From The Plot Of Yield Strength Versus
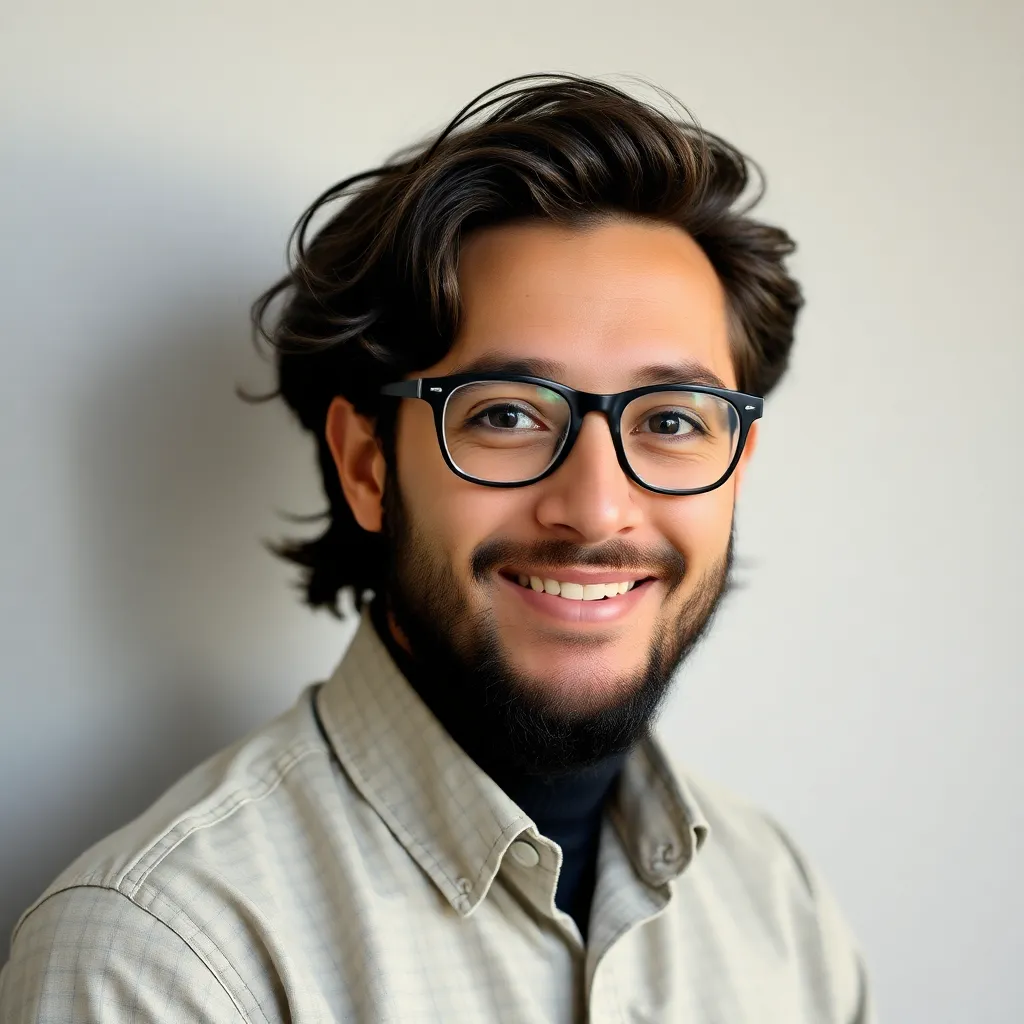
Holbox
Mar 28, 2025 · 6 min read
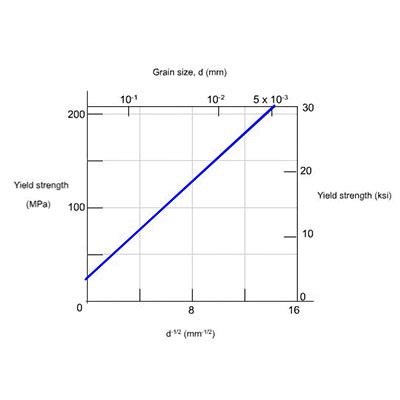
Table of Contents
- From The Plot Of Yield Strength Versus
- Table of Contents
- From the Plot of Yield Strength Versus…: Unveiling Material Behavior
- Understanding Yield Strength
- Yield Strength vs. Strain: The Fundamental Plot
- What the Plot Reveals:
- Yield Strength vs. Temperature: Understanding Thermal Effects
- What the Plot Reveals:
- Yield Strength vs. Grain Size: The Hall-Petch Relation
- What the Plot Reveals:
- Yield Strength vs. Strain Rate: The Effect of Loading Speed
- What the Plot Reveals:
- Yield Strength vs. Alloying Composition: The Impact of Additives
- What the Plot Reveals:
- Yield Strength vs. Cold Work: The Effects of Plastic Deformation
- What the Plot Reveals:
- Conclusion: The Importance of Yield Strength Plots
- Latest Posts
- Latest Posts
- Related Post
From the Plot of Yield Strength Versus…: Unveiling Material Behavior
Understanding the mechanical properties of materials is crucial in engineering design. A fundamental aspect of this understanding comes from analyzing stress-strain curves, particularly focusing on the yield strength. This article delves deep into the significance of yield strength and how its relationship with other parameters, depicted in various plots, provides invaluable insights into material behavior. We'll explore different plots involving yield strength, examining the information they reveal about a material's ductility, brittleness, and overall suitability for specific applications.
