Inventory Record Accuracy Would Be Decreased By
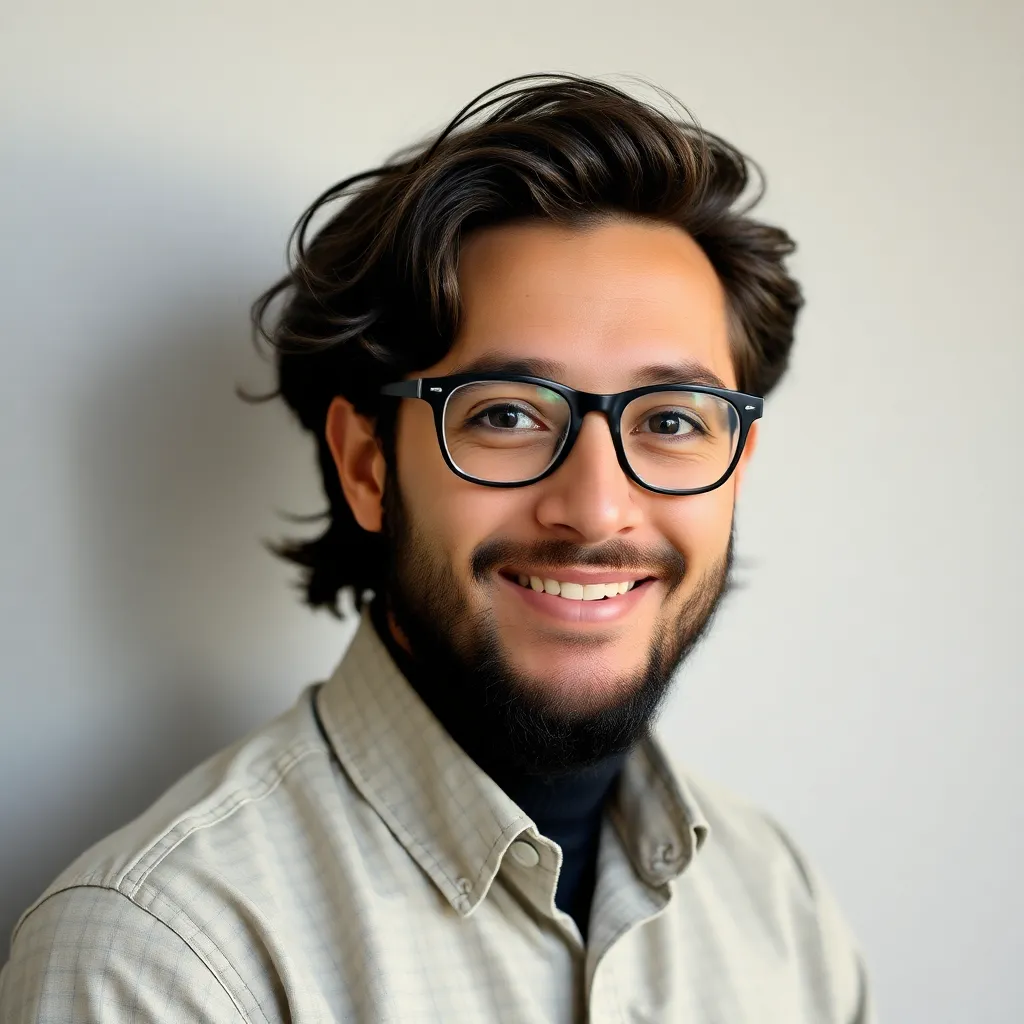
Holbox
Apr 07, 2025 · 6 min read

Table of Contents
- Inventory Record Accuracy Would Be Decreased By
- Table of Contents
- Inventory Record Accuracy: Factors Leading to Inaccuracies and Mitigation Strategies
- Primary Factors Decreasing Inventory Record Accuracy
- 1. Human Error: The Biggest Culprit
- 2. System-Related Issues: Technological Glitches and Limitations
- 3. Process-Related Inefficiencies: Gaps in Procedures and Practices
- 4. External Factors: Beyond Internal Control
- Mitigation Strategies: Improving Inventory Record Accuracy
- 1. Implementing Robust Inventory Management Systems
- 2. Improving Internal Processes and Procedures
- 3. Enhancing Staff Training and Communication
- 4. Leveraging Technology
- 5. Addressing External Factors
- Latest Posts
- Latest Posts
- Related Post
Inventory Record Accuracy: Factors Leading to Inaccuracies and Mitigation Strategies
Maintaining accurate inventory records is crucial for any business, regardless of size or industry. Accurate records directly impact profitability, customer satisfaction, and overall operational efficiency. When inventory record accuracy decreases, it creates a ripple effect of negative consequences. Let's delve into the key factors contributing to inaccuracies and explore effective mitigation strategies.
