Flexible Manufacturing Systems Can Be Extended __________.
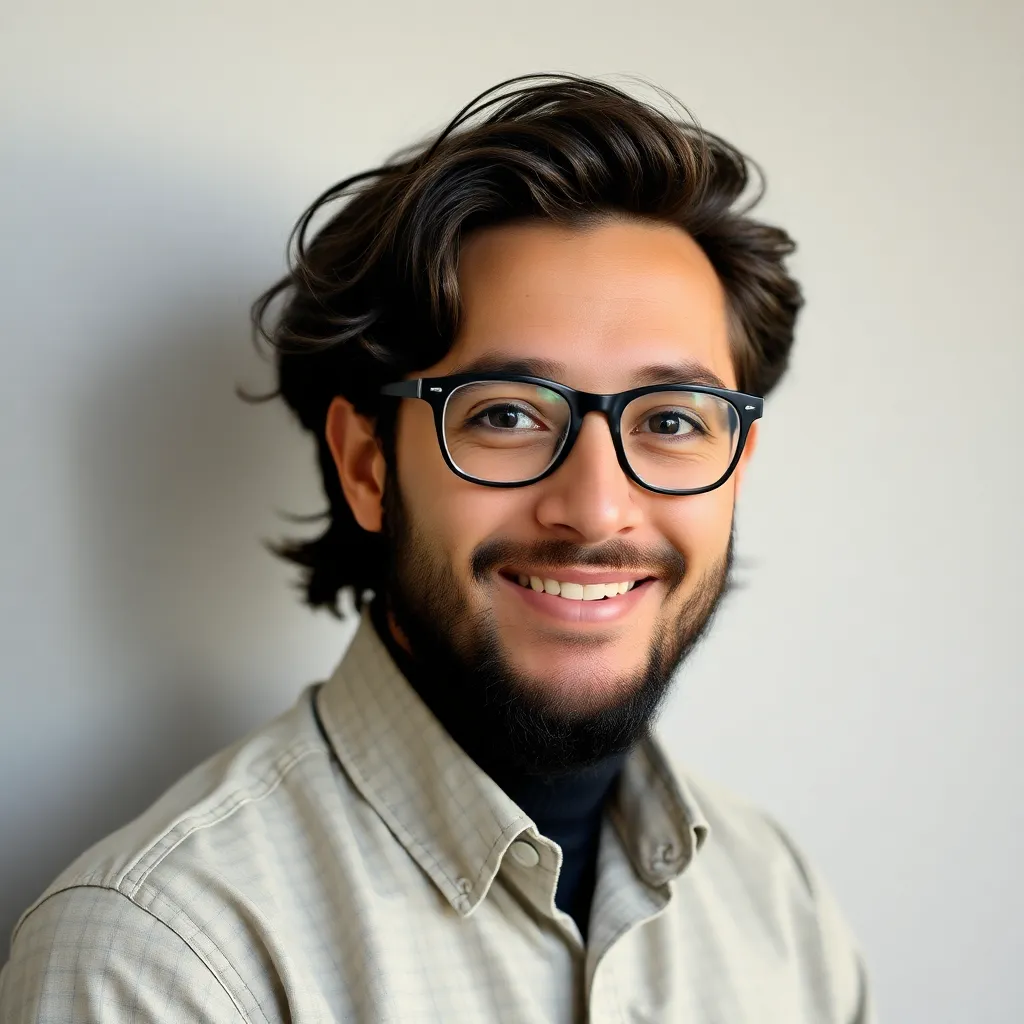
Holbox
Mar 14, 2025 · 7 min read
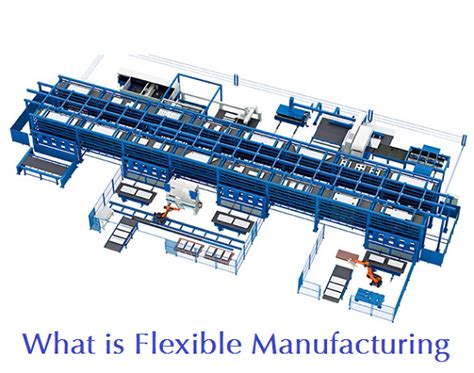
Table of Contents
- Flexible Manufacturing Systems Can Be Extended __________.