Understanding Yield Strength
Before we dive into the intricacies of plots, let's establish a firm understanding of yield strength. Yield strength represents the stress at which a material begins to deform plastically. This means that once the stress exceeds the yield strength, the deformation becomes permanent; the material will not return to its original shape upon removal of the load. This is a critical point in material selection, as it dictates the limit of elastic deformation. Engineers must ensure that the stress applied to a component in service remains below its yield strength to avoid permanent deformation and potential failure.
The yield strength is typically determined from a stress-strain curve obtained through a tensile test. The curve shows the relationship between the applied stress and the resulting strain in a material. The yield point is often identified by the intersection of a line parallel to the elastic portion of the curve (usually at 0.2% offset) and the stress-strain curve itself. This is known as the 0.2% offset yield strength. Other methods include identifying the point where the curve deviates from linear elasticity.
Yield Strength vs. Strain: The Fundamental Plot
The most basic and crucial plot is the stress-strain curve itself. This graph directly visualizes the relationship between applied stress and resulting strain. The yield strength is prominently featured on this curve, marking the transition from elastic to plastic deformation.
What the Plot Reveals:
-
Elastic Modulus (Young's Modulus): The slope of the linear elastic portion of the curve represents the elastic modulus, a measure of a material's stiffness or resistance to elastic deformation. A steeper slope indicates a stiffer material.
-
Yield Strength: As discussed, this is the point where plastic deformation begins. Its value is critical for design considerations.
-
Tensile Strength (Ultimate Tensile Strength): The highest point on the stress-strain curve represents the ultimate tensile strength, the maximum stress the material can withstand before failure.
-
Ductility: The elongation to fracture, or the total strain at failure, provides a measure of the material's ductility – its ability to deform plastically before fracturing. A larger elongation signifies greater ductility.
-
Brittleness: Conversely, a material with a small elongation before fracture is considered brittle. Brittle materials exhibit minimal plastic deformation before failure.
Yield Strength vs. Temperature: Understanding Thermal Effects
Temperature significantly impacts the mechanical properties of materials. Plotting yield strength versus temperature allows us to observe this relationship and understand how a material's strength changes with varying temperatures. This is particularly important in applications involving high or low temperatures.
What the Plot Reveals:
-
Temperature Dependence of Yield Strength: Most materials exhibit a decrease in yield strength with increasing temperature. This is because higher temperatures increase atomic mobility, facilitating dislocation movement and making plastic deformation easier. However, some materials may show anomalous behavior depending on their microstructure and composition.
-
Creep Behavior: This plot can also provide insights into a material's susceptibility to creep, a time-dependent deformation at elevated temperatures under sustained stress. A steep drop in yield strength at higher temperatures suggests a greater susceptibility to creep.
-
Design Considerations for High-Temperature Applications: This plot is essential for selecting materials suitable for high-temperature environments. The material's yield strength at the operating temperature needs to be sufficient to resist the applied stresses.
