Inventory Recoreds For Herbs Chemicals Revealed Fifo
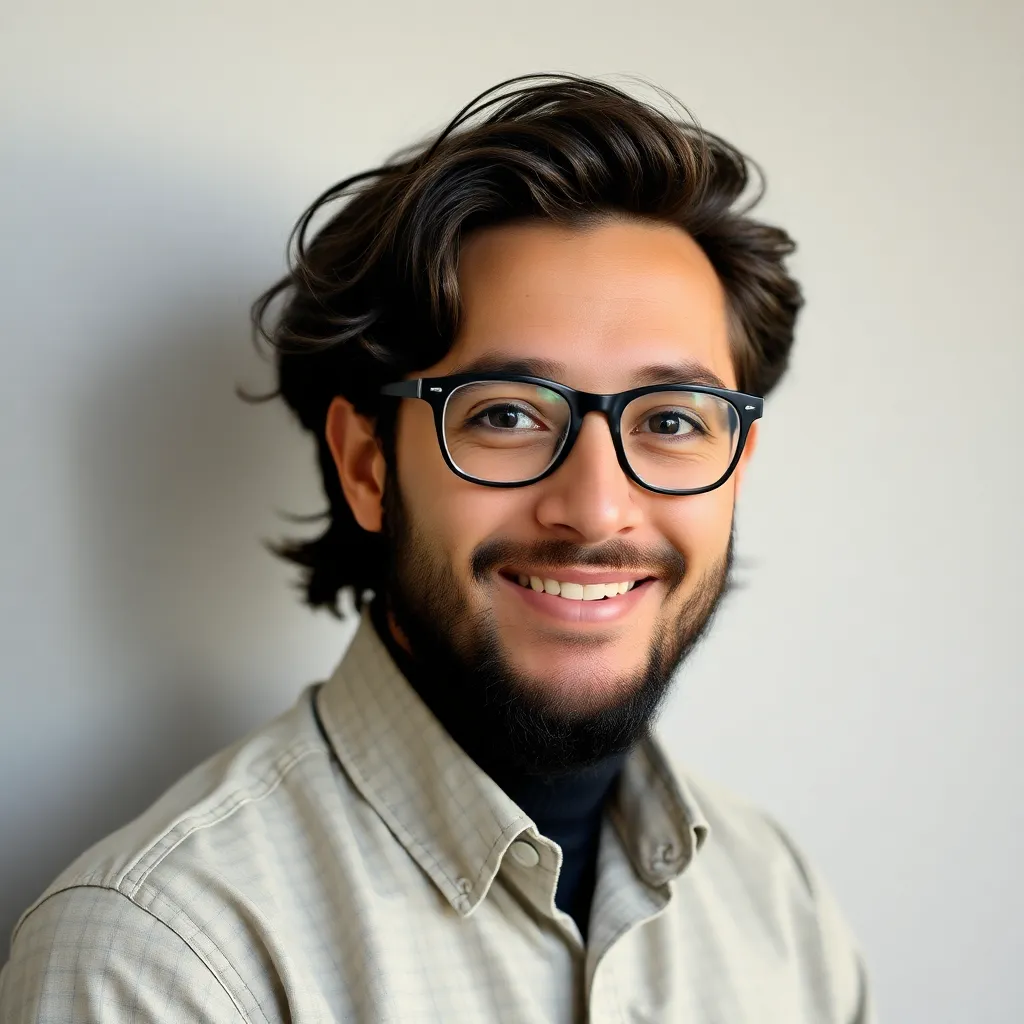
Holbox
Mar 13, 2025 · 7 min read
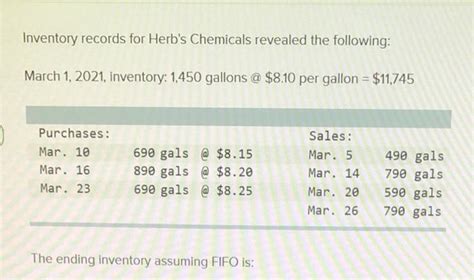
Table of Contents
- Inventory Recoreds For Herbs Chemicals Revealed Fifo
- Table of Contents
- Inventory Records for Herbs & Chemicals: Unveiling the FIFO Method
- Understanding FIFO (First-In, First-Out)
- Maintaining Accurate Inventory Records: Best Practices
- FIFO Calculations and Cost of Goods Sold (COGS)
- Comparing FIFO with Other Inventory Costing Methods
- Advanced Considerations for Herbs and Chemicals
- Conclusion
- Latest Posts
- Related Post
Inventory Records for Herbs & Chemicals: Unveiling the FIFO Method
Accurate inventory management is crucial for any business dealing with herbs and chemicals, whether you're a small-scale herbalist, a large-scale pharmaceutical manufacturer, or anywhere in between. The nature of these materials – their potential for degradation, varying shelf lives, and stringent regulatory requirements – necessitates meticulous record-keeping. Among several inventory costing methods, the First-In, First-Out (FIFO) method stands out as a popular and often preferred choice due to its advantages in managing perishable goods and aligning with generally accepted accounting principles (GAAP). This comprehensive guide delves into the intricacies of inventory records for herbs and chemicals, focusing on the FIFO method.
