Effectiveness And Efficiency Can Be Measured By
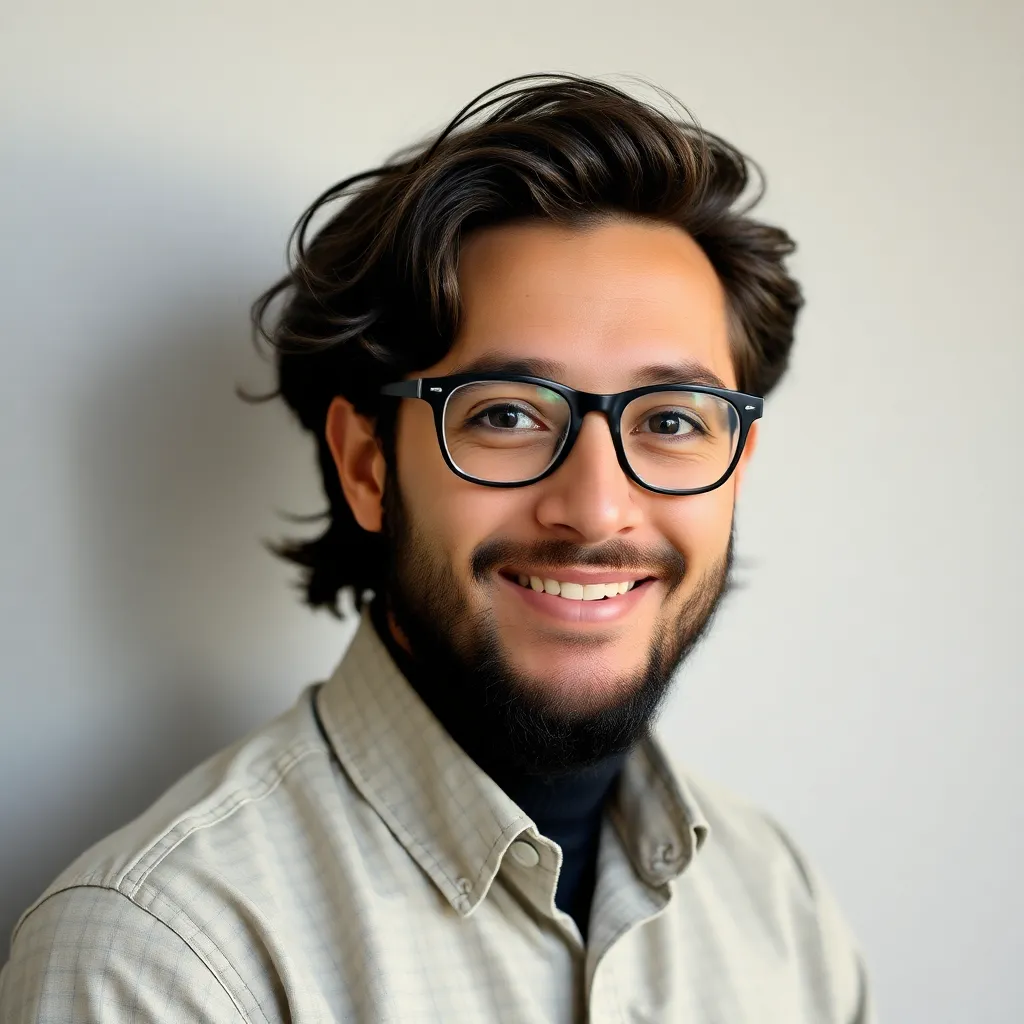
Holbox
Apr 03, 2025 · 6 min read

Table of Contents
- Effectiveness And Efficiency Can Be Measured By
- Table of Contents
- Effectiveness and Efficiency: How to Measure What Truly Matters
- Understanding the Difference: Effectiveness vs. Efficiency
- Measuring Effectiveness: Key Metrics and Approaches
- 1. Goal Achievement Rate:
- 2. Customer Satisfaction (CSAT) Scores:
- 3. Market Share:
- 4. Key Performance Indicators (KPIs):
- 5. Qualitative Data Analysis:
- Measuring Efficiency: Key Metrics and Approaches
- 1. Output per Unit of Input:
- 2. Cycle Time:
- 3. Inventory Turnover Rate:
- 4. Resource Utilization Rate:
- 5. Cost per Unit:
- 6. Defect Rate:
- Integrating Effectiveness and Efficiency Measurement
- Advanced Techniques for Measurement
- Challenges and Considerations
- Conclusion: A Continuous Improvement Journey
- Latest Posts
- Latest Posts
- Related Post
Effectiveness and Efficiency: How to Measure What Truly Matters
In today's fast-paced business environment, the ability to achieve goals (effectiveness) and to do so with minimal wasted effort or expense (efficiency) are paramount. While often used interchangeably, effectiveness and efficiency represent distinct yet interconnected concepts crucial for organizational success. Understanding how to measure both is key to optimizing performance and achieving sustainable growth. This article delves deep into the multifaceted world of measuring effectiveness and efficiency, exploring various metrics, methodologies, and best practices applicable across diverse industries and contexts.
