utilize various forecasting techniques, including:
- Time Series Analysis: Analyzing historical sales data to identify trends and seasonality. This involves using methods like moving averages, exponential smoothing, and ARIMA models.
- Market Research: Gathering information on market trends, competitor activities, and economic indicators to refine demand forecasts.
- Sales Force Input: Leveraging the knowledge and insights of the sales team to anticipate future demand.
- Causal Forecasting: Identifying factors that influence demand, such as price changes, promotions, and economic conditions, and incorporating these into the forecast.
3. Inventory Costs:
Logistix needs a clear understanding of all associated inventory costs:
- Holding Costs: These include warehousing costs, insurance, taxes, obsolescence, and the cost of capital tied up in inventory. Minimizing holding costs is a key objective.
- Ordering Costs: These are the costs associated with placing and receiving orders, including administrative costs, transportation costs, and receiving fees.
- Stockout Costs: These are the costs associated with running out of inventory, including lost sales, customer dissatisfaction, and potential damage to brand reputation.
- Disposal Costs: These are the costs associated with disposing of obsolete or damaged inventory.
Implementing Inventory Optimization Strategies
With a solid understanding of inventory needs and costs, Logistix can implement several strategies to optimize its inventory control:
1. Economic Order Quantity (EOQ):
EOQ is a classical inventory model that determines the optimal order quantity to minimize the total inventory costs. Logistix can use this model to determine the ideal order size for each item, balancing ordering costs and holding costs. However, the basic EOQ model makes several assumptions (constant demand, instantaneous replenishment) that may not hold true in reality. More advanced models should be considered.
2. Just-in-Time (JIT) Inventory:
JIT aims to minimize inventory levels by receiving materials only when needed for production. This requires close collaboration with suppliers and a highly efficient production process. JIT can significantly reduce holding costs, but it increases the risk of stockouts if there are disruptions in the supply chain.
3. Vendor-Managed Inventory (VMI):
VMI involves delegating the management of inventory to a supplier. The supplier is responsible for monitoring inventory levels, placing orders, and ensuring timely delivery. This frees up Logistix's resources and can lead to improved efficiency, but it requires a high degree of trust and collaboration with the supplier.
4. Safety Stock:
Safety stock is the extra inventory kept on hand to buffer against unexpected demand fluctuations or supply chain disruptions. Determining the appropriate level of safety stock requires careful analysis of demand variability and lead times. Excessive safety stock ties up capital, while insufficient safety stock increases the risk of stockouts.
5. ABC Analysis:
ABC analysis classifies inventory items into three categories (A, B, and C) based on their value and consumption. A-items are high-value items that represent a small percentage of the total number of items but a large percentage of the total value. B-items are medium-value items, and C-items are low-value items. Logistix can focus its inventory management efforts on A-items, which have the greatest impact on overall inventory costs.
6. Inventory Turnover Ratio:
The inventory turnover ratio measures how efficiently Logistix is selling its inventory. A high turnover ratio indicates efficient inventory management, while a low turnover ratio suggests excess inventory. Logistix should regularly monitor this ratio and identify opportunities to improve inventory turnover.
Technology and Automation in Inventory Management
Technology plays a crucial role in modern inventory management. Logistix can leverage various technologies to improve efficiency and accuracy:
1. Warehouse Management Systems (WMS):
WMS software automates various inventory management tasks, including receiving, putaway, picking, packing, and shipping. WMS provides real-time visibility into inventory levels and location, enabling better decision-making.
2. Radio Frequency Identification (RFID):
RFID tags can be attached to inventory items to track their movement throughout the supply chain. RFID provides more accurate and real-time inventory data than barcodes.
3. Enterprise Resource Planning (ERP) Systems:
ERP systems integrate various business functions, including inventory management, finance, and human resources. ERP systems provide a holistic view of the business and improve coordination across different departments.
4. Demand Planning Software:
Demand planning software uses advanced forecasting techniques to predict future demand with greater accuracy. This enables Logistix to optimize inventory levels and reduce stockouts.
5. Inventory Optimization Software:
This software uses sophisticated algorithms to optimize inventory levels, considering various factors such as demand variability, lead times, and service levels.
Continuous Improvement and Monitoring
Effective inventory management is not a one-time project but an ongoing process. Logistix needs to establish a system for continuous improvement and monitoring:
- Regular Inventory Audits: Conducting periodic physical inventory counts to verify inventory accuracy and identify discrepancies.
- Performance Metrics: Tracking key performance indicators (KPIs), such as inventory turnover ratio, stockout rate, and inventory holding costs, to monitor progress and identify areas for improvement.
- Regular Review of Forecasting Methods: Regularly evaluating the accuracy of demand forecasts and adjusting forecasting methods as needed.
- Collaboration and Communication: Fostering strong communication and collaboration between different departments, including purchasing, production, and sales, to ensure effective inventory management.
- Supplier Relationship Management: Building strong relationships with key suppliers to ensure reliable supply and reduce lead times.
By implementing these strategies and leveraging technology, Logistix Company can significantly improve its inventory management, reducing costs, increasing efficiency, and improving customer service. Remember that the optimal strategy will depend on the specific circumstances of the company, and a tailored approach is crucial for success. Continuous monitoring, adaptation, and a commitment to improvement are key to long-term success in inventory management.
Latest Posts
Related Post
Thank you for visiting our website which covers about Logisctix Company Had The Following Tiems . We hope the information provided has been useful to you. Feel free to contact us if you have any questions or need further assistance. See you next time and don't miss to bookmark.