Factory Burden Is A Synonym For
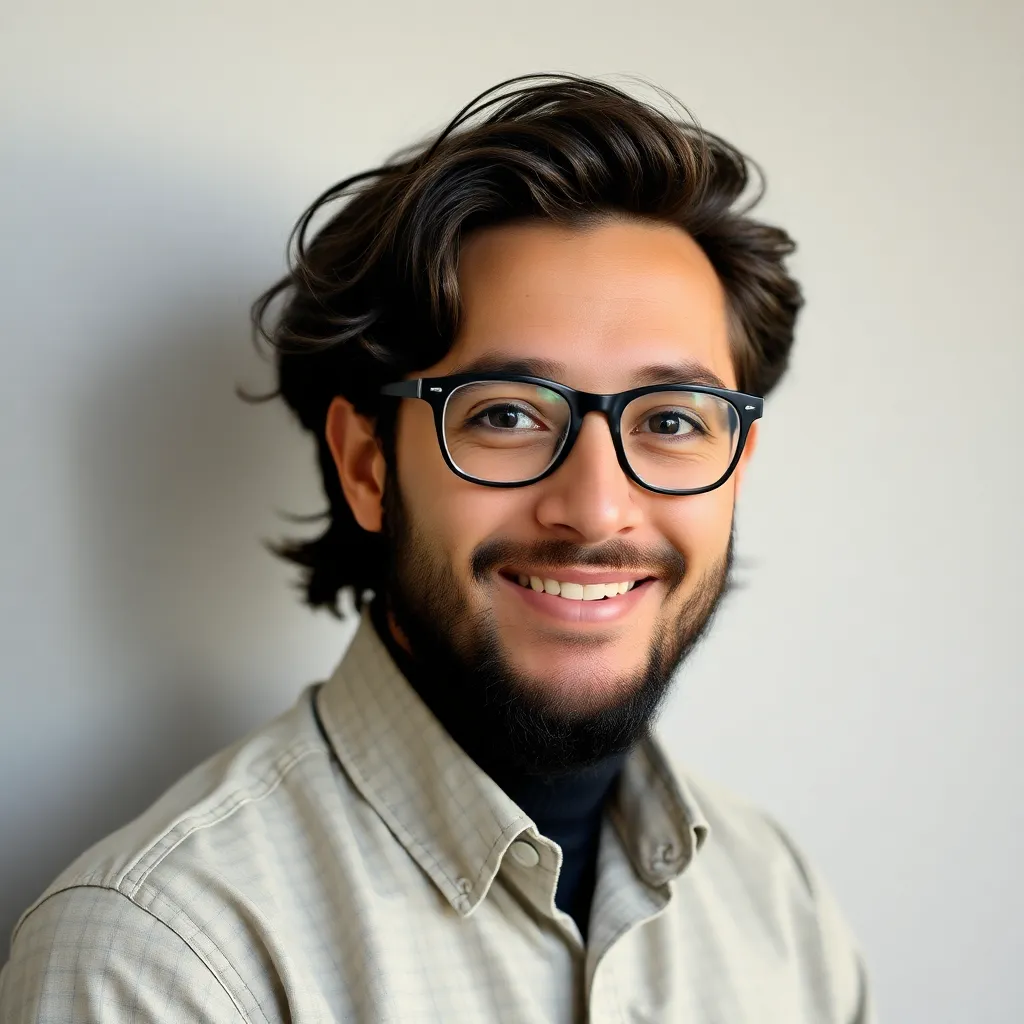
Holbox
May 09, 2025 · 6 min read
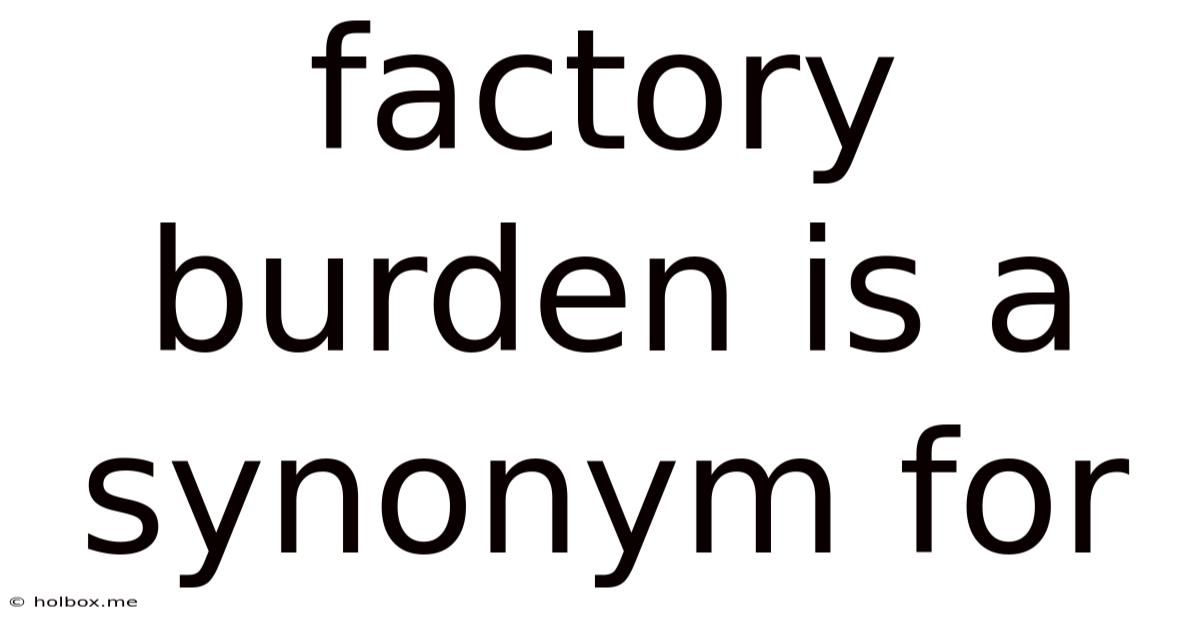
Table of Contents
- Factory Burden Is A Synonym For
- Table of Contents
- Factory Burden: A Comprehensive Guide to Synonyms, Calculations, and Importance
- Synonyms for Factory Burden: A Nuance of Meaning
- Components of Factory Burden: A Detailed Breakdown
- 1. Indirect Materials:
- 2. Indirect Labor:
- 3. Factory Rent and Utilities:
- 4. Factory Insurance:
- 5. Factory Property Taxes:
- 6. Depreciation of Factory Equipment:
- 7. Factory Supplies:
- 8. Factory Maintenance:
- Calculating Factory Burden: A Step-by-Step Guide
- Importance of Accurate Factory Burden Calculation
- Beyond the Basics: Advanced Considerations
- Conclusion: Mastering Factory Burden for Business Success
- Latest Posts
- Related Post
Factory Burden: A Comprehensive Guide to Synonyms, Calculations, and Importance
Factory burden, also known as manufacturing overhead, is a critical concept in cost accounting. It encompasses all indirect costs associated with operating a factory, excluding direct materials and direct labor. Understanding factory burden is crucial for accurate product costing, pricing decisions, and overall profitability analysis. While there isn't one single perfect synonym for "factory burden," several terms capture different aspects of this cost category. This article will delve deep into understanding factory burden, explore its synonyms, illustrate its calculation, and highlight its importance in business decision-making.
Synonyms for Factory Burden: A Nuance of Meaning
While "factory burden" is a precise term, several synonyms convey similar meanings, though often with subtle distinctions:
-
Manufacturing Overhead: This is arguably the most common and widely accepted synonym. It directly emphasizes the indirect nature of the costs included.
-
Indirect Costs: This is a broader term that encompasses factory burden but also includes indirect costs in other areas of a business beyond manufacturing.
-
