Family Furniture Corporation Incurred The Following Costs
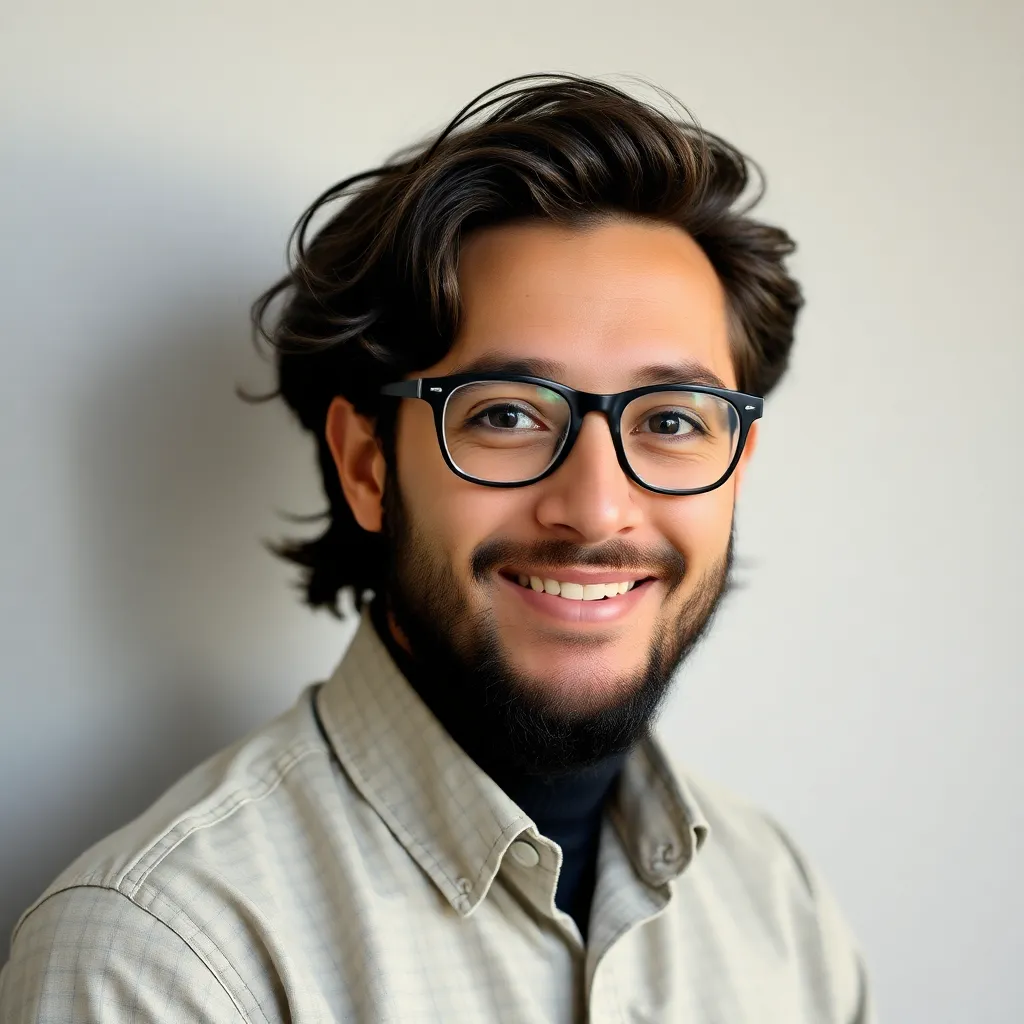
Holbox
Mar 27, 2025 · 6 min read
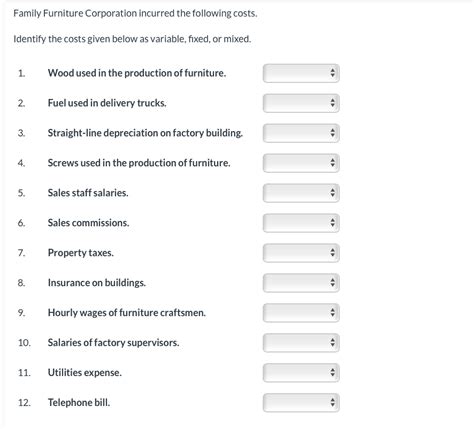
Table of Contents
Decoding Family Furniture Corporation's Costs: A Deep Dive into Financial Analysis
Family Furniture Corporation (FFC), like any business, incurs various costs in its operations. Understanding these costs is crucial for effective financial management, strategic decision-making, and ultimately, profitability. This article delves into the diverse cost structures of a furniture corporation like FFC, examining their categorization, impact on pricing strategies, and the importance of accurate cost accounting for long-term success.
