Ethylene Oxide Is Produced By The Catalytic Oxidation
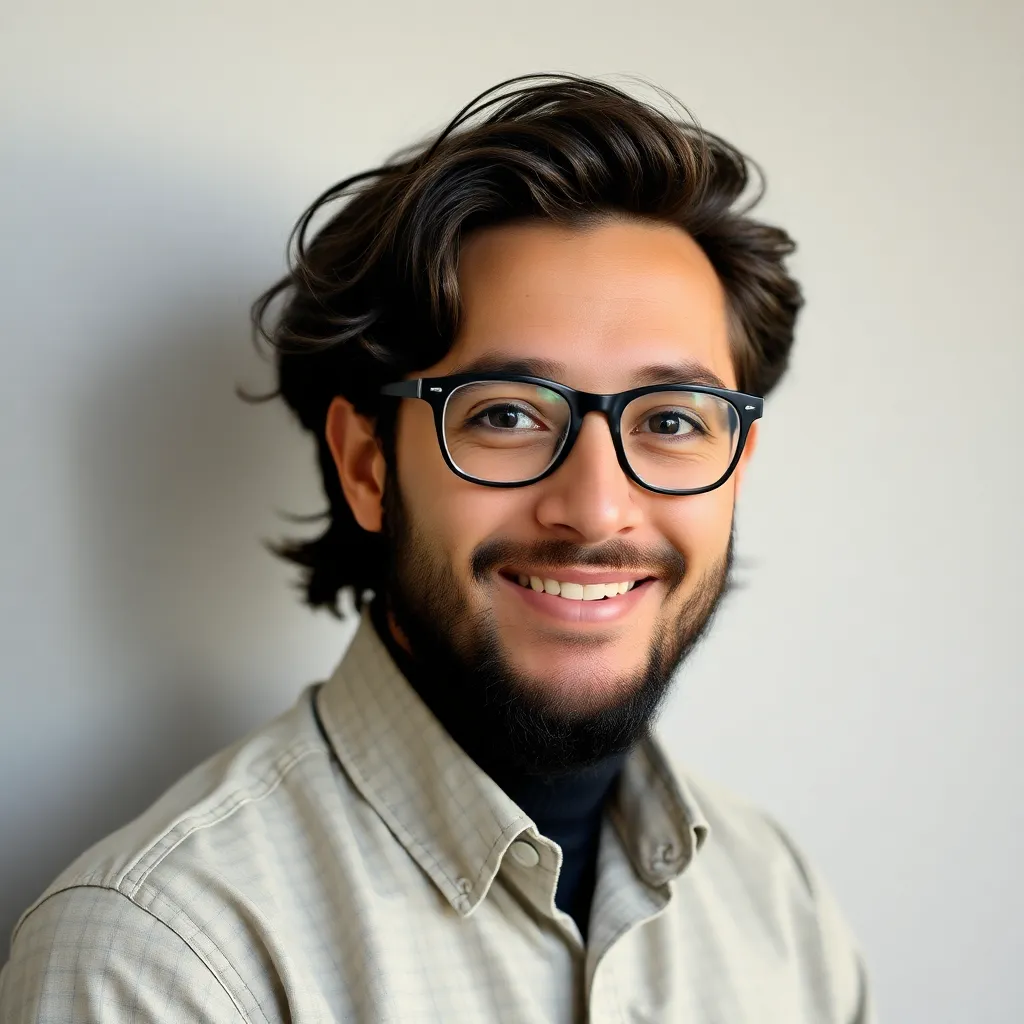
Holbox
Apr 14, 2025 · 8 min read

Table of Contents
- Ethylene Oxide Is Produced By The Catalytic Oxidation
- Table of Contents
- Ethylene Oxide: Production via Catalytic Oxidation
- The Catalytic Oxidation Reaction: A Closer Look
- Understanding the Reaction Mechanism
- The Catalyst: The Heart of the Process
- Silver Catalysts: The Industry Standard
- Optimizing Silver Catalyst Performance
- Exploring Alternative Catalysts
- Process Parameters: Fine-Tuning the Reaction
- Temperature Control: A Delicate Balance
- Pressure Optimization: Maximizing Conversion
- Feed Composition: Controlling Reactant Ratios
- Residence Time: Enhancing Conversion and Selectivity
- Reactor Design and Process Engineering
- Fixed-Bed Reactors: A Common Choice
- Fluidized-Bed Reactors: Enhanced Heat Transfer
- Membrane Reactors: Enhanced Selectivity
- Process Optimization and Control
- Advanced Control Systems: Maintaining Optimal Conditions
- Process Integration and Energy Efficiency
- Environmental Considerations and Safety
- By-product Treatment and Waste Management
- Safety Protocols and Risk Mitigation
- Future Trends and Research
- Catalyst Development: Seeking Improved Performance
- Process Intensification: Enhancing Efficiency
- Sustainable Processes: Reducing Environmental Impact
- Latest Posts
- Latest Posts
- Related Post
Ethylene Oxide: Production via Catalytic Oxidation
Ethylene oxide (EO), a crucial chemical intermediate, finds widespread application in various industries. Its production predominantly relies on the catalytic oxidation of ethylene. This process, a cornerstone of modern chemical manufacturing, involves a complex interplay of reaction conditions, catalyst selection, and process optimization to achieve high yields and selectivity. This detailed exploration delves into the intricacies of ethylene oxide production via catalytic oxidation, examining the reaction mechanism, catalyst technology, process parameters, and the crucial role of process engineering in maximizing efficiency and minimizing environmental impact.