Production Overhead: This term focuses specifically on the overhead costs related to the production process.
-
Factory Expenses: This is a simpler, more general term that highlights the expenditure aspect of factory burden.
-
Indirect Manufacturing Costs: This term explicitly connects the costs to the manufacturing process and their indirect nature.
-
Overhead Costs (in a manufacturing context): Using "overhead costs" alone is acceptable within the context of a discussion about manufacturing, although it lacks the specificity of "manufacturing overhead."
The choice of synonym often depends on the context and the intended audience. For accounting professionals, "manufacturing overhead" is preferred for its precision. In more general business discussions, "indirect costs" or "factory expenses" might be more readily understood.
Components of Factory Burden: A Detailed Breakdown
Understanding the various components that make up factory burden is vital for accurate calculation and analysis. These components can broadly be categorized as:
1. Indirect Materials:
These are materials used in the production process but are not directly traceable to a specific product. Examples include:
- Cleaning supplies: Used for maintaining a clean and safe work environment.
- Lubricants and oils: Used for maintaining machinery and equipment.
- Small tools and consumables: Items with short lifespans, like drill bits or sandpaper.
2. Indirect Labor:
This includes the wages and salaries of employees who don't directly work on the product but support the manufacturing process. Examples include:
- Supervisors: Overseeing production processes and workers.
- Maintenance personnel: Responsible for maintaining and repairing factory equipment.
- Quality control inspectors: Ensuring products meet quality standards.
- Material handlers: Moving materials within the factory.
3. Factory Rent and Utilities:
These are the costs associated with operating the factory building and its utilities:
- Rent or depreciation of the factory building: The cost of owning or leasing the factory space.
- Utilities: Electricity, gas, water, and other utility services.