- Table of Contents
- Flexible Manufacturing Systems Can Be Extended: Enhancing Productivity and Adaptability
- Extending FMS to Enhance Supply Chain Integration
- 1. Supplier Relationship Management (SRM):
- 2. Warehouse Management Systems (WMS) Integration:
- 3. Customer Relationship Management (CRM) Integration:
- Extending FMS to Enhance Internal Processes
- 1. Advanced Process Control & Monitoring:
- 2. Enhanced Human-Machine Interaction (HMI):
- 3. Integration with Enterprise Resource Planning (ERP) Systems:
- Extending FMS to Embrace Emerging Technologies
- 1. Artificial Intelligence (AI) and Machine Learning (ML):
- 2. Internet of Things (IoT) Integration:
- 3. Digital Twins:
- Conclusion: The Expanding Horizons of FMS
- Latest Posts
- Latest Posts
- Related Post
Flexible Manufacturing Systems Can Be Extended: Enhancing Productivity and Adaptability
Flexible Manufacturing Systems (FMS) represent a significant advancement in manufacturing, offering unparalleled adaptability and efficiency. But their capabilities don't end at the factory floor. The question, "Flexible Manufacturing Systems can be extended __________," opens up a wide range of possibilities. This article explores several key areas where FMS can, and should, be extended to further optimize production, enhance supply chain management, and improve overall business performance.
Extending FMS to Enhance Supply Chain Integration
One crucial area for extending FMS capabilities lies in seamlessly integrating them with the broader supply chain. This involves extending the system's reach beyond the factory walls to encompass:
1. Supplier Relationship Management (SRM):
Real-time Data Sharing: Extending FMS to include real-time data sharing with key suppliers allows for proactive inventory management. The system can automatically trigger orders based on production schedules and anticipated demand, minimizing delays and ensuring a consistent flow of materials. This requires developing robust data exchange protocols and integrating the FMS with supplier ERP systems.
Collaborative Planning: Advanced integration enables collaborative planning with suppliers. By sharing production schedules and forecasts, manufacturers can work with suppliers to optimize their own production processes, leading to better resource allocation and reduced lead times. This requires a strong focus on communication and shared goals.
Supplier Performance Monitoring: Extending the FMS to include supplier performance monitoring tools allows manufacturers to track key metrics like on-time delivery and quality. This information can then be used to improve supplier selection and performance, leading to increased reliability and reduced disruptions.
2. Warehouse Management Systems (WMS) Integration:
Automated Material Handling: Integrating FMS with WMS allows for automated material handling between the warehouse and the production floor. This reduces manual handling errors, minimizes delays, and improves overall efficiency. This necessitates the use of automated guided vehicles (AGVs) or robots to efficiently move materials.
Inventory Tracking & Optimization: Real-time tracking of materials within the warehouse ensures that the right components are available when needed. This reduces inventory holding costs and minimizes stockouts. This requires utilizing RFID or barcode technology for precise inventory tracking.
Optimized Storage & Retrieval: The FMS can inform the WMS about upcoming production needs, allowing the warehouse to optimize storage and retrieval strategies. This ensures that frequently used materials are readily accessible, reducing picking times and increasing efficiency.
3. Customer Relationship Management (CRM) Integration:
Demand Forecasting & Planning: Integrating FMS with CRM data enables more accurate demand forecasting. By analyzing customer orders and sales trends, manufacturers can better anticipate future demand, enabling them to adjust production schedules accordingly. This fosters agility and reduces wasted resources.
Personalized Manufacturing: Extending FMS to incorporate CRM data allows for personalized manufacturing. This might involve customizing products based on individual customer preferences, offering a greater degree of flexibility and responsiveness. This necessitates adaptable manufacturing processes and robust configuration management.
On-Time Delivery & Improved Customer Satisfaction: With better demand forecasting and optimized production planning, FMS integration with CRM can lead to improved on-time delivery rates, ultimately boosting customer satisfaction and loyalty. This requires a commitment to proactive communication and feedback loops with customers.
Extending FMS to Enhance Internal Processes
Extending the reach of FMS within the manufacturing facility itself offers significant improvements in efficiency and control. This involves:
1. Advanced Process Control & Monitoring:
Real-time Data Analytics: Extending FMS to include sophisticated data analytics tools allows for real-time monitoring of production processes. This enables early detection of anomalies and potential problems, allowing for proactive interventions and preventing costly downtime. This requires implementation of robust sensor networks and data processing capabilities.
Predictive Maintenance: Using data analytics, FMS can predict potential equipment failures before they occur, allowing for scheduled maintenance to prevent unexpected downtime. This results in increased equipment lifespan and reduced maintenance costs. This necessitates sophisticated algorithms and machine learning capabilities.
Automated Quality Control: Extending FMS to include automated quality control processes, such as vision systems and automated inspection tools, enhances product quality and reduces defects. This reduces waste and improves overall product quality.