The Catalytic Oxidation Reaction: A Closer Look
The heart of EO production lies in the direct oxidation of ethylene using oxygen as the oxidant. This exothermic reaction, represented below, is characterized by a delicate balance between achieving high conversion and minimizing undesirable side reactions:
CH₂=CH₂ + ½O₂ → C₂H₄O
While seemingly straightforward, this reaction is inherently challenging. The high reactivity of ethylene and the possibility of complete combustion to carbon dioxide and water necessitate precise control over reaction conditions. The primary challenge lies in achieving high selectivity towards EO formation, minimizing the formation of byproducts like CO₂, CO, and acetaldehyde.
Understanding the Reaction Mechanism
The catalytic oxidation of ethylene is a complex process involving several intermediate steps. The generally accepted mechanism involves the adsorption of both ethylene and oxygen onto the catalyst surface. These adsorbed species then undergo a series of surface reactions leading to the formation of EO. The exact nature of these surface reactions remains an area of ongoing research, but key steps include:
- Ethylene adsorption: The ethylene molecule interacts with the catalyst surface, weakening its double bond and making it more susceptible to oxidation.
- Oxygen activation: The oxygen molecule is activated on the catalyst surface, becoming more reactive and facilitating the oxidation process.
- Ethylene epoxidation: Activated oxygen interacts with adsorbed ethylene, forming the ethylene oxide molecule.
- Ethylene oxide desorption: The newly formed EO molecule desorbs from the catalyst surface, freeing up active sites for further reaction.
The Catalyst: The Heart of the Process
The catalyst plays a pivotal role in determining the efficiency and selectivity of the ethylene oxidation reaction. Silver-based catalysts have been the industry standard for decades, although ongoing research explores alternative materials to improve efficiency and reduce costs.
Silver Catalysts: The Industry Standard
Silver catalysts, typically supported on alumina, are highly effective in promoting the selective oxidation of ethylene. The silver particles provide active sites for the adsorption and reaction of ethylene and oxygen. The alumina support provides a high surface area, enhancing catalyst activity and dispersion. The preparation and activation of silver catalysts are crucial for their performance. Factors like silver loading, particle size, and support properties significantly influence catalyst activity and selectivity.
Optimizing Silver Catalyst Performance
Various strategies aim to optimize the performance of silver catalysts:
- Promoters: Adding promoters, such as chlorine or alkali metals, can enhance catalyst activity and selectivity. These promoters modify the electronic and structural properties of the silver, influencing the adsorption and reaction of reactants.
- Support Modification: Modifying the alumina support, for instance, by incorporating other oxides or adjusting its surface area, can further optimize catalyst performance.
- Catalyst Preparation Methods: Advanced catalyst preparation techniques, such as sol-gel methods, co-precipitation, or impregnation, can produce catalysts with improved dispersion, particle size control, and enhanced performance.
Exploring Alternative Catalysts
While silver catalysts dominate the industry, research into alternative catalysts continues. This pursuit aims to address limitations of silver catalysts, including susceptibility to deactivation and the need for high reaction temperatures. Research focuses on exploring transition metal oxides and other materials to discover catalysts with improved selectivity and lower operational costs.
Process Parameters: Fine-Tuning the Reaction
The successful production of EO demands precise control over various process parameters. These parameters significantly influence reaction rates, selectivity, and overall process efficiency. Careful optimization of these factors is essential for maximizing EO yield and minimizing byproduct formation.
Temperature Control: A Delicate Balance
The reaction temperature is a critical parameter affecting both reaction rate and selectivity. Operating at too low a temperature results in low conversion, while excessively high temperatures promote complete combustion, leading to reduced EO selectivity and increased energy consumption. Optimum temperature ranges typically fall between 200°C and 300°C, but specific optimal temperature is dependent on the specific catalyst and reactor design.
Pressure Optimization: Maximizing Conversion
The reaction pressure also influences the process. While higher pressures generally favor higher ethylene conversion, they can also increase the rate of side reactions. A balance needs to be struck to optimize EO selectivity. Typical operating pressures range from 1 to 3 MPa.
Feed Composition: Controlling Reactant Ratios
The ratio of ethylene to oxygen in the feed stream is crucial for selectivity. Excess oxygen can lead to increased combustion, while insufficient oxygen limits conversion. Precise control of the feed composition is vital for achieving optimal EO yields. Often, a slight excess of ethylene is used to mitigate complete combustion.