4. Factory Insurance:
This covers insurance premiums related to the factory building, equipment, and potential liabilities.
5. Factory Property Taxes:
These are property taxes levied on the factory building and land.
6. Depreciation of Factory Equipment:
This represents the allocation of the cost of factory equipment over its useful life.
7. Factory Supplies:
These are items used in the factory but are not directly incorporated into the product.
8. Factory Maintenance:
This covers the costs of maintaining and repairing factory equipment.
Calculating Factory Burden: A Step-by-Step Guide
Calculating factory burden involves aggregating all the indirect costs associated with factory operations. The most common method is to calculate a predetermined overhead rate, which is then applied to production. This rate is typically based on a chosen cost driver, such as direct labor hours or machine hours.
Steps to Calculate Factory Burden:
-
Identify all indirect costs: Compile a list of all costs categorized under indirect materials, indirect labor, factory rent, utilities, insurance, property taxes, depreciation, supplies, and maintenance.
-
Total indirect costs: Sum all the identified indirect costs to arrive at the total factory burden.
-
Select a cost driver: Choose a relevant cost driver that best reflects the factory's activity level. Common cost drivers include direct labor hours, machine hours, and direct labor costs.
-
Calculate the predetermined overhead rate: Divide the total factory burden by the chosen cost driver. The formula is:
Predetermined Overhead Rate = Total Factory Burden / Total Cost Driver
-
Apply the predetermined overhead rate: Multiply the predetermined overhead rate by the actual cost driver used for each product or job to allocate the factory burden.
Example:
Let's say a factory has total factory burden of $100,000 and 10,000 direct labor hours. The predetermined overhead rate would be:
$100,000 / 10,000 hours = $10 per direct labor hour
If a particular product requires 5 direct labor hours, the factory burden allocated to that product would be:
5 hours * $10/hour = $50
Importance of Accurate Factory Burden Calculation
Accurate calculation of factory burden is paramount for several reasons:
-
Accurate Product Costing: Properly allocating factory burden ensures accurate costing of products, which is crucial for pricing decisions, profitability analysis, and inventory valuation. Underestimating or overestimating factory burden can lead to incorrect pricing and ultimately affect the company's competitiveness and profitability.
-
Informed Pricing Decisions: Accurate product costs enable businesses to set competitive prices that cover all costs and generate a reasonable profit margin. Without accurate factory burden allocation, pricing decisions could be flawed, leading to losses or missed profit opportunities.
-
Performance Evaluation: Tracking factory burden helps in evaluating the efficiency of factory operations. Identifying areas where costs are higher than expected can lead to improvements and cost reduction strategies. Analyzing trends in factory burden over time can also reveal potential problems or areas needing attention.
-
Resource Allocation: Understanding factory burden allows businesses to effectively allocate resources to different production activities based on cost and efficiency. Knowing the costs associated with each aspect of production allows for data-driven decision-making in resource allocation.
-
Investment Decisions: Accurate factory burden calculations are crucial when considering investments in new equipment, technologies, or expansion projects. By understanding the impact of these investments on factory burden, companies can make well-informed decisions that maximize returns and minimize risks.
-
Compliance and Reporting: Accurate costing and the proper allocation of factory burden are essential for complying with accounting standards and generating accurate financial reports for stakeholders.
Beyond the Basics: Advanced Considerations
Several factors can influence the accuracy and complexity of factory burden calculations:
-
Multiple Cost Pools: Large factories often use multiple cost pools to allocate overhead costs more accurately, reflecting different activities and cost drivers within the factory.
-
Activity-Based Costing (ABC): ABC is a more sophisticated method that allocates overhead costs based on the activities that consume resources. This is particularly useful in complex manufacturing environments where different products consume resources in different ways.
-
Seasonality and Fluctuations: Fluctuations in production volume and seasonal factors can influence factory burden. Adjustments to the predetermined overhead rate might be needed to account for these variations.
-
Automation and Technology: The increasing use of automation and technology can change the composition of factory burden. For example, increased automation might reduce direct labor costs but increase depreciation and maintenance costs.
Conclusion: Mastering Factory Burden for Business Success
Factory burden, regardless of the synonym used, is a critical aspect of cost accounting in manufacturing. Understanding its components, calculating it accurately, and using the data to inform decision-making are essential for successful business operations. By mastering this concept, businesses can improve their product costing, pricing strategies, operational efficiency, and overall profitability. Choosing the right synonym for the context and utilizing advanced costing methods when appropriate further enhances the accuracy and utility of this crucial data.
Latest Posts
Related Post
Thank you for visiting our website which covers about Factory Burden Is A Synonym For . We hope the information provided has been useful to you. Feel free to contact us if you have any questions or need further assistance. See you next time and don't miss to bookmark.