Yield Strength vs. Grain Size: The Hall-Petch Relation
The Hall-Petch relation describes the relationship between yield strength and grain size in polycrystalline materials. Smaller grain sizes generally result in higher yield strengths. Plotting yield strength against the inverse square root of the grain size illustrates this relationship.
What the Plot Reveals:
-
Grain Boundary Strengthening: Grain boundaries act as barriers to dislocation motion. Finely grained materials have more grain boundaries per unit volume, increasing the resistance to plastic deformation and hence increasing the yield strength. This is the essence of grain boundary strengthening.
-
Hall-Petch Slope: The slope of the line in the plot gives the Hall-Petch slope, a material constant that reflects the effectiveness of grain boundaries in impeding dislocation movement.
-
Controlling Material Properties Through Grain Size: This relationship shows how controlling the grain size during material processing can be used to tailor the material's strength. Techniques like cold working or heat treatments can modify the grain size and consequently the yield strength.
Yield Strength vs. Strain Rate: The Effect of Loading Speed
The speed at which a load is applied also affects the material's response. A plot of yield strength versus strain rate reveals this dependence.
What the Plot Reveals:
-
Strain Rate Sensitivity: Materials often exhibit strain rate sensitivity, meaning their yield strength increases with increasing strain rate. This occurs because at higher strain rates, there is less time for dislocations to move and rearrange, requiring a higher stress to initiate plastic deformation.
-
Dynamic Loading: This plot is crucial in understanding material behavior under dynamic or impact loading conditions, like those experienced in accidents or explosive events. Materials need to possess sufficient strength at high strain rates to withstand such loads without failure.
Yield Strength vs. Alloying Composition: The Impact of Additives
Adding alloying elements can significantly alter the properties of a material, including its yield strength. Plotting yield strength versus alloying composition provides valuable insight into how different elements affect the strength.
What the Plot Reveals:
-
Solid Solution Strengthening: Alloying elements can occupy interstitial or substitutional positions in the crystal lattice, hindering dislocation motion and thereby increasing yield strength. This is known as solid solution strengthening.
-
Precipitation Hardening: Some alloying elements can form precipitates within the material. These precipitates act as obstacles to dislocation movement, leading to a significant increase in yield strength. This is a common method for strengthening many alloys.
-
Optimal Alloy Composition: The plot can help determine the optimal alloying composition to achieve a desired yield strength, balancing strength with other desirable properties like ductility and corrosion resistance.
Yield Strength vs. Cold Work: The Effects of Plastic Deformation
Cold working, or plastic deformation at room temperature, changes the microstructure of a material, influencing its yield strength. Plotting yield strength versus the amount of cold work helps to understand this phenomenon.
What the Plot Reveals:
-
Work Hardening (Strain Hardening): Cold working increases the dislocation density within the material, leading to increased resistance to further deformation. This is known as work hardening or strain hardening, resulting in a higher yield strength.
-
Annealing: The plot also shows that annealing (heat treatment) can reduce the yield strength to its pre-cold-worked level by allowing the dislocations to rearrange and recover.
Conclusion: The Importance of Yield Strength Plots
Analyzing different plots involving yield strength is fundamental to understanding material behavior and selecting appropriate materials for specific engineering applications. These plots provide valuable information about the material's strength, ductility, brittleness, temperature dependence, response to strain rate, and the effects of alloying and cold work. This knowledge is indispensable for engineers to design reliable and safe structures and components. The ability to interpret these plots empowers informed decision-making and facilitates the development of advanced materials with tailored properties. By carefully considering these relationships, engineers can optimize designs and ensure the structural integrity and longevity of their creations.
Latest Posts
Latest Posts
-
The Magnetic Field At A Disn
Mar 31, 2025
-
Which Of The Following Statements About Savings Accounts Is False
Mar 31, 2025
-
Draw The Product Of An Sn2 Reaction Shown Below
Mar 31, 2025
-
When Writers Use Long Paragraphs In Business Messages It
Mar 31, 2025
-
Fill In The Blanks In Symbol Column Of The Table
Mar 31, 2025
Related Post
Thank you for visiting our website which covers about From The Plot Of Yield Strength Versus . We hope the information provided has been useful to you. Feel free to contact us if you have any questions or need further assistance. See you next time and don't miss to bookmark.