Residence Time: Enhancing Conversion and Selectivity
The residence time of the reactants in the reactor directly impacts conversion and selectivity. Longer residence times can lead to higher conversion but also increase the likelihood of side reactions. Optimizing residence time requires a delicate balance to maximize EO yield while maintaining acceptable selectivity.
Reactor Design and Process Engineering
Reactor design plays a crucial role in maximizing EO production efficiency and minimizing environmental impact. Various reactor configurations have been employed, each with advantages and disadvantages.
Fixed-Bed Reactors: A Common Choice
Fixed-bed reactors are widely used in EO production. These reactors contain a packed bed of the catalyst, through which the reactant mixture flows. The design allows for efficient heat transfer and relatively simple operation. However, they can suffer from pressure drop limitations.
Fluidized-Bed Reactors: Enhanced Heat Transfer
Fluidized-bed reactors offer improved heat and mass transfer compared to fixed-bed reactors. In these reactors, the catalyst particles are suspended in a gas stream, enhancing contact between the reactants and the catalyst. However, they present challenges in catalyst separation and potential for catalyst attrition.
Membrane Reactors: Enhanced Selectivity
Membrane reactors offer opportunities for enhanced selectivity by selectively removing EO from the reaction mixture. This removal shifts the equilibrium towards EO formation, improving the overall yield. However, membrane fouling can limit their operational lifespan.
Process Optimization and Control
Optimizing the EO production process involves intricate control systems, ensuring consistent product quality and maximum yield. Advanced process control techniques are employed to maintain optimal reaction conditions despite variations in feed composition, catalyst activity, and other process parameters.
Advanced Control Systems: Maintaining Optimal Conditions
Modern EO plants utilize sophisticated control systems to monitor and adjust process parameters in real-time. These systems ensure that the reactor operates under optimal conditions despite fluctuations in the feedstock or catalyst performance. This sophisticated control ensures consistent product quality and maximizes yield.
Process Integration and Energy Efficiency
Process integration aims to minimize energy consumption and waste generation. Heat recovery systems and energy-efficient separation processes are incorporated into the design to improve the overall energy efficiency of the plant.
Environmental Considerations and Safety
The production of EO necessitates careful consideration of environmental and safety aspects. The process generates by-products such as carbon monoxide and carbon dioxide, requiring appropriate treatment and disposal methods. Rigorous safety protocols are vital to mitigate the risks associated with flammable and potentially toxic materials.
By-product Treatment and Waste Management
Proper disposal of byproducts is crucial for environmental protection. Techniques for CO and CO₂ abatement, such as absorption or combustion, are employed to minimize environmental impact. Wastewater treatment facilities are essential to manage waste streams and ensure compliance with environmental regulations.
Safety Protocols and Risk Mitigation
Ethylene and ethylene oxide are flammable and potentially toxic materials, requiring stringent safety protocols. Strict process control, regular equipment inspection, and emergency response plans are essential elements to minimize the risks associated with EO production.
Future Trends and Research
Research continues to explore ways to further improve the efficiency, selectivity, and sustainability of EO production. Areas of focus include the development of more efficient catalysts, improved reactor designs, and enhanced process control strategies.
Catalyst Development: Seeking Improved Performance
Ongoing research focuses on developing novel catalysts with higher selectivity, stability, and activity. This involves exploring alternative materials, optimizing catalyst preparation methods, and employing advanced characterization techniques.
Process Intensification: Enhancing Efficiency
Process intensification techniques, such as microreactor technology and supercritical fluid processing, aim to improve the overall efficiency of EO production. These approaches can lead to smaller reactor footprints, reduced energy consumption, and enhanced control over reaction parameters.
Sustainable Processes: Reducing Environmental Impact
The drive toward sustainability motivates research into more environmentally friendly EO production methods. This includes exploring alternative oxidants, developing more efficient separation techniques, and minimizing waste generation.
In conclusion, the catalytic oxidation of ethylene forms the bedrock of ethylene oxide production, a crucial process within the chemical industry. The successful implementation of this process demands a thorough understanding of reaction mechanisms, catalyst technology, process parameters, and rigorous process engineering. Continuous advancements in catalyst design, reactor technology, and process control pave the way for a more efficient, selective, and sustainable production of this vital chemical intermediate. The future of EO production undoubtedly lies in integrating sustainable practices and pushing the boundaries of process optimization to meet growing global demand while minimizing environmental impact.
Latest Posts
Latest Posts
-
Identify The True Statements About The Correlation Coefficient R
Apr 19, 2025
-
Draw A Curved Arrow Mechanism For The Reaction Shown
Apr 19, 2025
-
Fundamentals Of General Organic And Biological Chemistry
Apr 19, 2025
-
A Study Was Done On Proctored And Nonproctored Tests
Apr 19, 2025
-
Consider The Synthesis Of N N Dimethyl 2 Methylhexanamide
Apr 19, 2025
Related Post
Thank you for visiting our website which covers about Ethylene Oxide Is Produced By The Catalytic Oxidation . We hope the information provided has been useful to you. Feel free to contact us if you have any questions or need further assistance. See you next time and don't miss to bookmark.