Understanding FIFO (First-In, First-Out)
FIFO operates on the simple principle: the oldest inventory items are sold or used first. This is particularly vital for herbs and chemicals, many of which have expiration dates or a limited shelf life. By using the oldest stock first, businesses minimize the risk of spoilage, waste, and potential losses associated with expired or degraded materials.
Key Advantages of FIFO for Herbs and Chemicals:
- Minimizes Spoilage and Waste: FIFO ensures that items nearing their expiration dates are utilized before they spoil, reducing waste and saving money. This is especially critical for herbs that lose their potency over time.
- Improved Product Quality: Using older stock first guarantees that customers receive products made with fresher ingredients, enhancing product quality and customer satisfaction.
- Compliance with Regulations: Many industries regulating herbs and chemicals have specific guidelines regarding inventory management and expiration dates. FIFO helps businesses meet these regulatory requirements effortlessly.
- Accurate Cost of Goods Sold (COGS): FIFO provides a more accurate reflection of the cost of goods sold, as it utilizes the actual cost of the oldest inventory items. This leads to more precise financial reporting.
- Simple Implementation: While sophisticated inventory management software can automate the process, FIFO itself is relatively straightforward to implement, even with manual systems.
Maintaining Accurate Inventory Records: Best Practices
Maintaining accurate inventory records is paramount to successfully implementing the FIFO method. The following best practices ensure effective tracking and management:
1. Detailed Inventory Tracking System: Employ a robust inventory tracking system, whether it's a simple spreadsheet, dedicated inventory management software, or a combination of both. This system should track the following crucial details for each herb and chemical:
- Item Name and Description: Include a precise and unambiguous description of each item, including botanical names for herbs and precise chemical formulas.
- Quantity: Keep a real-time record of the quantity on hand for each item.
- Batch Number or Lot Number: Assigning a unique batch number to each incoming shipment allows for precise tracking of the items' origin, manufacturing date, and expiration date.
- Purchase Date: The date when the item was acquired is crucial for FIFO calculations.
- Expiration Date: Record the expiration date clearly. This is essential for managing shelf life.
- Storage Location: Knowing the storage location helps in quick retrieval and prevents mix-ups.
- Cost per Unit: Record the cost of each unit at the time of purchase.
- Incoming and Outgoing Records: Maintain detailed records of every item received and every item used or sold.
2. Regular Physical Inventory Counts: Conduct regular physical inventory counts to verify the accuracy of your records. Discrepancies between the recorded inventory and physical counts should be investigated and reconciled promptly. This helps identify potential issues like theft, damage, or inaccurate record-keeping.
3. Implement a "First-In, First-Out" Picking Strategy: When fulfilling orders or using inventory for production, always prioritize using the oldest items first. Clear labeling and organized storage contribute significantly to this process. A clear system of labeling with dates and batch numbers is crucial here.
4. Employing Barcode or RFID Technology: For larger businesses, barcode or RFID (Radio-Frequency Identification) technology can significantly streamline inventory management. These technologies offer faster and more accurate data capture, minimizing human error and enhancing efficiency.