I. Categorizing FFC's Costs: A Comprehensive Breakdown
FFC's costs can be categorized in several ways, offering different perspectives for analysis:
A. By Nature of the Cost:
-
Direct Costs: These are directly attributable to the production of furniture. For FFC, this would include:
- Raw Materials: The cost of wood, fabrics, foam, hardware, finishes, and other materials used in manufacturing. Fluctuations in lumber prices, for instance, would significantly impact FFC's direct costs.
- Direct Labor: Wages and benefits paid to employees directly involved in furniture manufacturing – carpenters, upholsterers, assembly line workers, etc. Labor costs are influenced by factors like minimum wage laws, employee skill levels, and union negotiations.
- Manufacturing Overhead: Costs indirectly related to production but necessary for the process. This category includes:
- Factory Rent and Utilities: Costs associated with the manufacturing facility.
- Depreciation of Machinery and Equipment: The allocation of the cost of equipment over its useful life.
- Factory Supplies: Consumables like glue, nails, and sandpaper.
- Quality Control Costs: Expenses related to ensuring product quality.
-
Indirect Costs (Overhead): These are not directly traceable to a specific product but are necessary for the overall operation of the business. For FFC, this encompasses:
- Selling and Marketing Expenses: Advertising, sales commissions, showroom rent, and promotional activities. The effectiveness of marketing campaigns directly impacts sales volume and profitability.
- Administrative Expenses: Salaries of administrative staff, office rent, utilities, insurance, legal fees, and accounting costs. Efficient administrative processes are essential for reducing overhead.
- Research and Development (R&D): Expenses dedicated to designing new furniture lines, improving existing products, and exploring innovative materials and manufacturing techniques. Investment in R&D can drive long-term growth and competitive advantage.
- Distribution and Logistics Costs: Expenses related to warehousing, transportation, and delivery of finished furniture. Efficient supply chain management is crucial for minimizing these costs.
B. By Behavior of the Cost:
This categorization focuses on how costs change with changes in production volume.
-
Variable Costs: Costs that fluctuate directly with production volume. For FFC, this includes:
- Raw Materials: More furniture produced means more raw materials are needed.
- Direct Labor (in some cases): If FFC employs hourly workers, labor costs will increase with production volume.
-
Fixed Costs: Costs that remain relatively constant regardless of production volume within a relevant range. For FFC, this includes:
- Factory Rent: Rent is typically fixed regardless of production levels.
- Salaries of Administrative Staff: Administrative salaries are usually fixed.
- Depreciation: Depreciation expense is calculated based on the asset's useful life, not production volume.
-
Mixed Costs (Semi-Variable Costs): Costs that have both fixed and variable components. An example for FFC could be:
- Utilities: There's a fixed base cost for utilities, but usage increases with higher production levels.
II. The Impact of Costs on FFC's Pricing Strategies
Understanding its cost structure is crucial for FFC to develop effective pricing strategies. Several approaches exist:
-
Cost-Plus Pricing: FFC calculates its total costs per unit and adds a markup percentage to determine the selling price. This ensures profitability but might price the furniture out of the market if competitors offer lower prices.
-
Value-Based Pricing: FFC focuses on the perceived value of its furniture to customers and sets prices accordingly. This approach may involve premium pricing if the furniture offers unique features or superior quality.
-
Competitive Pricing: FFC sets prices based on competitor offerings. This approach requires careful market analysis but could lead to price wars if not managed carefully.
-
Market Penetration Pricing: FFC sets initial prices low to gain market share, gradually increasing them as it establishes brand recognition. This strategy requires significant upfront investment but can lead to rapid growth.