Understanding the Difference: Effectiveness vs. Efficiency
Before diving into measurement, it's critical to clarify the fundamental distinction between effectiveness and efficiency.
Effectiveness focuses on achieving the desired outcome. It answers the question: "Are we doing the right things?" An effective organization successfully completes its objectives, meets its targets, and delivers on its promises. The emphasis is on achieving the intended results, regardless of the resources consumed.
Efficiency, on the other hand, focuses on optimizing resource utilization. It answers the question: "Are we doing things right?" An efficient organization minimizes waste, maximizes output with available resources, and operates at optimal capacity. The emphasis is on minimizing input (time, money, materials, etc.) while maximizing output.
The interplay: While both are essential, effectiveness takes precedence. Being highly efficient at doing the wrong things is ultimately unproductive. True success lies in the synergistic combination of both – achieving desired outcomes with minimal resource expenditure.
Measuring Effectiveness: Key Metrics and Approaches
Measuring effectiveness hinges on clearly defined goals and objectives. Without a clear understanding of what constitutes success, measuring effectiveness becomes meaningless. Here are several key metrics and approaches:
1. Goal Achievement Rate:
This is perhaps the most straightforward metric. It measures the percentage of pre-defined goals that have been successfully accomplished within a specified timeframe. For instance, a sales team might measure their effectiveness based on achieving a certain percentage of their sales targets. This metric requires clearly defined, measurable, achievable, relevant, and time-bound (SMART) goals.
2. Customer Satisfaction (CSAT) Scores:
In customer-centric businesses, CSAT scores provide a crucial measure of effectiveness. High CSAT scores indicate that the organization is successfully meeting customer needs and expectations, thus achieving its primary objective of customer satisfaction. This can be measured through surveys, feedback forms, and reviews.
3. Market Share:
For companies competing in a specific market, market share provides a valuable indicator of effectiveness. An increasing market share demonstrates the company's ability to capture a larger portion of the target market, signifying successful product/service differentiation and market penetration.
4. Key Performance Indicators (KPIs):
KPIs are specific, measurable metrics that track progress towards strategic goals. The choice of KPIs will vary greatly depending on the industry and organizational objectives. Examples include website traffic, conversion rates, customer acquisition cost, employee retention rates, and return on investment (ROI). Choosing the right KPIs is critical and requires a careful analysis of the organization's strategic priorities.
5. Qualitative Data Analysis:
Effectiveness isn't always easily quantifiable. Qualitative data, such as customer testimonials, employee feedback, and case studies, can provide invaluable insights into the impact of initiatives and programs. Analyzing this data can reveal areas of strength and weakness that quantitative metrics might miss.
Measuring Efficiency: Key Metrics and Approaches
Measuring efficiency involves tracking the relationship between inputs and outputs. The goal is to maximize output while minimizing input. Here are some effective methods:
1. Output per Unit of Input:
This is a fundamental efficiency metric. It calculates the amount of output produced for each unit of input. For example, in manufacturing, it could be units produced per labor hour. In a service industry, it could be the number of customers served per employee.
2. Cycle Time:
Cycle time measures the time it takes to complete a process from start to finish. Reducing cycle time indicates improved efficiency. This metric is widely used in manufacturing, software development, and other process-oriented industries.
3. Inventory Turnover Rate:
This metric measures how efficiently a company manages its inventory. A high inventory turnover rate indicates that the company is selling its inventory quickly, minimizing storage costs and the risk of obsolescence.