5. Using Inventory Management Software: Investing in inventory management software offers significant benefits for businesses of all sizes. These software solutions typically include features for automated tracking, reporting, and analysis, simplifying FIFO implementation and improving overall efficiency.
FIFO Calculations and Cost of Goods Sold (COGS)
Calculating the cost of goods sold (COGS) using FIFO is relatively straightforward. Let's illustrate with an example:
Suppose a company uses lavender essential oil in its production. Here's their inventory record:
- Batch A: 10 liters purchased on January 15th, cost $20/liter
- Batch B: 15 liters purchased on February 20th, cost $22/liter
- Batch C: 20 liters purchased on March 10th, cost $25/liter
The company uses 25 liters of lavender essential oil in March. Using FIFO:
- The first 10 liters are from Batch A (oldest): 10 liters * $20/liter = $200
- The remaining 15 liters are from Batch B: 15 liters * $22/liter = $330
- Total COGS for March: $200 + $330 = $530
This calculation assumes the assumption of a continuous flow of inventory. If there were discrete sales transactions, the calculations could be more granular, tracking the cost for each specific transaction.
The advantage of FIFO in this scenario is clear: it reflects the actual cost of the oils used and avoids overstating profits by using current inflated prices.
Comparing FIFO with Other Inventory Costing Methods
While FIFO is often favored, it's important to understand other inventory costing methods and their implications:
1. Last-In, First-Out (LIFO): LIFO assumes the newest items are sold first. This method can be beneficial in times of inflation, as it lowers COGS and increases reported profits. However, it can also lead to an inaccurate reflection of the actual cost of goods sold and is less commonly used for perishable goods. It is not permitted under IFRS (International Financial Reporting Standards).
2. Weighted-Average Cost: This method calculates the average cost of all inventory items and assigns that average cost to each item sold. It simplifies calculations but may not accurately reflect the actual cost of goods sold, especially when dealing with significant price fluctuations.
Advanced Considerations for Herbs and Chemicals
Beyond the basic principles of FIFO, several advanced considerations apply specifically to managing inventories of herbs and chemicals:
1. Shelf-Life Management: Implementing a robust system for tracking and managing shelf life is crucial. This requires careful monitoring of expiration dates, appropriate storage conditions, and regular rotation of inventory to minimize spoilage.
2. Quality Control: Regular quality checks are essential to ensure that herbs and chemicals maintain their potency and purity throughout their shelf life. This may involve testing for contaminants or assessing the chemical composition of the products.
3. Regulatory Compliance: Many herbs and chemicals are subject to stringent regulations concerning storage, handling, and disposal. Businesses must adhere to all applicable regulations to avoid penalties and maintain a safe and compliant operation. This often includes meticulous record-keeping and documentation.
4. Traceability: The ability to trace the origin and history of each herb or chemical is important for both quality control and regulatory compliance. Detailed records of batch numbers, suppliers, and handling procedures should be kept for auditing purposes.
5. Waste Management: Proper disposal of expired or unusable herbs and chemicals is crucial for environmental protection and compliance with regulations. Establish protocols for the safe and environmentally sound disposal of these materials.
Conclusion
Effective inventory management is not just about accurate record-keeping; it's a fundamental aspect of ensuring product quality, regulatory compliance, and financial success. The FIFO method, with its focus on utilizing older stock first, is particularly well-suited for managing herbs and chemicals. By adopting the best practices outlined in this guide, businesses can optimize their inventory management processes, minimize waste and losses, and build a robust foundation for long-term growth and sustainability. The implementation of a comprehensive inventory system, combined with regular physical checks, and the use of appropriate software, will allow for accurate accounting and efficient business operations. Remember, investing in a well-structured inventory system for herbs and chemicals is an investment in the future of your business.
Latest Posts
Related Post
Thank you for visiting our website which covers about Inventory Recoreds For Herbs Chemicals Revealed Fifo . We hope the information provided has been useful to you. Feel free to contact us if you have any questions or need further assistance. See you next time and don't miss to bookmark.