-
Price Skimming: FFC sets high initial prices to target early adopters and gradually lowers them over time. This strategy works best for innovative or high-demand products.
III. Cost Accounting and its Importance for FFC's Success
Accurate cost accounting is essential for FFC's long-term viability. It enables:
-
Effective Inventory Management: FFC can accurately track the cost of goods sold and manage inventory levels to minimize storage costs and spoilage.
-
Profitability Analysis: By accurately tracking costs, FFC can pinpoint profitable and unprofitable product lines, allowing for informed decision-making regarding product mix and resource allocation.
-
Budgeting and Forecasting: Detailed cost data forms the basis for accurate budgeting and financial forecasting, helping FFC plan for future investments and expansion.
-
Performance Evaluation: Tracking costs helps FFC evaluate the efficiency of its operations and identify areas for improvement in productivity and cost reduction.
-
Decision Making: Cost information is critical for making informed decisions regarding pricing, production levels, new product development, and investment in new technology or equipment.
IV. Advanced Cost Accounting Techniques for FFC
FFC could utilize several advanced cost accounting techniques to enhance its financial management:
-
Activity-Based Costing (ABC): This method assigns costs to activities and then allocates those costs to products based on their consumption of those activities. It provides a more accurate cost picture than traditional methods, especially for businesses with diverse product lines.
-
Target Costing: This approach starts with the desired selling price and works backward to determine the allowable cost of production. This encourages innovation and cost reduction from the design stage.
-
Lean Accounting: This focuses on eliminating waste and improving efficiency throughout the value chain. Lean accounting integrates cost accounting with lean manufacturing principles to drive continuous improvement.
V. The Role of Technology in Cost Management for FFC
Technology plays a crucial role in efficient cost management for FFC:
-
Enterprise Resource Planning (ERP) Systems: ERP systems integrate various business functions, including finance, inventory management, and production, providing a centralized platform for cost tracking and analysis.
-
Data Analytics and Business Intelligence: Analyzing cost data using advanced analytics tools can reveal trends, patterns, and anomalies, enabling proactive cost management and informed decision-making.
-
Automation: Automating tasks such as inventory tracking, production scheduling, and order processing reduces labor costs and improves efficiency.
VI. External Factors Impacting FFC's Costs
Several external factors significantly influence FFC's costs:
-
Economic Conditions: Recessions or economic downturns can impact consumer spending, reducing demand for furniture and potentially affecting FFC's sales volume and profitability.
-
Raw Material Prices: Fluctuations in the prices of lumber, fabrics, and other materials directly impact FFC's direct costs.
-
Competition: Intense competition can put pressure on FFC's pricing, affecting profitability.
-
Government Regulations: Environmental regulations, labor laws, and import/export tariffs can all affect FFC's costs.
-
Supply Chain Disruptions: Global events or natural disasters can disrupt supply chains, impacting the availability and cost of raw materials.
VII. Conclusion: A Holistic Approach to Cost Management for FFC
Effective cost management is paramount for Family Furniture Corporation's success. By employing robust cost accounting methods, leveraging technology, and understanding both internal and external factors, FFC can optimize its cost structure, develop effective pricing strategies, and ultimately enhance its profitability and competitive position in the furniture market. Regular monitoring, analysis, and adaptation are crucial in navigating the dynamic landscape of the furniture industry. A holistic approach, encompassing all aspects of cost management discussed above, will ensure FFC’s continued growth and sustainability.
Latest Posts
Latest Posts
-
The Area Labeled A Contains The
Mar 31, 2025
-
Ethics And College Student Life 3rd Edition
Mar 31, 2025
-
Match Each Term With Its Description
Mar 31, 2025
-
Income Smoothing Describes The Concept That
Mar 31, 2025
-
When Can A Notary Submit An Application For Reappointment
Mar 31, 2025
Related Post
Thank you for visiting our website which covers about Family Furniture Corporation Incurred The Following Costs . We hope the information provided has been useful to you. Feel free to contact us if you have any questions or need further assistance. See you next time and don't miss to bookmark.