2. Enhanced Human-Machine Interaction (HMI):
User-Friendly Interfaces: Improving the HMI through intuitive interfaces enhances operator efficiency and reduces the learning curve for new employees. This reduces errors and increases productivity. This requires a focus on ergonomics and user experience design.
Augmented Reality (AR) Support: Integrating AR technology into the FMS can provide operators with real-time information and guidance, leading to improved accuracy and efficiency. This enables operators to more effectively troubleshoot issues and perform maintenance tasks.
Collaborative Robots (Cobots): Extending FMS to incorporate collaborative robots allows for safer and more efficient human-robot interaction. Cobots can assist human workers with repetitive or physically demanding tasks, leading to increased productivity and reduced workplace injuries.
3. Integration with Enterprise Resource Planning (ERP) Systems:
Streamlined Data Flow: Integrating FMS with the company's ERP system creates a seamless flow of information between production planning, inventory management, and financial reporting. This provides a comprehensive overview of the manufacturing process and facilitates better decision-making. This necessitates developing effective data exchange standards.
Improved Production Scheduling: The integration allows for more accurate and efficient production scheduling, ensuring that resources are allocated optimally and production deadlines are met. This reduces bottlenecks and optimizes resource utilization.
Real-time Cost Tracking: Extending the system enables real-time tracking of production costs, enabling manufacturers to identify areas for improvement and reduce overall expenses. This facilitates improved cost control and profitability.
Extending FMS to Embrace Emerging Technologies
The future of FMS lies in its ability to embrace and integrate emerging technologies to further enhance its capabilities. This includes:
1. Artificial Intelligence (AI) and Machine Learning (ML):
Intelligent Scheduling and Optimization: AI and ML can be used to optimize production schedules based on real-time data and predicted demand. This enhances efficiency and reduces lead times. This requires advanced algorithms and computational power.
Predictive Quality Control: AI and ML algorithms can be used to predict potential quality issues before they occur, allowing manufacturers to take preventative measures and improve product quality. This ensures higher product quality and consistency.
Autonomous Decision-Making: In the future, AI could enable FMS to make autonomous decisions regarding production adjustments, resource allocation, and maintenance scheduling. This requires careful design and testing to ensure safety and reliability.
2. Internet of Things (IoT) Integration:
Real-time Data Collection: IoT sensors can collect real-time data from various points throughout the manufacturing process, providing a more complete picture of the system's performance. This enhances visibility and allows for timely interventions.
Improved Asset Tracking: IoT can be used to track the location and status of assets within the manufacturing facility, ensuring that equipment is available when needed and minimizing downtime. This requires implementation of robust tracking systems and data management.
Remote Monitoring & Control: IoT enables remote monitoring and control of FMS, allowing manufacturers to oversee operations from anywhere in the world. This enhances responsiveness and improves efficiency.
3. Digital Twins:
Virtual Representation of FMS: Creating a digital twin of the FMS allows for simulation and testing of new processes and configurations before implementation. This reduces the risk of errors and optimizes performance. This requires sophisticated modeling capabilities and data analysis.
Predictive Maintenance & Optimization: The digital twin can be used to predict potential equipment failures and optimize production parameters, leading to increased efficiency and reduced downtime. This utilizes real-time data to continuously improve the digital twin.
Process Improvement & Innovation: The digital twin provides a valuable tool for exploring process improvements and innovative manufacturing techniques without disrupting actual production. This enhances adaptability and enables continuous improvement.
Conclusion: The Expanding Horizons of FMS
Flexible Manufacturing Systems are not static entities; they are dynamic and evolving systems that require continuous adaptation and enhancement to remain competitive. By extending FMS to incorporate the strategies and technologies outlined above, manufacturers can unlock new levels of productivity, adaptability, and profitability. The future of manufacturing hinges on the ability to embrace the expanding horizons of FMS, creating more agile, responsive, and efficient production systems. The more integrated and intelligent the system becomes, the greater the benefits will be, solidifying the place of FMS as a cornerstone of modern manufacturing excellence.
Latest Posts
Latest Posts
-
What Are The Two Distinguishing Characteristics Of Political Socialization
Mar 15, 2025
-
Keeping A Food Frozen Until Thawed Will
Mar 15, 2025
-
Marketers Conduct Marketing Research Primarily To
Mar 15, 2025
-
Damage To Ependymal Cells Would Most Likely Affect The
Mar 15, 2025
-
Negation Often Symbolizes The Natural Language Word
Mar 15, 2025
Related Post
Thank you for visiting our website which covers about Flexible Manufacturing Systems Can Be Extended __________. . We hope the information provided has been useful to you. Feel free to contact us if you have any questions or need further assistance. See you next time and don't miss to bookmark.