Primary Factors Decreasing Inventory Record Accuracy
Several factors can contribute to decreased inventory record accuracy. These can be broadly categorized into:
1. Human Error: The Biggest Culprit
Human error is arguably the most significant contributor to inventory record inaccuracies. This encompasses a wide range of mistakes, including:
- Data Entry Errors: Incorrectly entering data during stock receipts, transfers, or sales transactions is a common issue. This includes typos, incorrect quantity entries, or using the wrong product codes.
- Counting Errors: Manual stocktaking, while necessary, is prone to human error. Fatigue, distraction, or lack of proper training can lead to miscounting items.
- Mislabeling: Incorrectly labeling products or storage locations can lead to confusion and inaccurate records.
- Lack of Training: Inadequate training for staff responsible for inventory management can result in inconsistent procedures and increased error rates.
- Poor Communication: Ineffective communication between different departments or individuals involved in inventory management can lead to discrepancies and inaccuracies.
2. System-Related Issues: Technological Glitches and Limitations
Technology plays a crucial role in inventory management, but technological issues can significantly impact accuracy:
- Outdated Inventory Management Systems (IMS): Using outdated or poorly designed IMS can lead to various problems, including data corruption, integration issues with other systems, and a lack of real-time visibility.
- Software Bugs and Glitches: Software bugs can lead to inaccurate data recording, missing data, or incorrect calculations.
- System Integration Problems: Problems with integrating the IMS with other business systems, such as point-of-sale (POS) or enterprise resource planning (ERP) systems, can cause discrepancies in inventory data.
- Lack of Data Backup and Recovery: Failure to regularly back up inventory data can result in significant data loss in case of system crashes or hardware failures.
- Insufficient System Security: Lack of proper security measures can lead to unauthorized access and manipulation of inventory data, compromising accuracy.
3. Process-Related Inefficiencies: Gaps in Procedures and Practices
Inefficient processes also contribute to inaccuracy:
- Lack of Standardized Procedures: The absence of clear, documented, and consistently followed inventory procedures leads to inconsistencies and errors.
- Inadequate Stocktaking Practices: Infrequent or improperly conducted physical stocktakes mean discrepancies between physical inventory and recorded inventory are not detected and corrected promptly.
- Poor Organization and Storage: A disorganized warehouse or storage area makes it difficult to locate items, leading to inaccurate counts and increased risk of damage or loss.
- Lack of Cycle Counting: Cycle counting, which involves regularly counting a small subset of inventory, is an effective way to identify and correct errors early. The lack of this practice allows small errors to accumulate.
- Inefficient Receiving and Shipping Processes: Errors during the receiving and shipping process, such as failing to properly scan barcodes or verify quantities, directly impact inventory accuracy.
4. External Factors: Beyond Internal Control
External factors can also influence inventory record accuracy:
- Theft and Shrinkage: Theft or shrinkage (losses due to damage, spoilage, or obsolescence) can lead to significant discrepancies between physical inventory and recorded inventory.
- Supplier Errors: Errors made by suppliers, such as incorrect shipments or inaccurate product information, can affect the accuracy of inventory records.
- Natural Disasters and Other Unforeseen Events: Natural disasters or other unexpected events can damage inventory and disrupt operations, impacting record accuracy.
- Damaged Goods: Goods that are damaged during transit or storage may not be properly accounted for, leading to inaccuracies.
- Obsolescence: Products that become obsolete or outdated can remain in inventory, leading to inaccurate reporting of available stock.
Mitigation Strategies: Improving Inventory Record Accuracy
Addressing the factors that contribute to inaccuracies requires a multi-faceted approach involving process improvements, technological upgrades, and employee training.