4. Resource Utilization Rate:
This metric assesses how effectively resources (equipment, personnel, facilities) are being utilized. A high resource utilization rate indicates minimal idle time and optimal resource allocation.
5. Cost per Unit:
This metric measures the cost of producing a single unit of output. Reducing cost per unit indicates improved efficiency. This metric is particularly relevant in manufacturing and production environments.
6. Defect Rate:
A low defect rate indicates higher efficiency as it signifies less rework, fewer material losses, and less time spent on correcting errors. This metric is crucial in quality control and manufacturing processes.
Integrating Effectiveness and Efficiency Measurement
While distinct, effectiveness and efficiency measurements are intertwined. A balanced scorecard approach integrates both perspectives by considering multiple performance indicators across different dimensions (financial, customer, internal processes, learning & growth). This holistic approach helps organizations understand their overall performance and identify areas for improvement.
Here’s how to integrate both effectively:
- Establish clear goals: Define SMART goals that are both effective (achieving desired outcomes) and efficient (achieving them with optimal resource use).
- Identify key performance indicators (KPIs): Choose KPIs that measure both effectiveness (e.g., customer satisfaction, market share) and efficiency (e.g., cycle time, cost per unit).
- Track and monitor data: Regularly collect and analyze data related to the chosen KPIs to identify trends and areas for improvement.
- Implement process improvements: Based on data analysis, implement process improvements to enhance both effectiveness and efficiency.
- Regularly review and adapt: Regularly review the measurement system and adapt it as needed to reflect changing business needs and priorities.
Advanced Techniques for Measurement
Beyond basic metrics, more advanced techniques can provide deeper insights into effectiveness and efficiency:
- Data Analytics and Business Intelligence: Leverage data analytics tools to identify patterns, trends, and anomalies in performance data. This can lead to more targeted improvements and better decision-making.
- Benchmarking: Compare your organization's performance to industry best practices and competitors. This provides insights into areas where improvement is needed and can identify areas of excellence.
- Six Sigma and Lean methodologies: These methodologies provide structured approaches to process improvement, focusing on eliminating waste and maximizing efficiency.
- Simulation and Modeling: Use simulation techniques to model different scenarios and predict the impact of proposed changes on effectiveness and efficiency before implementing them.
Challenges and Considerations
Measuring effectiveness and efficiency isn't always straightforward. Several challenges need to be addressed:
- Data Availability and Accuracy: Accurate and reliable data is crucial for effective measurement. Data inconsistencies, inaccuracies, or incomplete data can lead to flawed conclusions.
- Defining and Measuring Intangibles: Some aspects of effectiveness, such as employee morale or brand reputation, are difficult to quantify. Creative approaches and qualitative data analysis are needed to address these challenges.
- Resistance to Change: Implementing changes to improve effectiveness and efficiency may face resistance from employees who are accustomed to existing processes. Careful change management strategies are crucial.
- Balancing Short-Term and Long-Term Goals: Focusing solely on short-term efficiency gains can sometimes hinder long-term effectiveness. A balanced approach is necessary to ensure sustainable success.
Conclusion: A Continuous Improvement Journey
Measuring effectiveness and efficiency is not a one-time event but rather an ongoing process of continuous improvement. By regularly monitoring relevant metrics, analyzing data, and implementing necessary changes, organizations can optimize their performance, achieve their objectives, and thrive in an increasingly competitive landscape. The key lies in embracing a holistic approach, combining quantitative and qualitative data, and fostering a culture of continuous improvement focused on both achieving the right goals and doing so efficiently. This ongoing pursuit of excellence will ultimately lead to sustainable growth and long-term success.
Latest Posts
Latest Posts
-
Draw The Additional Resonance Structure S Of The Structure Below
Apr 08, 2025
-
Which Of The Following Represents An Efficient Synthesis Of 1 Methylcyclohexene
Apr 08, 2025
-
Z Owns A Disability Income Policy
Apr 08, 2025
-
In The Schedule Of Cost Of Goods Manufactured
Apr 08, 2025
-
Gold Nest Company Of Guandong China
Apr 08, 2025
Related Post
Thank you for visiting our website which covers about Effectiveness And Efficiency Can Be Measured By . We hope the information provided has been useful to you. Feel free to contact us if you have any questions or need further assistance. See you next time and don't miss to bookmark.