1. Implementing Robust Inventory Management Systems
Investing in a modern, reliable IMS is crucial. The system should:
- Provide Real-Time Visibility: Offer real-time tracking of inventory levels, location, and movement.
- Integrate with Other Systems: Seamlessly integrate with POS, ERP, and other relevant systems to eliminate data silos.
- Support Barcode or RFID Tracking: Enable efficient tracking of individual items using barcodes or Radio Frequency Identification (RFID) tags.
- Offer Data Analytics and Reporting: Provide comprehensive reports and dashboards to identify trends, patterns, and potential problem areas.
- Include robust security features: Protect against unauthorized access and data manipulation.
2. Improving Internal Processes and Procedures
Streamlining internal processes is essential:
- Develop Standardized Procedures: Create clear, documented, and consistently followed procedures for all inventory-related activities, including receiving, storage, picking, packing, and shipping.
- Implement Cycle Counting: Regularly conduct cycle counts to identify and correct discrepancies early, preventing them from accumulating.
- Enhance Stocktaking Procedures: Implement robust stocktaking procedures, including proper training for staff, clear instructions, and verification processes.
- Improve Warehouse Organization: Optimize warehouse layout and organization to improve efficiency and reduce the risk of misplacing items.
- Conduct Regular Audits: Perform regular audits of inventory records and procedures to identify and address potential problems.
3. Enhancing Staff Training and Communication
Investing in employee training is crucial:
- Provide Comprehensive Training: Train staff responsible for inventory management on proper procedures, data entry techniques, and the use of inventory management systems.
- Encourage Cross-Training: Train staff in multiple aspects of inventory management to improve flexibility and reduce reliance on individual employees.
- Improve Communication: Establish clear communication channels between different departments and individuals involved in inventory management to ensure consistency and accuracy.
- Implement regular feedback mechanisms: Encourage staff to report potential errors and inefficiencies.
- Reward accurate work: Recognize and reward staff for maintaining accurate inventory records.
4. Leveraging Technology
Technology can significantly improve accuracy:
- Utilize Barcode or RFID Technology: Implement barcode or RFID systems for efficient tracking of individual items. This minimizes manual data entry and reduces the likelihood of human errors.
- Automate Data Entry: Automate data entry wherever possible to reduce manual input and associated errors.
- Use Mobile Devices: Equip staff with mobile devices for real-time inventory updates and tracking.
- Employ Data Analytics: Use data analytics to identify patterns and trends in inventory data, helping to pinpoint areas needing improvement.
- Implement Cloud-Based Solutions: Cloud-based systems provide increased accessibility, improved security, and enhanced scalability.
5. Addressing External Factors
Managing external factors requires a proactive approach:
- Build Strong Relationships with Suppliers: Establish strong relationships with suppliers to minimize errors in shipments and ensure timely delivery.
- Implement Security Measures: Implement robust security measures to prevent theft and shrinkage, including surveillance cameras, access controls, and employee background checks.
- Regularly review and update inventory: Regularly check for damaged or obsolete goods to maintain accuracy.
- Develop contingency plans: Develop plans to mitigate the impact of natural disasters or other unexpected events on inventory.
- Implement robust quality control measures: Check the quality of incoming goods upon delivery to ensure they meet specifications.
By implementing these strategies, businesses can significantly improve inventory record accuracy, leading to increased profitability, enhanced customer satisfaction, and improved operational efficiency. The investment in improved processes, technology, and training is crucial for long-term success and competitive advantage. Remember, the goal is not just to identify errors but to build a system that minimizes their occurrence in the first place.
Latest Posts
Latest Posts
-
Which Italian Insects Often Fall In Love
Apr 14, 2025
-
A Production Manager At A Pottery Factory
Apr 14, 2025
-
To Encourage Entrepreneurial Growth Governments Might
Apr 14, 2025
-
Optimistic People View Challenges As Opportunities To Influence Decisions
Apr 14, 2025
-
Label The Abdominal Contents Using The Hints If Provided
Apr 14, 2025
Related Post
Thank you for visiting our website which covers about Inventory Record Accuracy Would Be Decreased By . We hope the information provided has been useful to you. Feel free to contact us if you have any questions or need further assistance. See you next time and don't miss to bookmark.